Filtration systems and screencangers for industrial applications
Filtration is a process that separates or purifies substances. The mechanical separation processes of Maag filtration systems are physical. The principles are used in filters and screen converters for separating and cleaning plastic melts, chemicals and lubricants. They are also used in recycling, extrusion, rotational molding, in general in industrial applications and in the pharmaceutical and food industries.
DFS - Continuous large area polymer filtration systems
MAAG’s new generation Duplex Filter System (DFS). The new DFS incorporates a new patented solid body DIVEXpro switch over valve. The vent and drain valves are also newly designed and integrated into the body of the DIVEXpro. Combined with MAAG’s established MICRONEX® filter candles the new generation filter system can meet the harsh demands of polymer filtration. For chemical recycling applications with low viscosity and high contamination levels the new generation DFS-BF is capable of performing an automated backflush cleaning of the filter candles during operation.
Suitable for Resin & Virgin Polymer Production
Reliable sealing
Improved venting
Better draining
Simplified vessel changeout
Improved accessibility
Safer operation
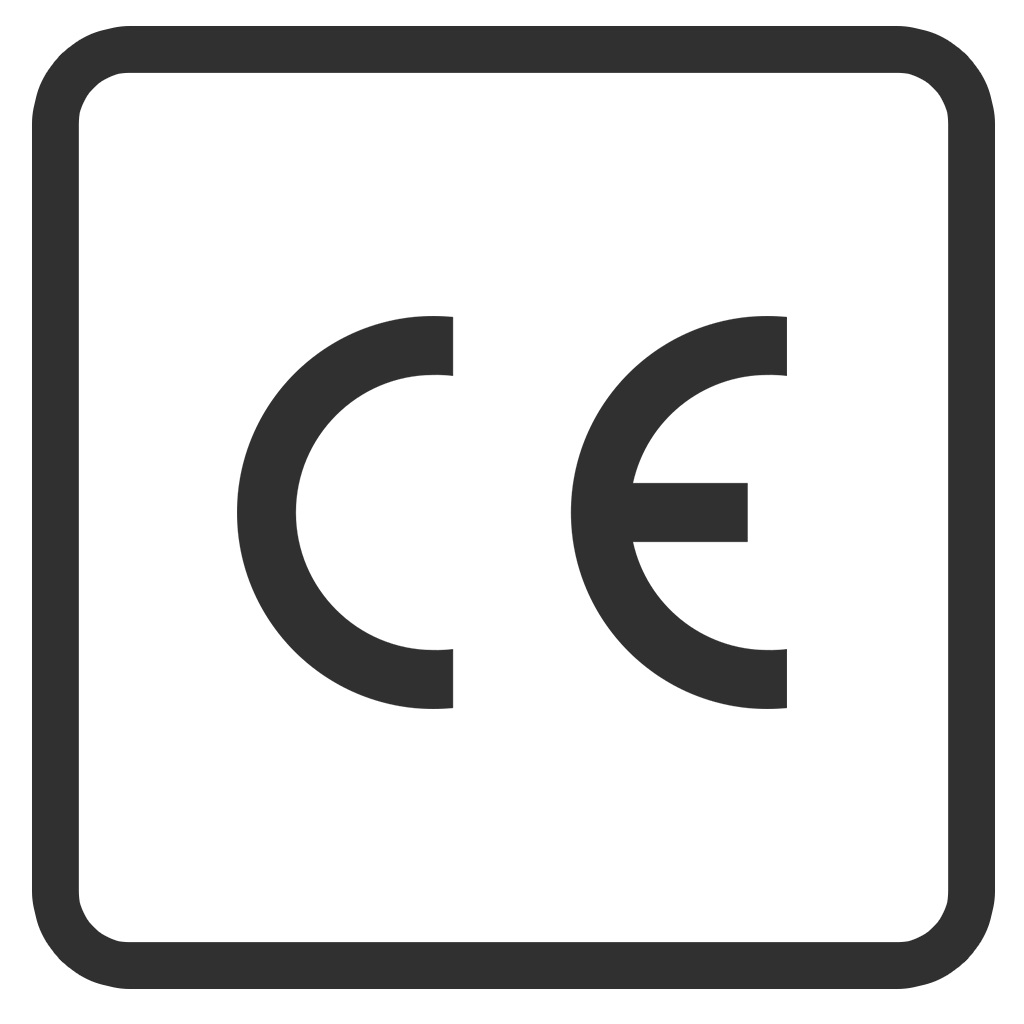
micronex
Polymer application and polymer filtration with filter elements for large areas
MAAG offers high-quality polymer filter elements designed for long term use and multiple cleanings. MAAG can provide standard design polymer application or build to your requirements regarding:
Filter elements designed for individual processes
Optimized polymer flow
Maximized filter area
Lowest possible pressure loss
Designed to retain hard and deformable particles
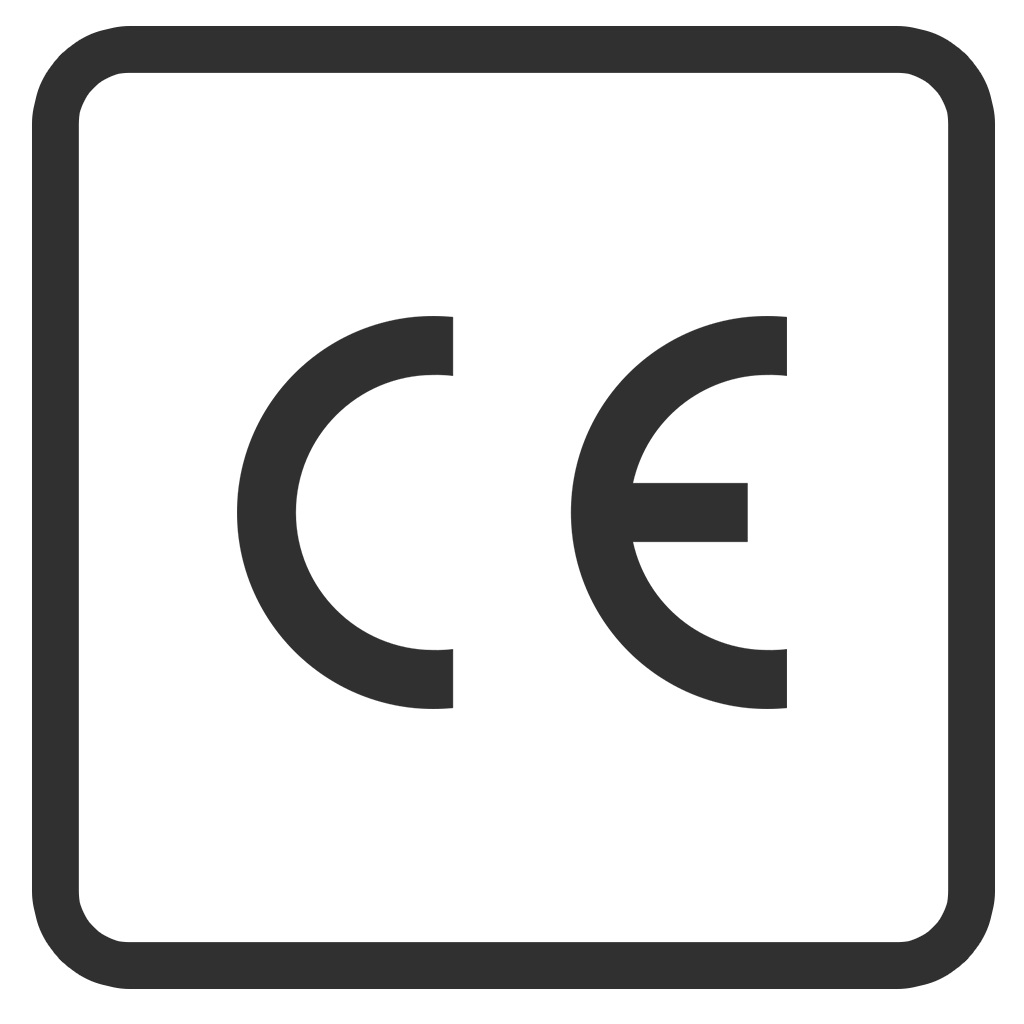
multinex
Polymer filter candles and application for masterbatch and polymer filtration
MAAG multinex polymer filter candles are tailor-made for use in continuously operating dual bolt screen changers of the MAAG CSC-P/C series for polymer filtration.Compared to typical polymer application round screen plates, they increase the active screening area up to 60
Optimized for high viscosities
Reusable candle bodies
Economic perforated sleeve exchange
Screen mesh or metal fiber fleeze
Filter fineness 0.5-500 micron
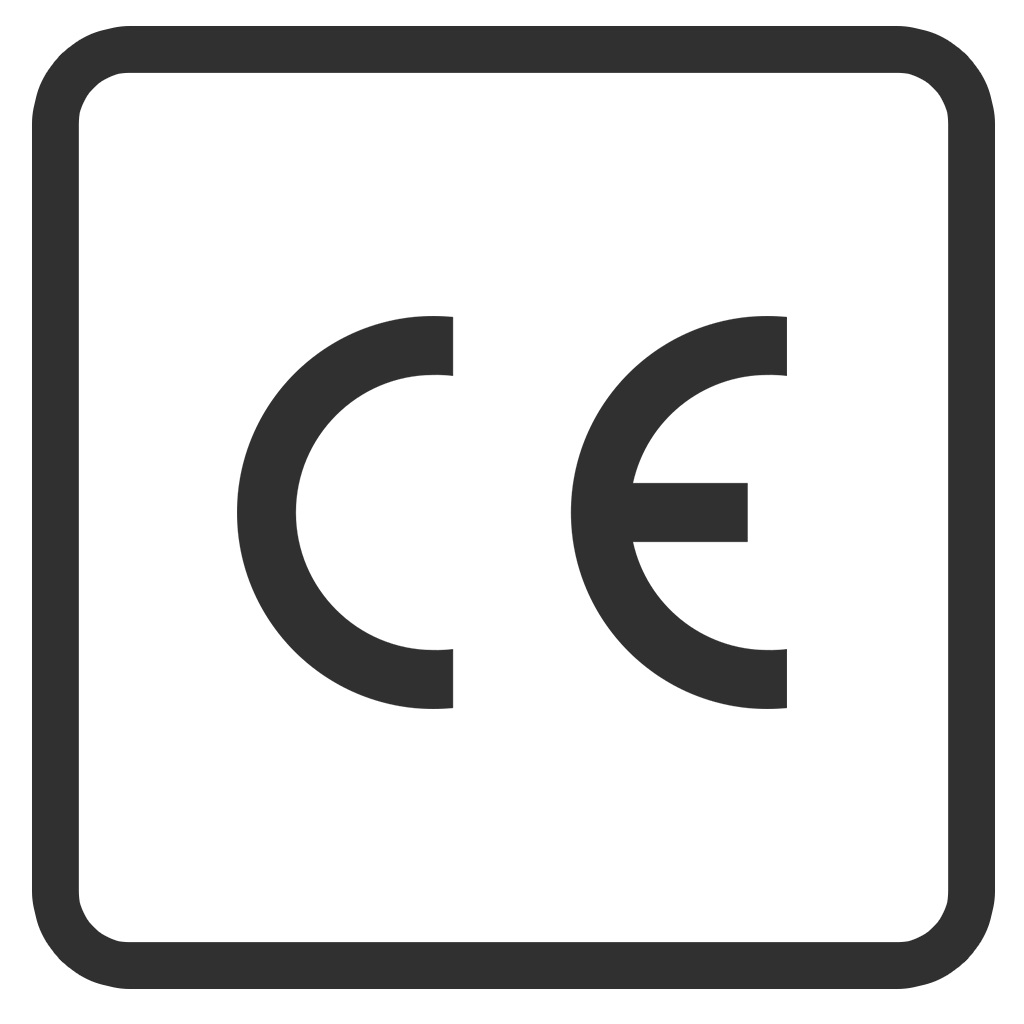
Simplex - Discountinuous large area polymer filtration applications for industry and extrusion
MAAG-designed simplex polymer filter systems can be provided with either fixed or removable vessels. A compact preheat station with spare vessel is also available for locating near the polymer processing line for quick changeout. They are custom designed to minimize initial pressure drop and maximize polymer filter element life. Our proprietary sizing program, based on more than 20 years of experience in the field of polymer production and extrusion, incorporates your operating data to size each system for maximum performance and optimized flow while maintaining compact dimensions.
Suitable for Resin & Virgin Polymer Production, Extrusion
Lower cost
Easier operation
Less space requirements
Minimized pressure drop
Horizontal or vertical design
No diverter valves
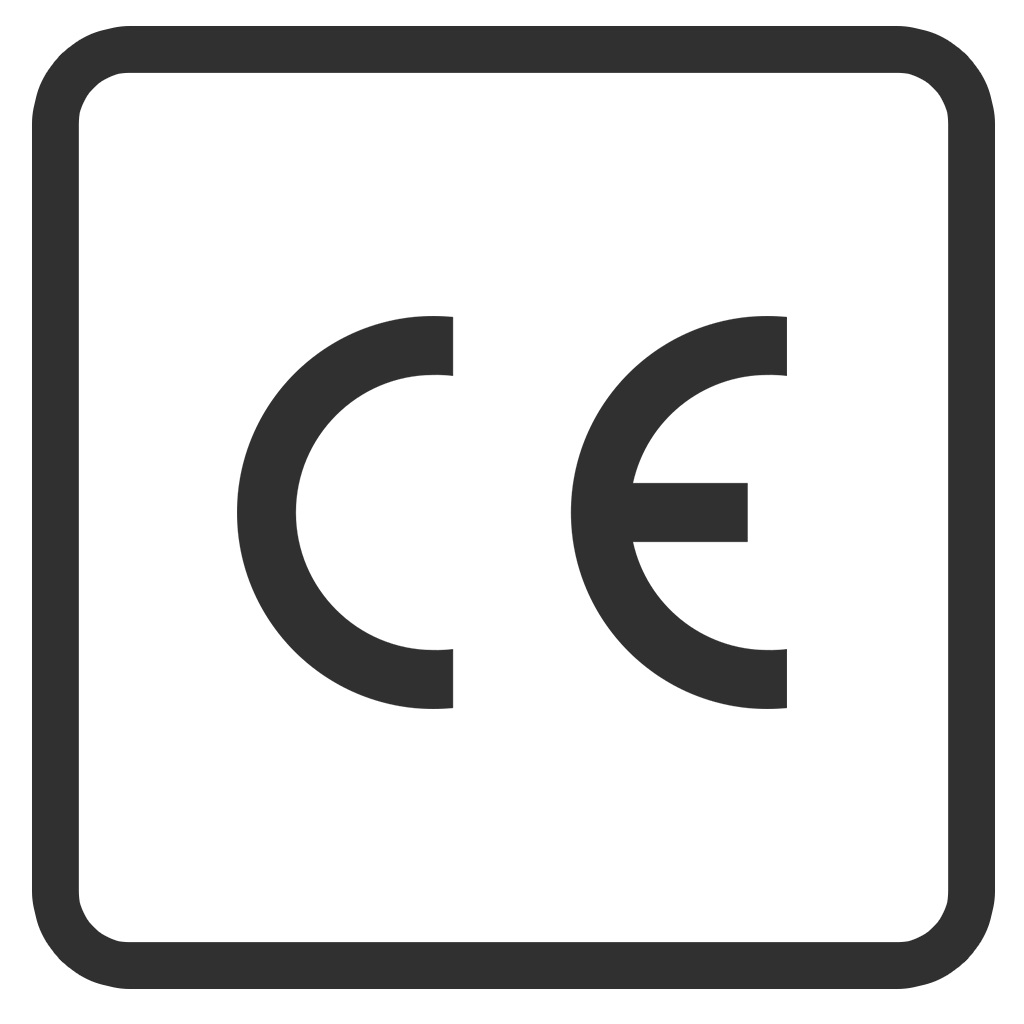
CSC-C - Polymer filtration for polymer production, polymer processing and extrusion
MAAG’s CSC-C large scale screen changer with candle filter elements is the right choice if short melt residence time, small footprint and a simplified candle change are required. Depending on the polymer type, melt viscosity, reactor throughput, and filter fineness, the screen changer size and number of pistons are customized to the application. The patented design allows the use of pleated micronex® candle filter elements with fiber metal felt (FMF) media, or cylindrical Multinex candles filter elements with interchangeable filter sleeves.
Suitable for Resin & Virgin Polymer Production
Filter elements
Vertical / horizontal installation
2/4 pistons
Patented design
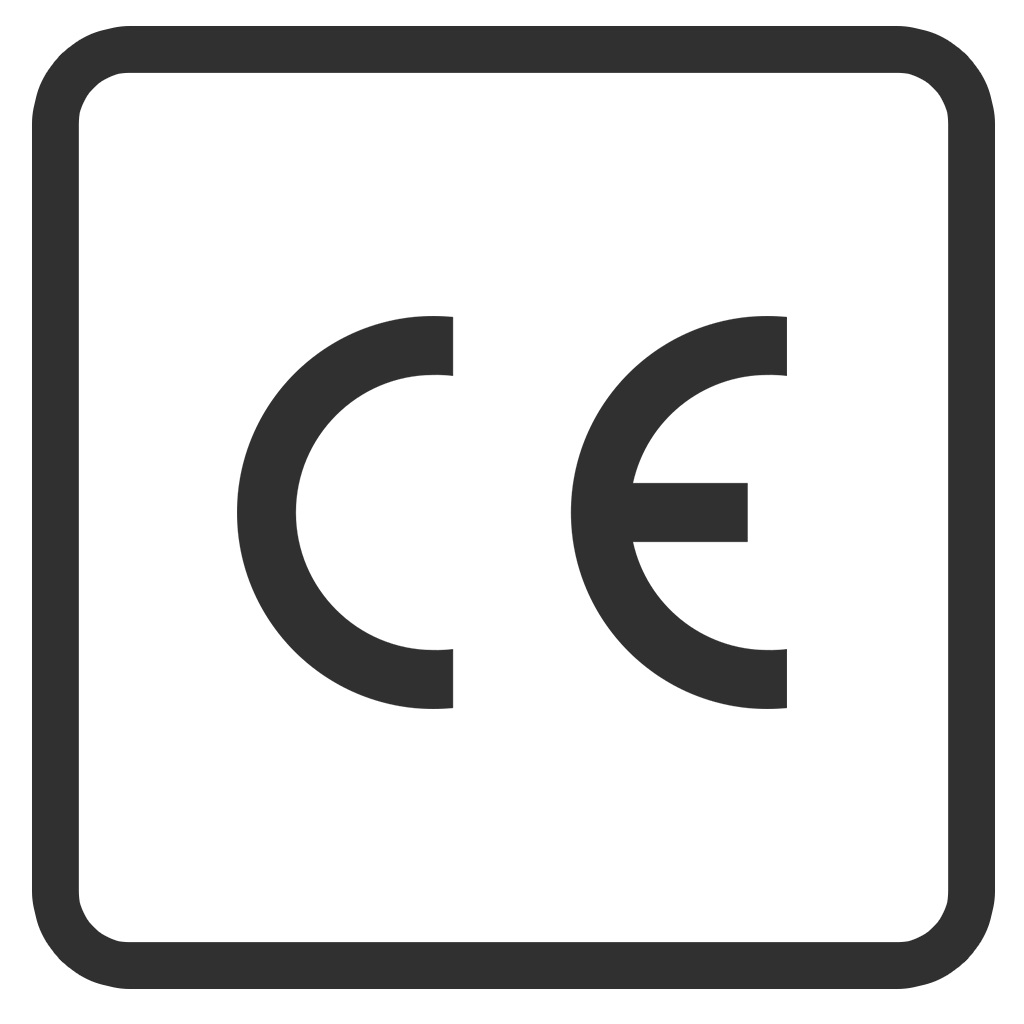
CSC-R - Screen changer with curved filter screens
MAAG’s CSC-R large scale screen changer with curved screens is designed for the use of one-way filter screens which do not require cleaning after the simple and safe screen change. The screen bearing pistons belong to MAAG’s modular filter system and its patented design use 75% of the piston surface as active filtration area. Also this filter execution can be installed for vertical or horizontal melt flow directly at the reactor discharge melt pump or pelletizer booster melt pump to avoid additional piping for reduction of melt residence time.
Suitable for Resin & Virgin Polymer Production
Up to 4x more filter area than circular screen cavities
Higher throughput
Multiplied screen life time
Smaller hydraulic unit
Lower melt pressure
Higher filtration fineness
Reduced flux rate kg/h/cm2
Ultra-compact design
Less heating capacity
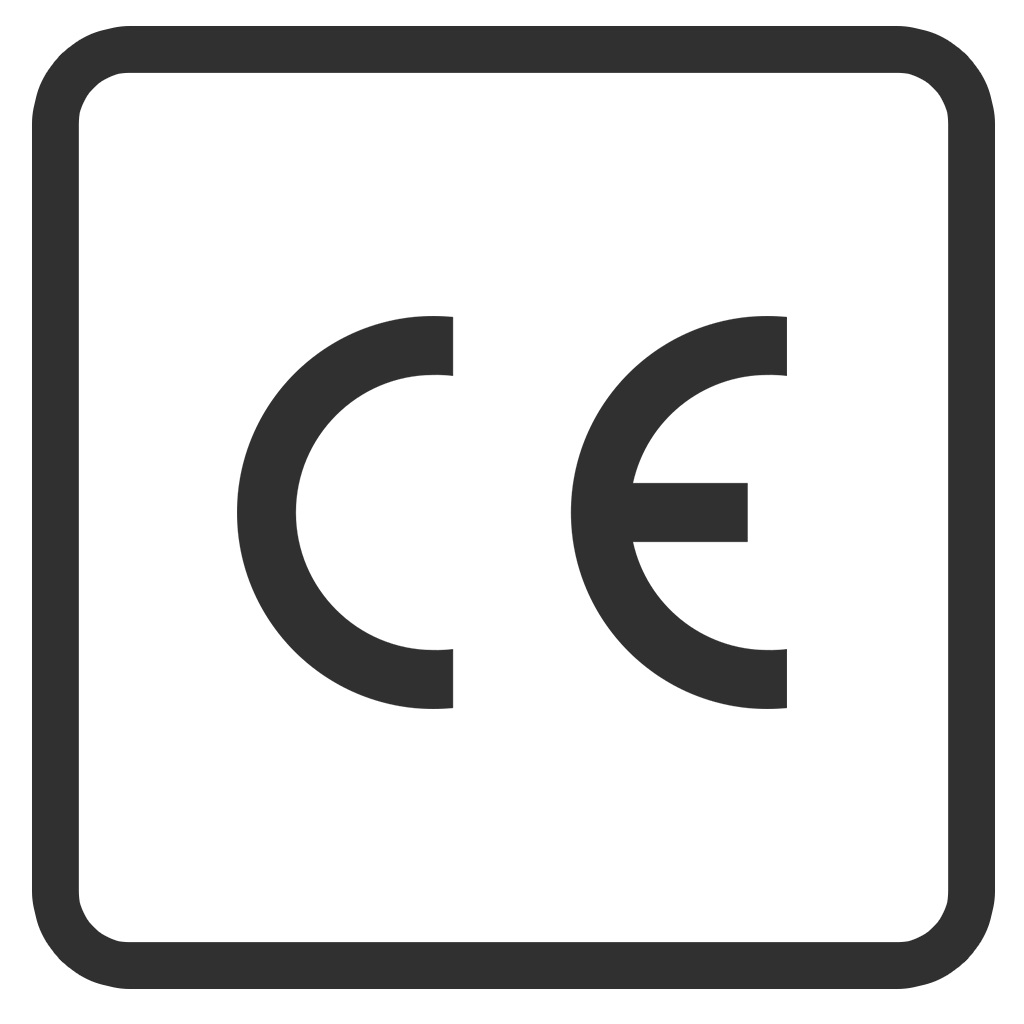