PEARLO®
Underwater pelletizers for highly profitable throughput rates of up to 36,000 kg per hour
The PEARLO® underwater pelletizer has been designed to process a wide range of polymers and thermoplastics. PEARLO® works perfectly with our process water system PURO® and pellet dryer CYCLO® and produces first-class spherical pellets.
Excellent quality of pellets
Opening / closing the cutting chamber with one hand
Quick product change
Unrivaled long life
Maintenance free automatic (EAC)
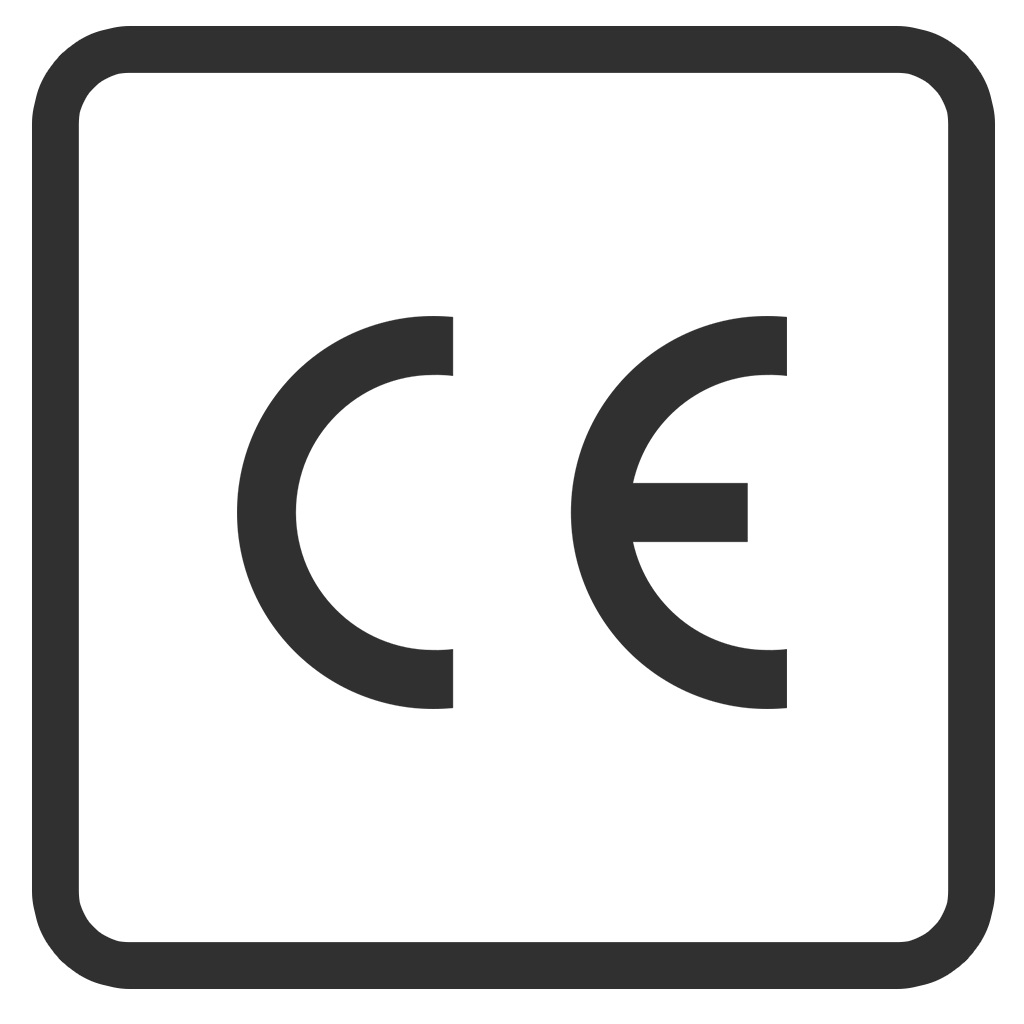
PEARLOFLEX SYSTEM®
Underwater Pelletizing System for frequent product and color changes up to 500 kg per hour
The PEARLOFLEX SYSTEM® for underwater pelletizing has been specifically designed to process polymers and thermoplastics and produces first-class spherical pellets. This extremely efficient and flexible underwater pelletizing system is applied in the production of compounds, masterbatches, engineeringg plastics, recyclate, organic and wood polymer composites, thermoplastic elastomers, and more.
Proven technology
Compact design
Changeover valve, pelletizer, dryer
Optionally with melt pump and / or filtration system
Easy operation
High flexibility
Automated (EAC)
Various water filtration options
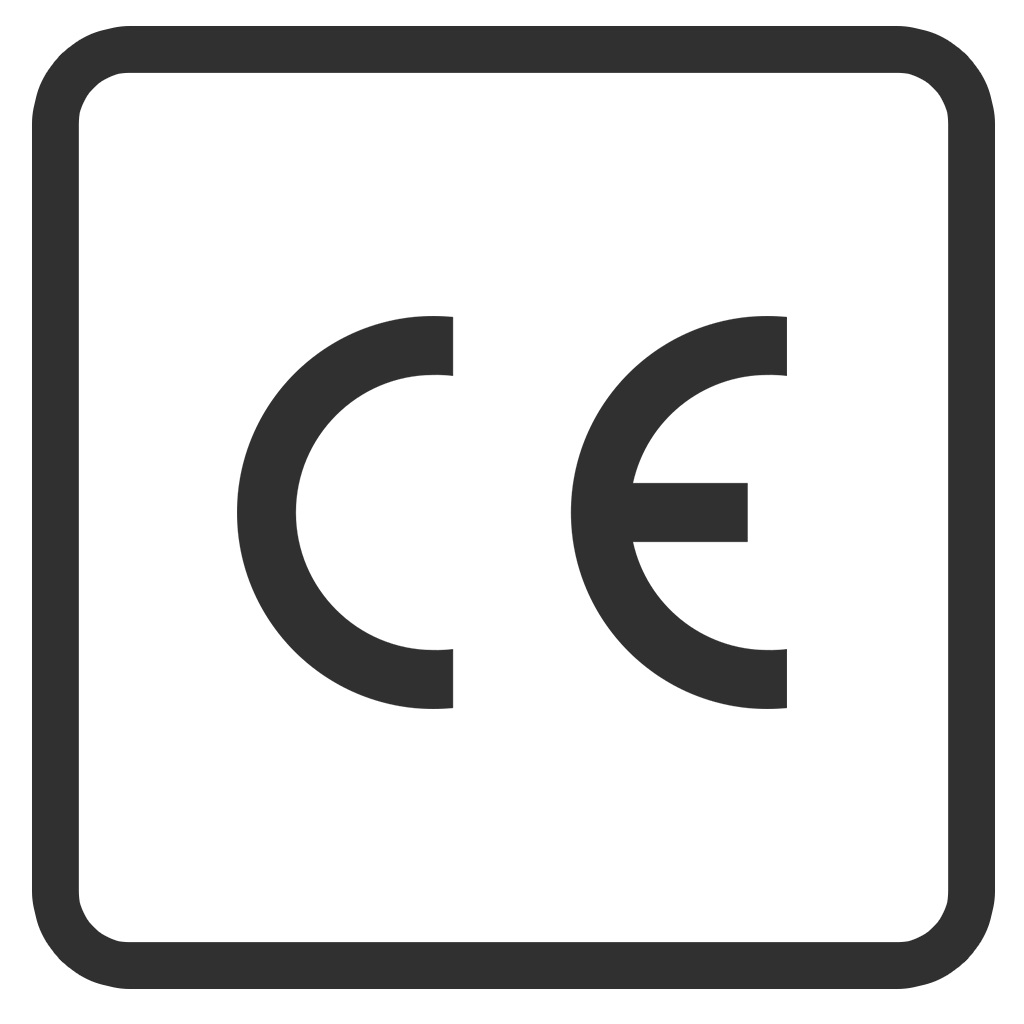
LPU® Laboratory Pelletizing System
Pellet Processing Systems for the Plastics Industry
Gala’s LPU® Laboratory Underwater Pelletizing System is specifically designed for laboratory developmental work, market sampling, and light pellet production on materials such as PE, PP, ABS, PA 6, PA 6.6, PET, PBT, PPO, and more. The system is designed for pelletizing rates up to 100 kg/h (20–220 lbs/hr), depending on the material for underwater pelletizing processes.
Easy to clean
Simple and easy operation
Lightweight, portable
Affordable
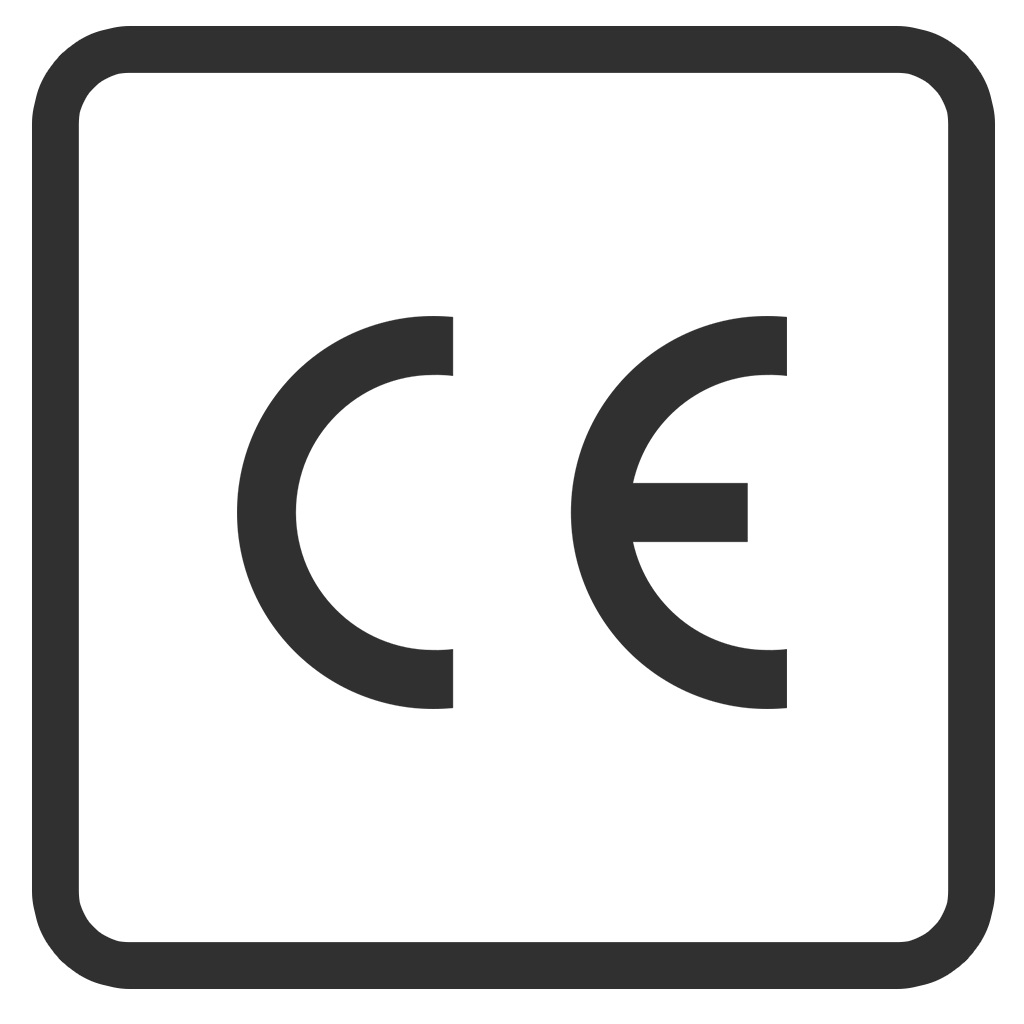
MAP
Manually Adjustable Pelletizer
The Manually Adjustable Pelletizer (MAP), a underwater pelletizing application, features a manual adjusting wheel to position the blades against the die plate. This simple blade adjustment design of the underwater pelletizer provides visual blade wear indication and maximum control of blade position. The unique design of the axial advance system replaces the need for a bearing housing assembly. The MAP design requires only one long life thrust bearing for accurate adjustments.
Easy blade adjustment
Application flexibility
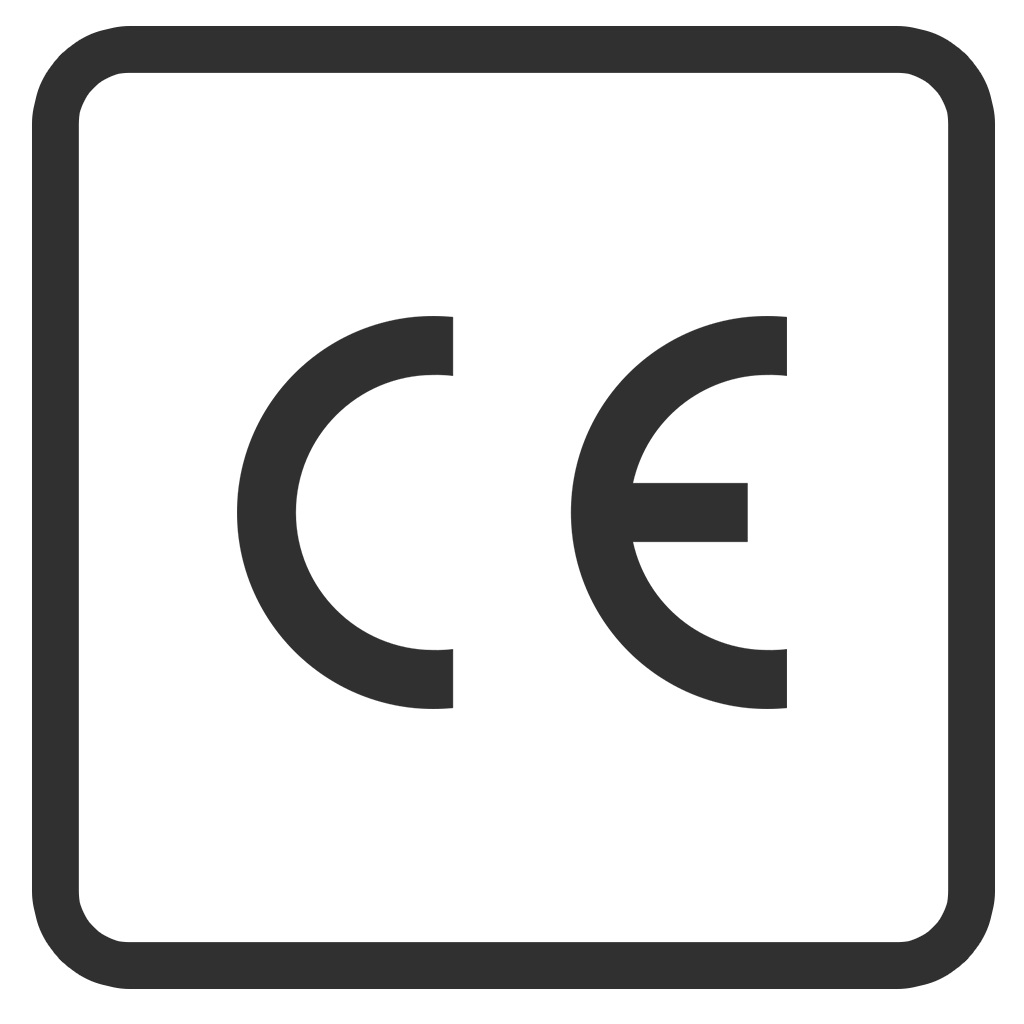
EAC
Electronically Adjustable Pelletizer
The EAC pelletizer for underwater pelletizing offers fully automated control of blade adjustment, positioning, and monitoring, resulting in maximum blade and die face life. Monitoring and adjustment processes are programmed in the Gala PLC controlled system. An optional integrated blade position measuring system for unterwater pelletizer is available, providing indication of blade position and warning of the need for a blade change.
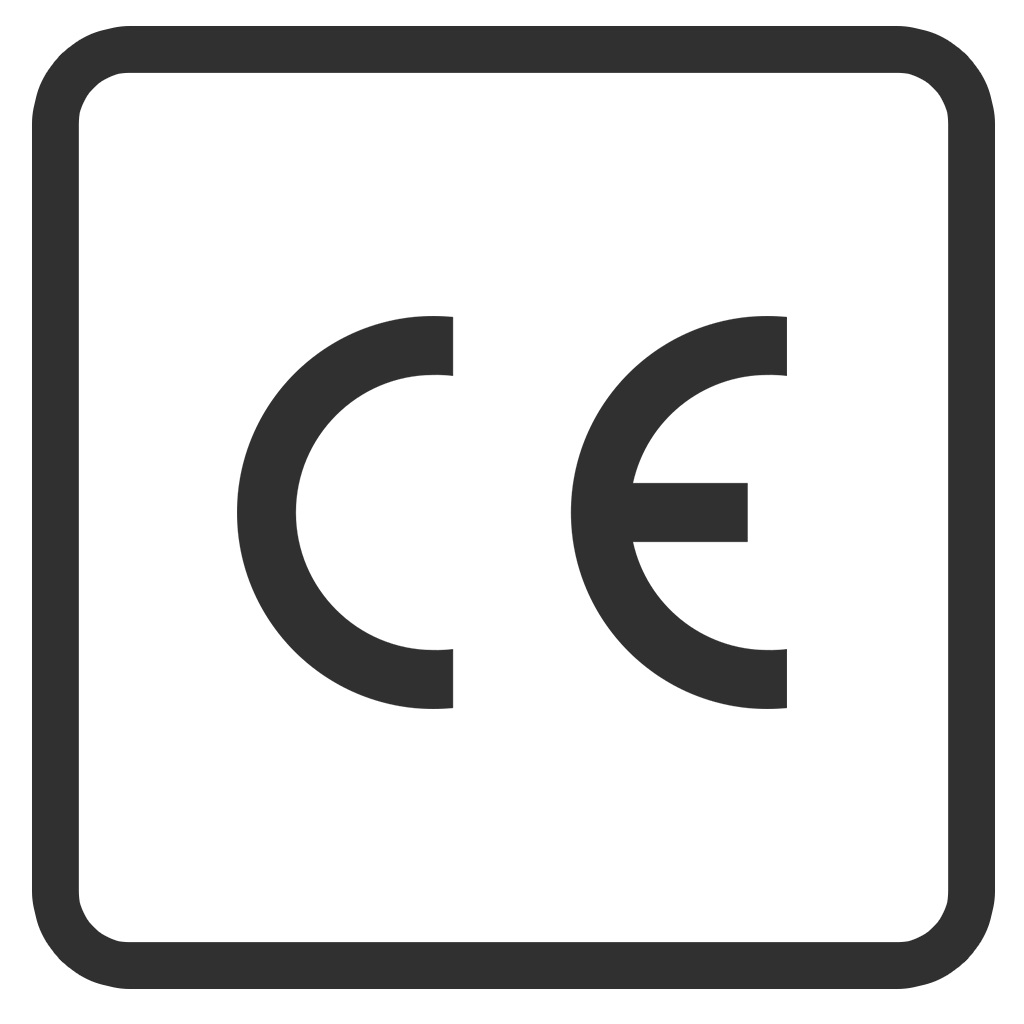
ZHULI®
Advanced, cost-effective underwater pelletizing technology
ZHULI® is an underwater pelletizing system with integrated pellet dryer and process water handling, designed to process a wide range of polymers and thermoplastics. The efficient system is characterized by high flexibility and small footprint. ZHULI® is manufactured locally with key components made in Germany. With an installed base of more than 9,000 underwater pelletizing systems, we help our customers to achieve the maximum level of profitability.
Ideal for all thermoplastics
Outputs up to 1,800 kg / h
Fully enclosed system
Small size and user friendly
Quick product exchange
Pellets of excellent quality
Long life
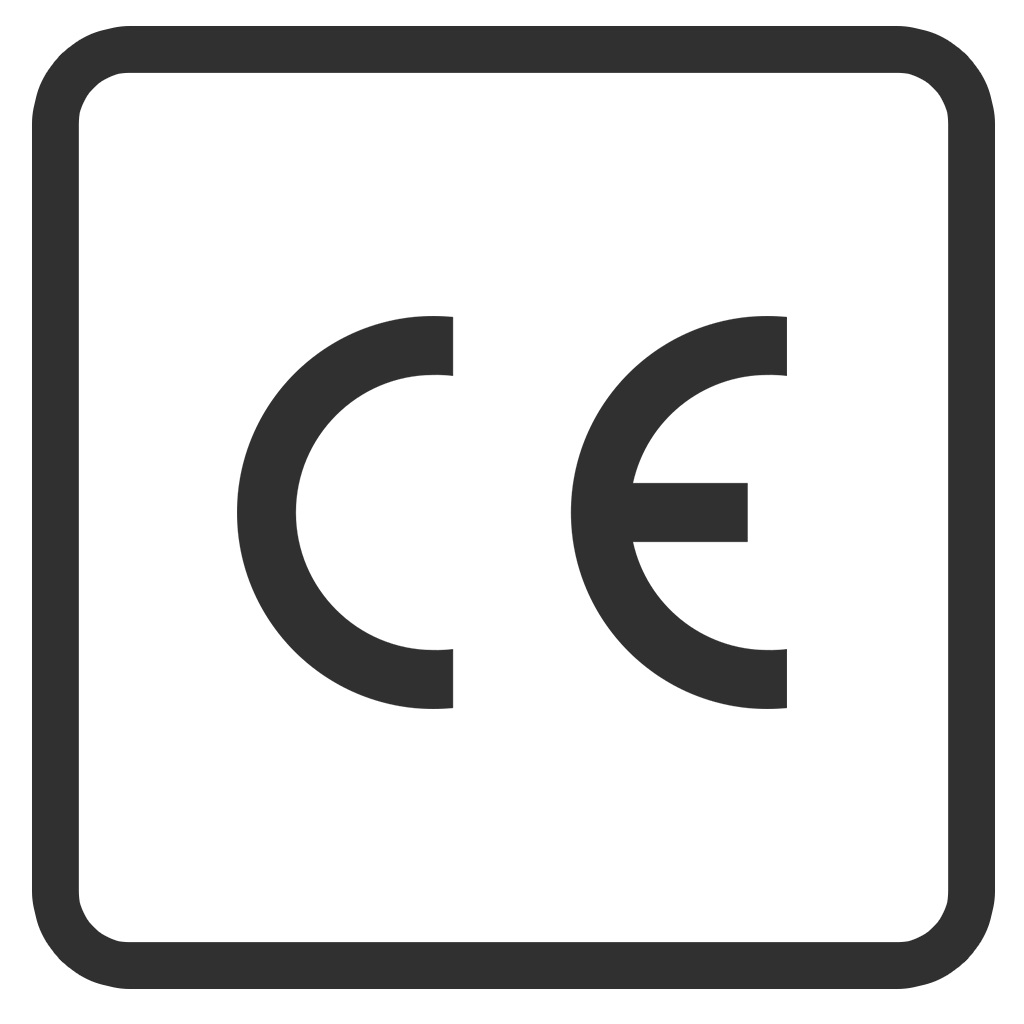
SLC
Spring-Loaded Pelletizer
The Spring Loaded Cutter (SLC) is a cost efficient solution for underwater pelletizing basic polymers at lower rates. The SLC pelletizer uses constant spring pressure to adjust the cutter blades to the die plate, reducing the need for operator attention and underwater cutting. The cutter hub is connected to the motor shaft through a telescoping spring sleeve, and the blades are automatically positioned against the die plate using spring force. The blade force can be adjusted per application or product by simply changing springs.
Cost effective solution
Simple control
Low maintenance
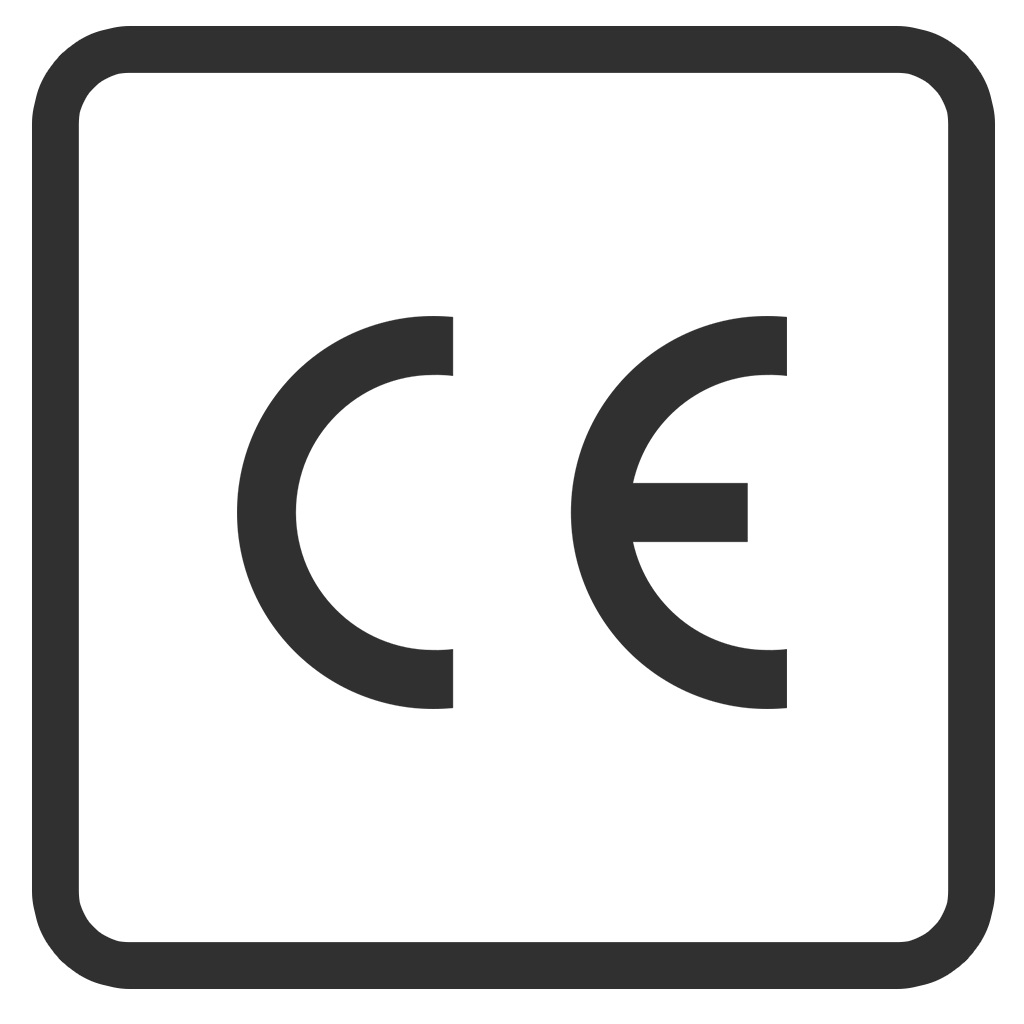
SPHERO®
Underwater pelletizing systems for highly profitable throughput rates of up to 36,000 kg per hour
The SPHERO® underwater pelletizing system has been particularly designed to process thermoplastics and produces spherical pellets. This most flexible system for underwater cutting is applied in the production of raw materials, compounds, masterbatches, engineering plastics, recyclate, organic and wood polymer composites, thermoplastics elastomers, microgranulate, hot-melt adhesives, and more.
It has reached the quality of a pellet
Convenient and safe service
Increased production performance
Fast product change
Optional approach
Increased process independence
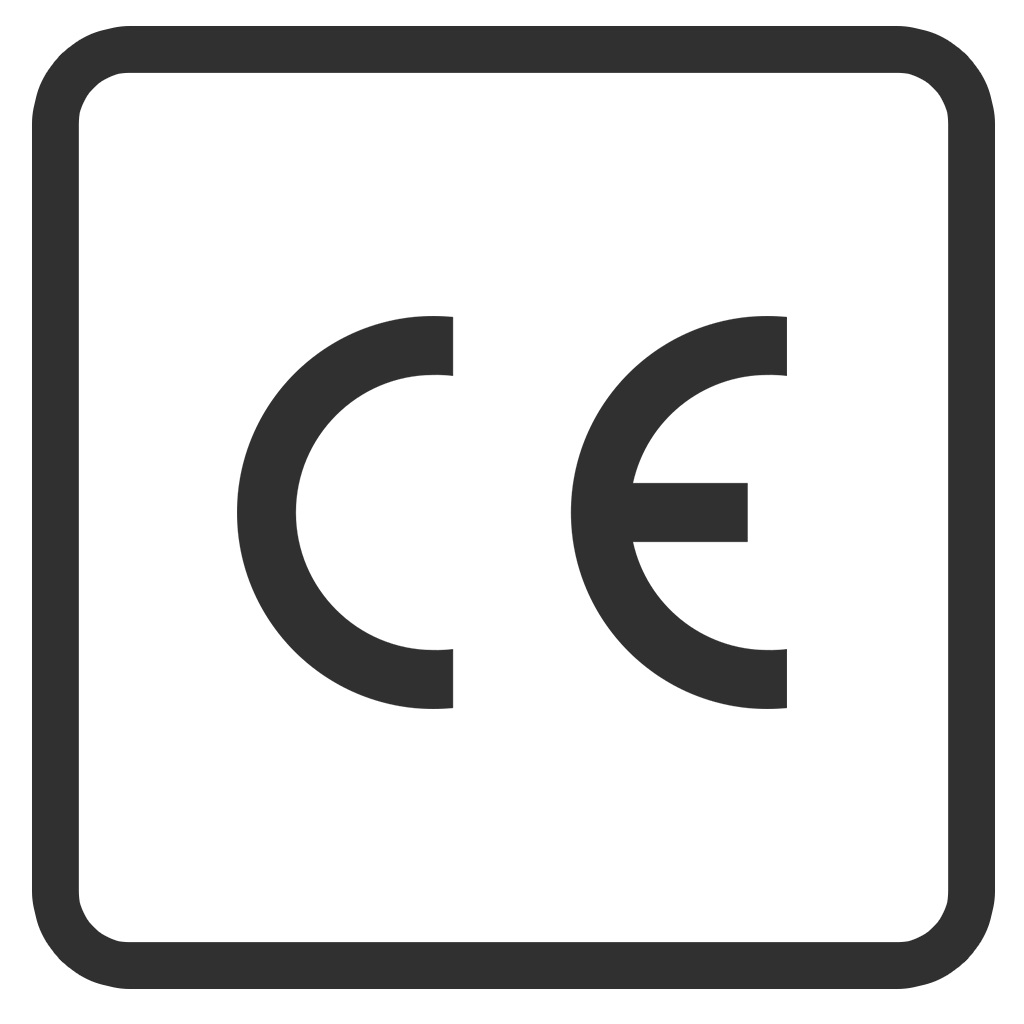
E-Series®
For pellet rates up to 1.500 kg/h, (depending on equipment configuration and polymers)
A value engineered underwater pelletizing system and underwater pelletizing process designed to economically pelletize and dry thermoplastics—polyethylene, polypropylene, polystyrene, rigid PVC, flexible PVC, and more—for polymer production at throughput rates of up to 1,500 kg/h (3307 lbs/hr.)
Simple and compact
Includes a fully functional control system
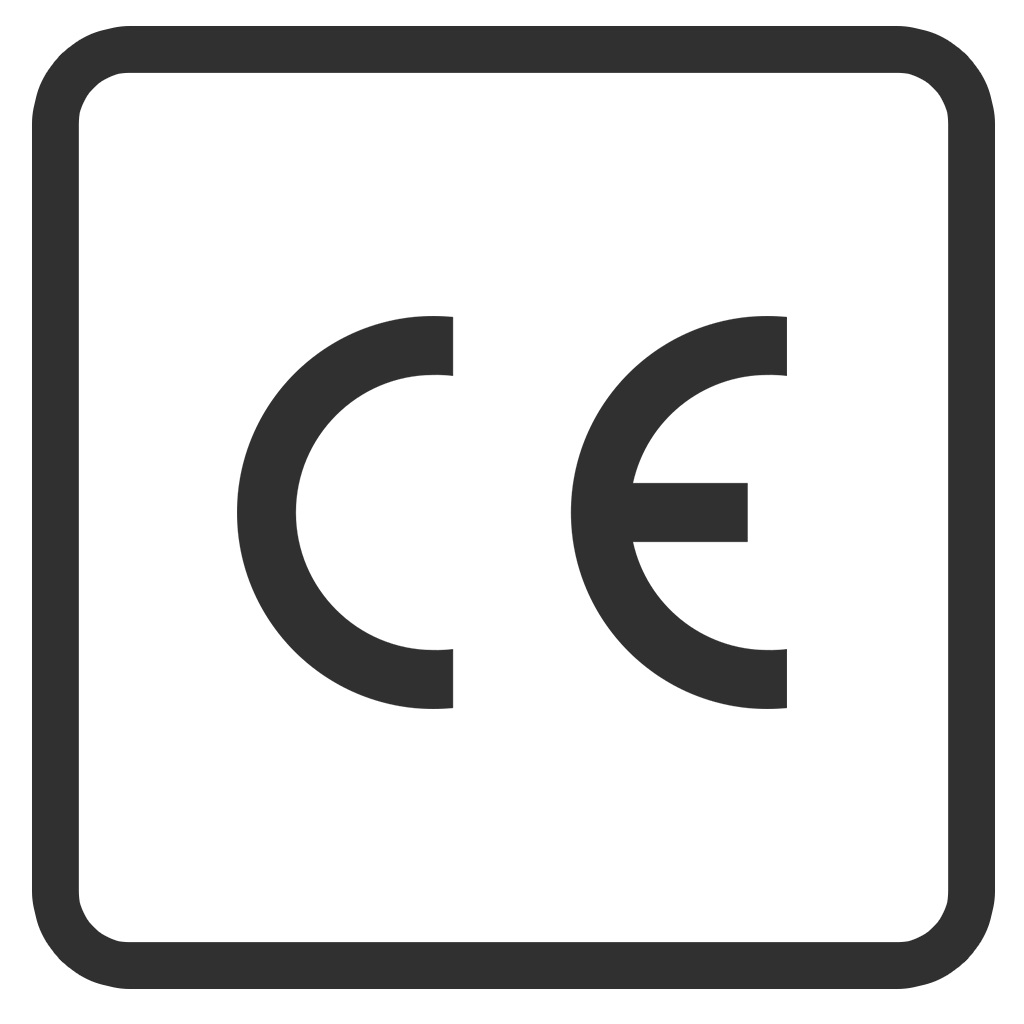
Flexline
The objective of the Flexline System for underwater pelletizing processes: The Flexline machine concept for underwater pellitizing systems is a logical extension of Gala technology. The machine concept permits complex product changes within a matter of minutes to minimize unproductive time for polymer and compound manufacturers.
Quick start
Minimal need for work
Flexibility in processing a wider range of recipes
Wear-resistant tools
Minimizes quality variations
Material savings
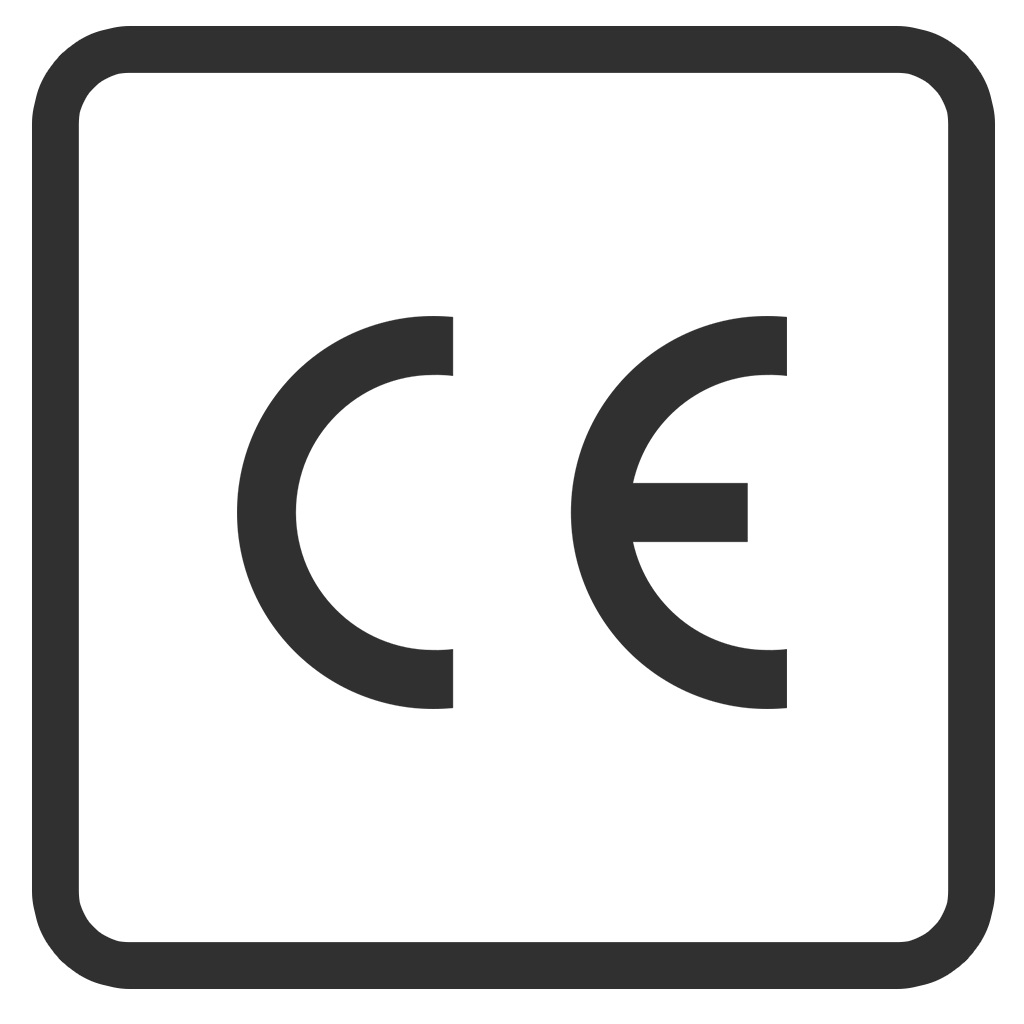
CLS Compact Lab System
Pellet Rates up to 500 kg/h
Gala’s COMPACT LAB SYSTEM, a underwater pelletizing system is used downstream of an extruder or gear pump for polymer production. Used in laboratory settings and by compounders when underwater pelletizing processes and drying samples of polyethylene, polypropylene, polystyrene, ABS, flexible PVC and other polymers.
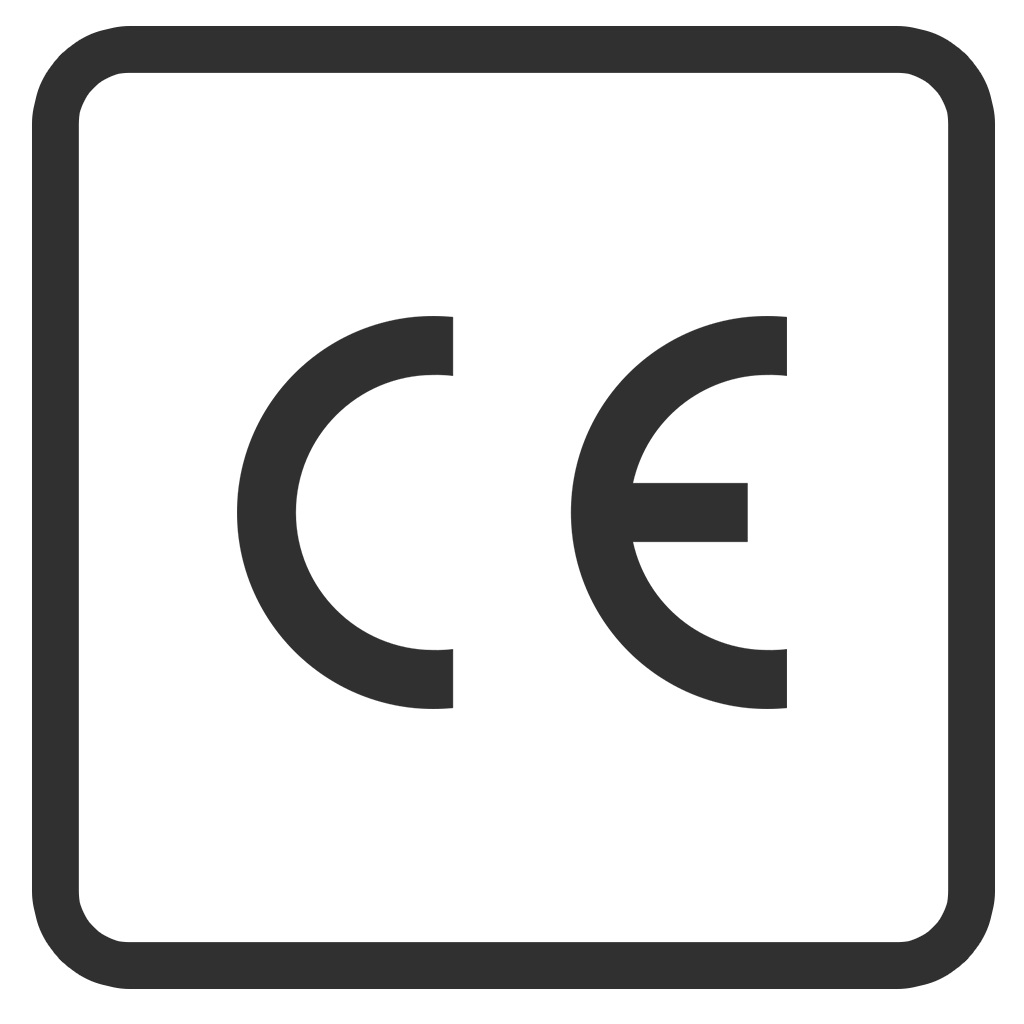
LWCP
Low Waste Continuous Production
The LWCP System concept was designed to allow the user to operate the production waste recycling machine on a continuous basis and to increase output without interruptions from a defined minimum throughput up to the maximum line throughput.
Lower costs for start-ups
Less material waste
Lower operating costs
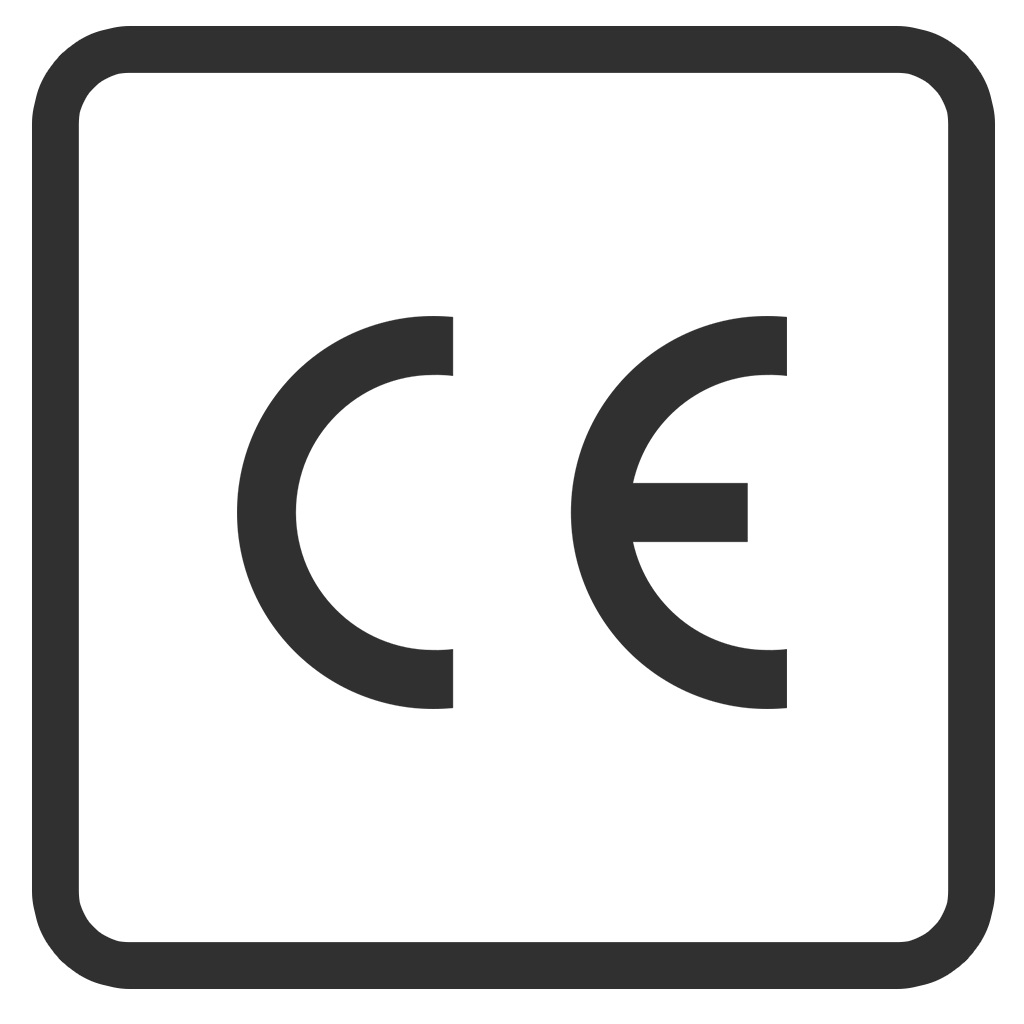