MAAG Company
The MAAG Group comprises successful and renowned companies, each with their own impressive history. Automatik Plastics Machinery, Ettlinger Kunststoffmaschinen, Maag Pump Systems, Gala Industries, Reduction Engineering Scheer and Xantec Steuerungs- und EDV Technik are today the strong and innovative product brands of the MAAG Group.
The history of the MAAG Group thus begins in the late 19th century, with the establishment of Scheer as a metal foundry and machine factory in Stuttgart, Germany, in 1890. Maag Pump Systems was founded in 1913. Automatik Plastics Machinery was founded in 1947. Gala Industries was founded in 1959, and Ettlinger Kunststoffmaschinen in 1983. The youngest member of MAAG Group – Xantec Steuerungs- und EDV-Technik was founded in 1994. Over the decades, they have all grown into experts in the various fields of polymer production and processing.
All the members of the MAAG Group contribute their supreme expertise and years of experience in developing and manufacturing superb machines, plants, systems, and software – and will continue doing so in the future. The bundling of core competencies, industry best practices, the attentive maintenance of existing business relationships and creation of new ones, all provide the foundations for maximum customer satisfaction throughout the Group.
HSC
Manual screen changer and plate screen changer for filtration solutions and extrusion processes
Manual screen changers from MAAG have been the first choice of cost-effective filtration systems in extrusion lines for many years. Starting at size 45, the manual screen changers optionally come with transmission gearing.
Simple operation with quick screen change
High operational reliability
Short material residence time
Leak-free mode of operation
Low pressure consumption
Flow channel geometry without any dead spots
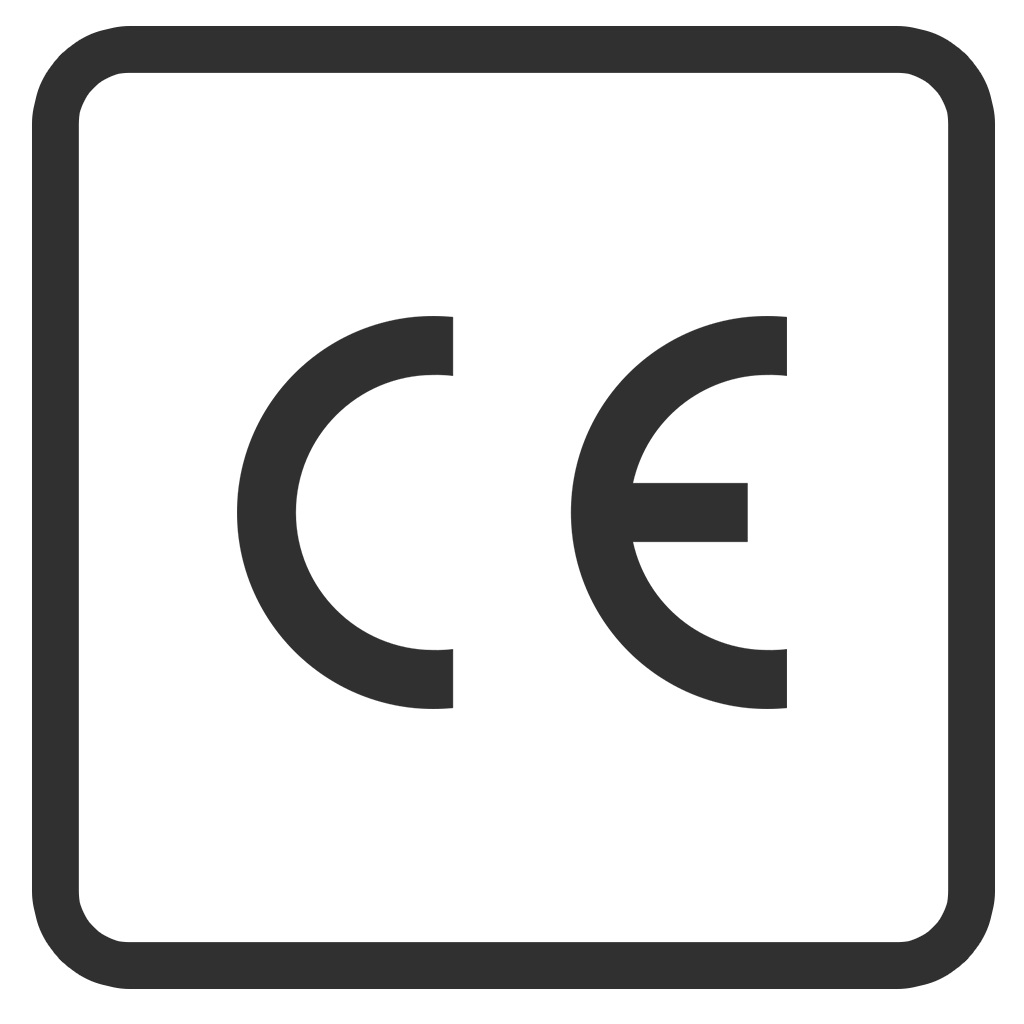
FSC
Hydraulic screen changer for filtration systems and polymer production
FSC hydraulic screen changers from MAAG are equipped with a pressure-adaptive sealing system as a standard for filtration systems. Thanks to this sealing system, the required sealing forces are automatically adjusted by the screen changer to the actual melt pressure.
Simple operation and uncomplicated screen changing
High operational reliability
Short material residence time
Leak-free mode of operation
Low pressure consumption
Flow channel geometry without any dead spots
Short residence time
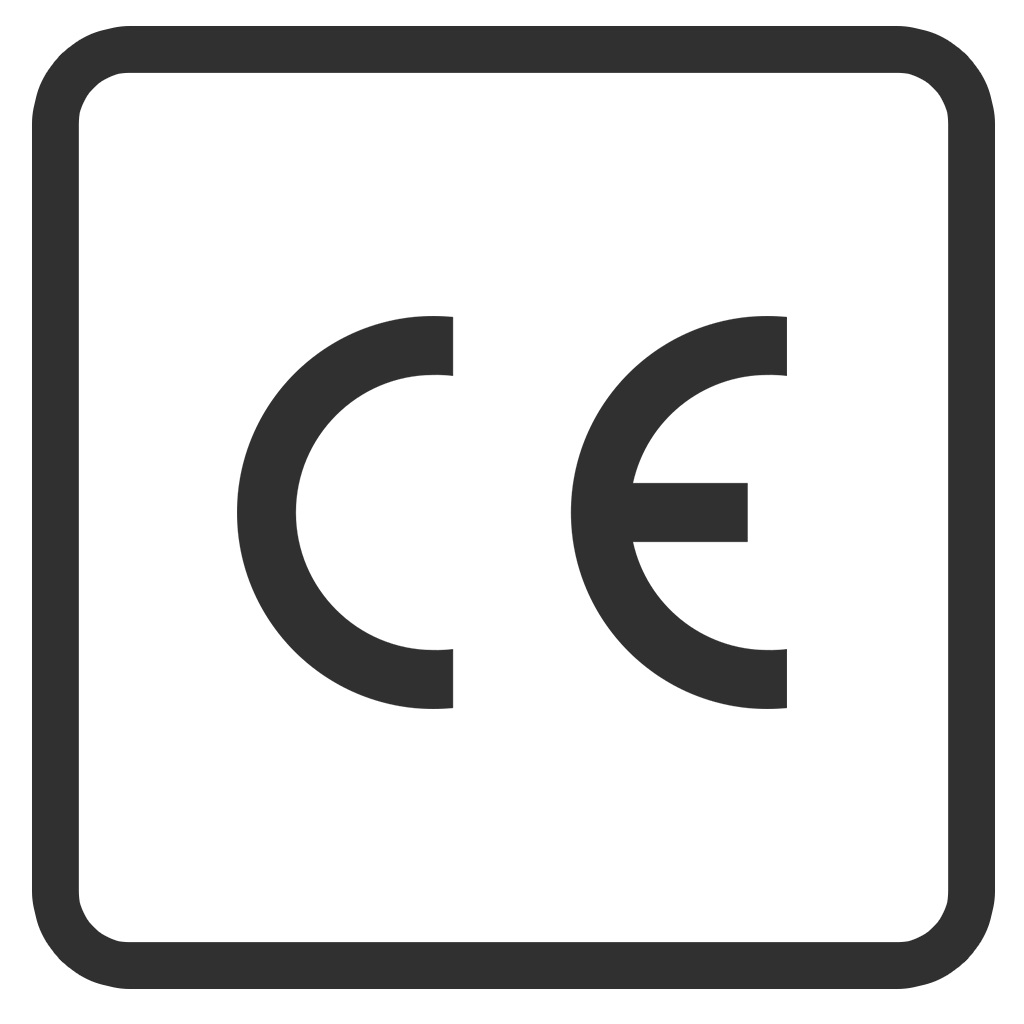
SSC
Effective single piston screen changer for reliable melt cost effective filtration solution
The compact single-piston screen changers SSC from MAAG provide a cost-effective filtration alternative for extrusion applications which allow for interruptions in the melt stream during screen changeovers. SSC operate without any additional seal.
Simple operation and uncomplicated screen changing
High operational reliability
Short material residence time
Leak-free mode of operation
Low pressure consumption
Flow channel geometry without any dead spots
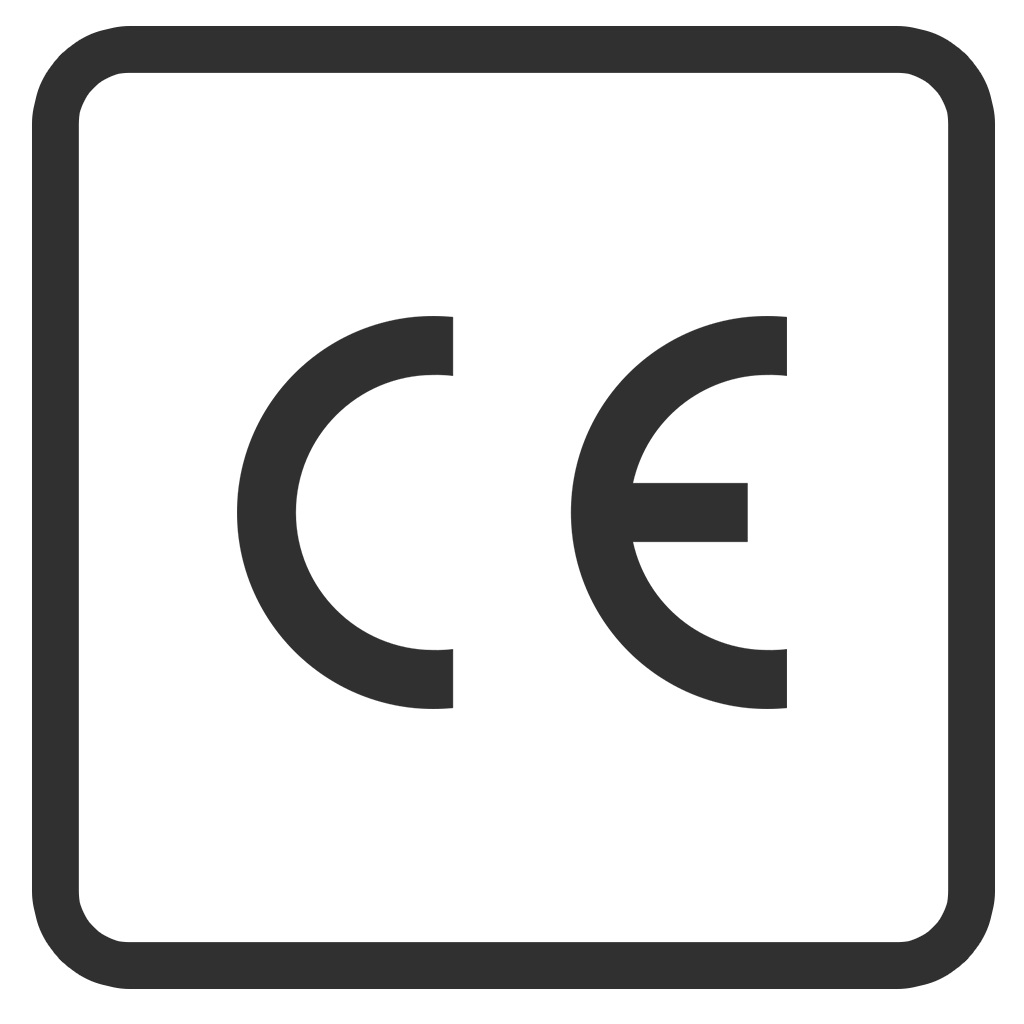
DSC
Single piston screen changer for filtration systems and demanding extrusion process
The discontinuously operating single piston screen changer, equipped with a screen cavity, offers a robust and economic alternative for extrusion and compounding applications which permit a brief interruption in the melt flow when changing the screen.
Simple operation and uncomplicated screen changing
High operational reliability
Short material residence time
Leak-free mode of operation
Low pressure consumption
Flow channel geometry without any dead spots
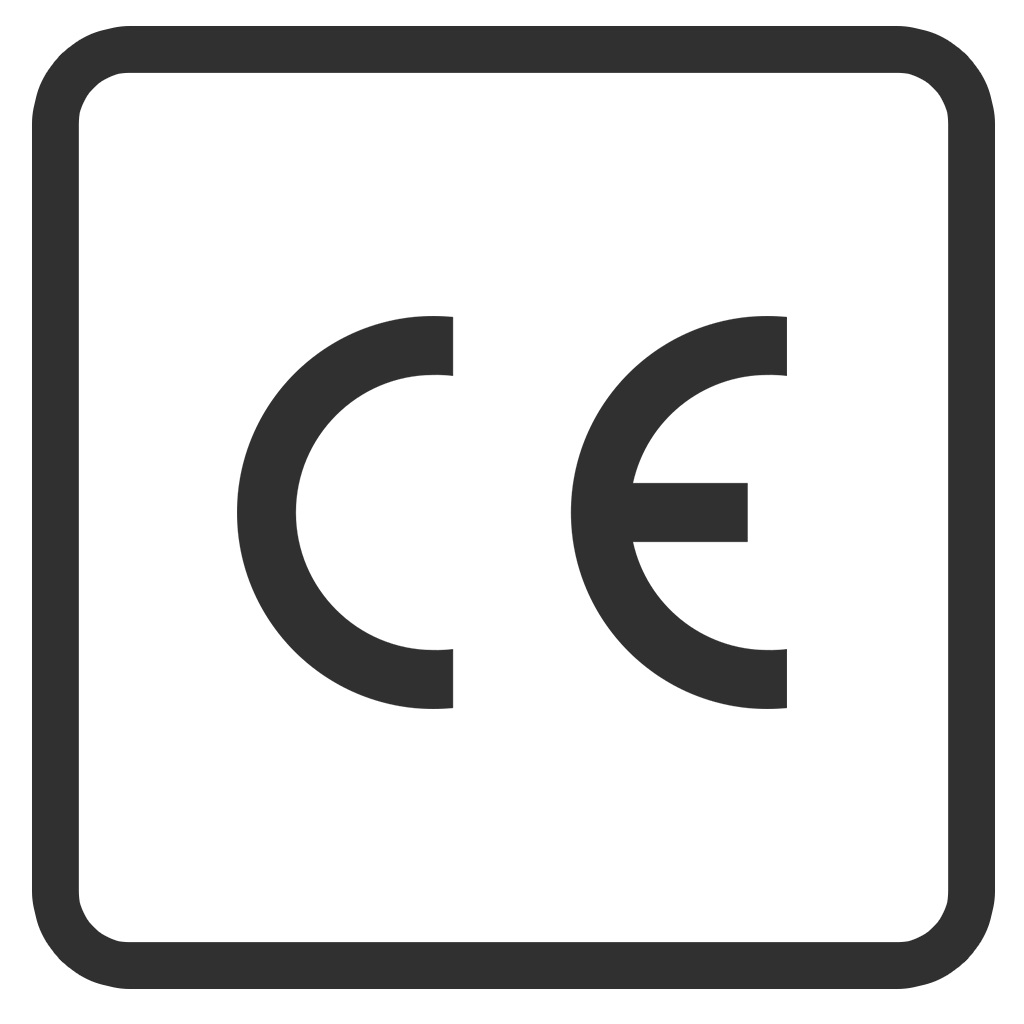
Extrex-Y adapter
Twin outlet gear pump for complex extrusion applications
The extrex⁶ Y-Adaptor unites two extrex x⁶ class gear pumps to ensure optimum efficiency and cost-effectiveness in extrusion systems.
Multilayer films
Improved output consistency
Larger range of applications
Short delays
Compact design
Self-cleaning properties
Extrex⁶ MP
Maximum Pressure gear pump for your thermoplastic applications
Extrusion operations require extremely reliable gear pump systems with high output consistency and a confi guration to suit each application.
More spec. St. than trudex
Greater wear resistance
Larger sealing surface
Lower energy consumption
Lower temperature rise
Less pulsation
thermorex⁶ TR/TB/TP
Booster pump for the polymer industry
Polymer processes require booster pumps and polymer metering pumps that gently process both high and low viscosity plastic melt through the polymer processing system.
High-pressure pump
Different polymers
Long life
Challenging applications
extrex⁶ EP
Extra Pressure gear pump for thermoplastic applications
The extrex6 EP gear pump is an intermediate pressure solution for applications requiring higher pressure, greater load bearing considerations for low lubricity products. With the new x6 class design you have additional benefits compared to the classic gear pump designs.
Higher pressure than GP
More spec. St. than HP
Greater wear resistance
Larger sealing surface
Lower energy consumption
Lower temperature rise
Less pulsation
extrex⁶ SP
Super Pressure gear pump solution for thermoplastic applications
The extrex⁶ SP gear pump is a high pressure gear pump for applications dictating high pressures and loads. With the new x⁶ class design you have additional benefits compared to the classic gear pump designs.
Higher pressure than GP
More spec. St. than HP
Greater wear resistance
Larger sealing surface
Lower energy consumption
Lower temperature rise
Less pulsation
extrex⁶ GU
General Use gear pump for thermoplastic applications
Extrusion operations require extremely reliable gear pump systems with high output consistency and a configuration to suit each application.
More resistant to wear
Larger sealing surface
Lower energy consumption
Lower temperature rise
Less pulsation
extrex® PFS – 20GP
Gear pump for the pharmaceutical industry
The extrex® PFS gear pumps are specially designed for applications in the pharmaceutical industries. Such applications require specific design characteristics: high discharge pressure capability, constant throughput, gentle conveying, and narrow temperature ranges. In such an environment, the proven extrex® gear pumps unfold their full potential.
Self-cleaning properties
Accurate dosing
Pulsation elimination
Effective pressure increase
Low energy
Improved quality
Necessary micropellets
Compatible