Echo sensors are designed to meet customer requirements by providing a combination of economic value and performance for general extrusion applications while providing a ±0.2% repeatability when measuring process pressures. Use Echo Series sensors when the application requires a quality measurement for optimized control, but not the costs of all the extra features.
Rigid Stem pressure sensors are easily installed into the mounting hole of the production line, ensuring a simple and robust design that is suitable for applications where the sensor is not exposed to radiant heat from the line and the electronics are not subjected to extreme temperatures. We do not recommend installing these sensors in a vertical position above the line (12 o'clock position), as radiant heat can negatively affect the sensor's electronics lifespan. In such cases, we recommend using a sensor design with a flexible capillary, which allows the electronics to be diverted away from the radiant heat, ensuring a long sensor life. The main advantages of this type of sensor include resistance to impacts and vibrations, enabling them to withstand mechanical stress, which increases their lifespan and reduces the need for maintenance. They also feature high accuracy, ensured by quality materials and advanced measurement technology, which is crucial for efficient process control.
Echo™ Series - With rigid stem and flexible capillary
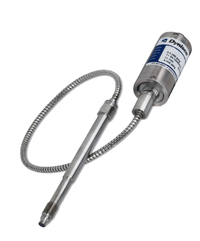
Pressure sensors with flexible capillaries represent a professional solution suitable for applications with limited space or exposure to radiant heat from heating elements in production lines. Thanks to the thoughtful extended design, the sensor's electronics are located out of reach of the radiant heat source, reducing the risk of damage.
The flexible capillary is designed to be resistant to damage and allow a high degree of bending, which facilitates installation and handling of the sensor. It is essential to properly secure the sensor head to the included adapter, which is part of the package. To achieve optimal performance, we recommend placing the adapter on a part of the machine where unwanted vibrations or shocks do not occur, as these could negatively affect the sensor.
The length of the rod and flexible capillary can be customized according to individual needs, as well as other optional components. This ensures maximum flexibility in integrating the sensor into a wide range of industrial applications.
Echo™ Series - Combined sensor with rigid stem, flexible capillary and built-in temperature sensor
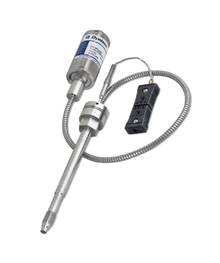
Combined pressure sensors with flexible capillaries represent a professional solution suitable for applications with limited space or exposure to radiant heat from heating elements in production lines. Thanks to the thoughtful extended design, the sensor's electronics are located out of reach of the radiant heat source, reducing the risk of damage.
Additionally, these sensors are equipped with a temperature sensor, allowing the customer to choose the type of sensor, whether it is a type J, K thermocouple, or an RTD (pt100). By selecting a compatible sensor for temperature measurement, the customer obtains information about the melt temperature from a single process connection, increasing measurement efficiency and accuracy.
The flexible capillary is designed to be resistant to damage and allow a high degree of bending, which facilitates installation and handling of the sensor. It is essential to properly secure the sensor head to the included adapter, which is part of the package. To achieve optimal performance, we recommend placing the adapter on a part of the machine where unwanted vibrations or shocks do not occur, as these could negatively affect the sensor.
The length of the rod and flexible capillary can be customized according to individual needs, as well as other optional components. This ensures maximum flexibility in integrating the sensor into a wide range of industrial applications.
Performance Characteristics
Input, Excitation: |
mV/V: 10VDC recommended, 12VDC max
VDC: 16-30VDC
mA: 14-30VDC |
Output, Analog: |
3.33mV/V, 0-10VDC, or 4-20mA |
Accuracy*: |
±0.5% FS |
Repeatability: |
±0.2 FSO |
Electronics Operating Temp, max: |
mV/V: 250°F (120°C); mA, VDC: 185°F (85°C) |
Overload Pressure Rating: |
1.5 x FSO |
Pressure Ranges (psi): |
0 - 15 000 PSI |
Pressure Ranges (Bar): |
0 - 1000 Bar |
Pressure Ranges (MPa): |
0 - 100 Mpa |
Pressure Units: |
PSI, Bar, Kg/cm2 , MPa, KPA |
Zero Balance Adjustment (±% FS): |
mV/V: na; VDC: ±15%; mA: ±20% |
Zero Balance Setting (±% FS): |
mV/V: ±10%; VDC, mA: ±0.5% |
Bridge Resistance: |
mV/V: 345Ω, min |
Insulation Resistance: |
mV/V: 1000 MΩ @50VDC; VDC, mA: 100 MΩ @50VDC |
Internal Shunt Calibration (R-Cal): |
80% FSO ±1.0% FSO |
Mechanical & Packaging
Sensor Technology: |
4-arm bonded foil strain gage Wheatstone bridge |
Diaphragm Temperature: |
662°F (350°C) for Rigid; 752°F (400°C) for Flex |
Zero Shift (process temp change) Mercury: |
25 psi/100°F (45psi/100°C), nominal |
Zero Shift (process temp change) NaK: |
43 psi/100°F (90psi/100°C), nominal |
Diaphragm Wetted Parts: |
17-4 PH SST |
Electrical Connection: |
6 pin or Hirschmann |
Process Connection: |
1/2-20 UNF thread (45° conical seal) M14, M18, M22 |
Mounting Torque: |
250 in/lbs, max |
Temperature Sensor (optional): |
J or K-type thermocouple with 3 inch flex, PT100 RTD |
Approvals & Certifications
CE: |
Directive 2004/108/EC |
Recommended Accessories
Mounting Hole Matching Tool Kit: |
Part Number 200925 |
6-pin Bendix Mating Connector: |
Part Number 711600 |
Mounting Bracket (Electronics): |
Part Number 200941 |
Cable Assemblies, Indicators, Controllers: |
Consult distributor or Dynisco |
Replacement Thermocouples: |
|
K Type 6" Snout |
Item Number HY001715 |
J Type 6" Snout |
Item Number HY001722 |
J Type 9" Snout |
Item Number HY001723 |
J Type 12" Snout |
Item Number HY001724 |
PT100 RTD 6" Snout |
Item Number HY001726 |
*Accuracy is defined as the combined error expressed as a percentage of full scale output. Combined error includes linearity (BSL), as defined in ISA-S37.1. **To avoid bending a 6" snout using a 12" wrench, do not apply more than listed torque without supporting bending moment. When applying torque to a snout longer than 12", counteract the bending moment with a support.
Ordering Guide for Echo™ Series with Mercury
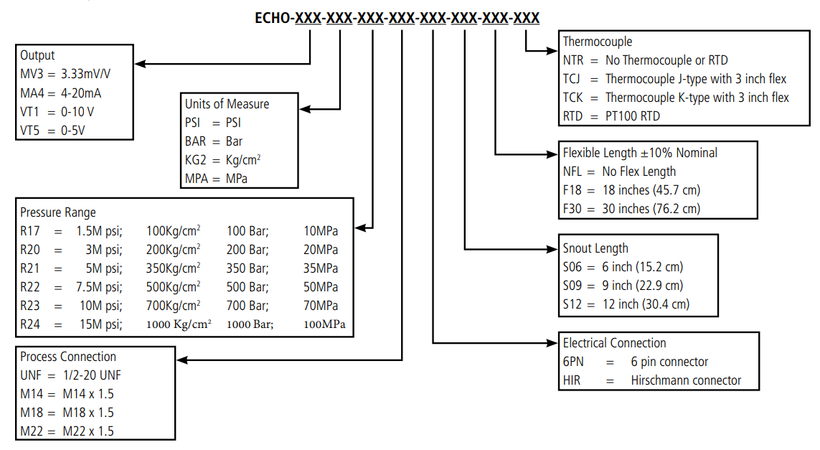
Ordering Guide for Echo™ Series with Mercury
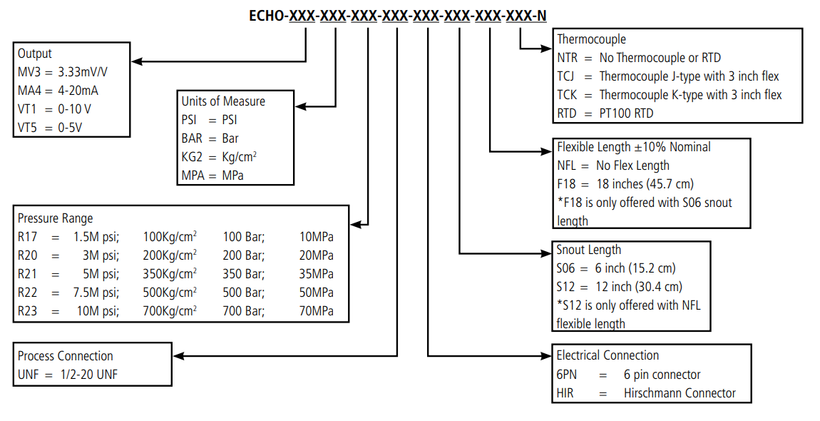
Echo™ Series - With rigid stem - Dimensions
All dimensions are inches (mm) unless otherwise specified.
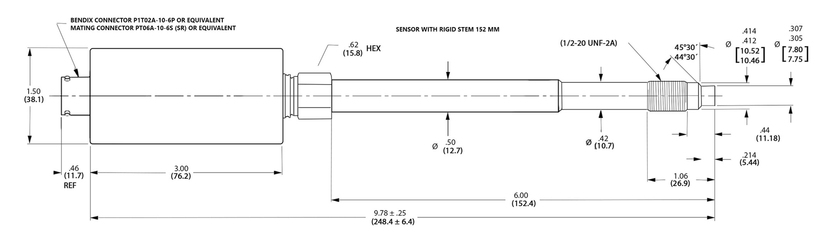
Echo™ Series - With flexible capillary - Dimensions
All dimensions are inches (mm) unless otherwise specified.
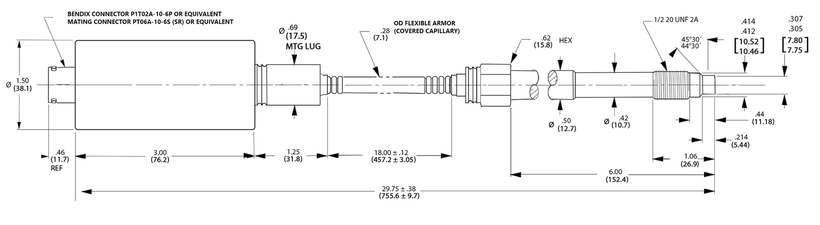
Echo™ Series - Combined sensor - Dimensions
All dimensions are inches (mm) unless otherwise specified.
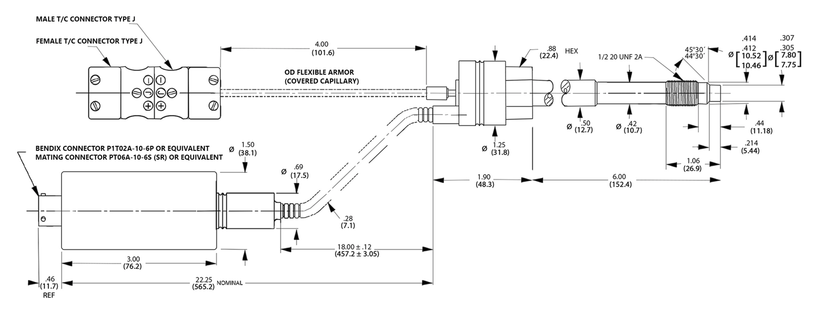