Ettlinger Company
ETTLINGER is a brand in the plastics industry under which you can equip powerful and reliable melt filtration systems for extrusion and injection molding applications for more than 35 years. Ettlinger is now part of the MAAG Group and is developing special high-performance melt filtration systems, together with high-capacity injection molding machines and tailor-made applications for every customer.
ETTLINGER offers globally unique expertise in filtration and recycling systems and injection molding machines. Our continuously operating high-performance melt filters are successfully used worldwide to filter polymer feedstocks with varying degrees of contamination. Each system incorporates decades of experience, thorough know-how and state-of-the-art technology, thanks to which ETTLINGER sets global standards as part of the MAAG Group.
Ettlinger melt filters are state-of-the-art technology for processing a variety of recycled materials - with a patented principle that has already proven its functionality and performance in many industrial applications around the world. The ERF and ECO series are capable of processing virtually any standard polymer that occurs in recycling plants in the production of films and boards, in the production of tapes and fibers, etc. technologies. Thanks to their uniquely compact design, they are also ideal for retrofitting existing lines.
High performance Melt Filters - The ERF Series
The continuous melt filters in the ERF series are suitable for materials with up to 16% by weight contamination and are guaranteed to remain in use for long periods without changing the filter. Our ERF melt filters are capable of processing a wide range of polymers (e.g. LDPE, LLDPE, HDPE, PP, PS, ABS, PC / ABS, TPE, TPU, POM). All solid or elastomer foreign particles such as paper,wood, aluminum, copper, rubber, silicone, or high-melting polymer composites are efficiently removed.
The classic application for ERF melt filters is repelletizing lines, but they are also successfully employed for sheet and profile extrusion. ERF melt filters can in principle be used in any extrusion line – either single or twin-screw and irrespective of the type of pelletizing system or other downstream unit. Three different sizes enable throughputs from 150 to 10,000 kg/h depending on the application.
Suitable for Compounding, Recycling, Extrusion
Fully automatic, continuous operation
Up to 18% contaminants removed
Extremely low melt losses
More reliable processing due to constant pressure at the filter outlet
No need to replace the screen for several weeks, or possibly months, depending on the material and the application
Completely closed system with no entrapped air
Short contaminant residence times in the filter
Very simple replacement of the scraper from outside using a hydraulic cylinder
Elastomers (rubber, silicone) are efficiently filtered and discharged before they have a chance to be forced through the filter screen
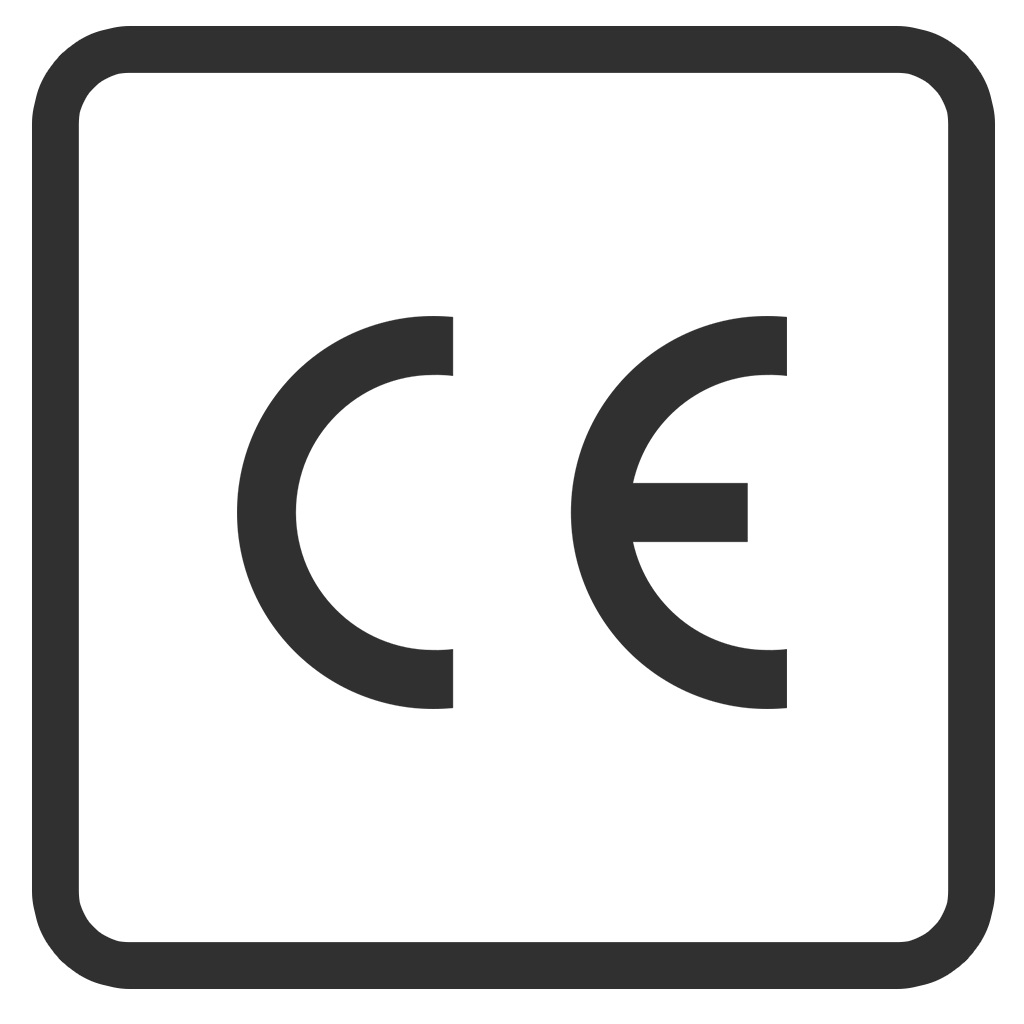
High performance Melt Filters – The ECO Series
The continuous melt filters in the ERF series are suitable for materials with up to 16% by weight contamination and are guaranteed to remain in use for long periods without changing the filter. Our ERF melt filters are capable of processing a wide range of polymers (e.g. LDPE, LLDPE, HDPE, PP, PS, ABS, PC / ABS, TPE, TPU, POM). All solid or elastomer foreign particles such as paper,wood, aluminum, copper, rubber, silicone, or high-melting polymer composites are efficiently removed.
The classic application for ERF melt filters is repelletizing lines, but they are also successfully employed for sheet and profile extrusion. ERF melt filters can in principle be used in any extrusion line – either single or twin-screw and irrespective of the type of pelletizing system or other downstream unit. Three different sizes enable throughputs from 150 to 10,000 kg/h depending on the application.
Suitable for Compounding, Recycling, Extrusion
Fully automatic, continuous operation
Up to 18% contaminants removed
Extremely low melt losses
More reliable processing due to constant pressure at the filter outlet
No need to replace the screen for several weeks, or possibly months, depending on the material and the application
Completely closed system with no entrapped air
Short contaminant residence times in the filter
Very simple replacement of the scraper from outside using a hydraulic cylinder
Elastomers (rubber, silicone) are efficiently filtered and discharged before they have a chance to be forced through the filter screen
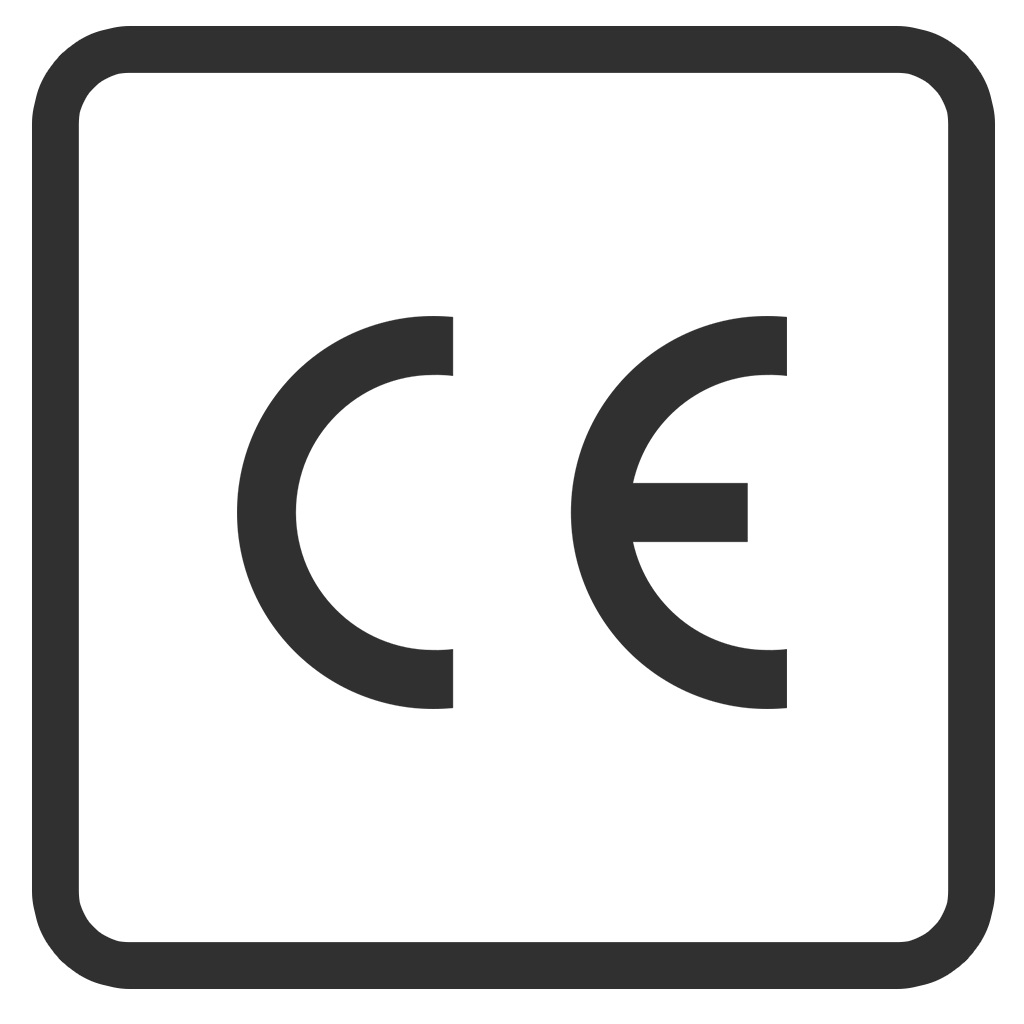