MAAG Company
The MAAG Group comprises successful and renowned companies, each with their own impressive history. Automatik Plastics Machinery, Ettlinger Kunststoffmaschinen, Maag Pump Systems, Gala Industries, Reduction Engineering Scheer and Xantec Steuerungs- und EDV Technik are today the strong and innovative product brands of the MAAG Group.
The history of the MAAG Group thus begins in the late 19th century, with the establishment of Scheer as a metal foundry and machine factory in Stuttgart, Germany, in 1890. Maag Pump Systems was founded in 1913. Automatik Plastics Machinery was founded in 1947. Gala Industries was founded in 1959, and Ettlinger Kunststoffmaschinen in 1983. The youngest member of MAAG Group – Xantec Steuerungs- und EDV-Technik was founded in 1994. Over the decades, they have all grown into experts in the various fields of polymer production and processing.
All the members of the MAAG Group contribute their supreme expertise and years of experience in developing and manufacturing superb machines, plants, systems, and software – and will continue doing so in the future. The bundling of core competencies, industry best practices, the attentive maintenance of existing business relationships and creation of new ones, all provide the foundations for maximum customer satisfaction throughout the Group.
Magnetic Coupling
Sealed design with our double containment shell for chemical pumps as a industrial application
MAAG offers Magnetic Couplings with our double containment shell for chemical pumps. The magnetic couplings provide a hermetically sealed design for chemical transfer pumps and is virtually maintenance free. The couplings come in special designs for industrial applications with suction pressures up to 200 bar.
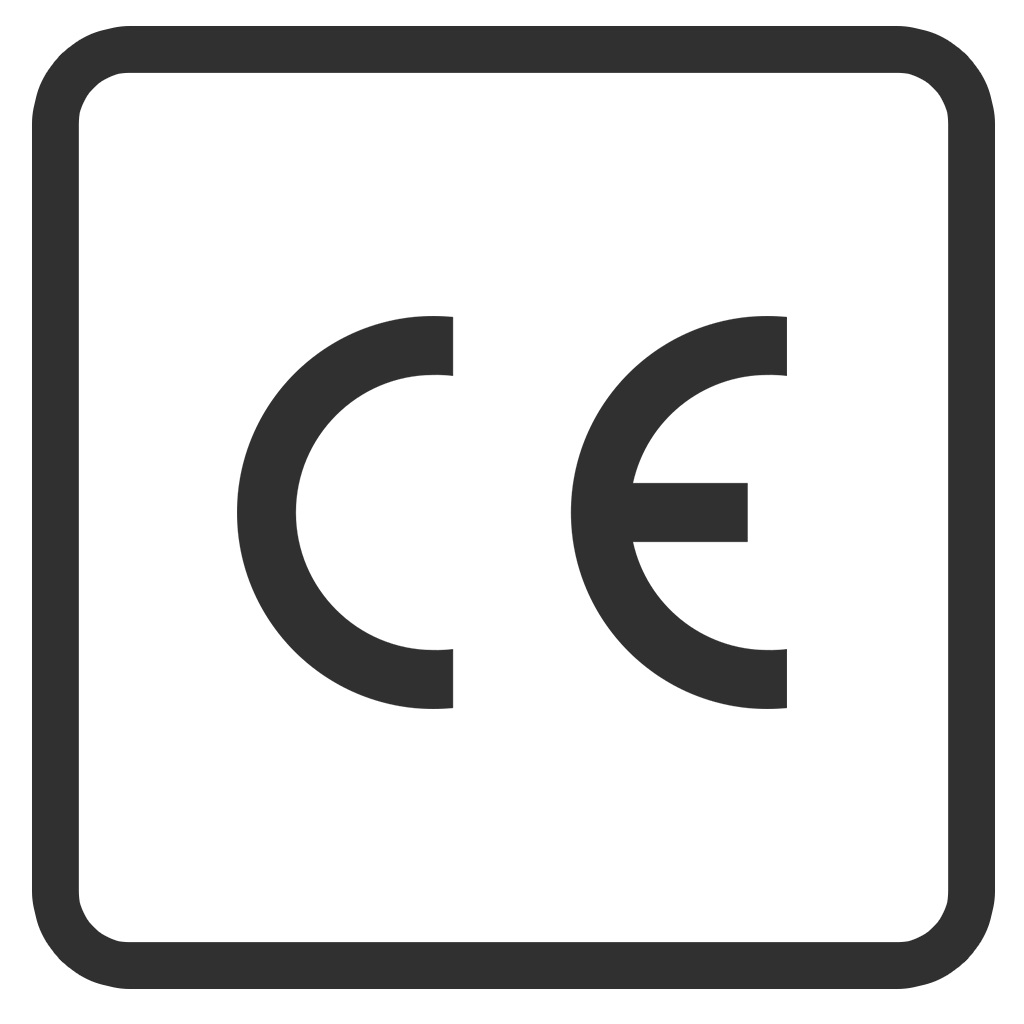
Vispac
Seal for polymer gear pumps and polymer pump systems and applications
High reliability and functionality are crucial for a seal in the polymer application discharging process for guaranteeing optimized product quality and line availability. The vispac® shaft seal is known for its robustness and reliability and especially for its easy handling. This low-maintenance seal is a proven combination of the viscoseal system and sealed packing glands for polymer pump systems.
Extremely large range of applications
Reliability and safety
Low wear and low maintenance
Simple and reliable adjustment of the seal control pressure
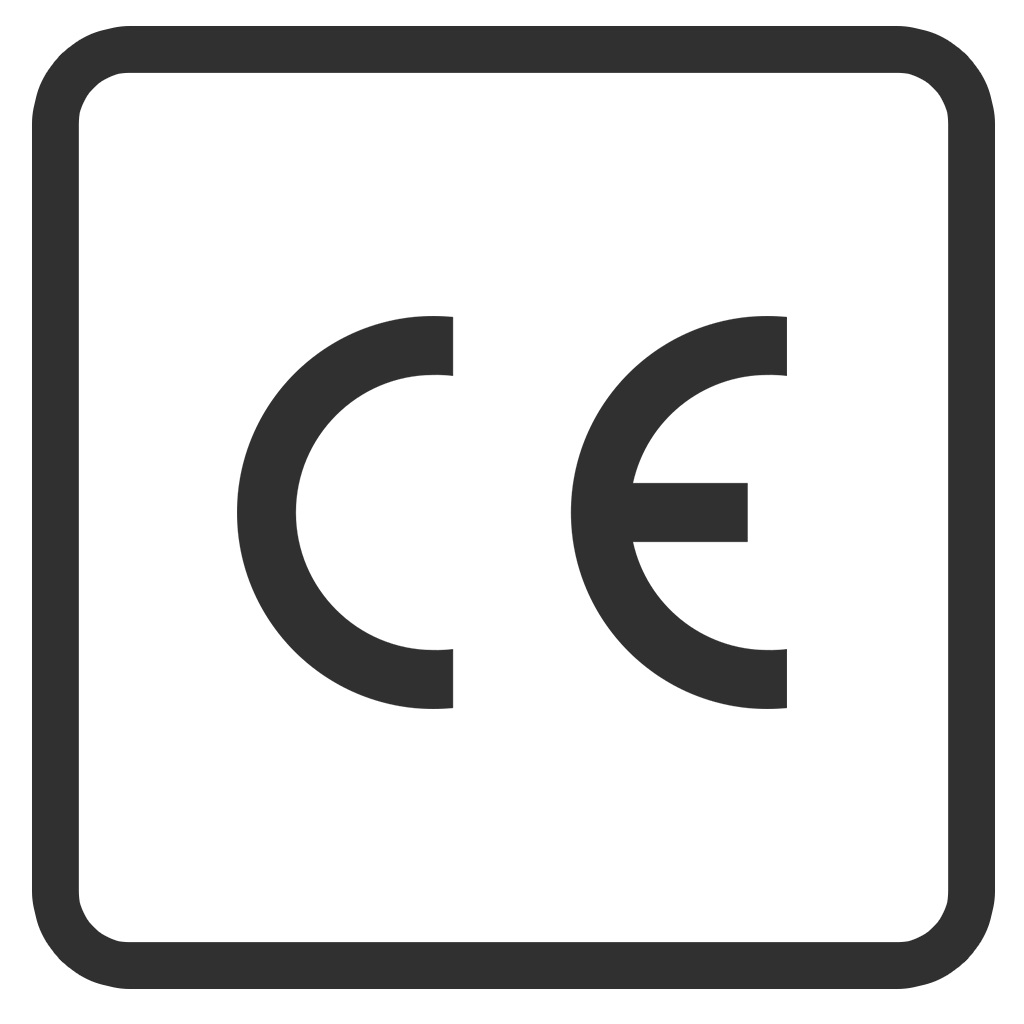
Drive units
Together with the extrex6 we can also provide the drive unit as a package. For optimum performance it is important the drive units are calculated to the application requirements and as accurately as possible. Maag has both the experts and high level modeling programs to assure just the right combination of torque, speed and efficiency.
Newly introduced is our Dual Drive unit designed for high abrasive, recycling and Fluoro polymer applications. The Dual drive unit is a Maag own development to bring up an economical and effective solution for processes requiring minimum gear toothand loading.
Calculated to your applications by expert with high level modeling capability
Complete service solution
Contact free operation of the gear pump
Longer lifetime of the gear pump
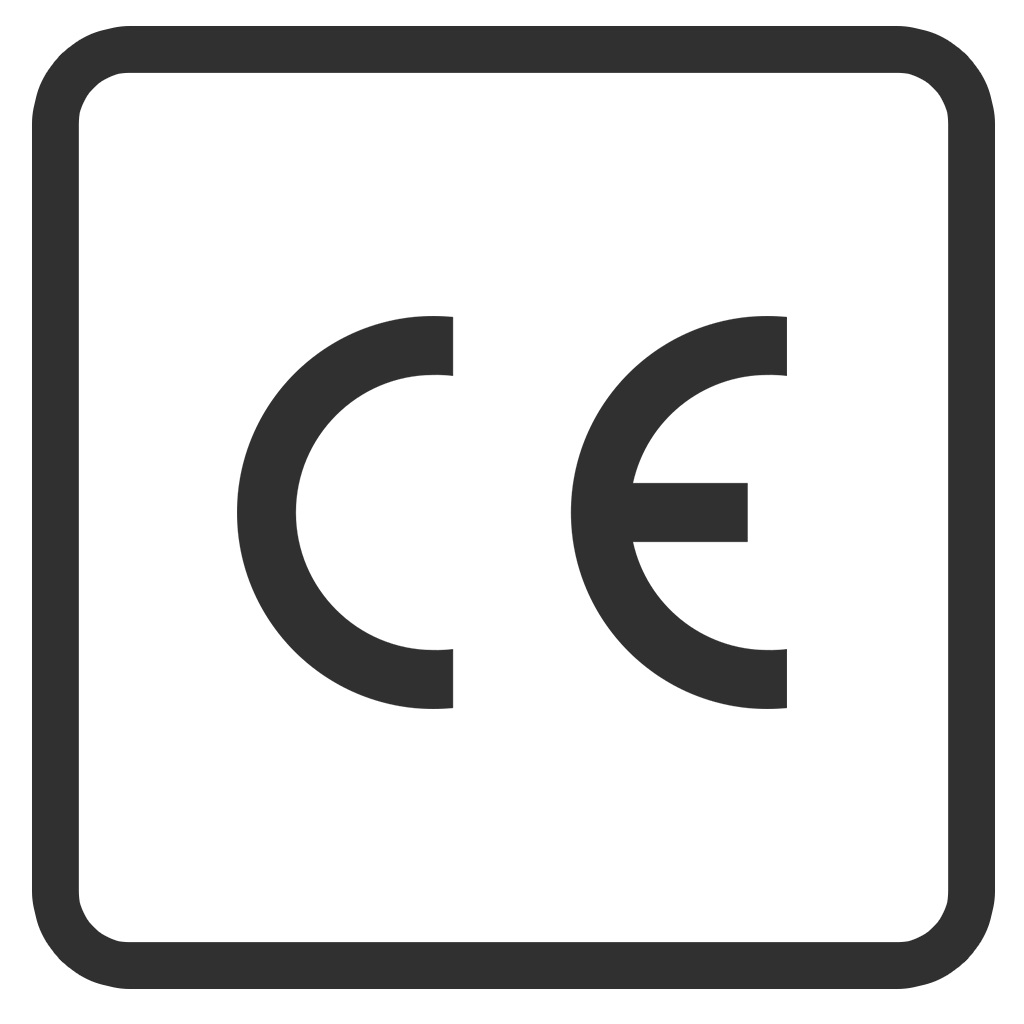
Maxx BF
Automatic self cleaning backflush screen changer for filtration systems
Maax® BF is MAAG’s well-proven control system for the fully automatic backflush screen changers. It allows the processor of highly contaminated polymer melts simple handling of the backflush screen changer and fully automatic screen cleaning for multiple use of the built-in screens. The automation system is particularly well suited for retrofitting extrusion lines with automatic self cleaning screen changers with backflush function. Operation, control, regulation, and monitoring of operating parameters are simplified. Process and operation reliability of the filtration systems of the entire system are increased.
Simple and clear operation of filter and system functions
Increased productivity through storage of recipes in parameter lists
Integrated temperature control of the system components
Rapid error detection via clear text messages
Scalable visualization of different operation parameters in a trend display
Increased productivity
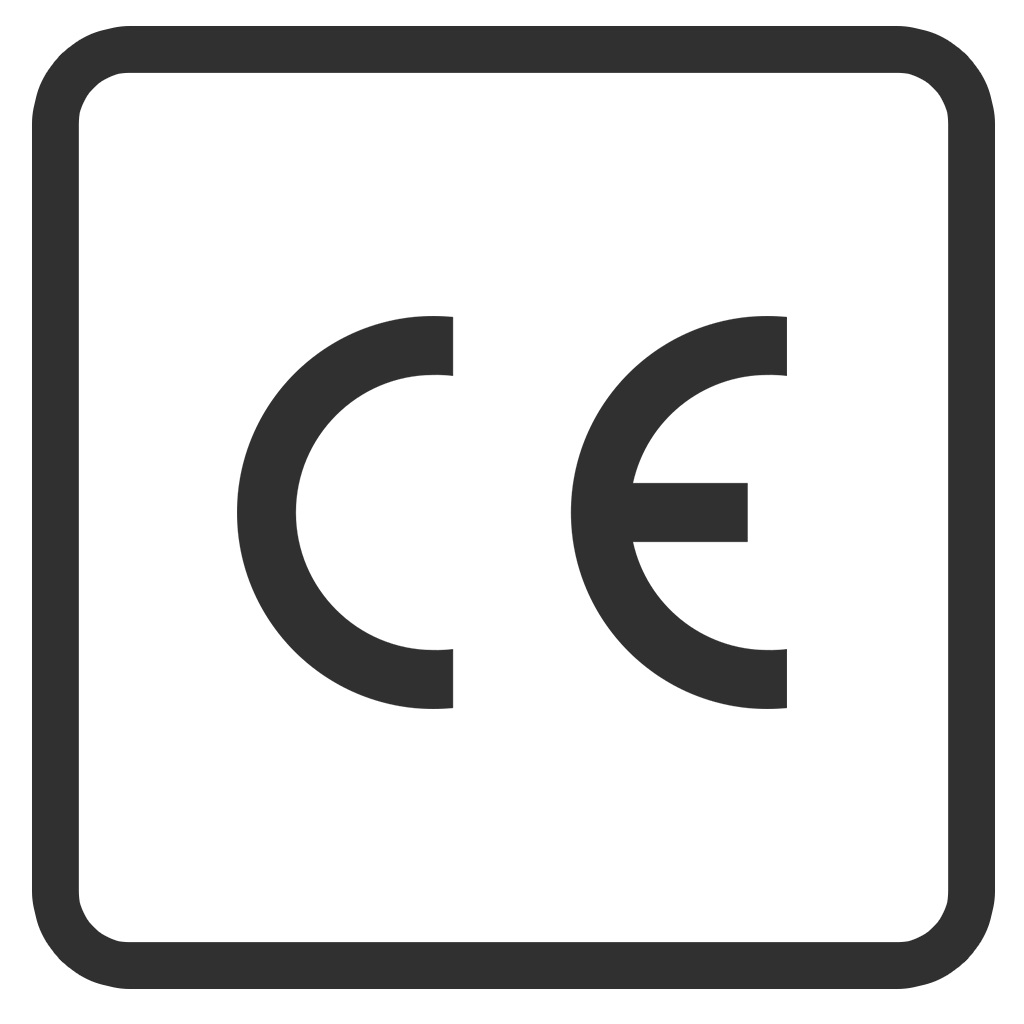
Maax 3S
Automation system for retrofitting in extrusion lines
The automation system maax® 3S simplifies the operation, control, regulation, and monitoring of the operating parameters. Production data are displayed transparently and operation is simple and intuitive. Process and production safety of the line are increased. The maax® 3S automation system is particularly suitable for the retrofitting of gear pumps or screen changers in extrusion lines.
Simple and clear operation of the start-up and shutdown routines
Modular expansion to include screen changer controllers
Quick and precise control of the extruder or pump speeds
Independent start-up and production control of the pump speed
Integrated temperature control of the line components
Fast troubleshooting thanks to plain text messages
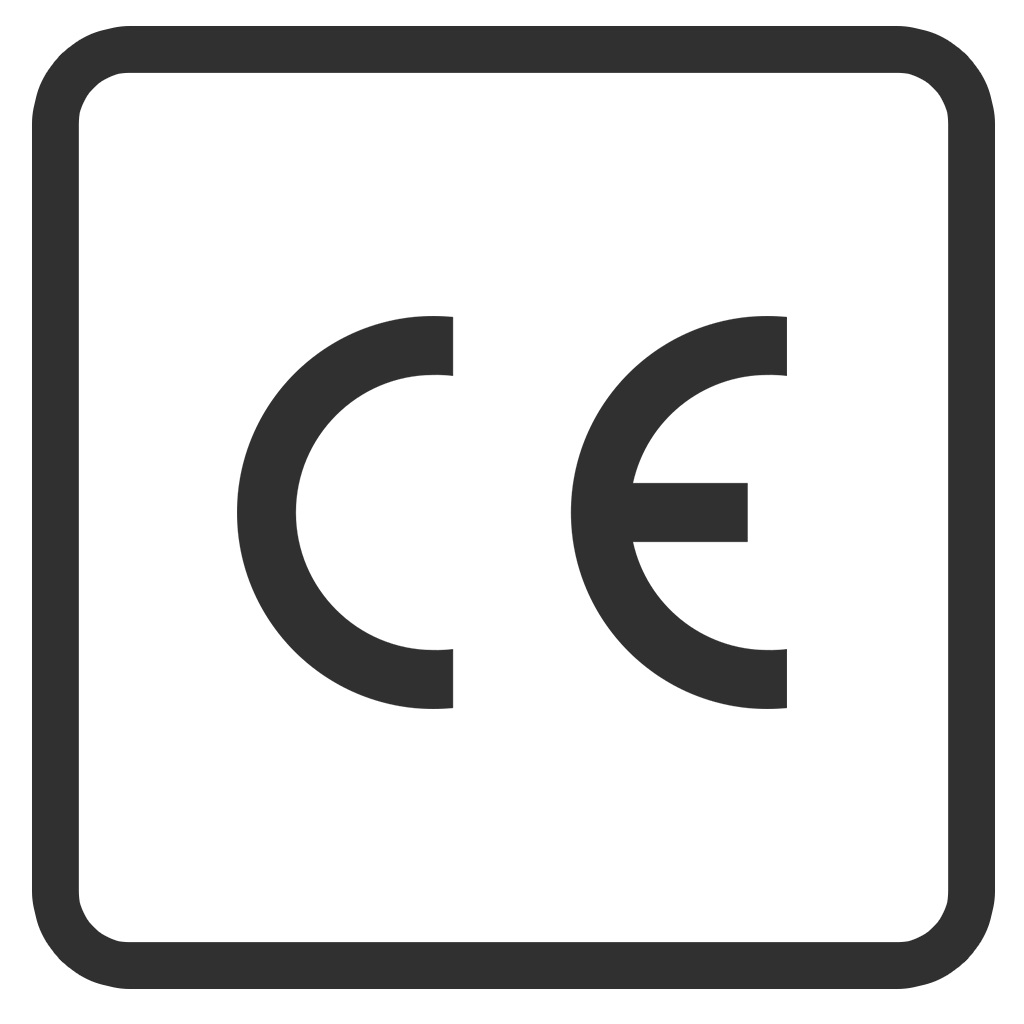
Maax 100S / 400S / 600S
Extrusion gear pump and melt pump system for the polymer extrusion industry
The maax® automation system simplifies operation, control, adjustment, and monitoring of the operating parameters. This guarantees optimum protection and operation of the extrusion gear pump system, melt pump system, and screen changer. Process and operational reliability of the entire system is increased. The maax® 100S automation system is the ideal solution for integrating melt pumps and screen changers into the extrusion line. maax® 400S is for upgrading coextrusion lines. The maax® 600S automation system is the ideal solution for equipping complete and complex extrusion and compounding plants in the polymer extrusion industry.
Simple and clear operation of the line-start and stop proceures
Increased productivity, by saving recipies in parameter lists
Rapid and precise control of extruder and pump speed, depending on application
Integrated temperature control of system components
Quick error detection by plain text messages
Scalable visualisation of various operating parameters in a trend display
Additional for maax® 100S/400S/600S: configurable System and Software configuration
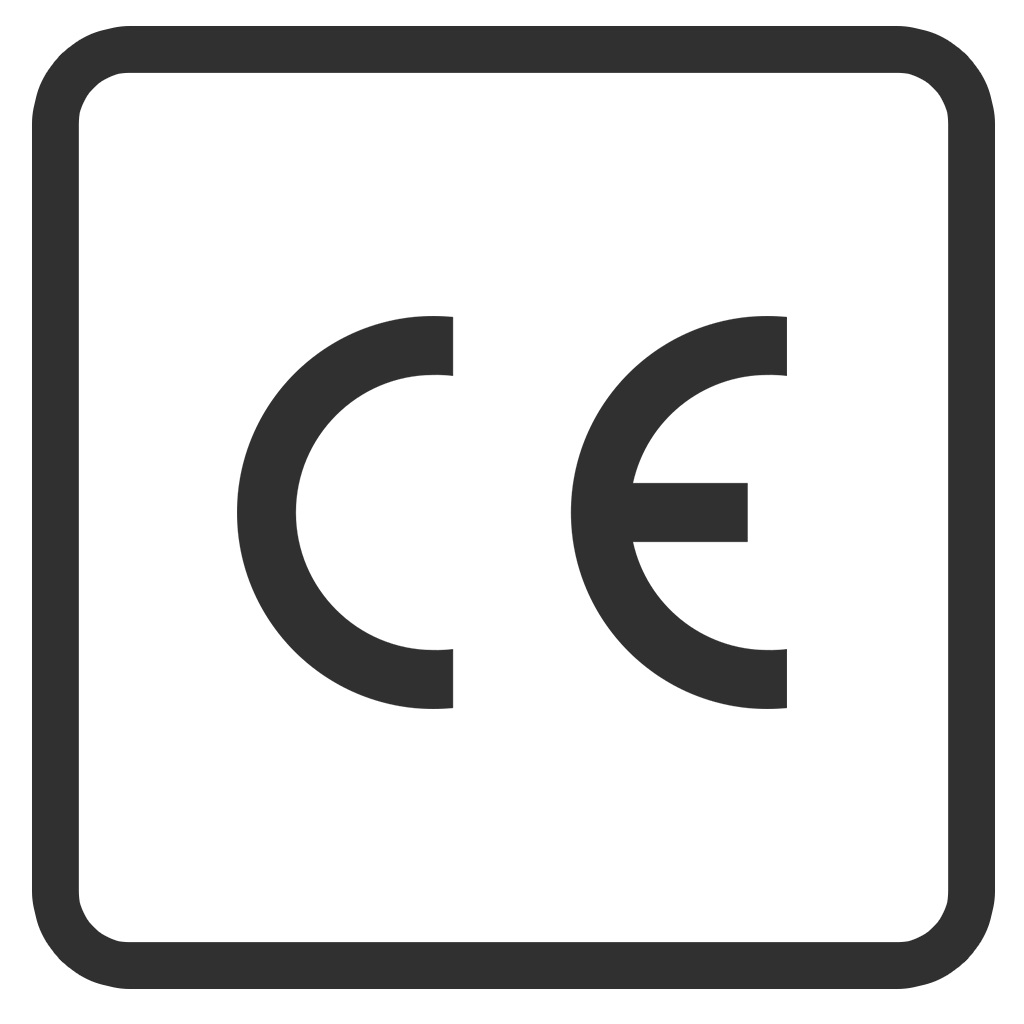
Single Mechanical Seal
Chemical pumps and chemical transfer pumps for abrasive fluids in industrial applications
This seal on the chemical transfer pump is applicable for high temperatures. A different material combination is available for aggressive and corrosive media. The sealing ring in SSiC can be used for abrasive fluids in industrial applications.
For corrosive fluids: Good fit
For abrasive fluids: Good fit (with SSiC)
TA-Luft certified: No
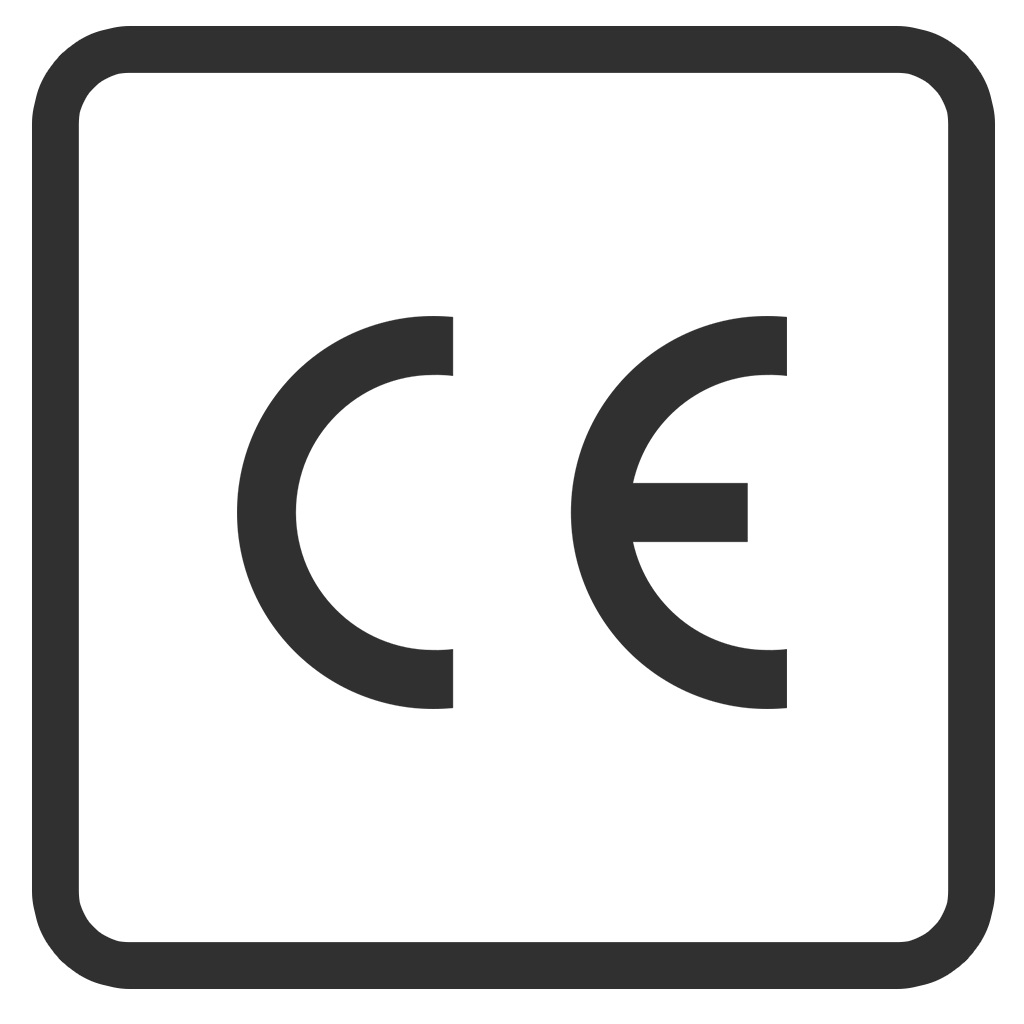
Double Mechanical Seal
Seal with buffer fluid for chemical pumps and chemical transfer pumps in industrial applications
The Double Mechanical Seal is a MAAG brand for industrial application and chemical pumps. It has a robust design with buffer fluid. Therefore, it is suitable for corrosive and abrasive applications. The sealing rings are available in carbon and SSiC (sintered silicon carbide ceramic) for chemical transfer pumps.
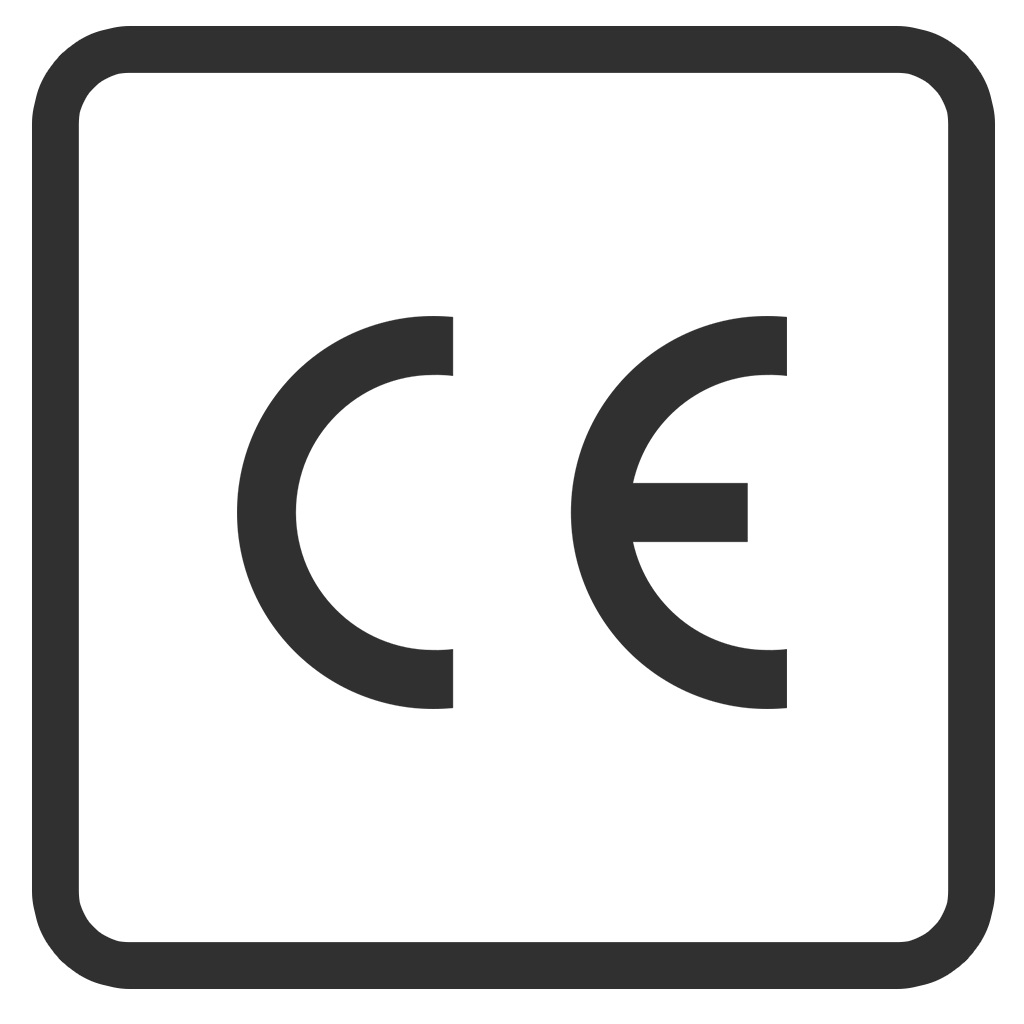
Blendrex®
Polymer processing, polymer systems, and polymer applications for extrusion in the polymer industry
MAAG specializes in the design and application of blendrex® heat exchangers used to preheat polystyrene melt prior to devolatilization and to cool polyester prior to spinning or pelletizing by polymer processing. blendrex® heat exchangers are problem solvers for many types of difficult heating and cooling polymer applications.
Significantly improve heat transfer rates of polymers and other viscous products. Three to seven times the rate obtainable compared to an “open tube” (no blendrex® elements) design
Provide a shorter product residence time inside the unit
blendrex® tube is a “plug flow” device
Tubes eliminate localized “hot spots”, and provides uniform temperature profile across the tube section
Contain alternating helical twist elements to obtain the high performance capabilities
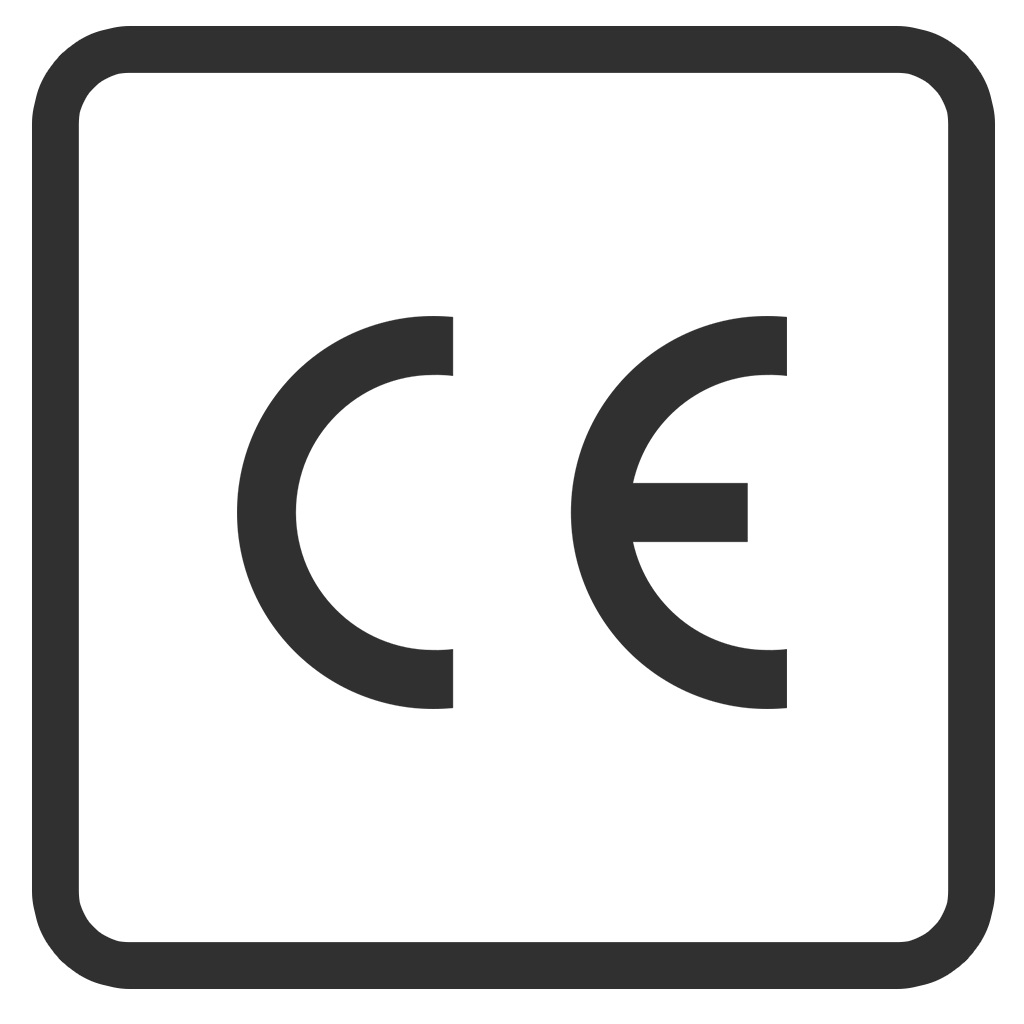
TUMBLER™
Pellet Processing Systems for the Plastics and Adhesive Industries
The Gala Tumbler may be used as a defluidizer or dryer for brittle products, a pellet coater for tacky products, or a pellet classifier for any type of product.
Aluminum case
Stainless steel drum
Folding doors
Leveling equipment
The drum can be completely removed
May absorb solids or liquids
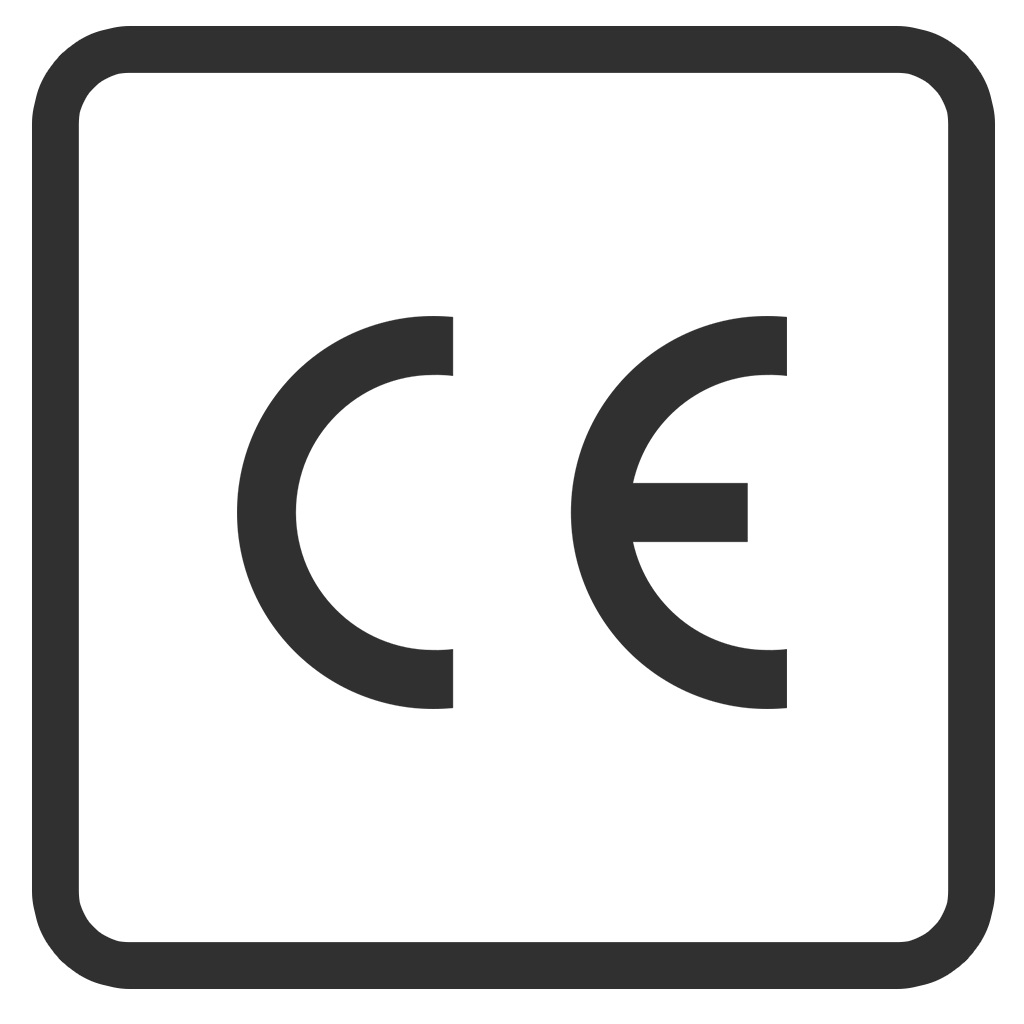
DURO
Efficient pellet drying technology for abrasive pellets
The DURO belt dryer in combination with the underwater pelletizing systems from Gala and Automatik is the perfect solution for the production of abrasive or brittle pellets such as compounds highly filled with fiber glass or minerals. The drying process does not use any rotating parts and thus is a very gentle process reducing costs related to wear to a minimum.
The most gentle handling of pellets
Minimal dust
High product quality
Minimized life cycle costs
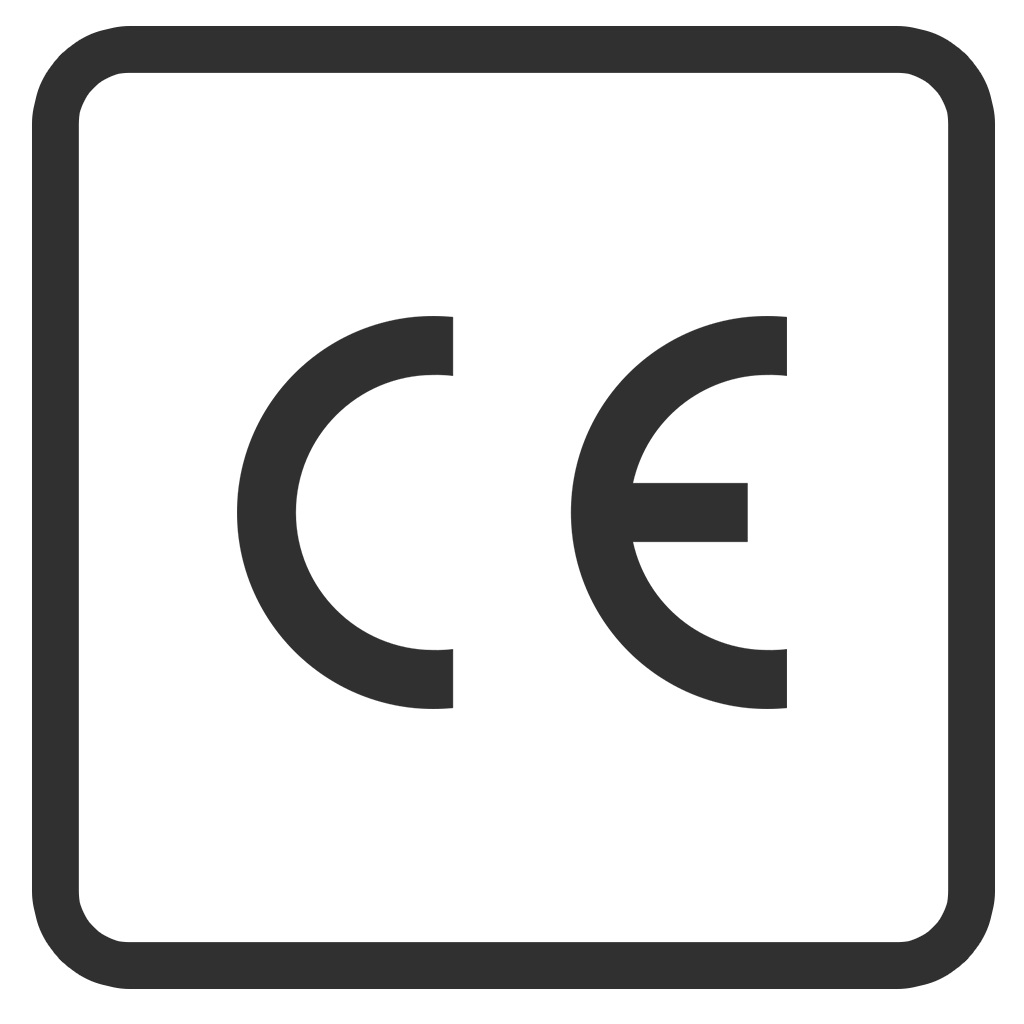
Centrifugal Dryer for Recycled Products
Centrifugal Dryer for Recycled Products
Pellet dryer designs are based on current product rate testing. Gala has been conducting extensive testing on our centrifugal recycled plastic pellet dryers at full production rates since early 2007.
Door timed interlocks
Easy access
FEA designed
Clean operation
Low noise emissions
Low energy consumption
Suitable for various applications
Minimum floor space
Proven reliability
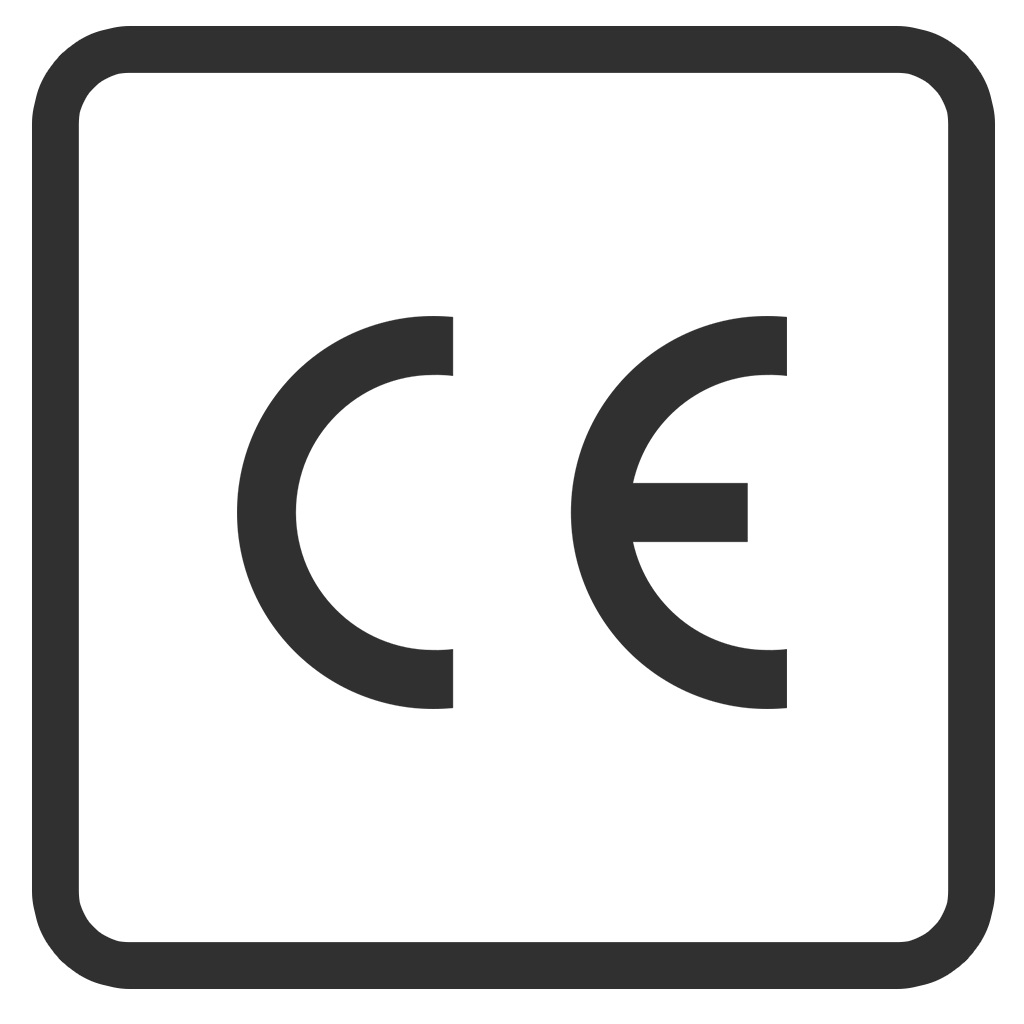