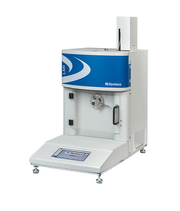
How to work with the LMI 5000 series
The video manual will guide you through the complete use of the LMI 5000. The capillary melt flow indexer and its use on polypropylene will guide you through the measurement procedure method A, method A / B, and method B. All three methods are shown in detail and you have an idea of how each method can work. on your metal. The video is also focused on cleaning the device, removing the capillary, and complete the preparation of further measurements. If you have any questions about any of the procedures you have seen, do not hesitate to contact us. We will be happy to explain everything about capillary melt flow indexer.
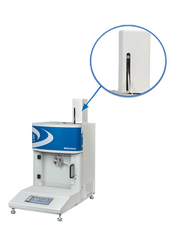
Digital encoder calibration
Video manual focused on digital encoder calibration for the LMI 5000 capillary plastometer. This is a quick help if your device requires digital encoder calibration or Video describes in detail how to properly calibrate the digital encoder step by step. From switching on the device to switching off. Describes the measuring piston by marking it with lines and inserting weights on the piston, including the weights
LMI 5000 touch screen calibration
We calibrate Dynisco devices directly at the customer, according to the ISO 17025 standard, and we issue a report on the calibration of the device. Calibration is focused on the mechanical dimensions of functional parts, temperature sensors, heating elements, and weights or load cells of the device. More information about calibrations. We calibrate Dynisco devices directly at the customer, according to the ISO 17025 standard, and issue a report on the calibration of the device. Calibration is focused on the mechanical dimensions of functional parts, temperature sensors, heating elements, and weights or load cells of the device. More information about calibrations.
Panel Indicator 1490 - configuration
The video shows the connection and configuration of the panel indicator 1490, including the subsequent calibration of the sensors. When calibrating the pressure sensor, it is necessary to pay increased attention to the following points. The system must be warmed to operating temperature. The pressure sensor is installed in a mounting hole that has been hot cleaned and inspected. And no pressure is generated in the system. After observing these points, it is possible to check and calibrate the pressure sensors using the indicator 1490.
UPR 900 indicator - settings / configuration
The video shows the connection and configuration of the UPR 900 panel indicator, including the subsequent calibration of the sensors. When calibrating the pressure sensor, it is necessary to pay increased attention to the following points. The system must be warmed to operating temperature. The pressure sensor is installed in a mounting hole that has been hot cleaned and inspected. And no pressure is generated in the system. After observing these points, it is possible to check and calibrate the pressure sensors using the UPR 900 indicator. The connection of another sensor (temperature) is also shown here.
ATC 990 controller - settings / configuration
The video shows the connection and configuration of the ATC 990 panel controller, including the subsequent calibration of the sensors. When calibrating the pressure sensor, it is necessary to pay increased attention to the following points. The system must be warmed to operating temperature. The pressure sensor is installed in a mounting hole that has been hot cleaned and inspected. And no pressure is generated in the system. After observing these points, it is possible to check and calibrate the pressure sensors using the ATC 990 controller. The connection of another sensor (temperature) is also shown here. And setting the control of an extruder or other motor, for example for the operation of a gear pump.
Pressure sensor calibration [mV/V]
Calibration of pressure sensors is crucial especially for the correct operation and ensuring safe operation of extrusion lines. A pressure sensor that is set correctly and calibrated will accurately display the measured values of pressure or temperature. The following procedure is required for proper setup and calibration. Before starting the calibration of pressure sensors, it is necessary that the sensor is already installed in the mounting hole of the line, which has been cleaned and checked beforehand. Each calibration procedure differs according to the type of sensor or output signal.
Pressure sensor calibration [mA]
Calibration of pressure sensors is crucial especially for the correct operation and ensuring safe operation of extrusion lines. A pressure sensor that is set correctly and calibrated will accurately display the measured values of pressure or temperature. The following procedure is required for proper setup and calibration. Before starting the calibration of pressure sensors, it is necessary that the sensor is already installed in the mounting hole of the line, which has been cleaned and checked beforehand. Each calibration procedure differs according to the type of sensor or output signal.
Pressure sensor calibration [V]
Calibration of pressure sensors is crucial especially for the correct operation and ensuring safe operation of extrusion lines. A pressure sensor that is set correctly and calibrated will accurately display the measured values of pressure or temperature. The following procedure is required for proper setup and calibration. Before starting the calibration of pressure sensors, it is necessary that the sensor is already installed in the mounting hole of the line, which has been cleaned and checked beforehand. Each calibration procedure differs according to the type of sensor or output signal.
Pressure Sensor Care and Maintenance
In order to maintain your Dynisco pressure sensor's reliability and accuracy over time, certain maintenance and cleaning procedures should be followed. This video focuses on the removal, care, and maintenance process of a Dynisco pressure sensor from an extruder.
Melt Flow Indexer Cleaning Procedures
Dynisco melt flow indexers are used to evaluate the processability of materials. Get quick and accurate measurements of melt flow characteristics to determine material quality, lot to lot consistency, and ensure what you are buying is what you need. Demonstrated here is the proper method of cleaning your Dynisco melt flow indexer after each test in order to maintain the machine's precision, accuracy, and longevity.
IV Method B Test Using the Dynisco LMI5500 Melt Flow Indexer
Dynisco melt flow indexers are used to evaluate the processability of materials. Get quick and accurate measurements of melt flow characteristics to determine material quality, lot to lot consistency, and ensure what you are buying is what you need. Let’s take a look at a specific use case for the LMI5500: the measurement of the intrinsic viscosity of the polymer PET using the Method B Test.
Online Rheometers - Basic Operations Guide
With Dynisco's Online Rheometers, you can verify your polymer rheology of not only your virgin material, but virgin and recycled polymer, and eliminate quality issues before production. Learn more by visiting our website at the link below.
Online Rheometers - System Parameters
With Dynisco's Online Rheometers, you can verify your polymer rheology of not only your virgin material, but virgin and recycled polymer, and eliminate quality issues before production. Learn more by visiting our website at the link below.