Palletizing systems for the production of polymers
Pelletization plays an important role in the production and processing of polymers. The right pelleting system for the application is crucial. That is why MAAG offers pelletizing systems and pelletizing solutions designed for a wide range of different processing methods, such as the production of blends, the production of premixes, the production of virgin polymers and the processing of recycled materials. Pellet solutions offer safe, efficient and profitable processing of standard plastics, biopolymers, hot melt adhesives and rubber bases. MAAG also offers methods for processing recycled plastics and systems for the production of plastic pellets. All MAAG pelleting systems from Gala, Reduction Engineering Scheer and Automatik provide maximum flexibility as required by today's polymer industry. The design concepts of MAAG pellet machines meet the requirements for polymers of various pellet sizes and pellet shapes. In addition to underwater pelleting and strand cutting systems, MAAG also offers a drip process for dust-free pellets.
SGS 600-L / SGS 800-L / SGS 1000-L
Strand pelletizing and dry cut pelletizing application – SGS 600-L / SGS 800-L / SGS 1000-L
The strand pelletizers of the SGS series are a development from Scheer for the production of pellets from thermoplastics. Their robust design, paired with outstanding workmanship, makes the SGS series a top-quality product in strand pelletizing and dry cut pelletizing technology. Some of the practical features which characterize these machines are a deposit-free interior, dual-shell design, forced cutting of all strands, bearings outside the cutting area, and a variable-speed drive. The serial production of optional components allows a variety of combination possibilities, which can be used to adapt the SGS to each individual application.
Short change-over time
Easy handling
High machine availability
Favourable alternative compared with a spare cutter
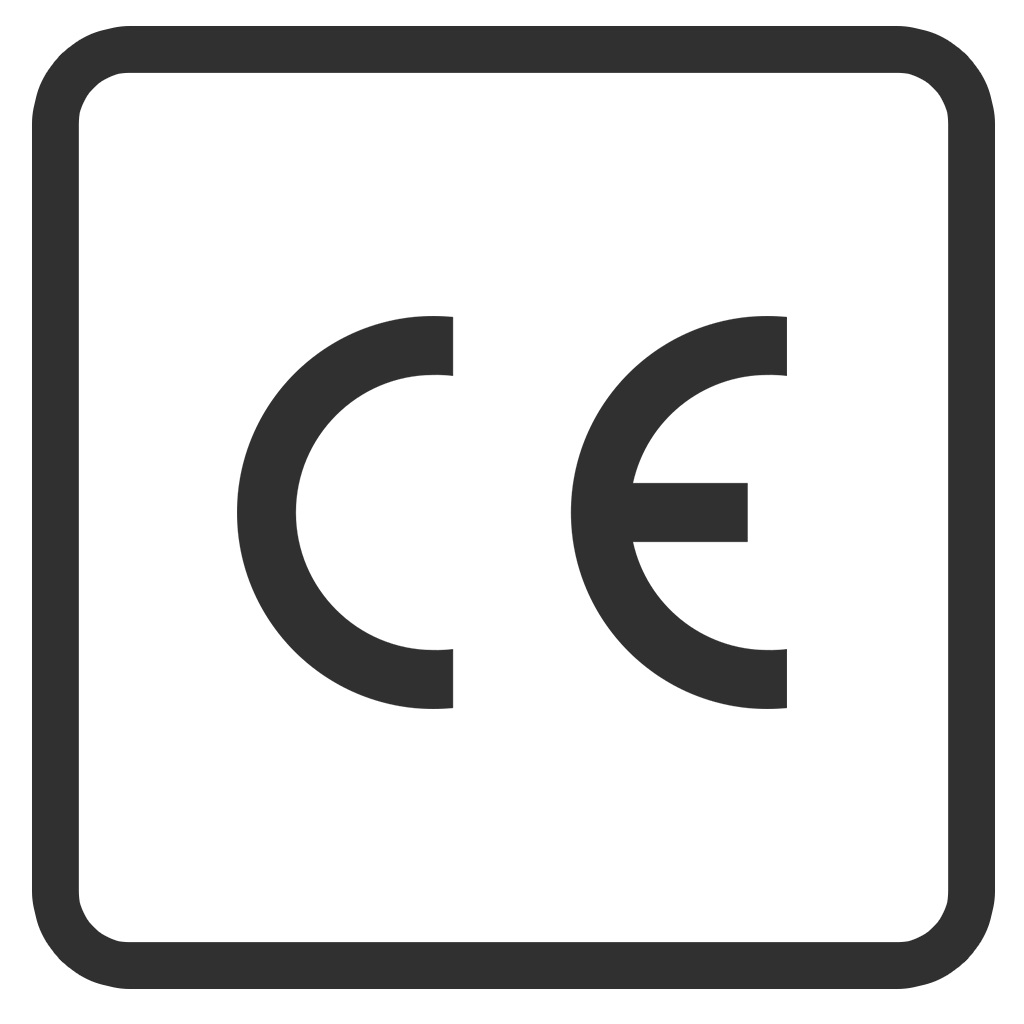
M-ASG
Dry cut pelletizing and strand pelletizing for further processing – M-ASG
The proven WSG dry-cut pelletizing and strand pelletizing systems with M-ASG pelletizers produce top-quality cylindrical pellets that are ideal for further processing.
Robust double-sided bearing
Changes in the length and weight of pellets
Dual Drive
It handles high temperatures
Integration into the JSG system
Very long service life
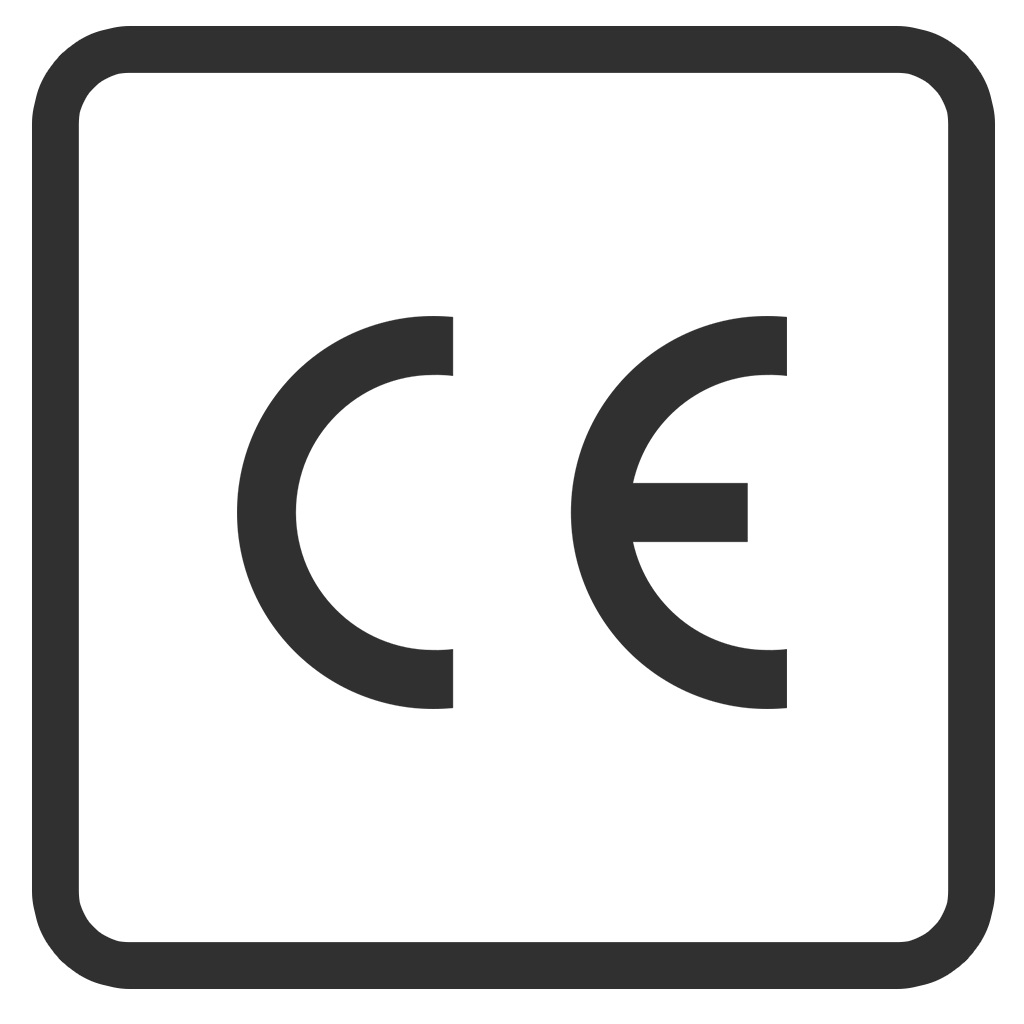
M-ASG for pultruded LFT pellets
Strand pelletizing and dry cut pelletizing processing - M-ASG for pultruded LFT pellets
The proven WSG dry-cut pelletizing and strand pelletizing systems with M-ASG pelletizers produce the highest quality of cylindrical pellets particularly suitable for further processing.
Compact solution
Robust design
Feed roller with its own motor
Changes in the length and weight of pellets
Long life
Wear resistance
Easy access for cleaning
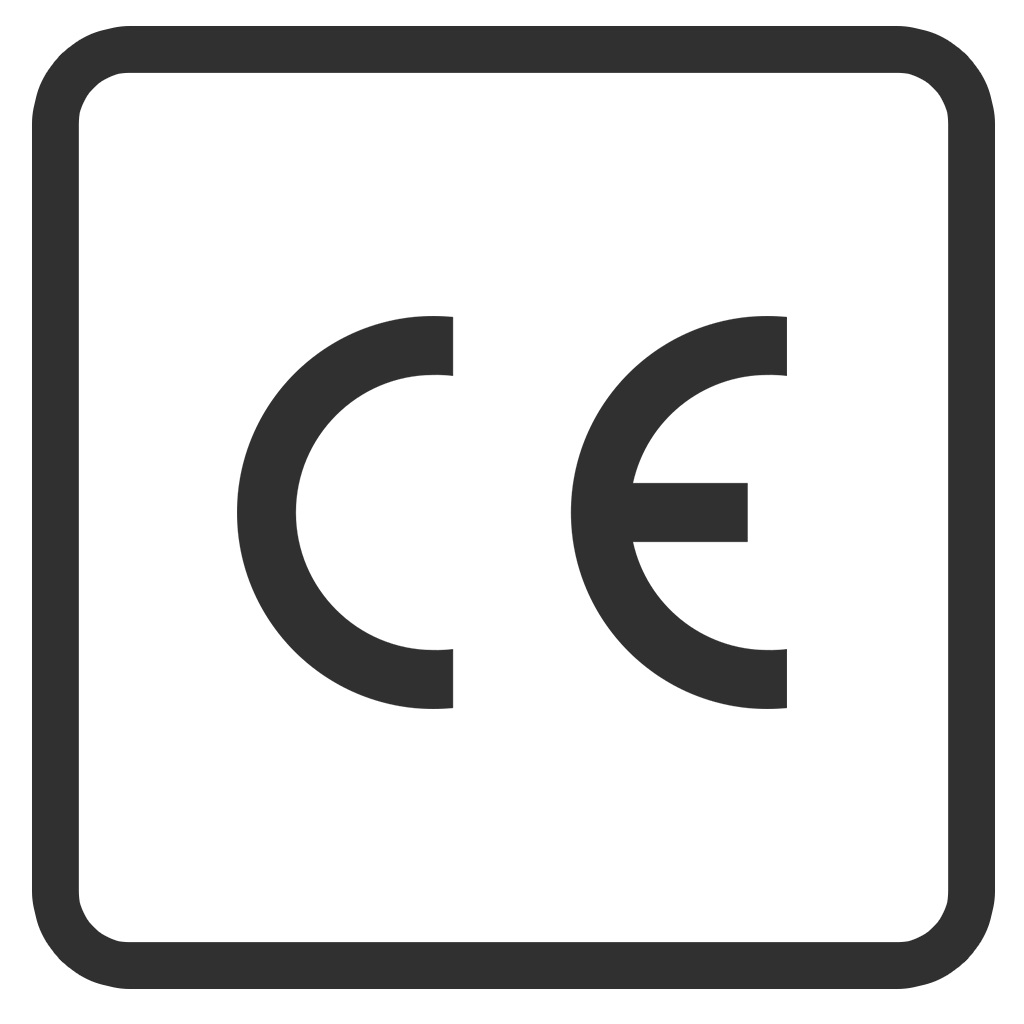
M-USG
Underwater pelletizing system for spring pelletizers - M-USG
The M-USG underwater pelletization system has been producing virgin polymers worldwide for decades. The extremely flexible system guarantees a high level of system availability, especially during continuous operation, and meets the highest quality requirements for cylindrical pellets.
Excellent, consistent quality pellets
Outputs up to 20,000 kg / h
Quick-change cutting head
High level of automation
Easy availability
Extremely durable cutting tools
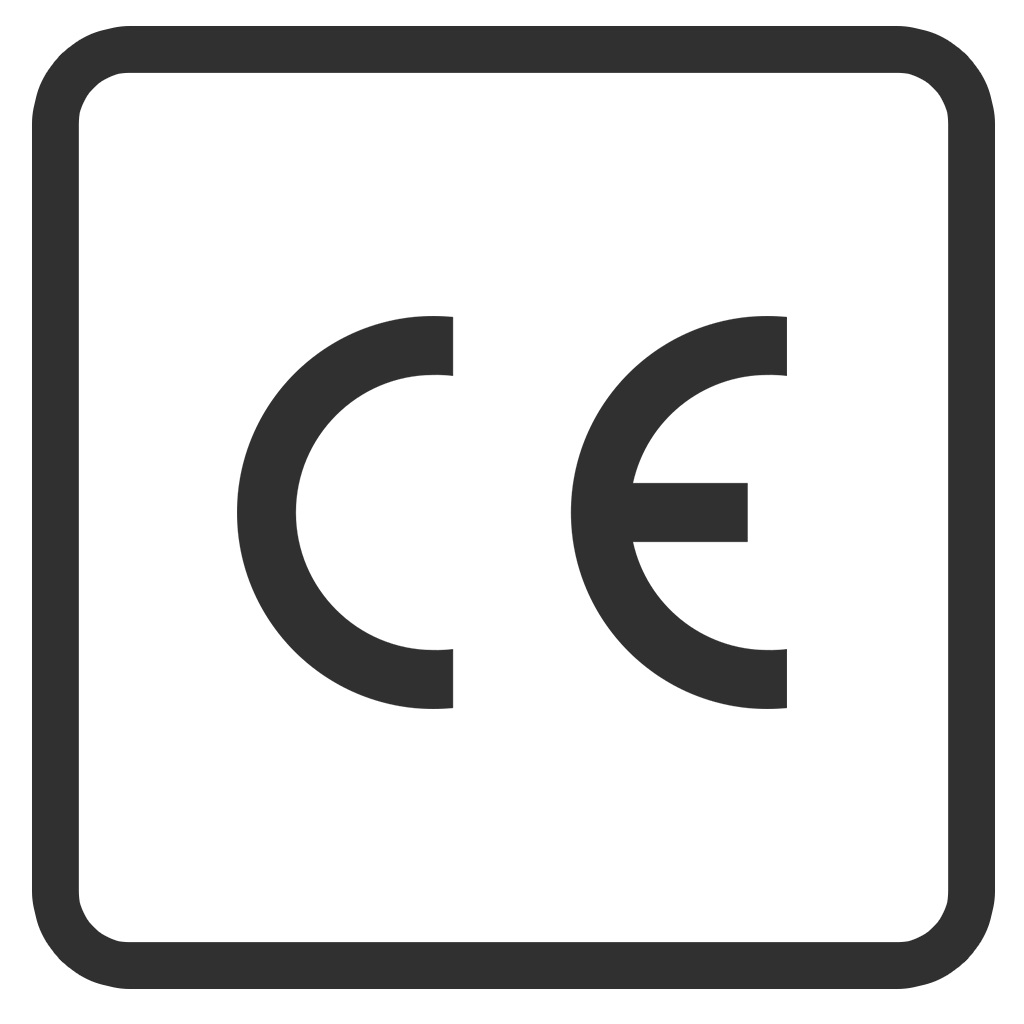
S3000 Pultrusion Series
Strand pelletizing and dry cut pelletizing for extrusion technology - S3000 Pultrusion Series
New extrusion technology of strand pelletizing and dry cut pelletizing is helping compounders of long fiber reinforced materials reach faster line speeds. Reduction Engineering Scheer was asked to specifically design a plastic pelletizer for better strand control and improve the pellets’ shape and cut quality. Traditionally, pultrusion pelletizers were fed strands by a belt puller only. The S3000 Series has been fitted with a front end feedroll mechanism. Coupled with the puller, the feedrolls ensure the strand control necessary for pellet accuracy and quality.
Unique Rotor Design for Maximum throughputs
Wide Feed Entrance
Insulated sound hood optional
Stainless Steel contact areas
Tool-less entry
Air Actuated Upper Feedroll
Dual drive optional
Designed per customer application
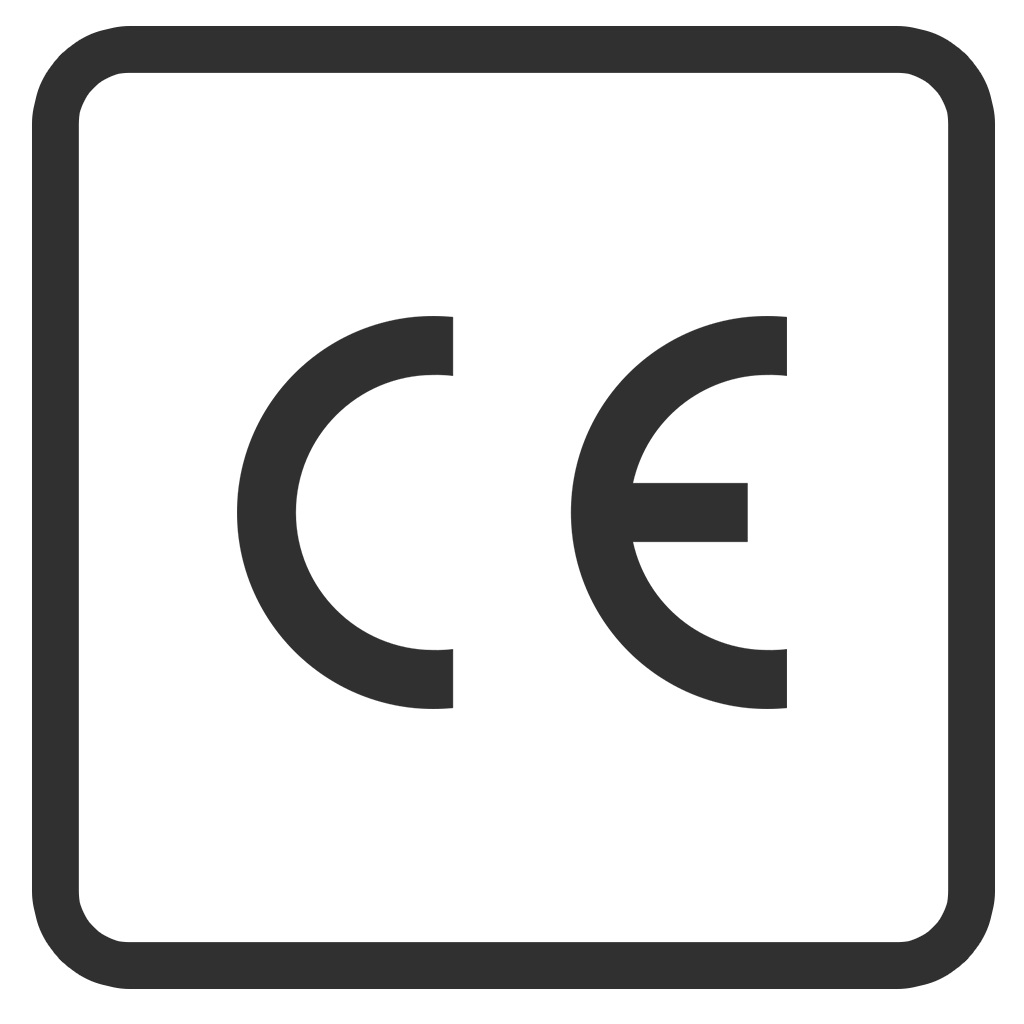
P-USG
Underwater strand pelletizing system for cost-effective production – P-USG
The P-USG underwater strand pelletizing systems made by MAAG Automatik have been particularly designed for both the production of virgin polymers with lower throughput rates and for recycling applications. The simple design of the strand pelletizing machine stands for engineeringg reduced to the essentials while featuring high process stability and pellet quality.
Consistent outstanding pellet quality
Automatic strand lacing on start-up and during production
Operating speeds up to 250 m/min
Excellent quality of the feed tools and cutting tools
Simple operation
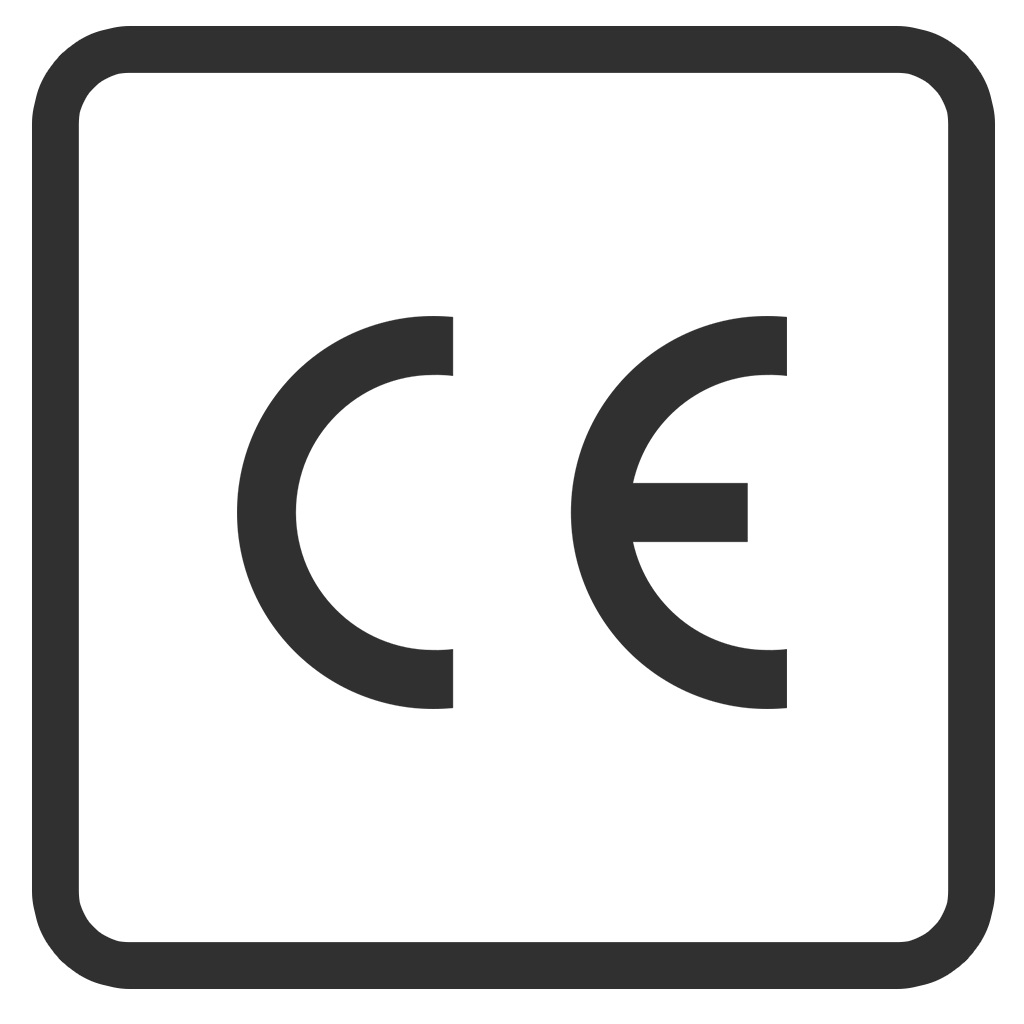
Strand Cooling Belt PFS
Unlike conventional extrusion in a water bath, the Strand Cooling Belt PFS does not require manual threading of strands. Strands are deposited directly on the conveyor belt and automatically conveyed to the strand pelletizer. The cooling is done by special air nozzles with high cooling capacity.
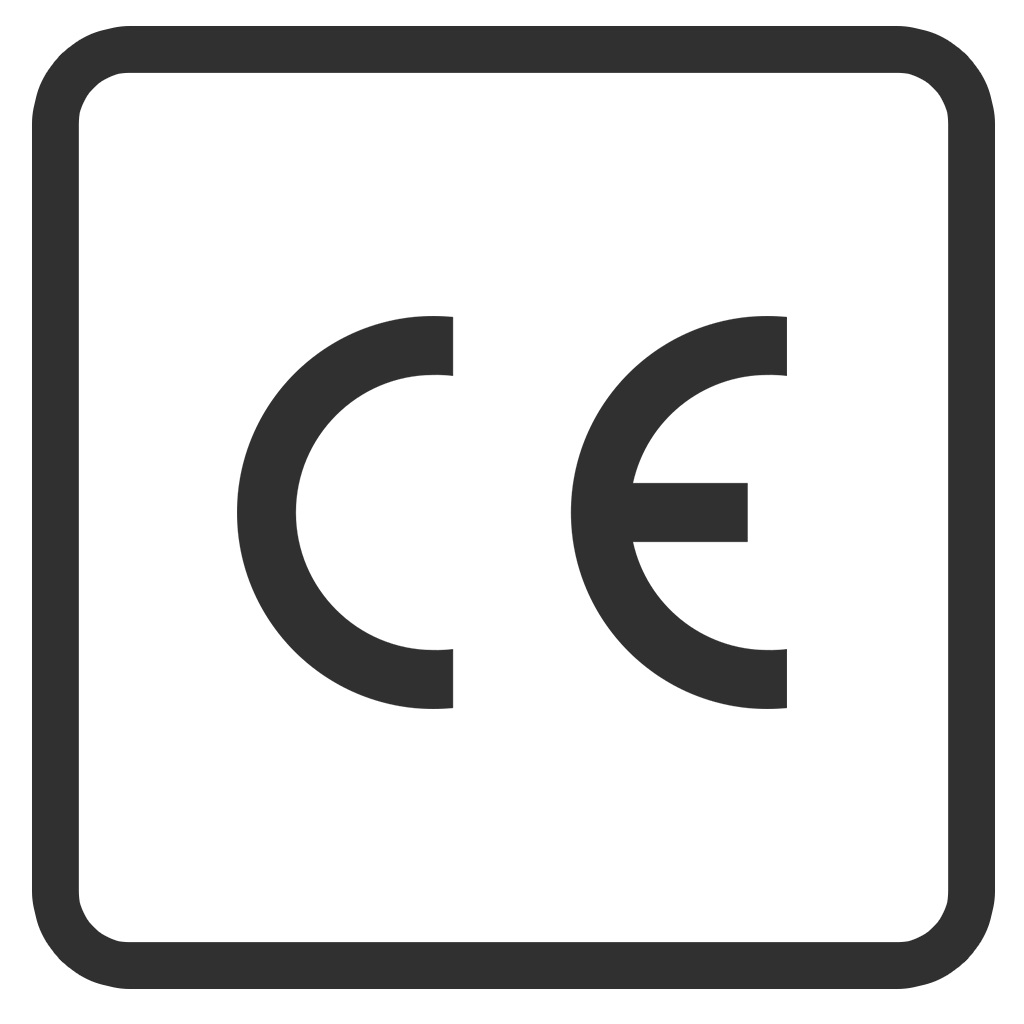
Belt-Cooling Pelletizing System PFS Series 30
The Belt-Cooling Pelletizing System PFS is specially designed for water soluble and brittle formulations. The variable system configuration enables perfect adaptation to the product being processed and guarantees continuous manufacturing. Even elastic and very flexible polymers can be handled by the belt system in a simple and efficient way. The system produces top-quality cylindrical pellets or micro-pellets which are ideal for further downstream processing.
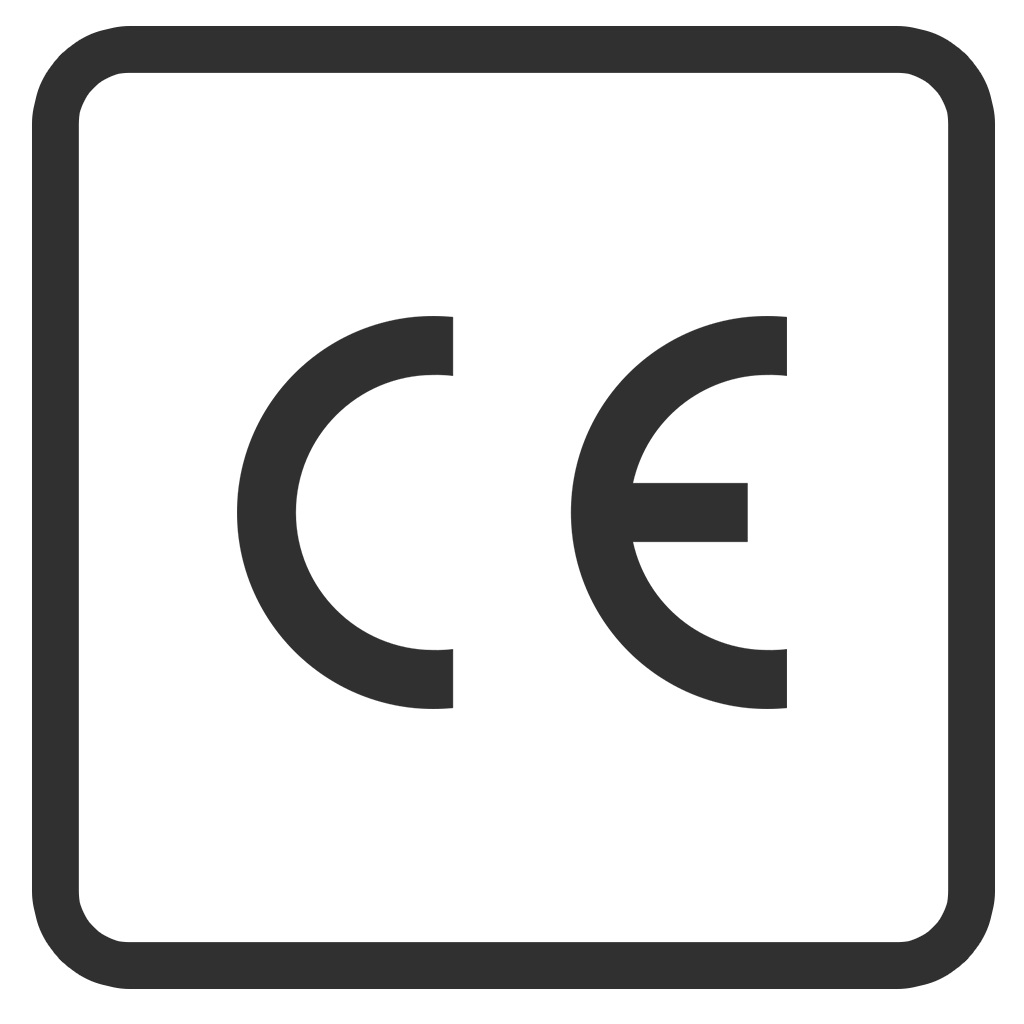
EBG Belt Conveyor Pelletizing System
Dry cut pelletizing and strand pelletizing system - EBG Belt Conveyor Pelletizing System
The belt conveyor pelletizing system EBG is specifically designed for the compounding of water-sensitive or highly filled (> 60 %) or fragile products in strand pelletizing and dry cut pelletizing. Variable system configuration permit a perfect adaptation to the product to be processed. Using the belt conveyor, even elastic and very flexible polymers may be handled easily and efficiently.
Wide processing window
Retro-fitting to existing pelletizing lines possible
Due to linear pelletizer feed, no strand breaks
Very slow drawing speed possible, starting at 8 m /min – Strand cooling by air, water, or both
Processing belt adaptable to different pelletizing heights
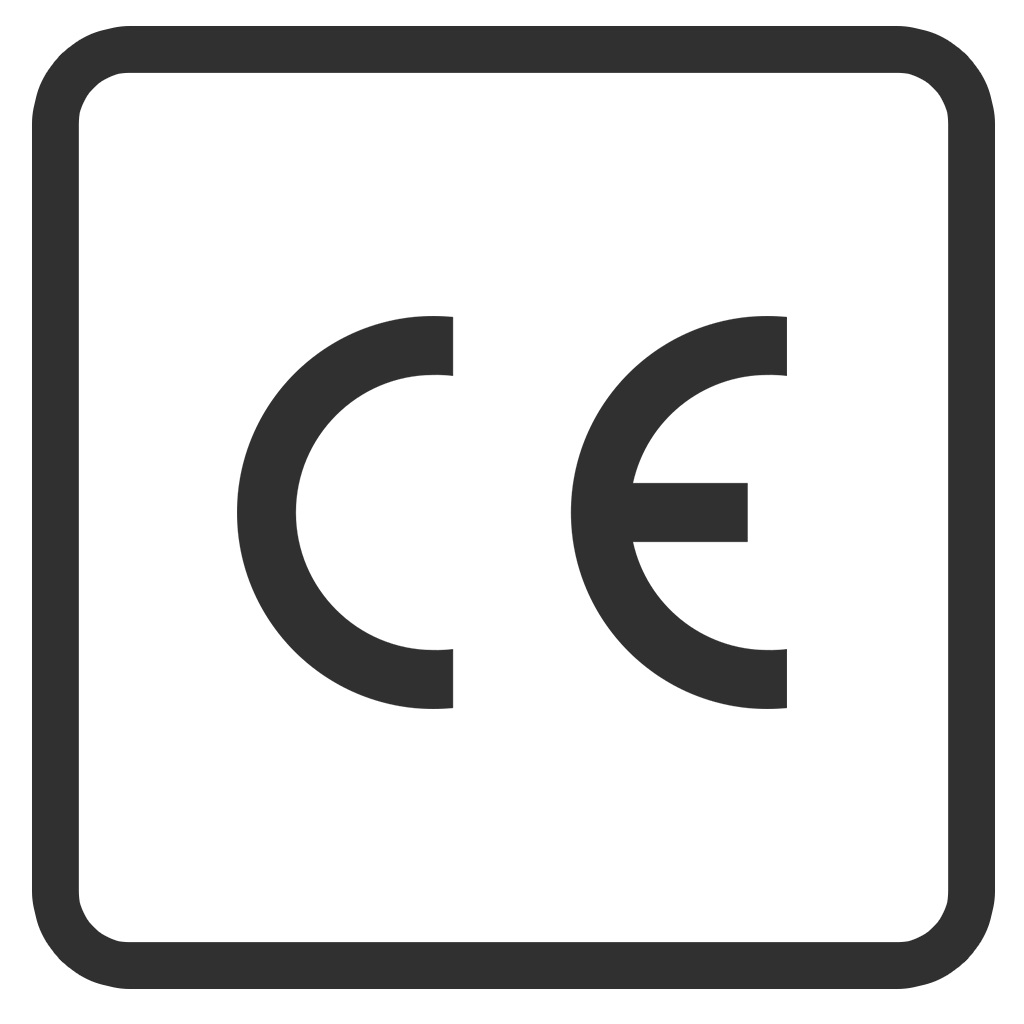
JSG
Automatic dry cut strand pelletizing system and dry cut belt conveyor pelletizing system – JSG
The proven JSG strand pelletizing systems are designed to achieve highest throughput rates in plastics compounding. The JSG systems produce cylindrical pellets of perfect quality for automatic dry cut strand pelletizing systems and dry cut belt conveyor pelleitizing systems, ideally suitable for further processing. Variable system configurations allow for optimal adaptation to the material to be processed.
Stability of the production process
Minimum residual humidity
Outputs up to 9,000 kg / h
Excellent quality of pellets
Perfectly customizable
Very long service life
Low demands on employees
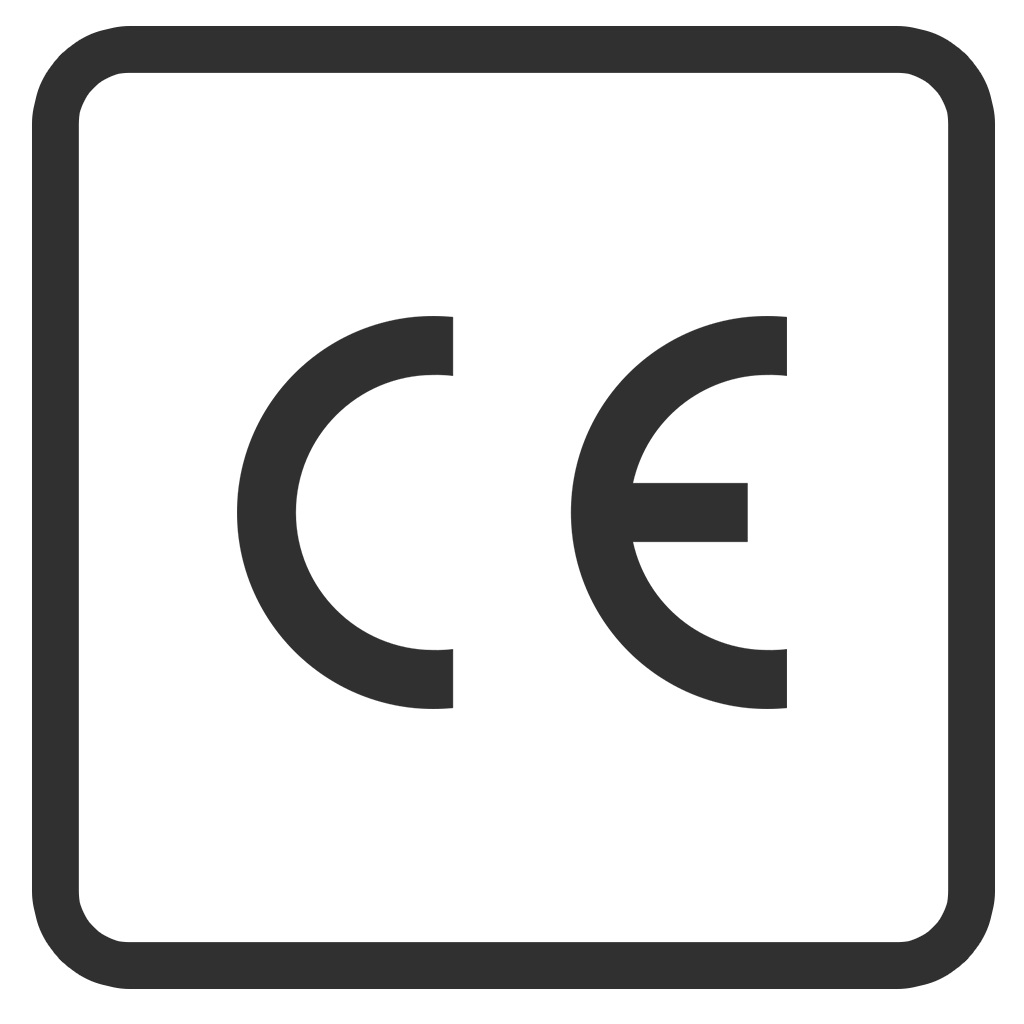
Wet Cut “WS” Series
Waterslide pelletizing system and wet cut strand pelletizing system
The “WS” Series Wet Cut Waterslide pelletizing system and Wet Cut Strand pelletizing system enables you to run a wide variety of materials with little or no operator assistance. Strand conditioning water is used to improve pellet quality by reducing fines.
Custom Built
Superior Service
In-house Engineering Support
Increased Production
Less Floor Space Required
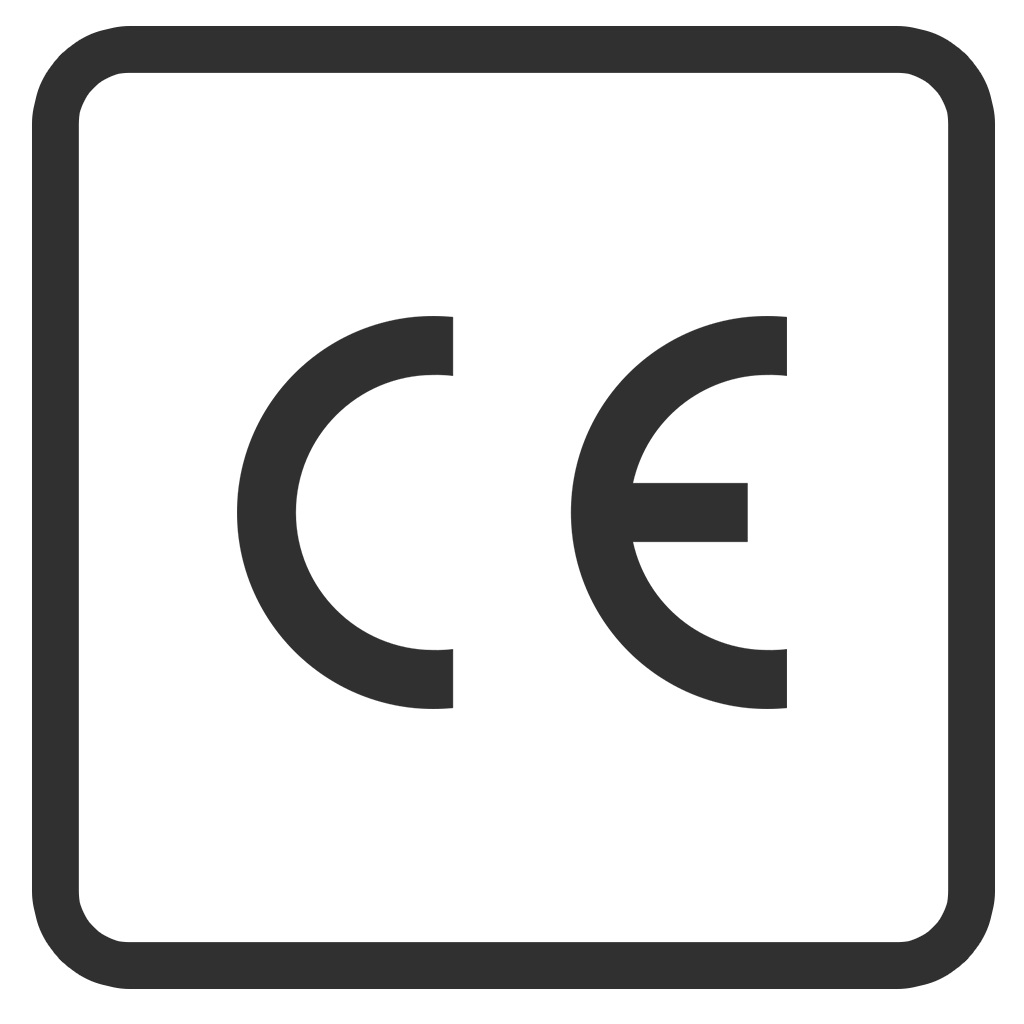
Flexline
The objective of the Flexline System for underwater pelletizing processes: The Flexline machine concept for underwater pellitizing systems is a logical extension of Gala technology. The machine concept permits complex product changes within a matter of minutes to minimize unproductive time for polymer and compound manufacturers.
Quick start
Minimal need for work
Flexibility in processing a wider range of recipes
Wear-resistant tools
Minimizes quality variations
Material savings
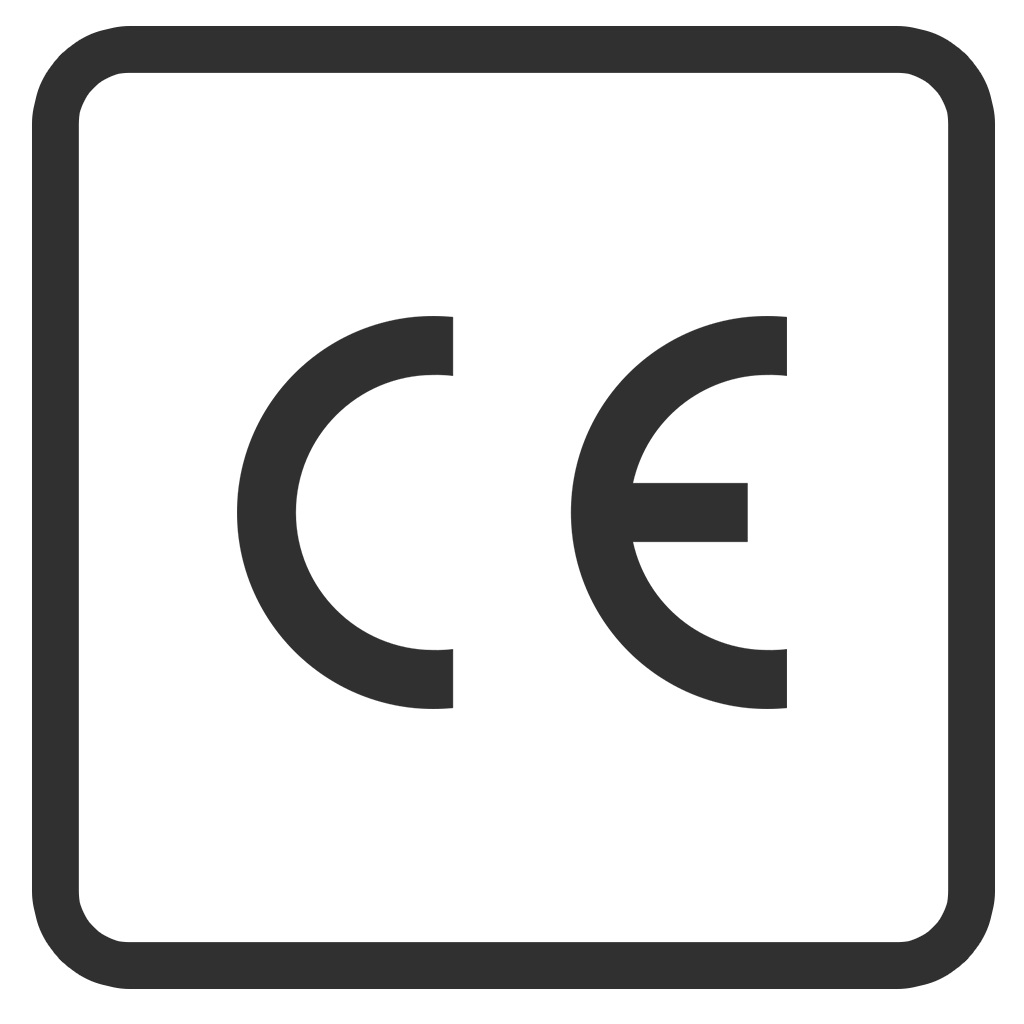