Providing Innovative Solutions
With more than 6 decades of commitment to helping customers, Dynisco provides the tools and services for the polymer industry allowing customers a “window into the process”.
Today’s customers require accurate information that will allow them to validate and if necessary adjust their process ensuring the products they make meet or exceed their specifications. The information Dynisco provides allows our customers to keep their process consistent regardless of their global locations.
Dynisco’s diverse portfolio of sensing and polymer test equipment delivers some of the most accurate information available in the market for the measurement of polymer rheology, pressure, and temperature.
Dynisco provides our customers the ability to correlate the data derived from pilot to laboratory environments with online production, 24 hours a day. This data allows for immediate response and adjustment to critical parameters ensuring any variations are promptly corrected to guarantee quality while maximizing their output.
Dynisco History
Known worldwide for leading-edge pressure and temperature measurement and control products for the plastics extrusion industry, Dynisco has been developing innovative, high-quality solutions for plastics extrusion processing for 60 years built on the expertise of an engineering staff that averages 15-20 years experience. Dynisco sensors, controls, and analytical instruments have proven to offer better control, reduced downtime, minimum scrap, and unmatched reliability and working life. Our dedication and ability to collaborate with you to help you measure, analyze and outfit extrusion control systems that fit your exact needs are unmatched. From breakthrough technology in the industry’s most complete line of sensors to renowned quality and performance in indicators, controls, and analytical instruments.
Dynisco Sensors Designed specifically for the rugged environment of the plastic industry, Dynisco has developed some of the most innovative measurement solutions for plastic extrusion, molding and process control applications. Manufacturing a wide range of robust mV/V, mA, VDC and HART-compatible melt pressure sensors, through engineering excellence built on expertise and experience.
Dynisco Analytical Instruments Process quality begins with the material being used. Dynisco's analytical instruments allow the processor to verify material specifications and optimize process conditions. These instruments include melt flow
[Dynisco Heilbronn Germany Facility]
indexers, capillary rheometers, and small laboratory mixing extrusion systems. Dynisco also offers the most comprehensive and accurate line of online rheometers available in the market today.
Dynisco offers a full range of global service and technical support for our complete line. Dozens of highly skilled, technical support personnel are stationed internationally to provide:
- Expert consultation
- Custom design solutions
- On-site equipment diagnostics and trouble-shooting
- Transducer repair and maintenance ∙ Installation services
- Operator training for equipment ∙
- System repairs, replacement parts, preventive maintenance and more
Customers around the world have come to depend on Dynisco for product innovation and advanced system solutions that have a significant impact on their manufacturing process efficiencies.
PT199 Pressure sensor
The PT199 pressure sensor is designed to measure pressure on turbine systems. Provides information on pressure or temperature in gas or fuel systems such as gas turbines to regulate gas or fuel flow.
Stainless steel construction
Adjustable zero and upper range
Excellent temperature compensation
Ranges 0-15 PSI to 0-15000 PSI
Advanced electronic design
Accuracy ±0.25% PT199B, PT199S, APT199S
Accuracy ±0.5% PT199
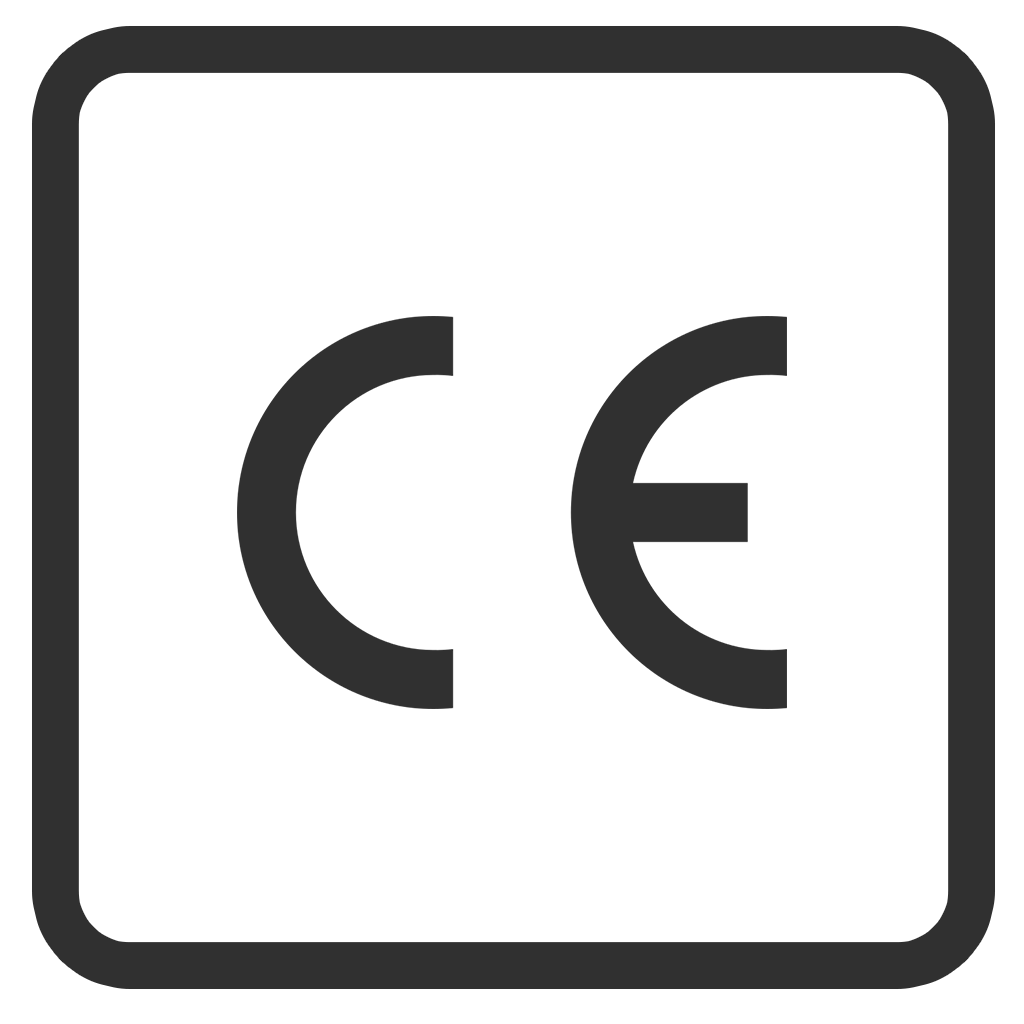
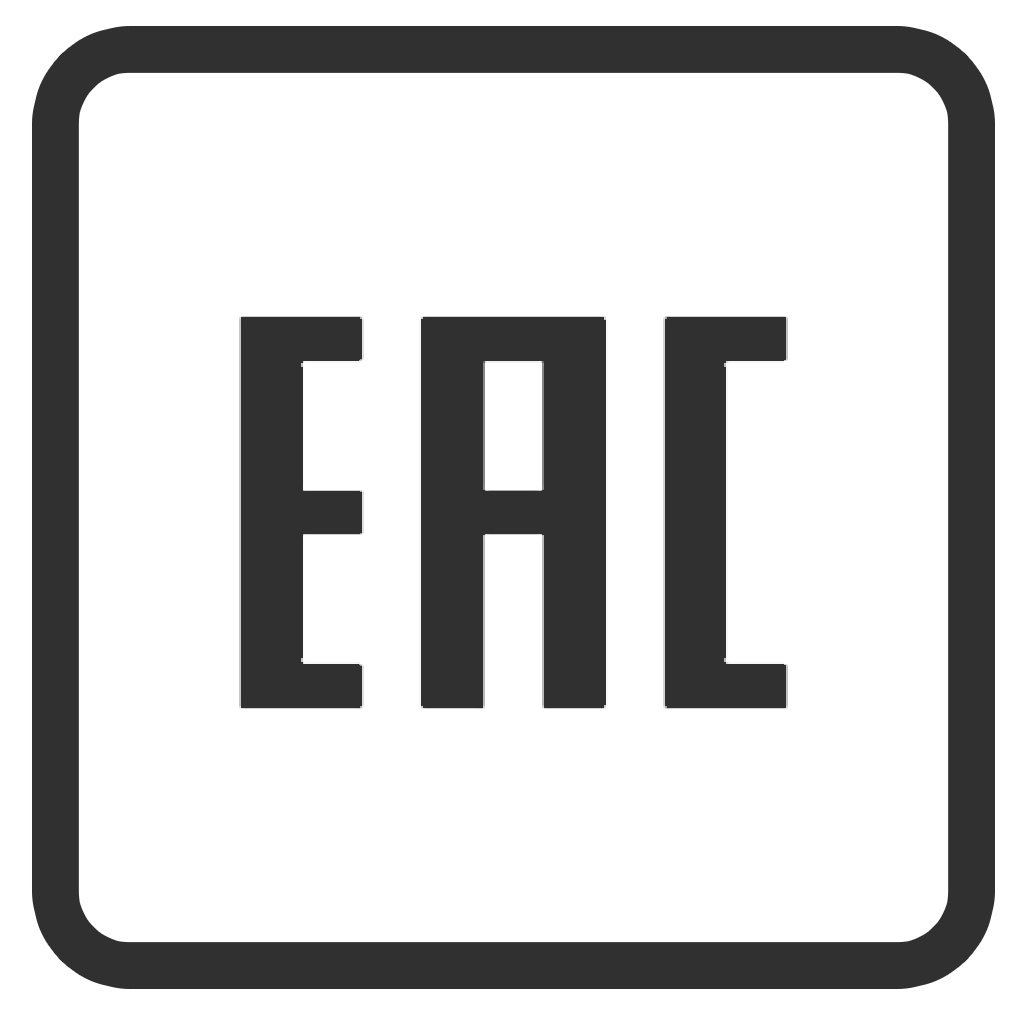
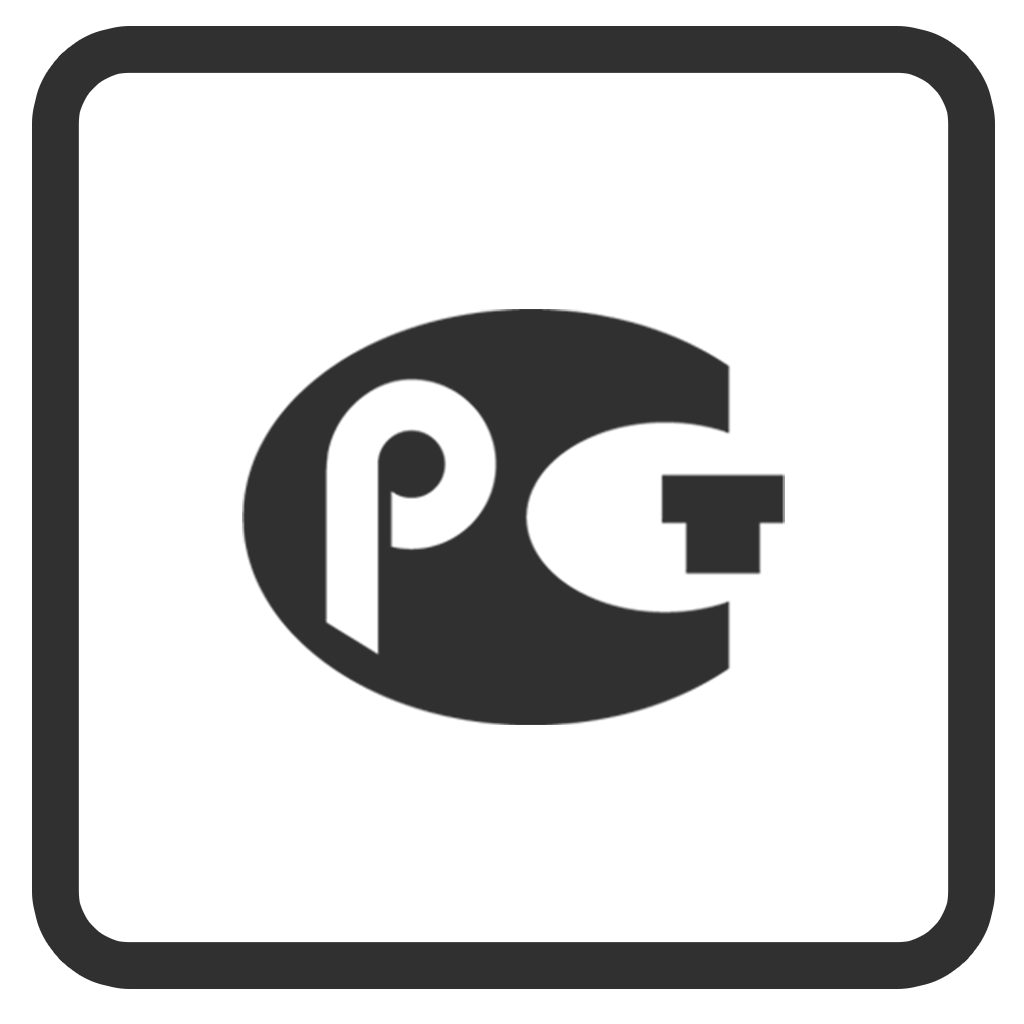
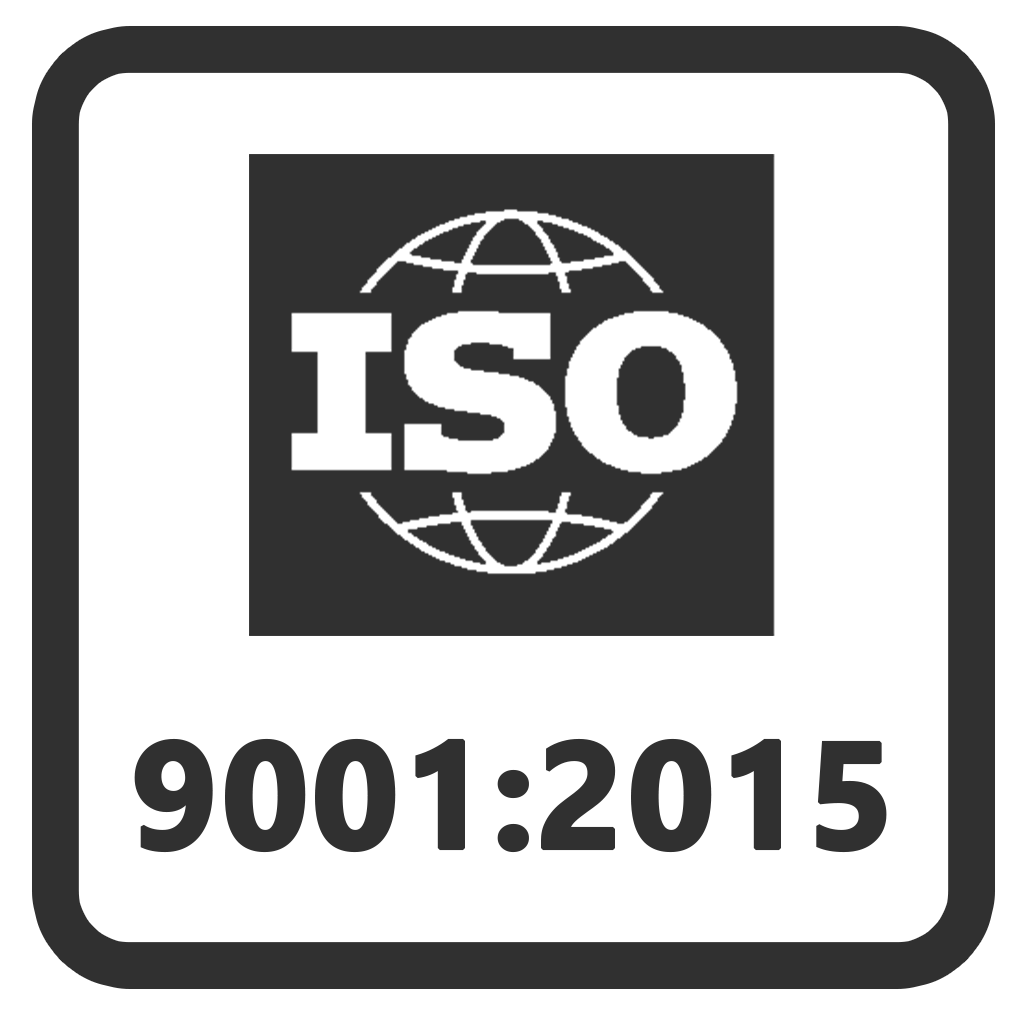
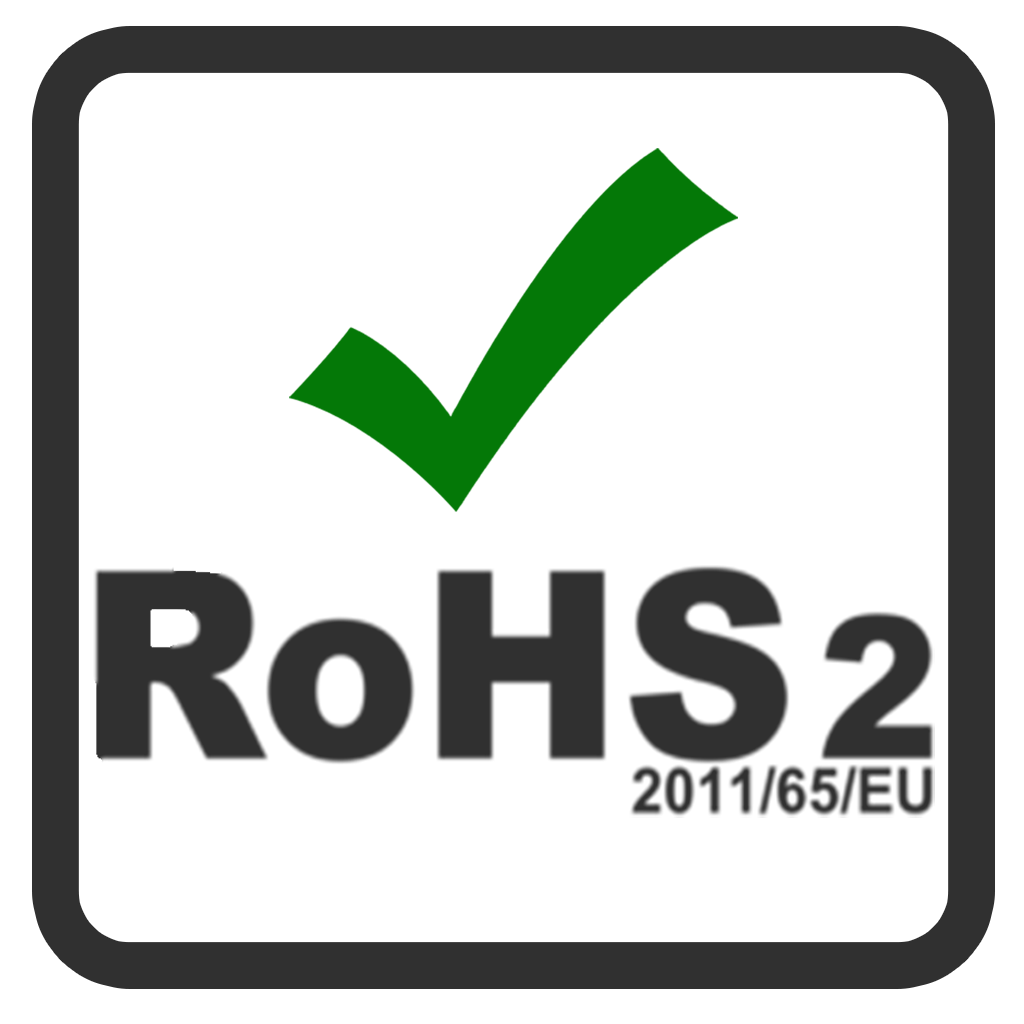
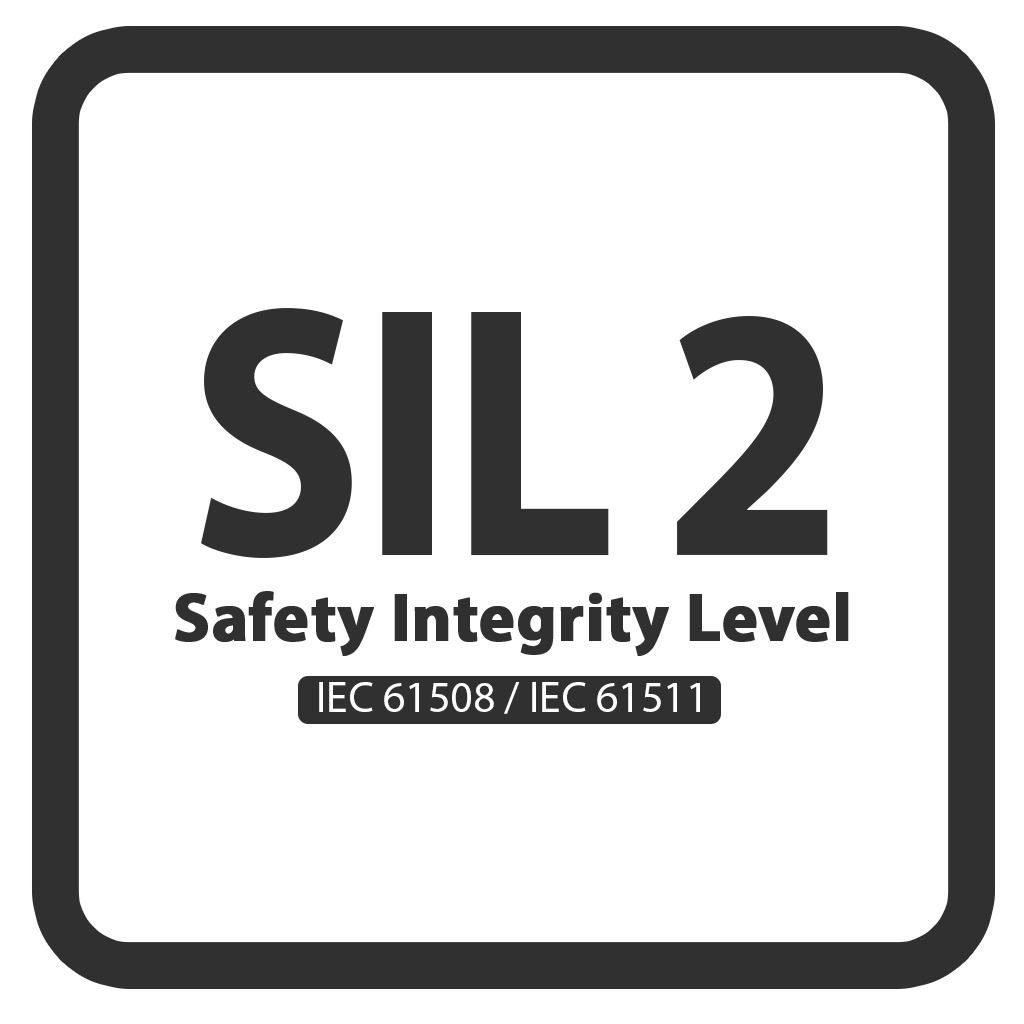
PT139 | PT139A
Dynisco PT139 and PT139A pressure sensors are designed to measure hydraulic pressure in extreme conditions for testing vehicles, stands and other hydraulic and pneumatic applications. These sensors withstand cyclic pressure and provide excellent performance during demanding industrial conditions.
Full power 3 mV/V
Accuracy better than ± 0.5%
The pressure range is from 0-15 PSI to 0-10,000 PSI
Pressure and vacuum support
Extended operating temperature range
Fully welded stainless steel construction
It resists strong shocks and vibrations
Internal 80% calibration
CE approval
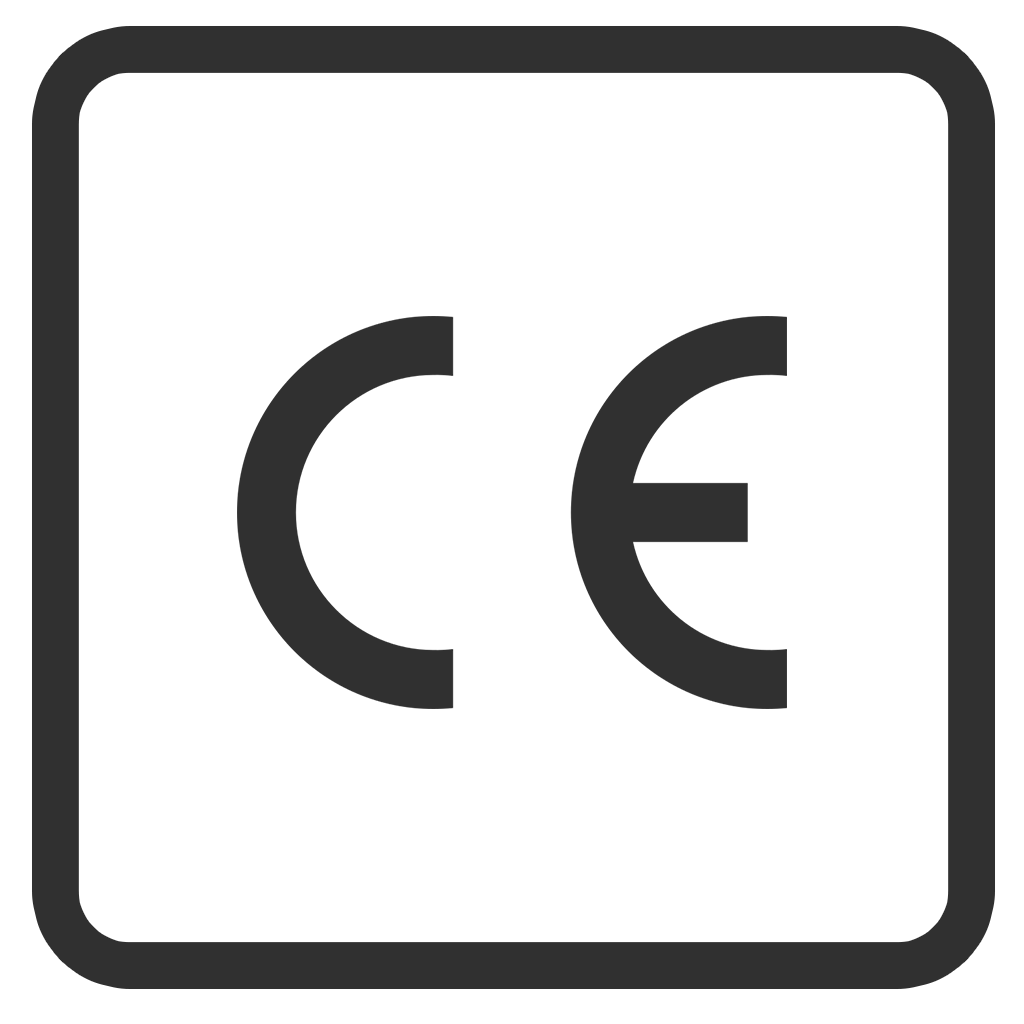
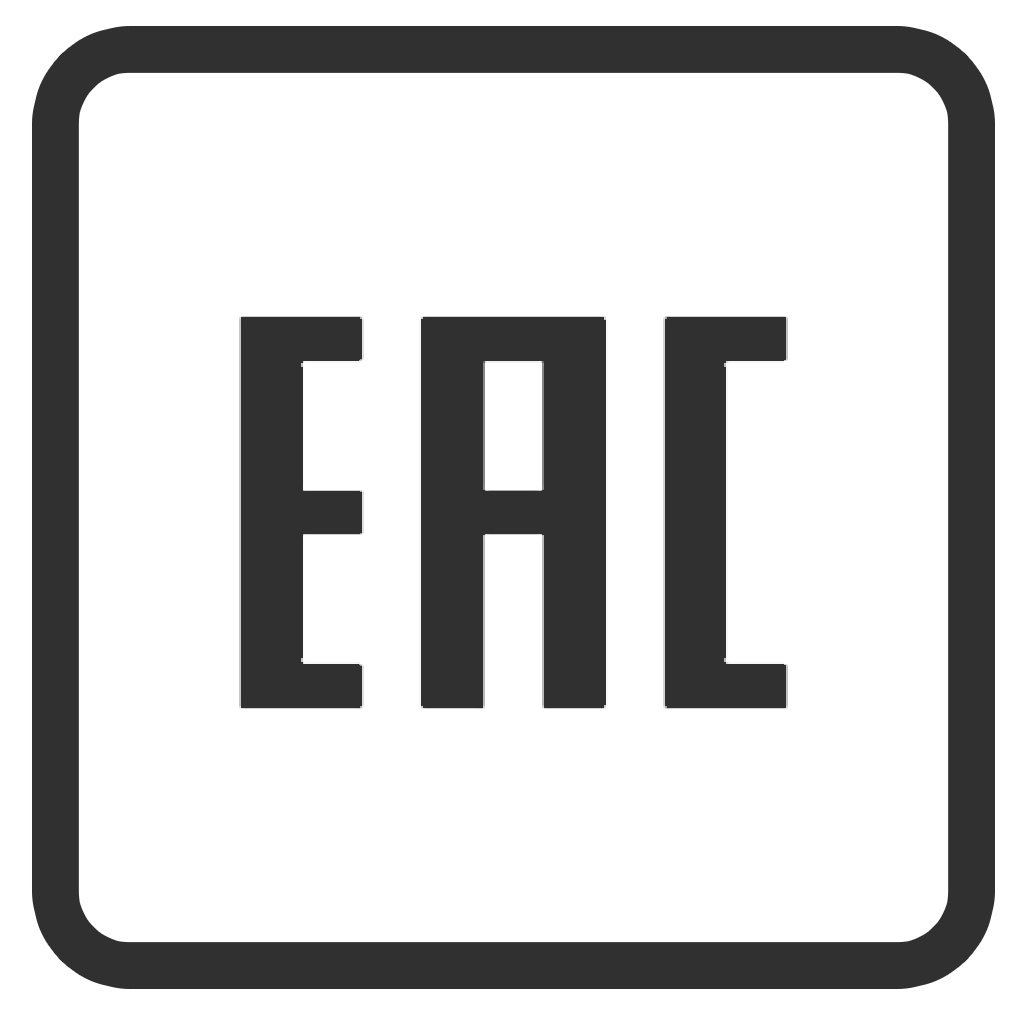
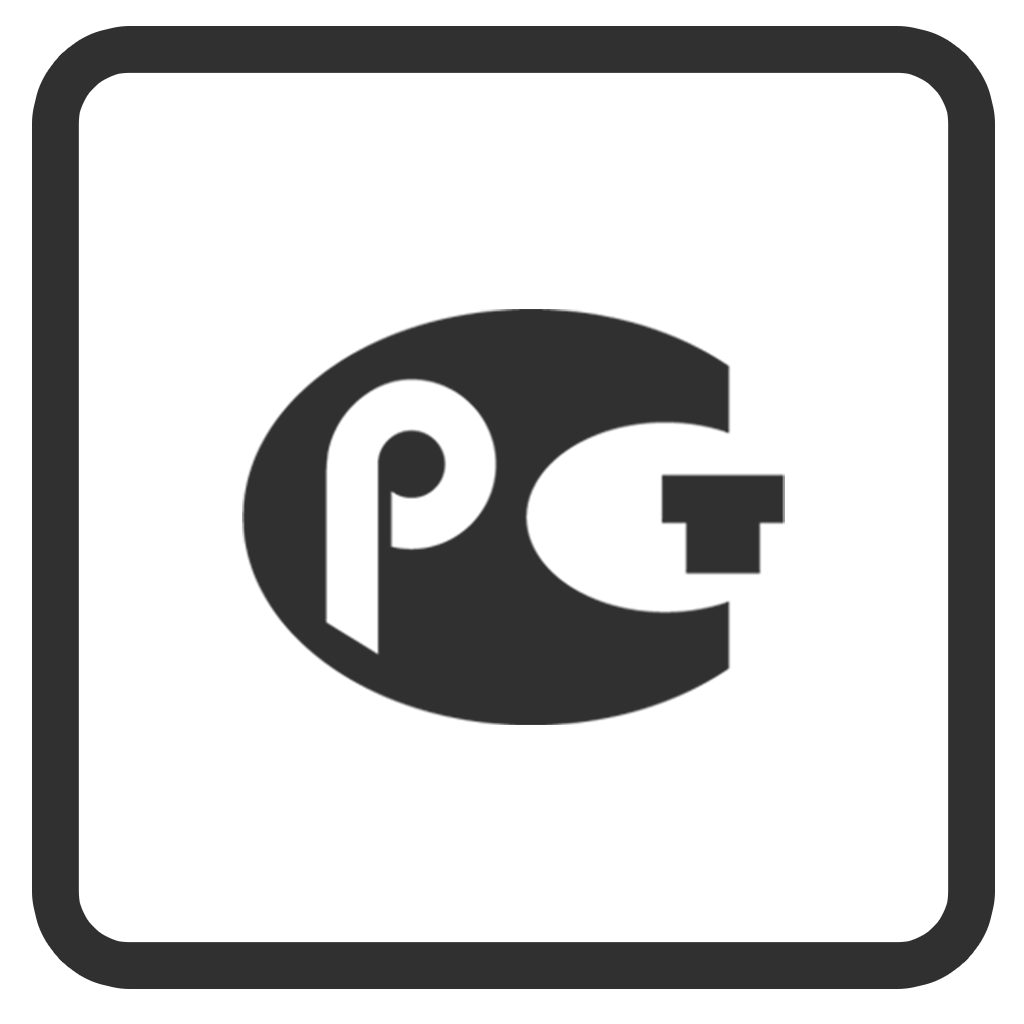
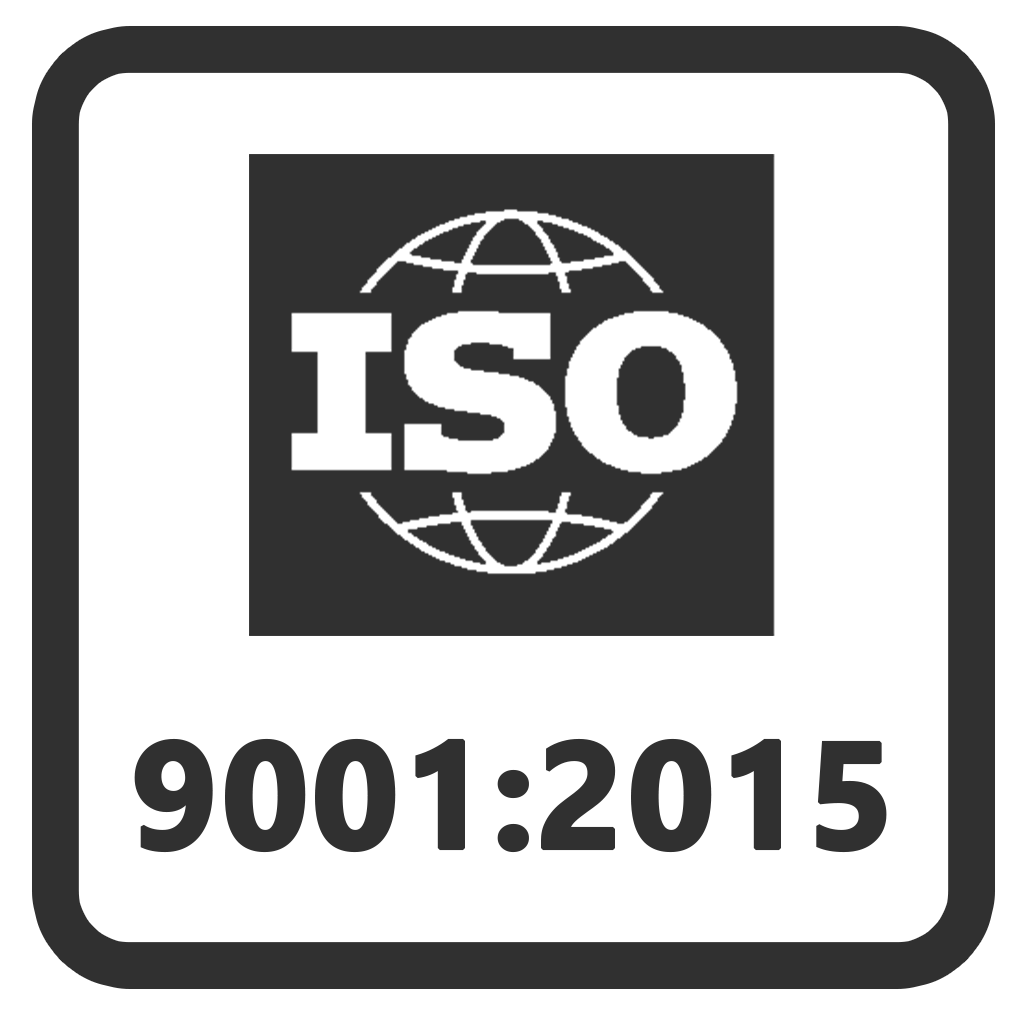
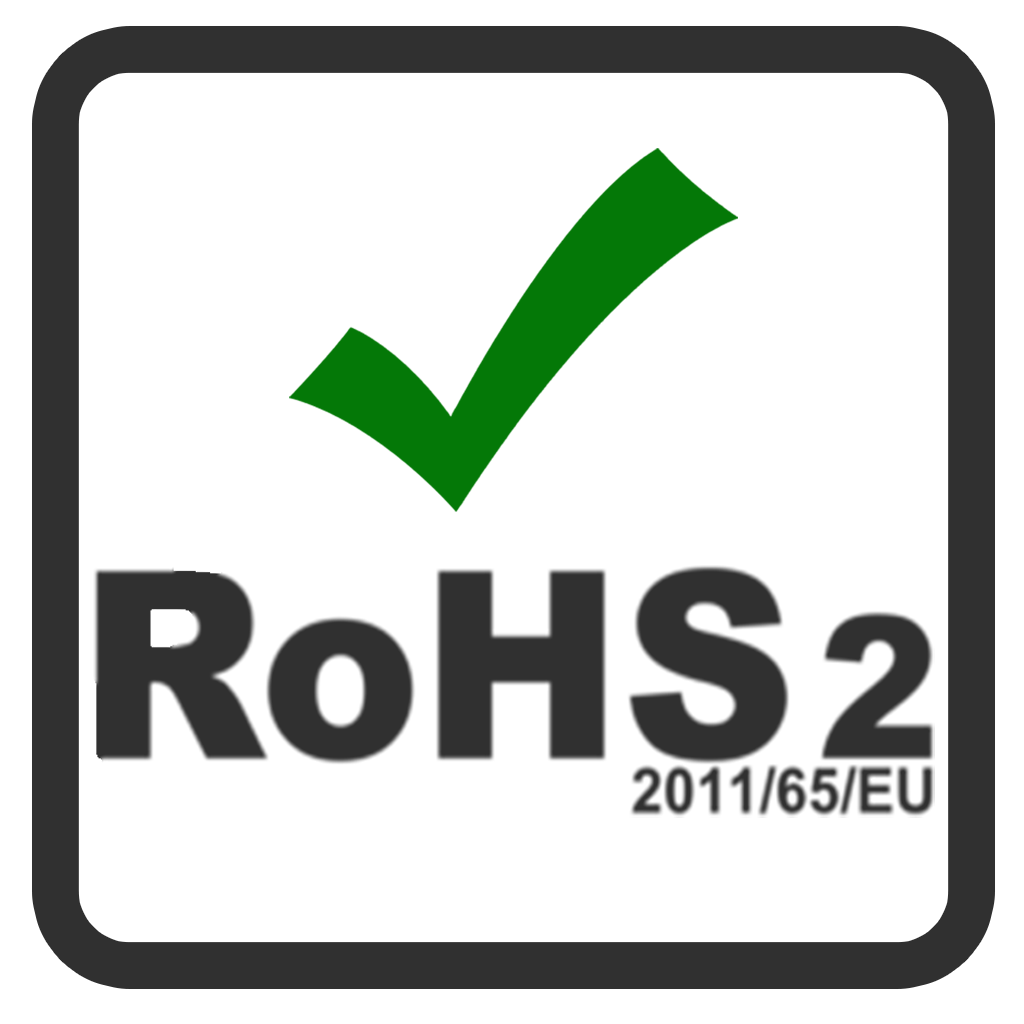
PT4656XL
The PT4656XL models represent an optimal solution for precise melt pressure measurement in nozzles or distribution channels within injection molding applications.
The flexible capillary extends from its electronic housing to the positioned tip in the machine melt, ensuring exceptional durability and prolonged sensor lifespan thanks to its robust construction.
1 "bending radius
Inconel 718 membrane
Cap nut for easy installation
Scanning accuracy ± 0.5%
Usable up to 400°C
Zero and range calibration
Optional output signal
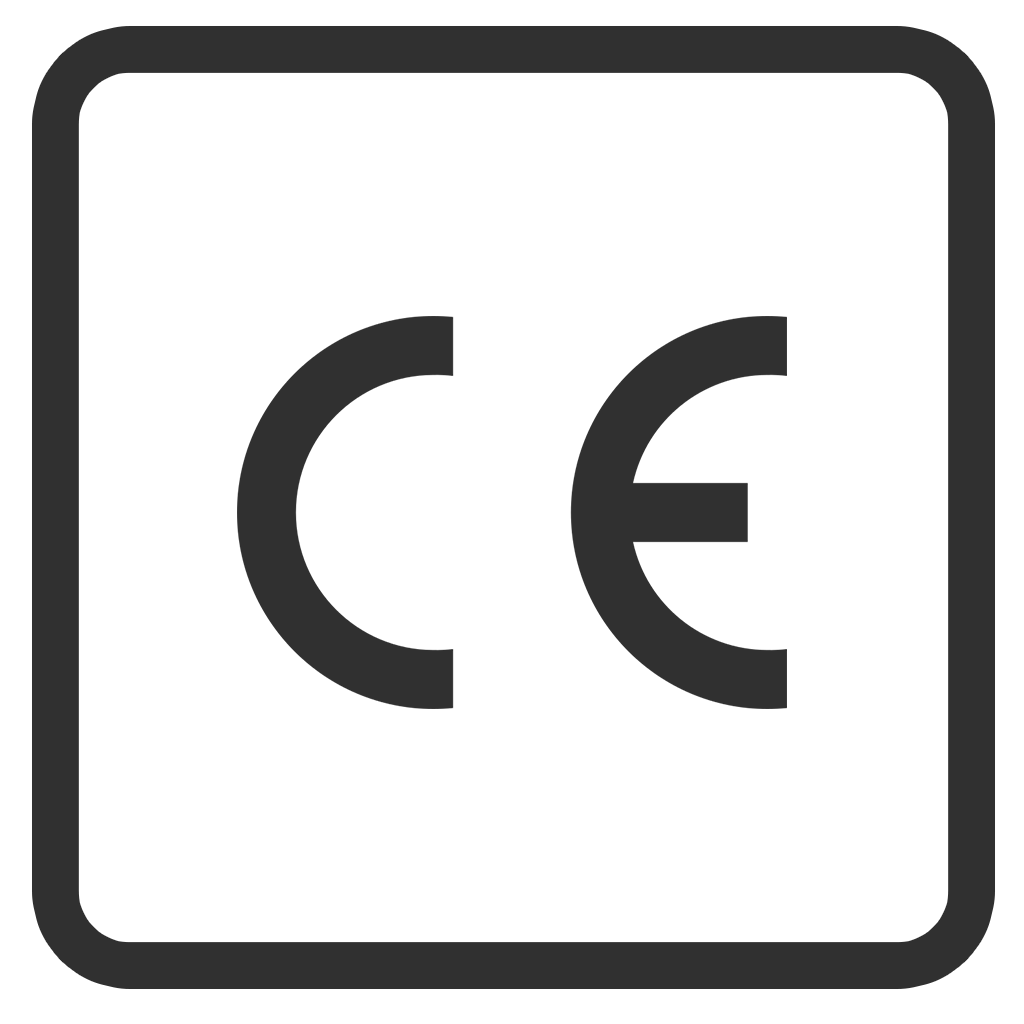
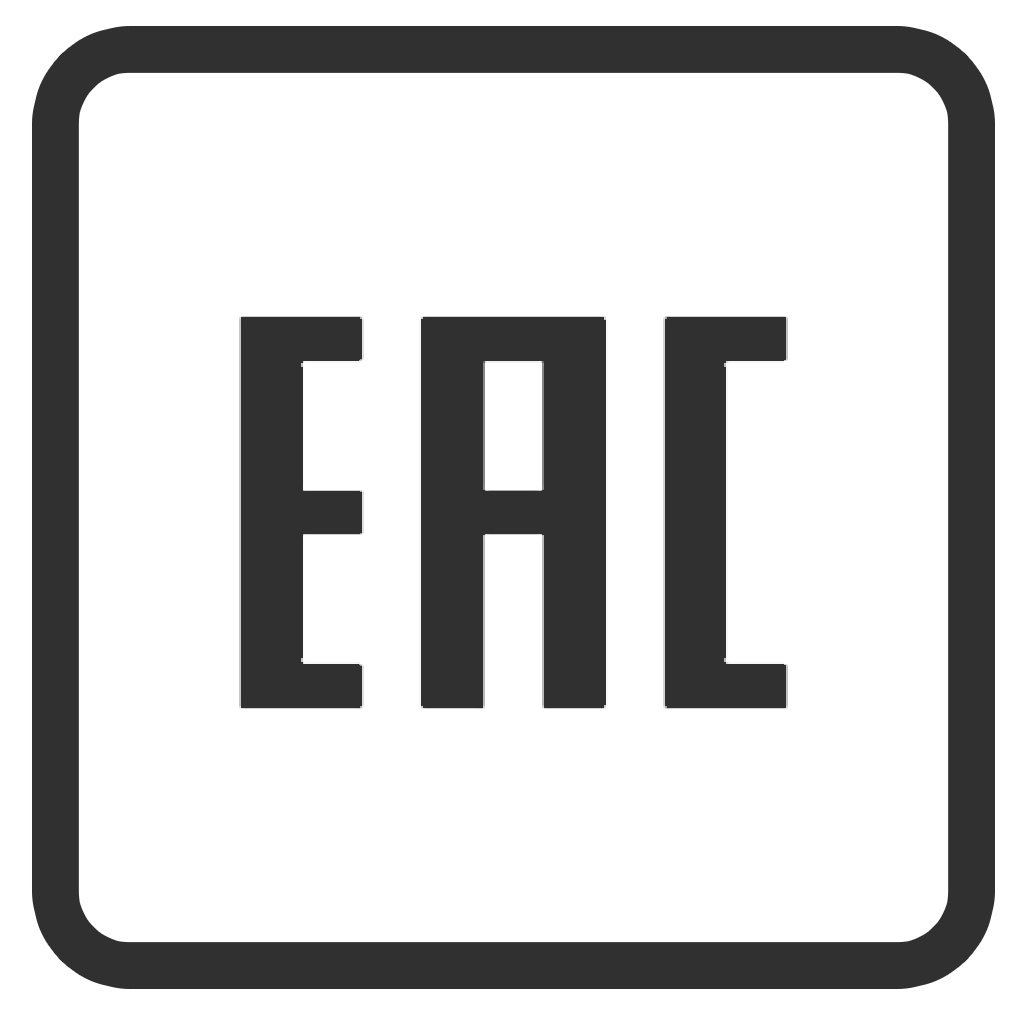
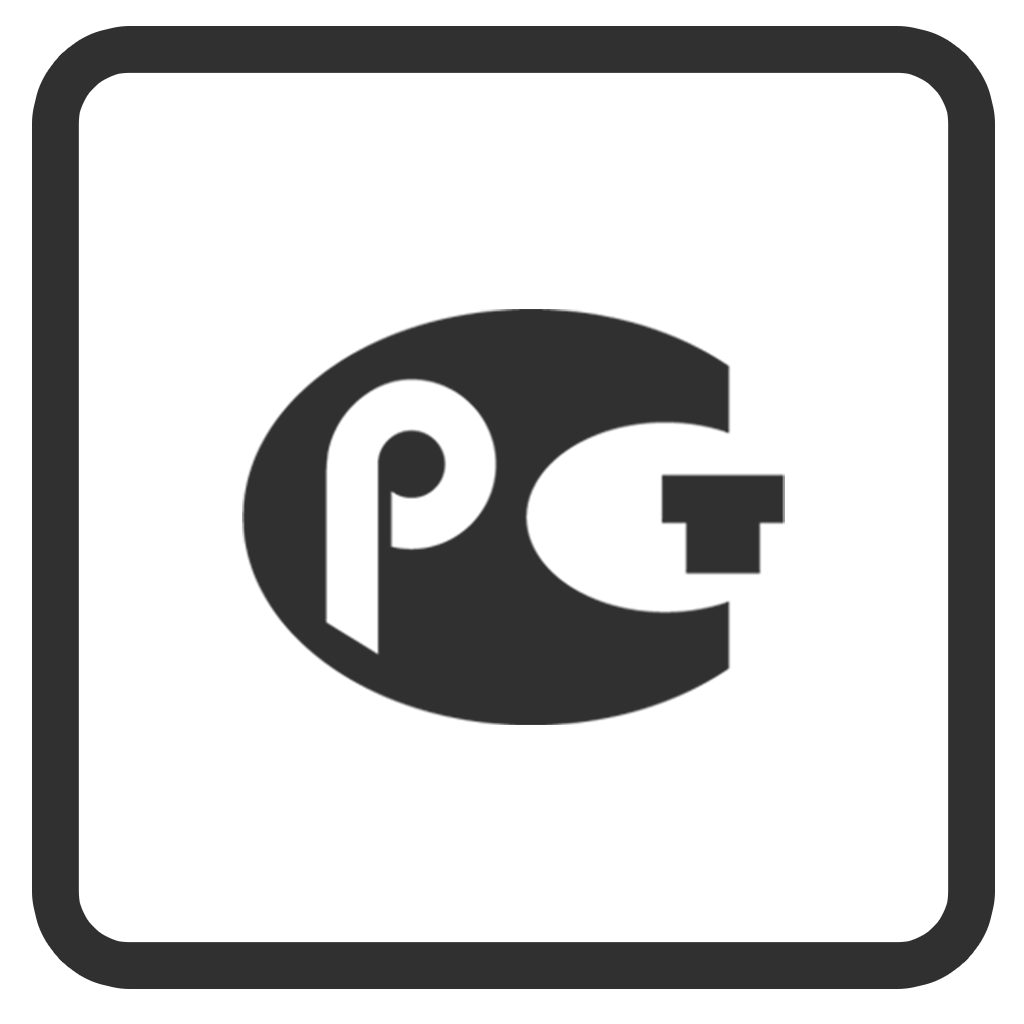
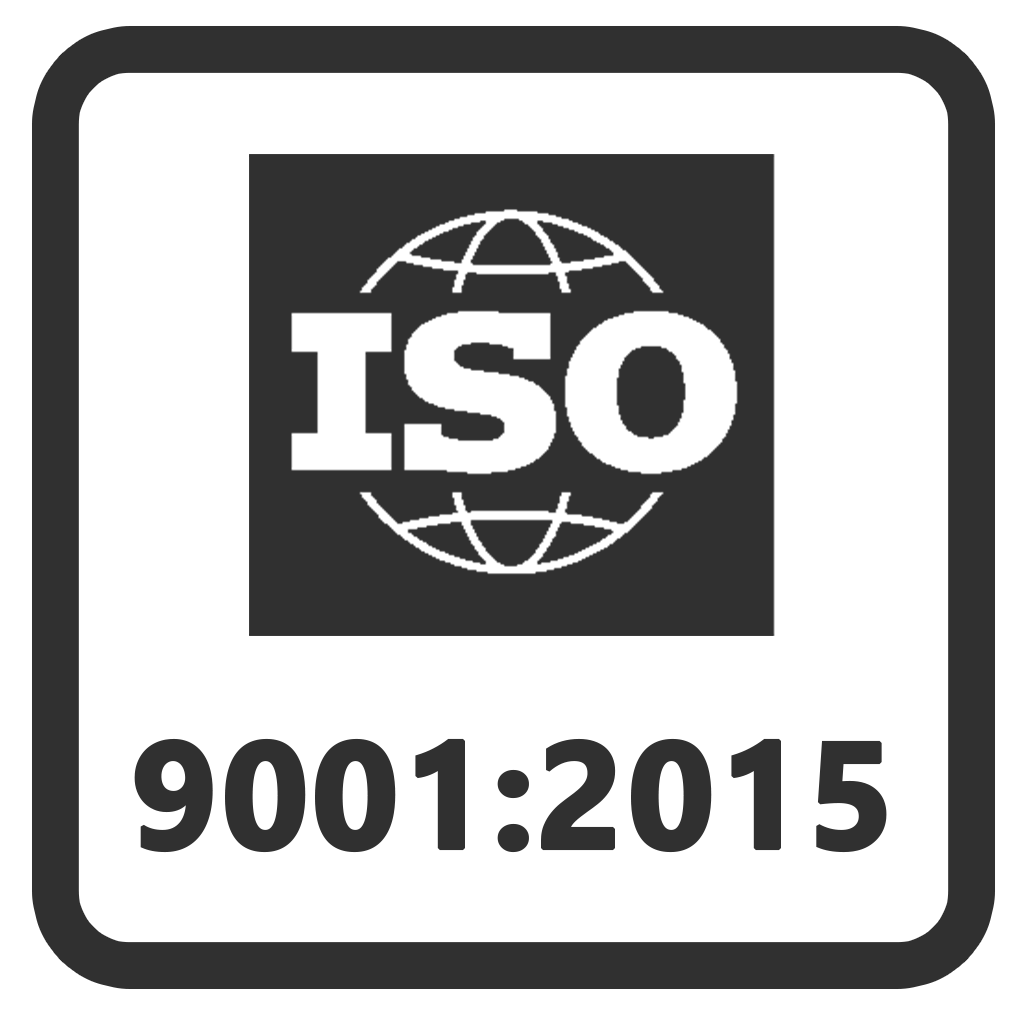
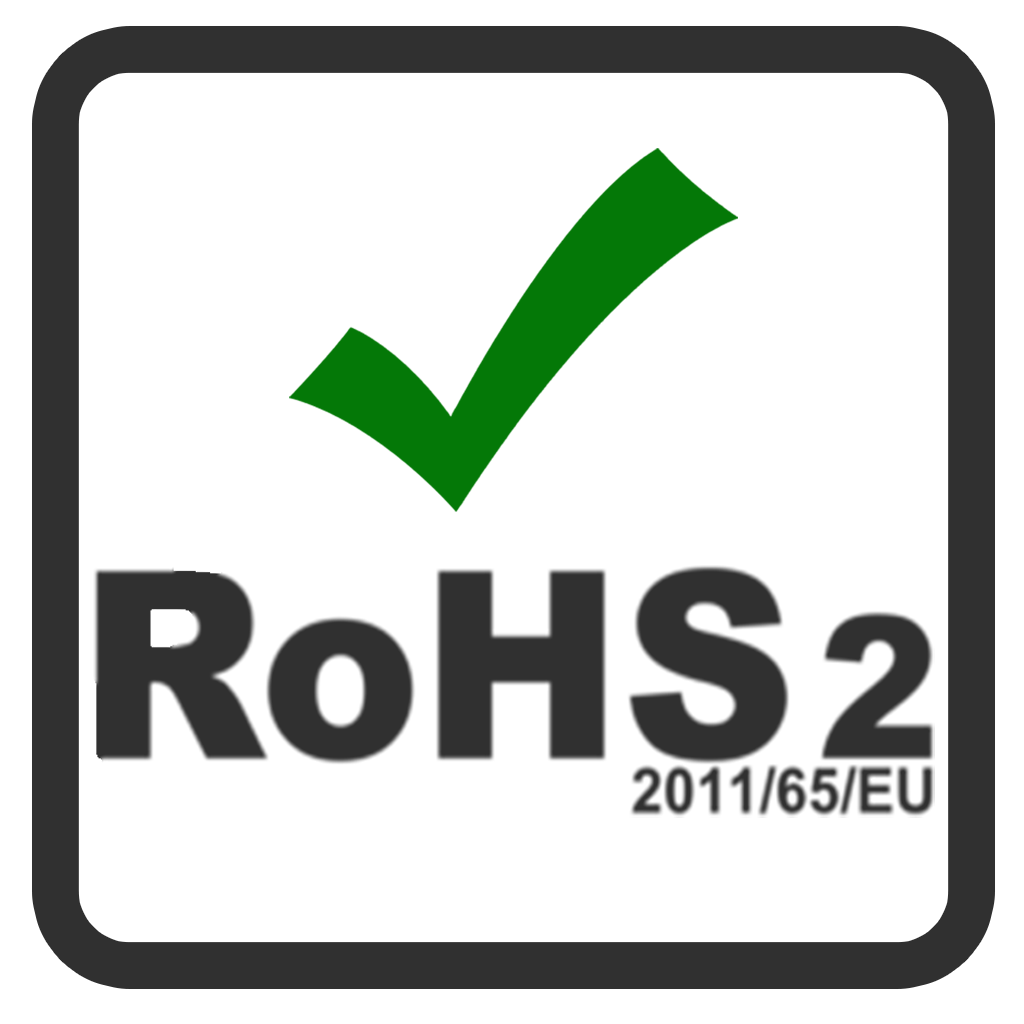
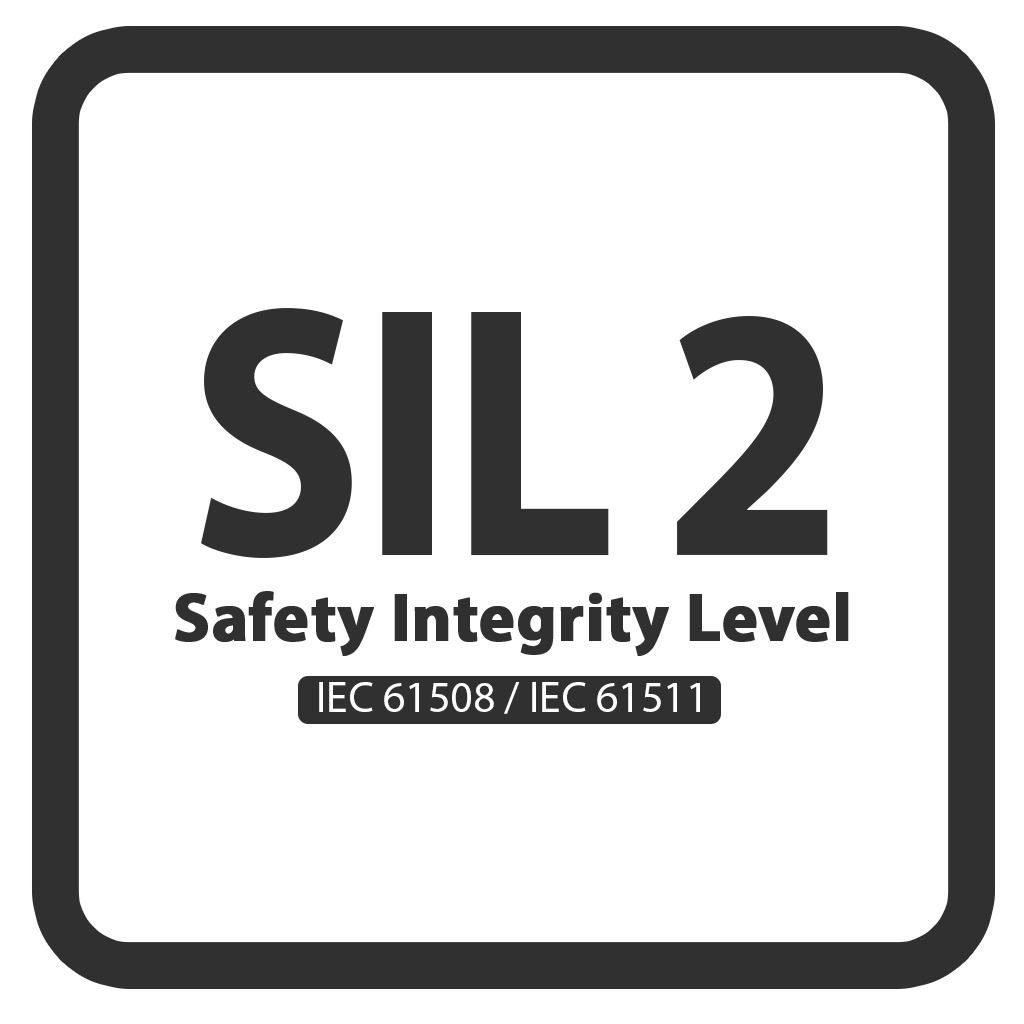
PT4655XL
The PT4655XL models represent an optimal solution for precise melt pressure measurement in nozzles or distribution channels within injection molding applications.
The flexible capillary extends from its electronic housing to the positioned tip in the machine melt, ensuring exceptional durability and prolonged sensor lifespan thanks to its robust construction.
1 "bending radius
Inconel 718 membrane
Cap nut for easy installation
Scanning accuracy ± 0.5%
Usable up to 400°C
Zero and range calibration
Optional output signal
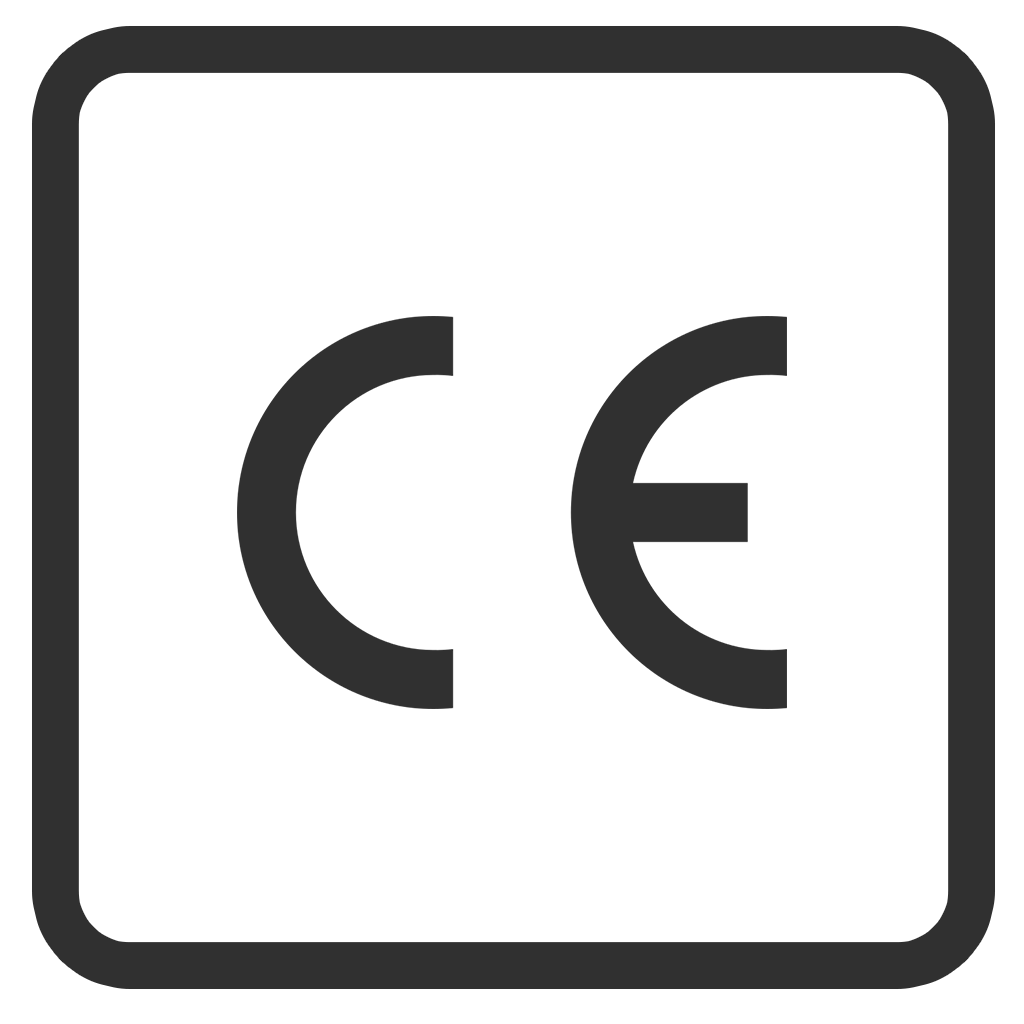
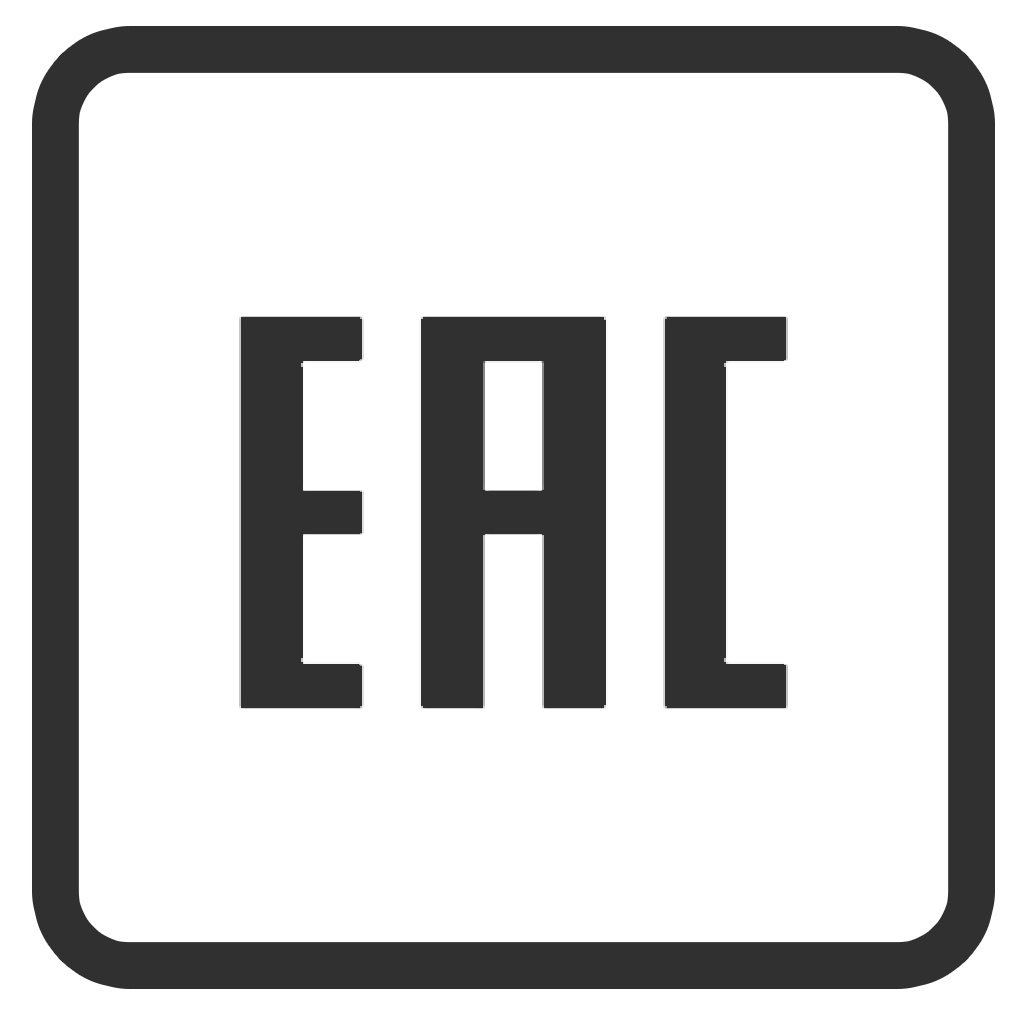
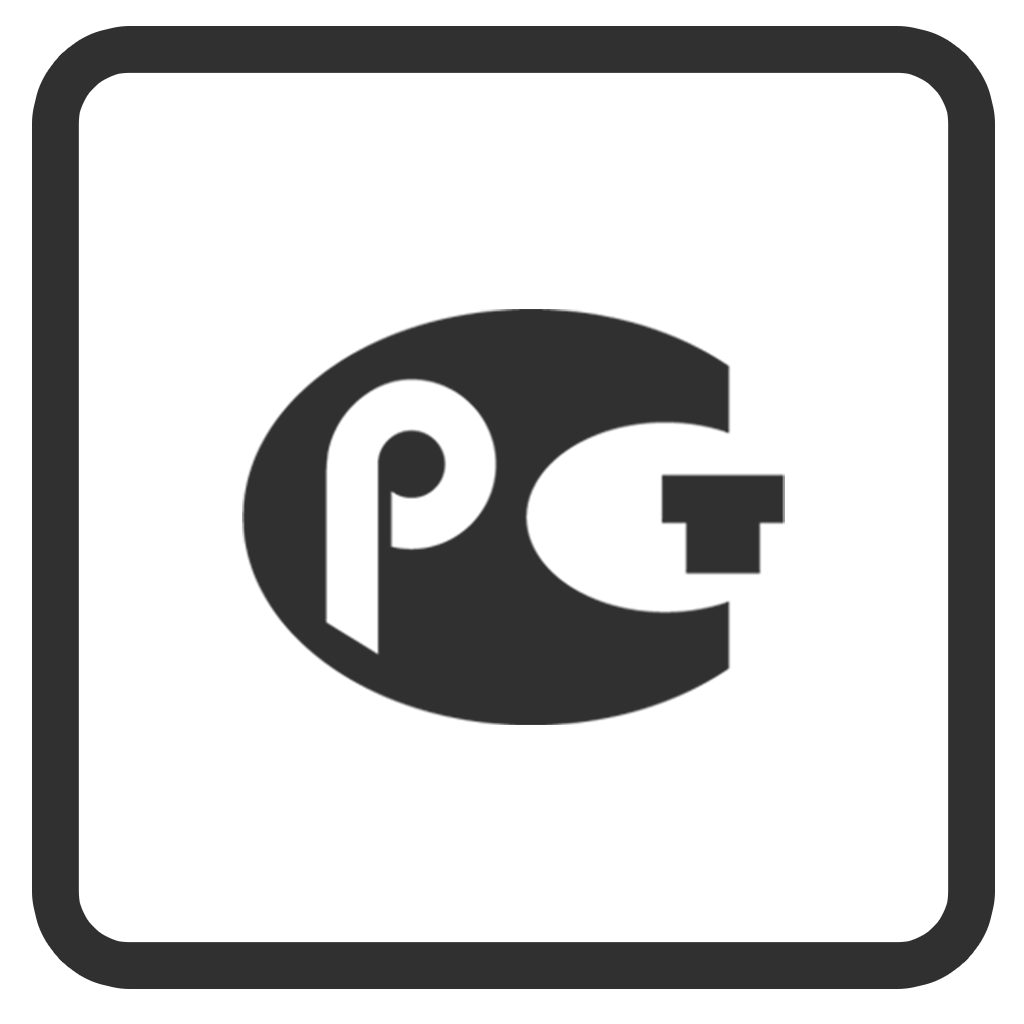
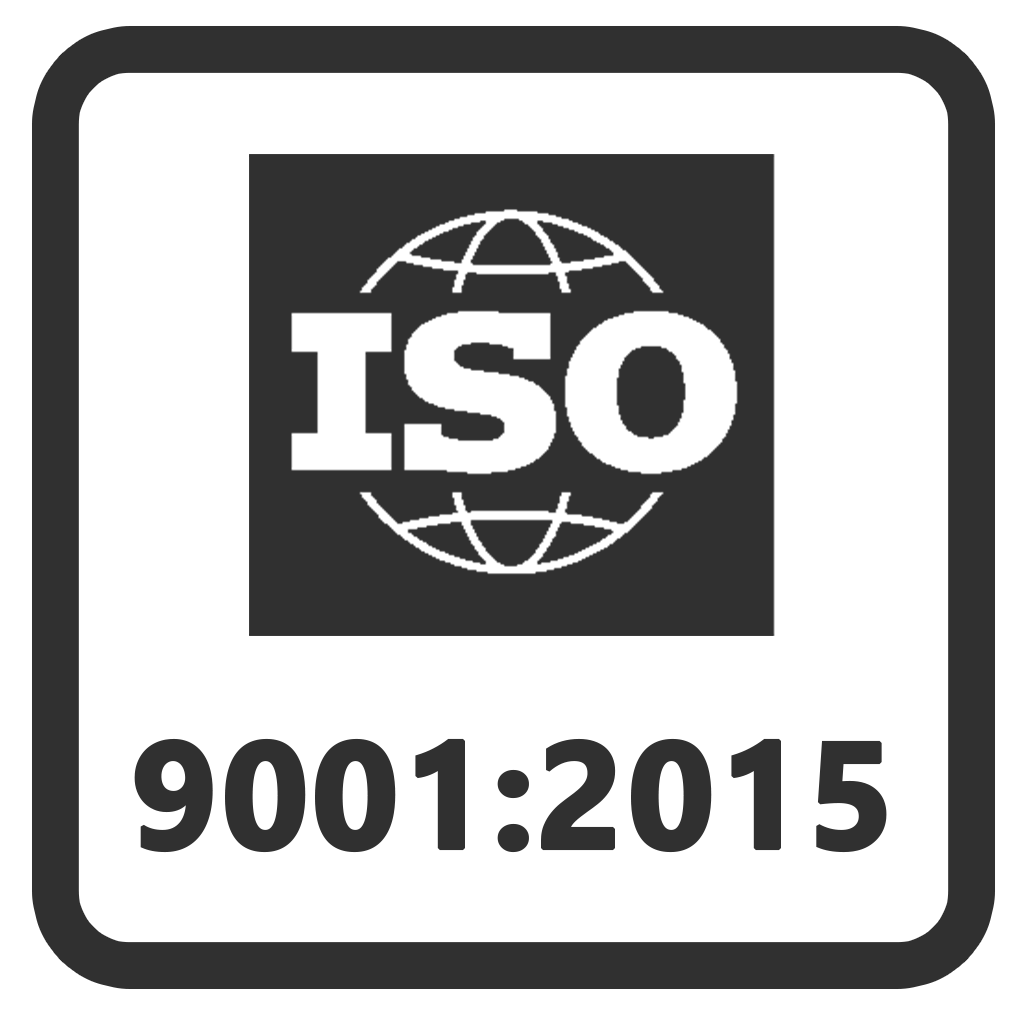
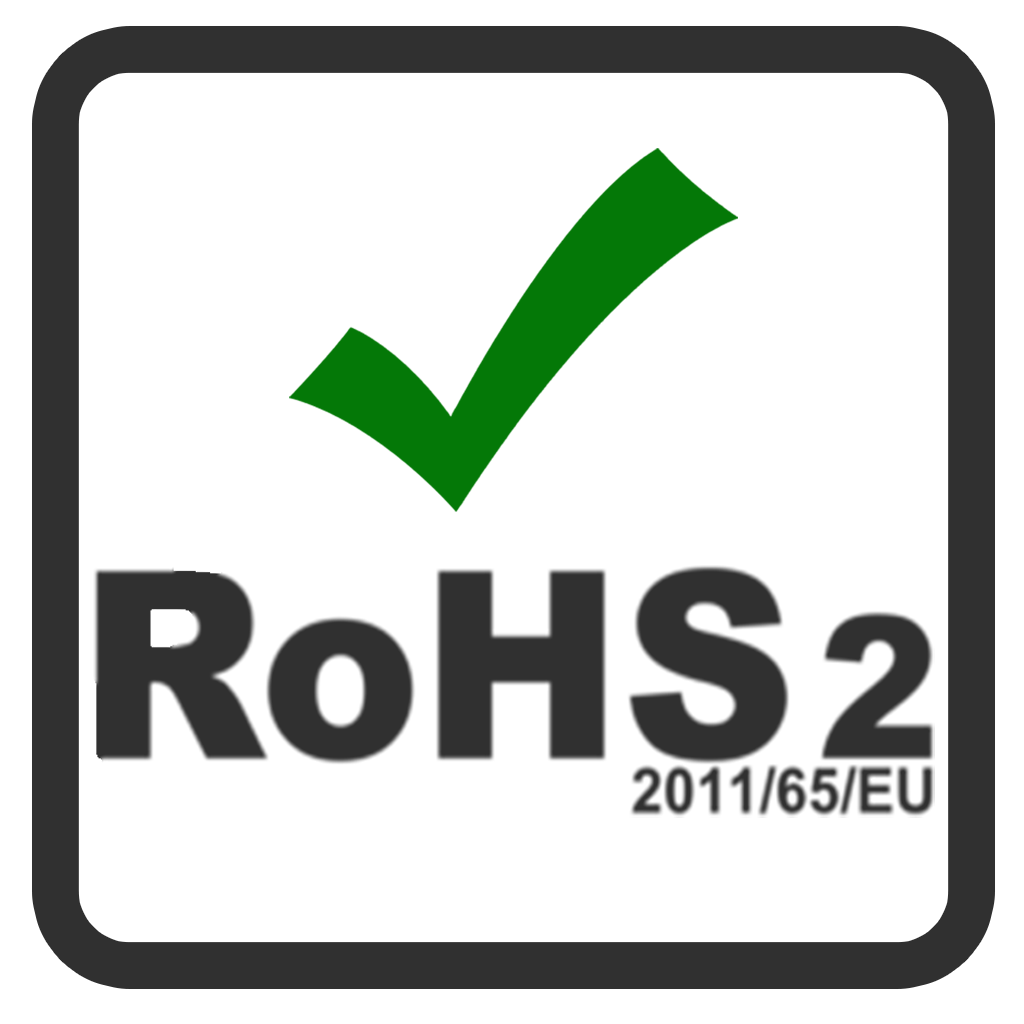
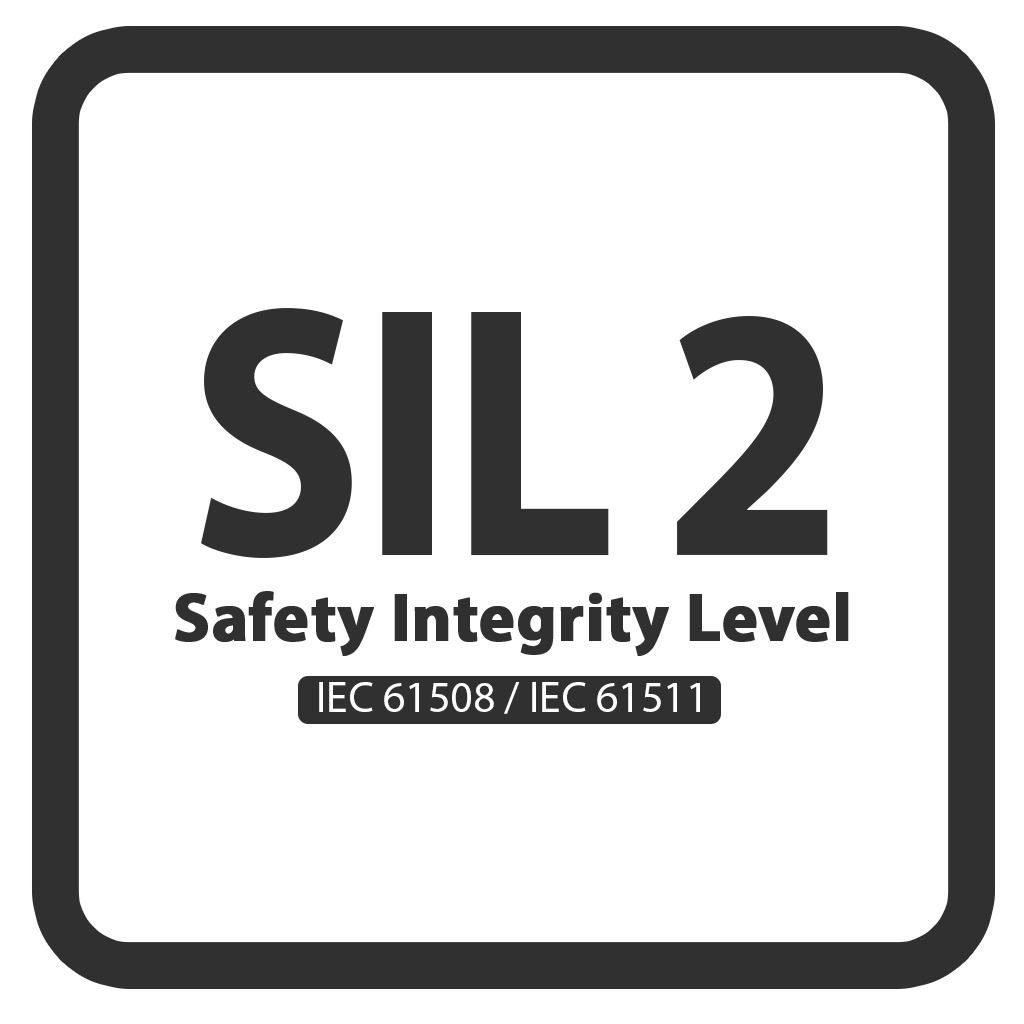
PT4654XL
The PT4654XL models represent an optimal solution for precise melt pressure measurement in nozzles or distribution channels within injection molding applications.
The flexible capillary extends from its electronic housing to the positioned tip in the machine melt, ensuring exceptional durability and prolonged sensor lifespan thanks to its robust construction.
1 "bending radius
Inconel 718 membrane
Cap nut for easy installation
Scanning accuracy ± 0.5%
Usable up to 400°C
Zero and range calibration
4-20mA output signal
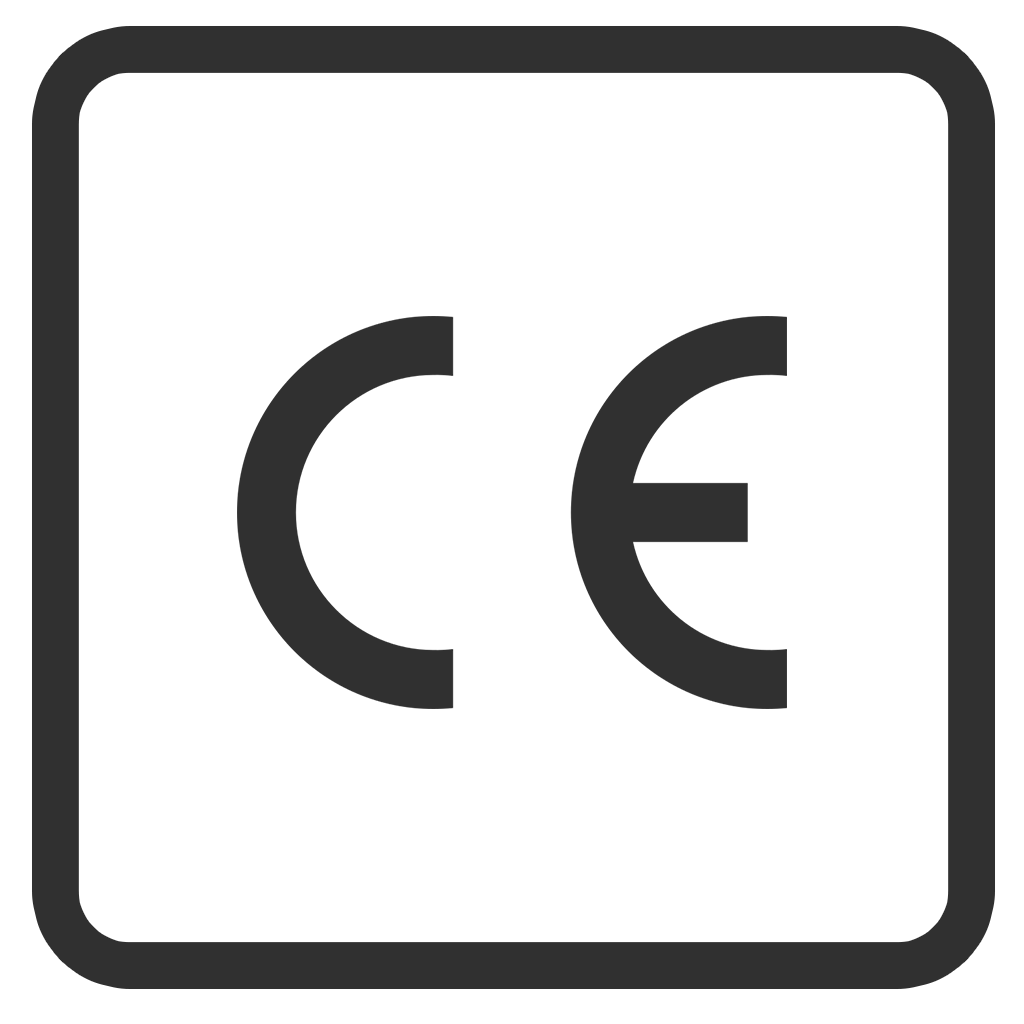
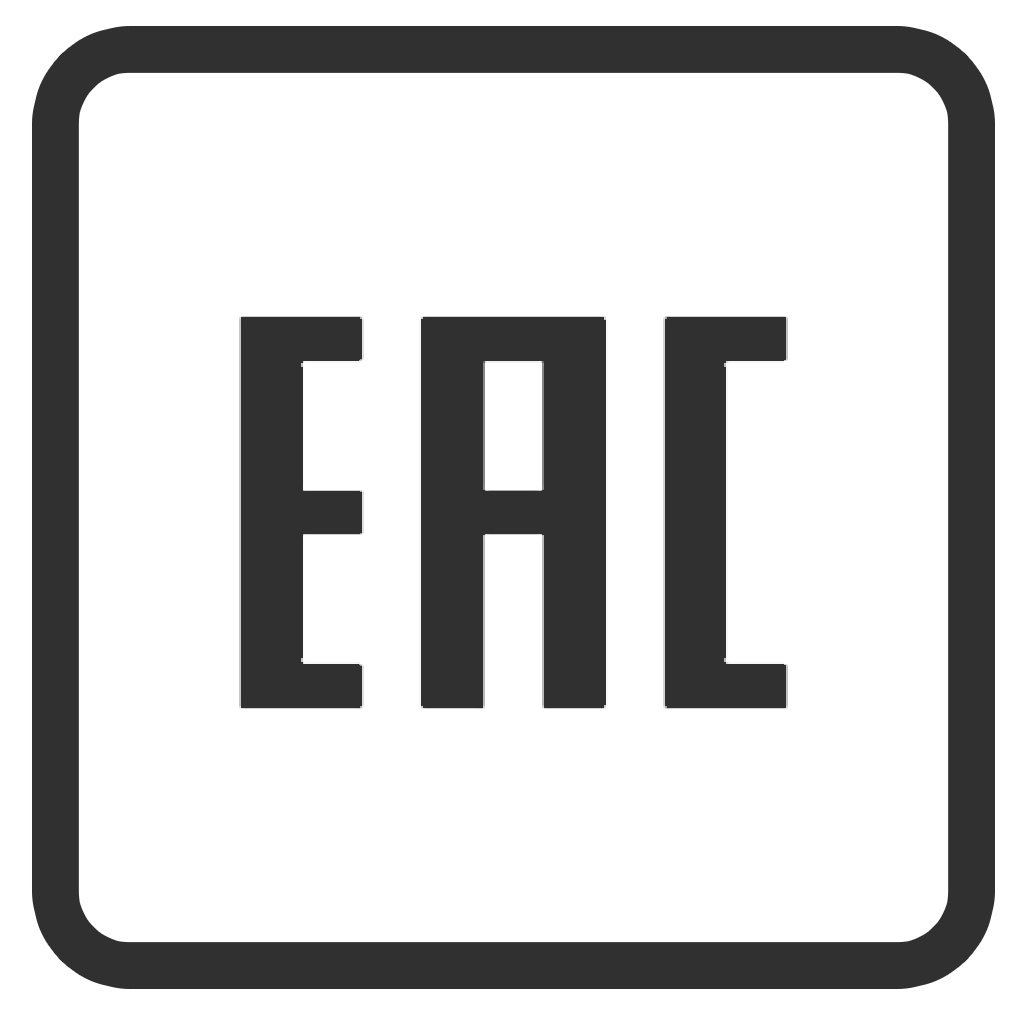
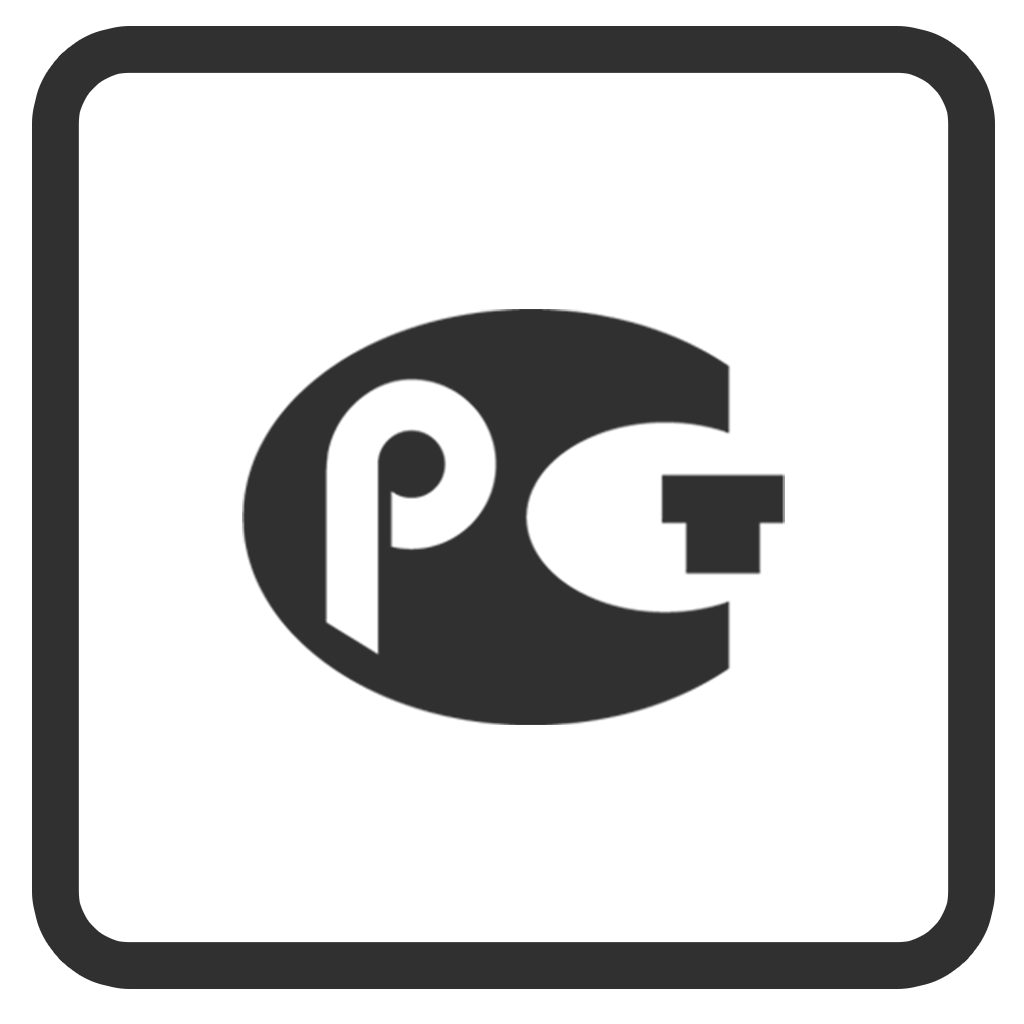
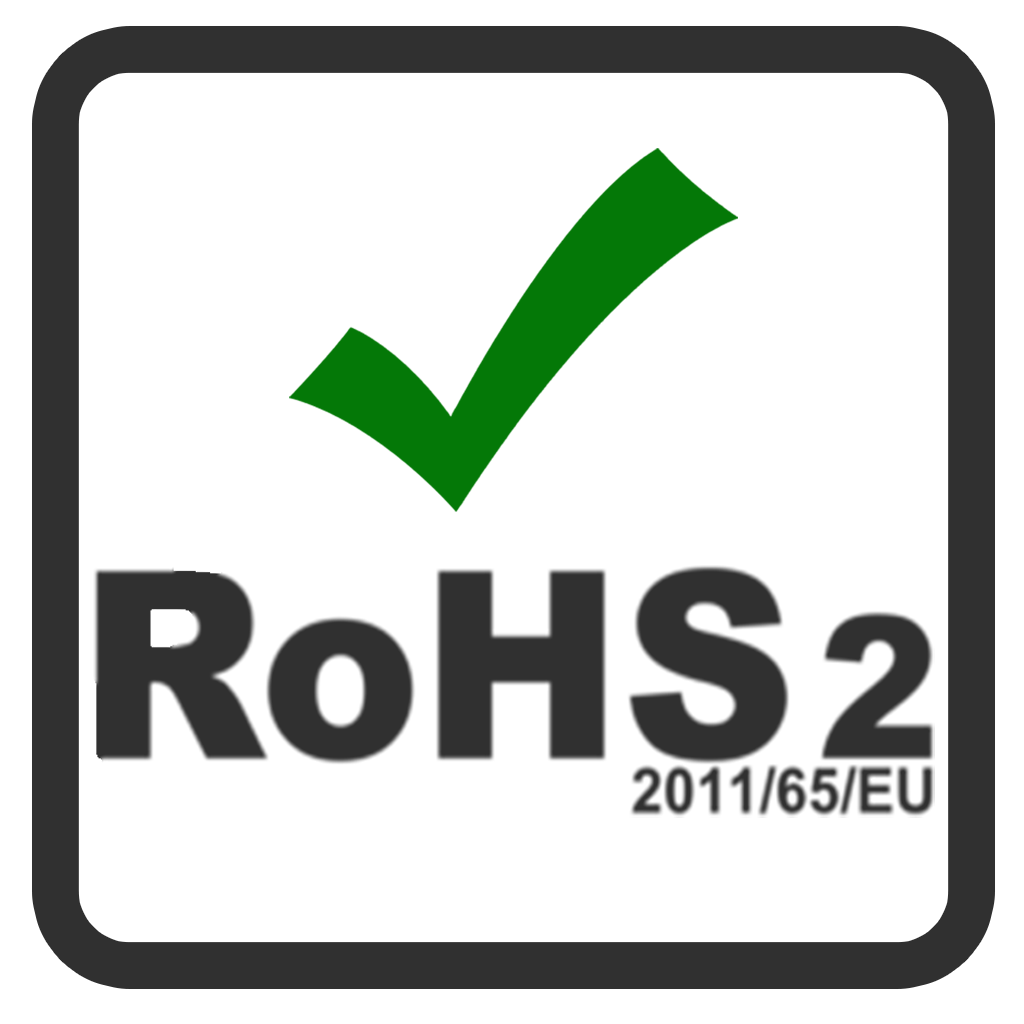
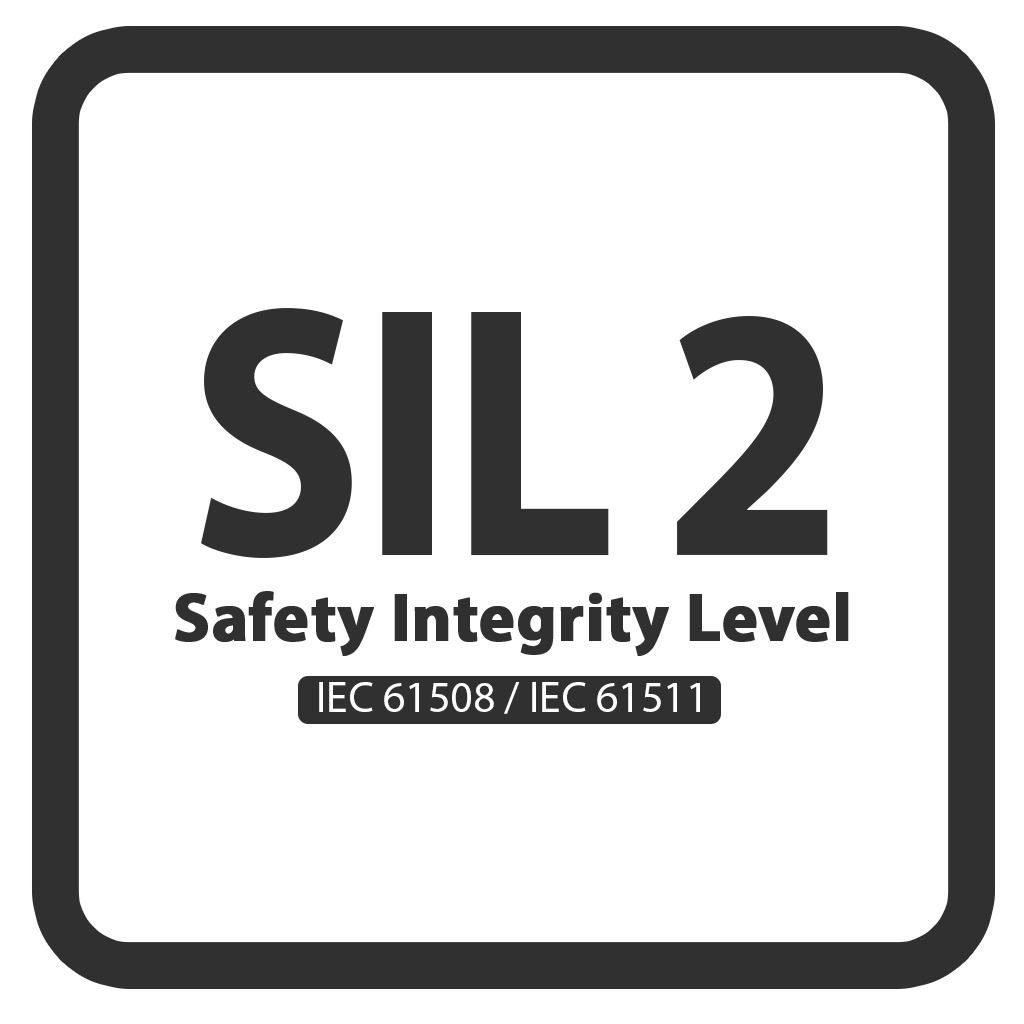
PT467XL
PT467XL- Pressure sensor with flexible and exposed capillary In a version with a more durable membrane(XL).
The PT467XL series of pressure transmitters are the ideal choice for applications with high accuracy and minimal mounting space. The PT 467XL models have an accuracy of ± 0.5% of range and an exposed capillary with a diameter of 1.5 mm, which allows bending in a radius of 1/16 inch. The sensors are supplied with a Dymax® membrane, which ensures an increase in wear resistance and thus a longer service life. Sensors marked XL have a protector (flexible capillary) up to the tip of the sensor.
Durable membrane XL
0 - 30,000 PSI
Output signal 3.33 mV / V
Accuracy ±0.25%
Power supply 10-12 Vdc
Units - PSI
6 Pin connector
Shunt calibration
Excellent thermal stability and repeatability
Exposed, bendable capillar
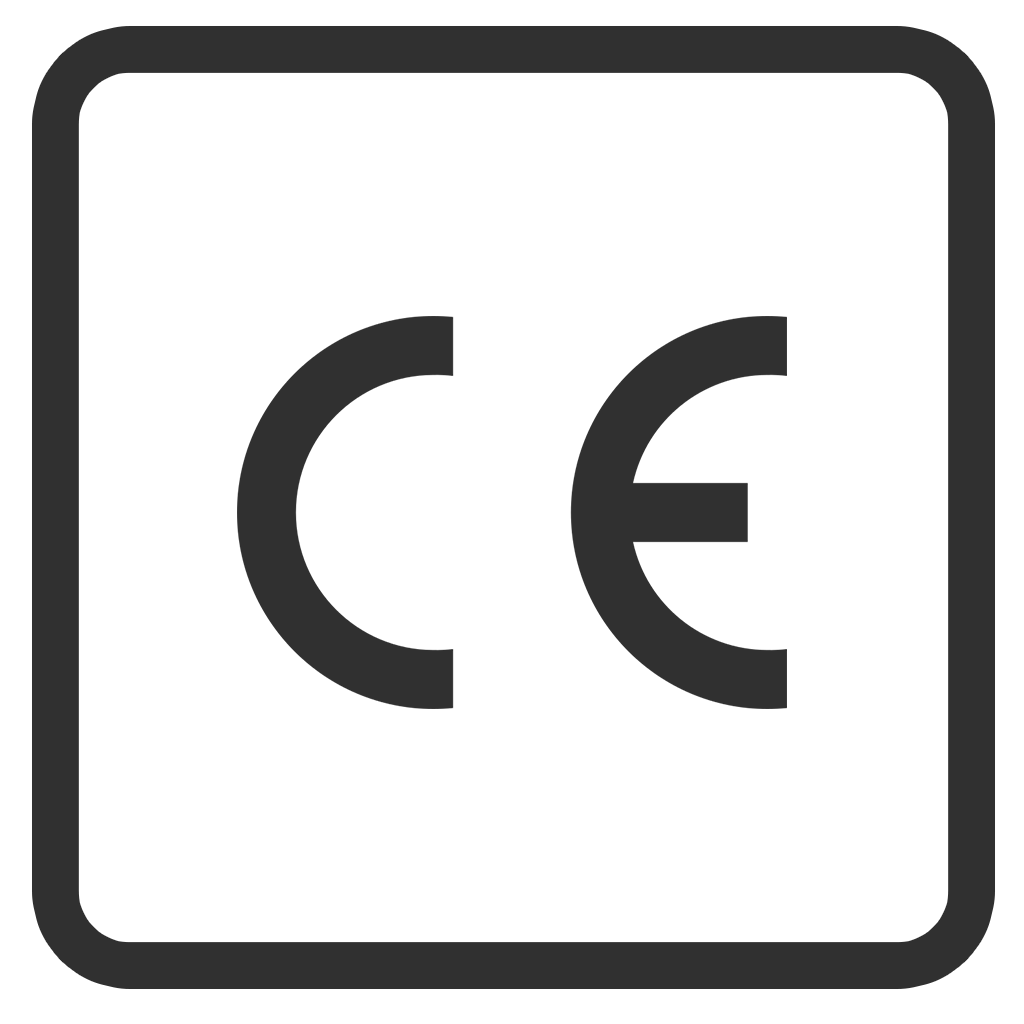
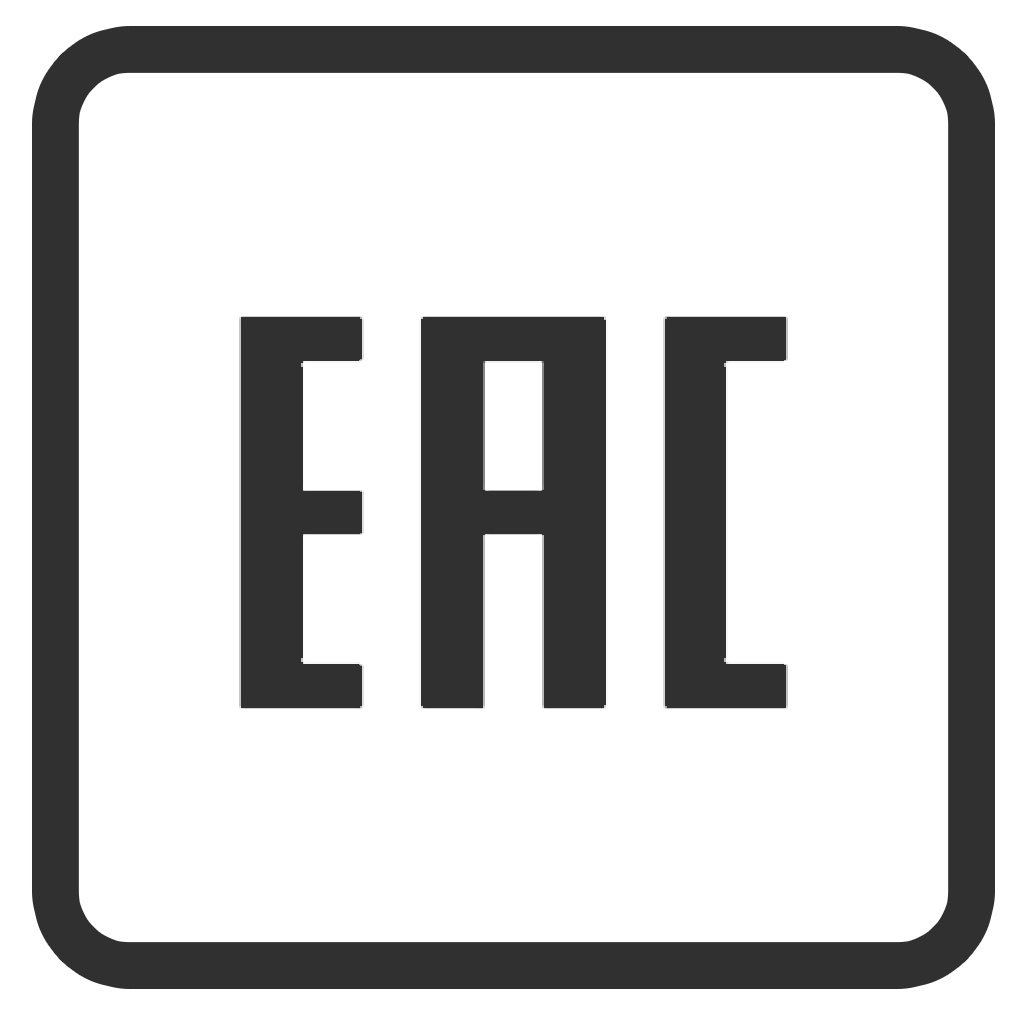
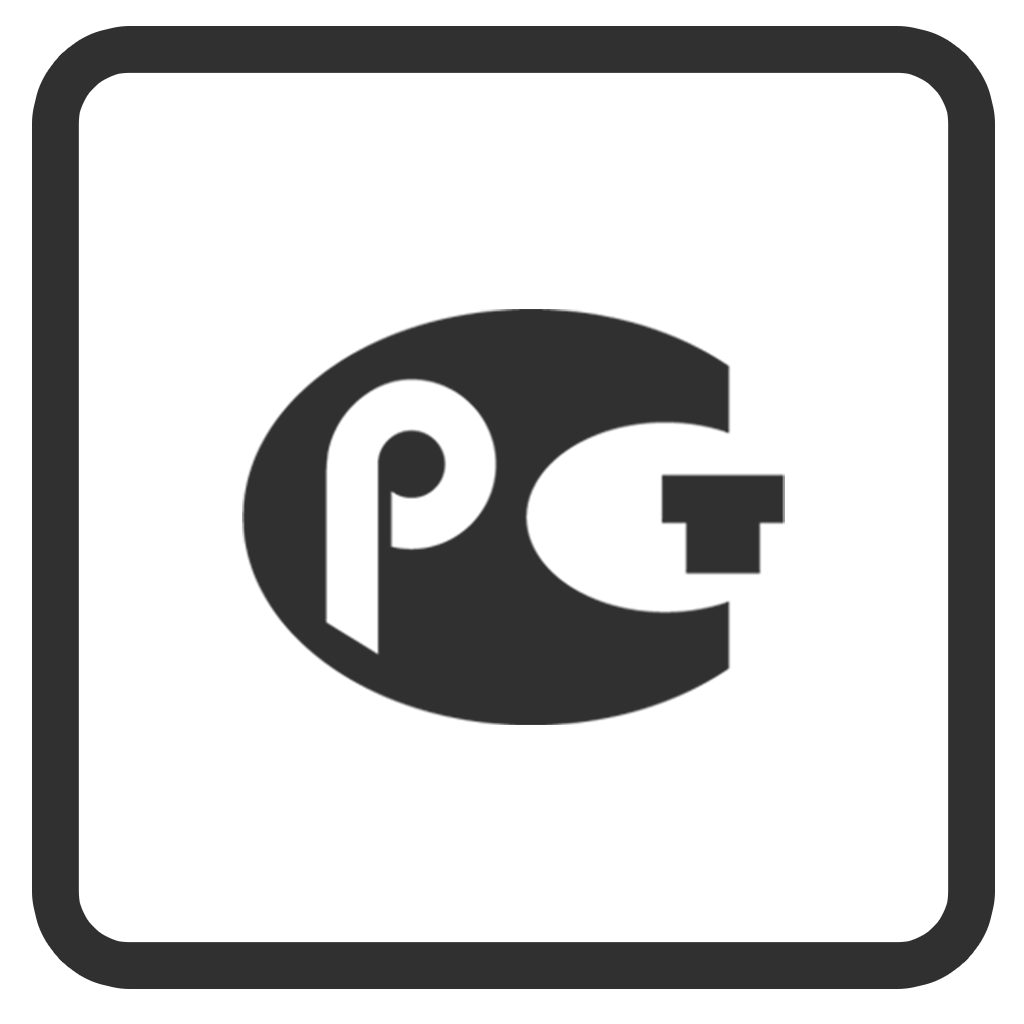
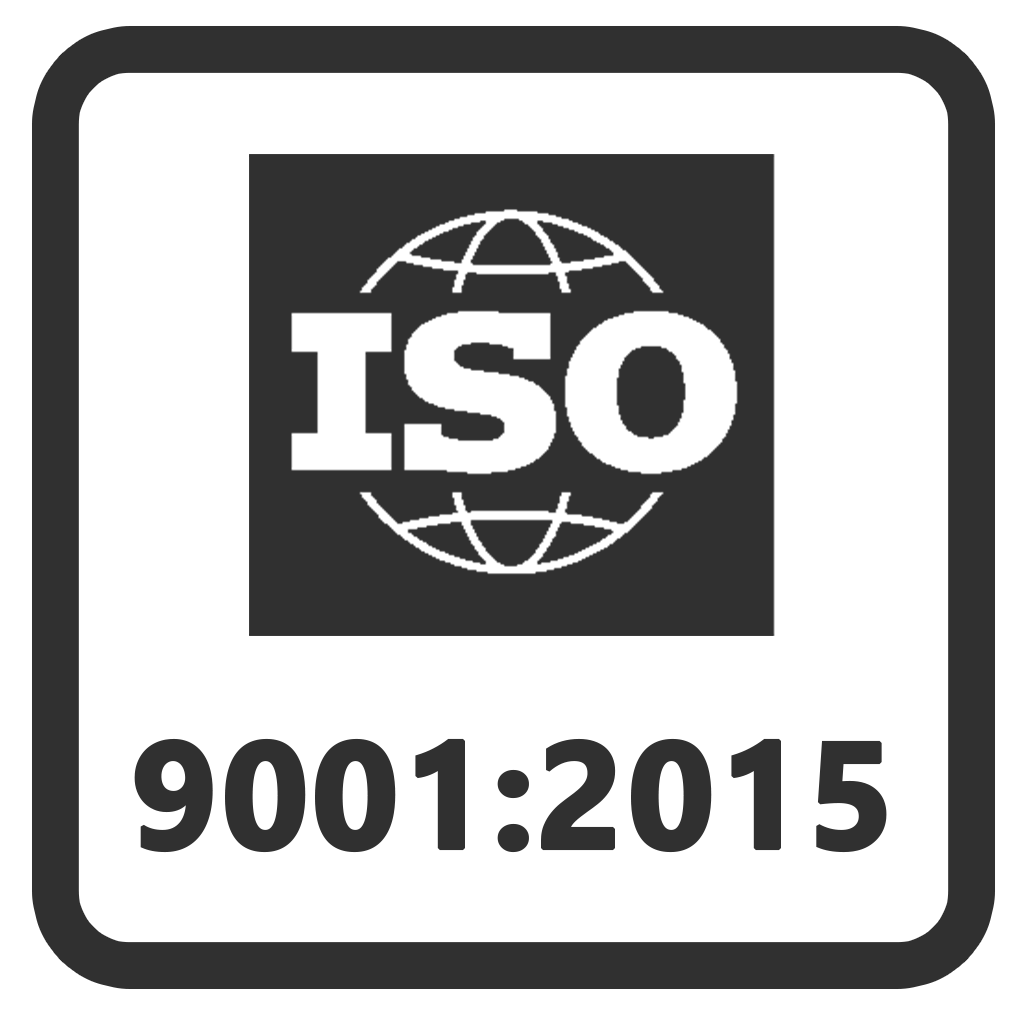
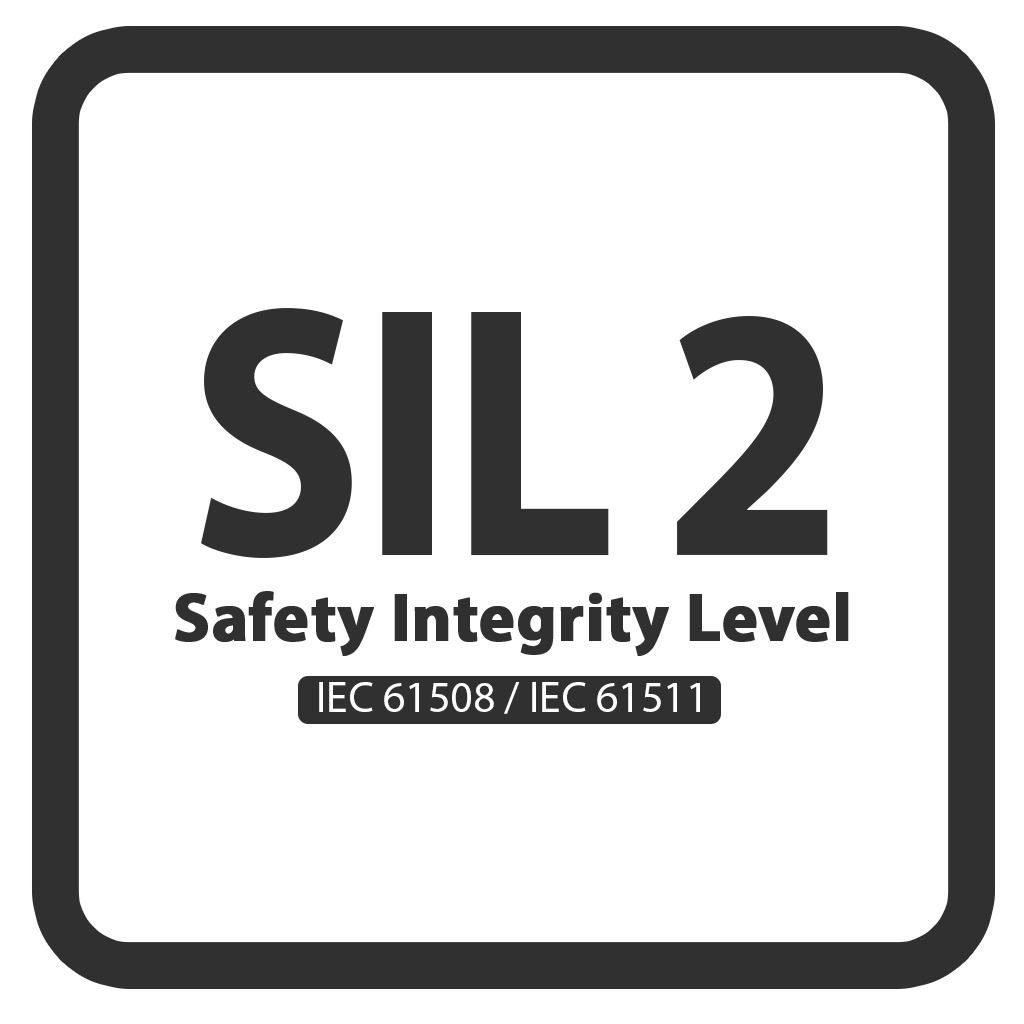
1480 Panel Indicator
1480 is a universal pressure or temperature indicator with one or double configurable alarm as well as optional linear retransmission of the displayed process. Ideal for use in extrusion applications.
Universal entrance
2 alarm outputs
Optional retransmission
Min. / max. values
FCR-R - Rheometer
Specifically designed for the synthetic fiber production industry, the Dynisco FCR-R series can be configured to measure a range of apparent shear viscosities, dual melt flow rate, simultaneous melt flow rate and extensional viscosities using the Cogswell Equations. The FCR-R system consists of two parts: a rheometer head and a rheometer control unit (RCU). The rheometer head is connected directly to the process which samples, conditions, and measures the melt viscosity of the molten resin through two separate dies. The RCU controls the rheometer test parameters (temperature, pressure and rate) and takes in data from the measurement head as well as provides outputs of computed results.
On-line apparent viscosities at a wide shear rate range
Unique double capillary design with return current
On-line measurement of polymer elongation properties
Data exchange via analog and digital inputs / outputs
Easy calibration
CMR IV - Rheometer
Specifically designed for the thermoplastics resin industry, the Dynisco CMR series can be configured to measure melt flow rate, high/low load melt flow rate, apparent viscosities, or to perform other customer defined tests.The CMR system consists of two parts: a rheometer head connected directly to the process which samples, conditions, and measures the melt flow of the resin, and an RCU (Rheometer Control Unit) that controls the CMR test parameters (temperature, pressure, rate), and provides outputs of computed results, and communications to an external distributed control system when required.
Online measurement
Data export via mA signal or RS232
Customer solutions
The system is also designed for places with a risk of explosion
Vertex® sensors used for high accuracy
Range of dosing pumps for specific applications
Easy calibration
Alarm system
Robust industrial design
ViscoSensor
The ViscoSensor provides continuous measurements of the melt flow rate or apparent viscosity directly on the manufacturing process. The ViscoSensor system consists of two parts: a Viscosensor Rheologic Sensing Unit (RSU), connected directly to the process, and a Rheologic Control Unit that controls the ViscoSensor test parameters, provides outputs of computed results, and provides communications to an external distributed control system when required.
Connection via M18 hole or flange
An effective solution for monitoring online values
The measured polymer is returned to the processing
ASTM D1238, ISO 1133, or JIS K 7210
On-line shear viscosity and intrinsic viscosity (IV)
Easy calibration
2 Vertex pressure sensor for the highest accuracy
ViscoIndicator
Specifically designed for the thermoplastics resin industry. The ViscoIndicator duplicates the test conditions of a laboratory Melt Flow Rate (MFR) tester or capillary rheometer. Melt viscosity measurements such as melt flow rate and Intrinsic viscosity are primary specifications of thermoplastic resins.
Dont forget- our ViscoIndicator is IoT enabled. The IoT native software of the ViscoIndicator allows for real-time access to your testing information.With the Dynisco Cloud Connect Subscription, you get comprehensive access of rheological data, correlations, and dashboards. This interface allows for a complete “Window into the Process” providing valuable insight to your polymer process.
Connection instead of pressure sensor
Windows ™ 10 IoT
Continuous MFR indication
Continuous indication of shear viscosity
Continuous indication of intrinsic viscosity
Vertex mercury-free sensors
Easy installation
Easy integration
Quick capillary change
Melt Flow Indexer LMI 5000
The LMI is a cultivation of feedback from customers incorporating a series of key features and options: Color Touch-Screen Display incorporating a user friendly menu structure, USB communications, pneumatic weight lift system with stackable weights, a force packer, higher accuracy digital encoder, software and NEW! auto cutter option.
The melt flow indexer provides results in the form of MFR, MVR, Melt Density, IV, Shear Viscosity and Shear Rate.
Meets standards:
ASTM D1238 and D3364, ISO 1133, BS 2782, DIN 53735, JIS K7210.
Melt Flow Rate - MFR
Melt Volume Rate - MVR
Intrinsic Viscosity - IV
Melt Density
Shear Viscosity
Shear Rate
USB, Printer, Software