Filtration systems and screencangers for industrial applications
Filtration is a process that separates or purifies substances. The mechanical separation processes of Maag filtration systems are physical. The principles are used in filters and screen converters for separating and cleaning plastic melts, chemicals and lubricants. They are also used in recycling, extrusion, rotational molding, in general in industrial applications and in the pharmaceutical and food industries.
BRF - Basic model for continuous melt filtration in modern plastics recycling
Basic model for continuous melt filtration in modern plastics recycling
The BRF is the entry-level model for continuous filtration technology. Its effective melt flow combined with an optimized discharge system ensures high quality in processing all common polymers including LDPE, LLDPE, HDPE, PP, PS, ABS, etc. with low to high contamination levels. Thanks to their robust screens, the new continuous melt filters of the BRF series also make a major contribution to cutting operating costs in day-to-day production – especially when processing melts with mineral components.
Suitable for Compounding, Recycling,Extrusion
Robust screens for longer life
Also suitable for mineral contaminants
Controlled dirt discharge in a safe process environment
Flexible application options based on different screen fineness grades
Innovative control unit for user-friendly operation
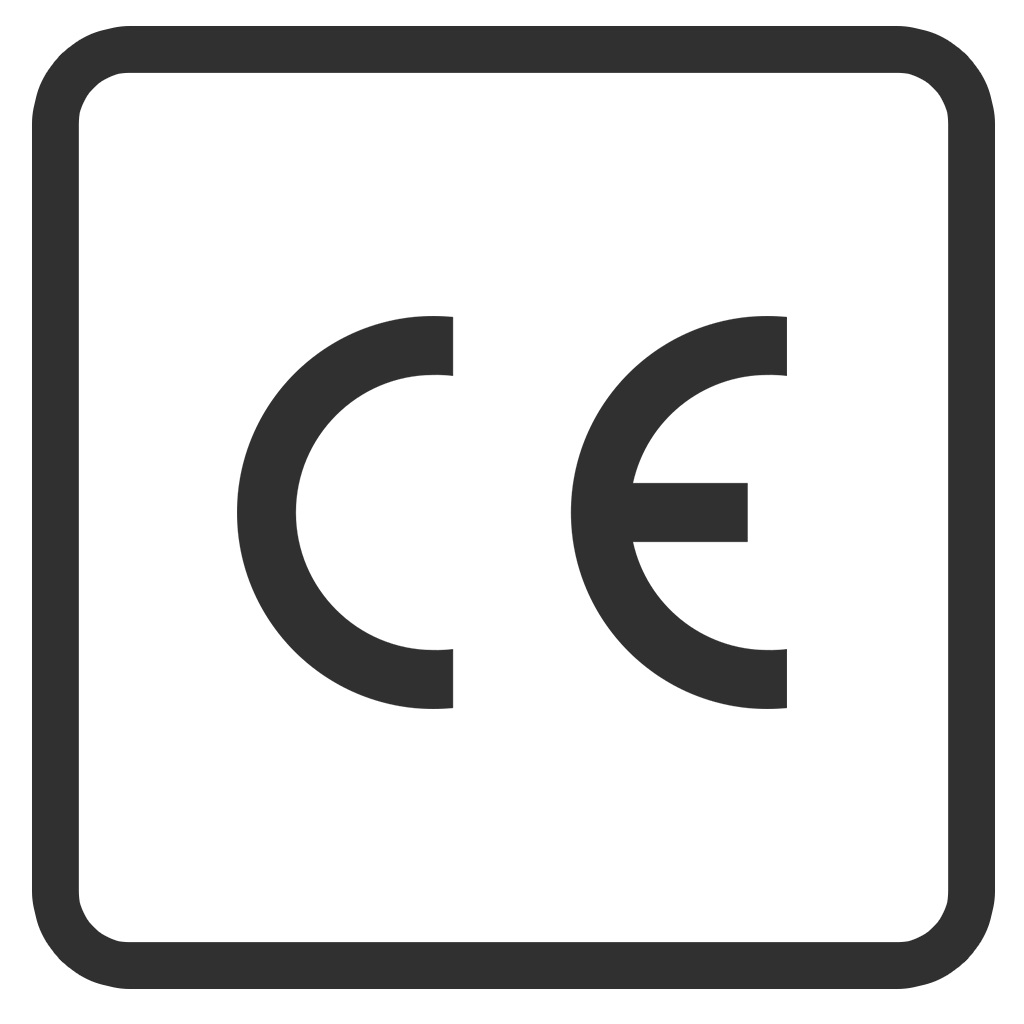
High performance Melt Filters – The ECO Series
The continuous melt filters in the ERF series are suitable for materials with up to 16% by weight contamination and are guaranteed to remain in use for long periods without changing the filter. Our ERF melt filters are capable of processing a wide range of polymers (e.g. LDPE, LLDPE, HDPE, PP, PS, ABS, PC / ABS, TPE, TPU, POM). All solid or elastomer foreign particles such as paper,wood, aluminum, copper, rubber, silicone, or high-melting polymer composites are efficiently removed.
The classic application for ERF melt filters is repelletizing lines, but they are also successfully employed for sheet and profile extrusion. ERF melt filters can in principle be used in any extrusion line – either single or twin-screw and irrespective of the type of pelletizing system or other downstream unit. Three different sizes enable throughputs from 150 to 10,000 kg/h depending on the application.
Suitable for Compounding, Recycling, Extrusion
Fully automatic, continuous operation
Up to 18% contaminants removed
Extremely low melt losses
More reliable processing due to constant pressure at the filter outlet
No need to replace the screen for several weeks, or possibly months, depending on the material and the application
Completely closed system with no entrapped air
Short contaminant residence times in the filter
Very simple replacement of the scraper from outside using a hydraulic cylinder
Elastomers (rubber, silicone) are efficiently filtered and discharged before they have a chance to be forced through the filter screen
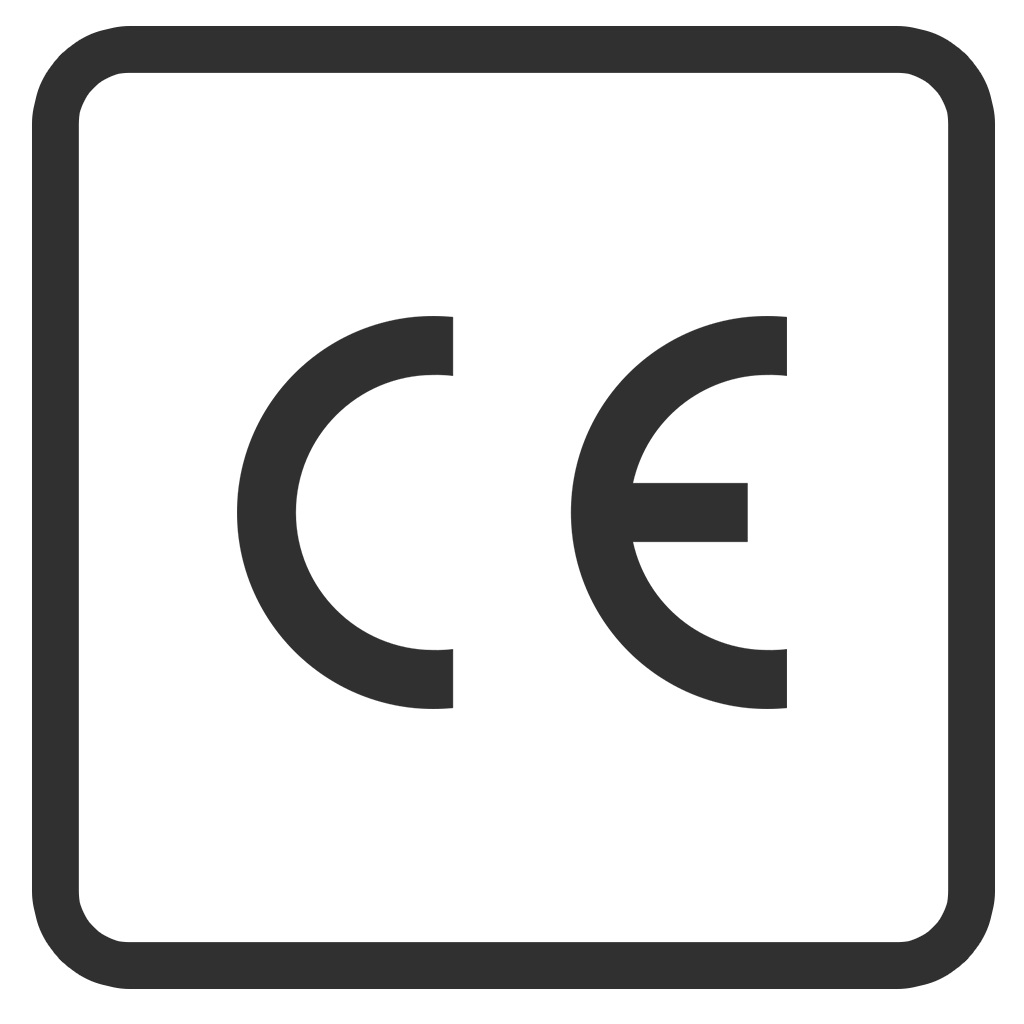
High performance Melt Filters - The ERF Series
The continuous melt filters in the ERF series are suitable for materials with up to 16% by weight contamination and are guaranteed to remain in use for long periods without changing the filter. Our ERF melt filters are capable of processing a wide range of polymers (e.g. LDPE, LLDPE, HDPE, PP, PS, ABS, PC / ABS, TPE, TPU, POM). All solid or elastomer foreign particles such as paper,wood, aluminum, copper, rubber, silicone, or high-melting polymer composites are efficiently removed.
The classic application for ERF melt filters is repelletizing lines, but they are also successfully employed for sheet and profile extrusion. ERF melt filters can in principle be used in any extrusion line – either single or twin-screw and irrespective of the type of pelletizing system or other downstream unit. Three different sizes enable throughputs from 150 to 10,000 kg/h depending on the application.
Suitable for Compounding, Recycling, Extrusion
Fully automatic, continuous operation
Up to 18% contaminants removed
Extremely low melt losses
More reliable processing due to constant pressure at the filter outlet
No need to replace the screen for several weeks, or possibly months, depending on the material and the application
Completely closed system with no entrapped air
Short contaminant residence times in the filter
Very simple replacement of the scraper from outside using a hydraulic cylinder
Elastomers (rubber, silicone) are efficiently filtered and discharged before they have a chance to be forced through the filter screen
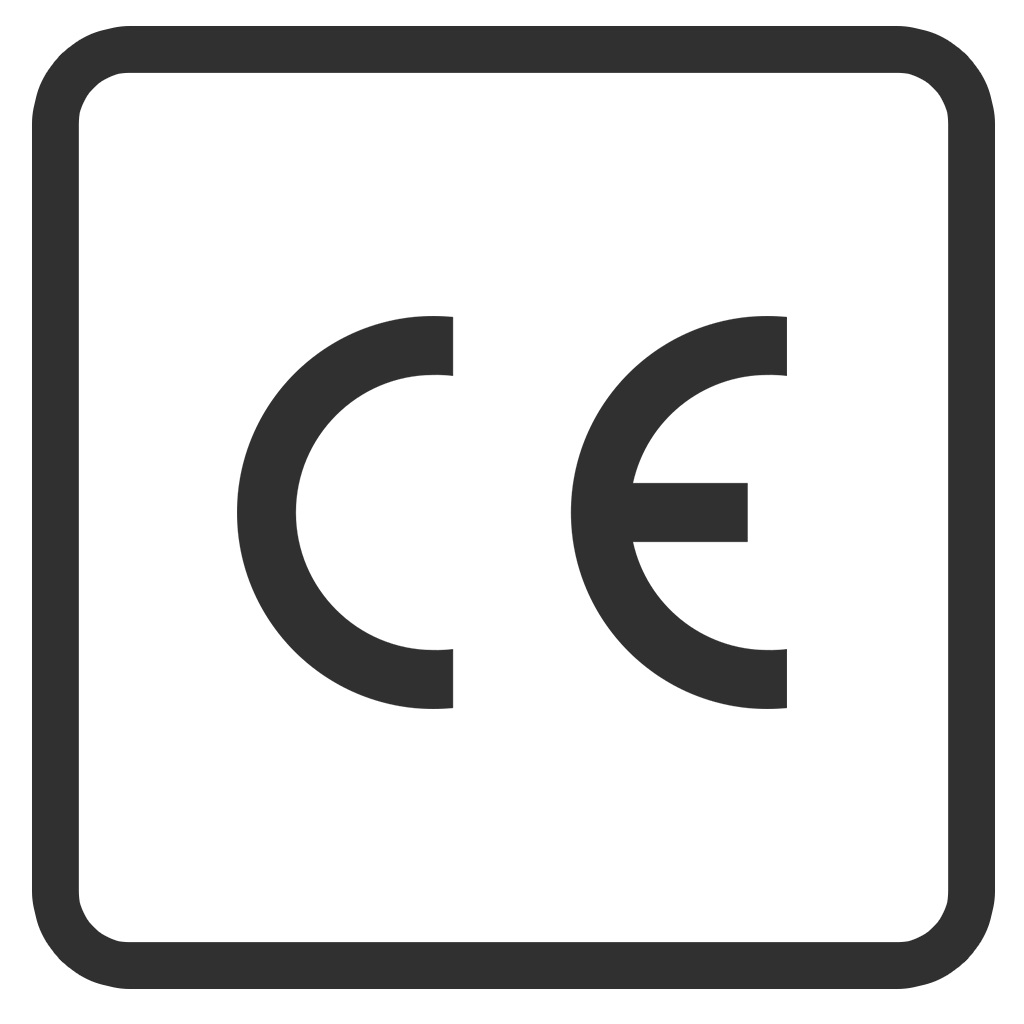
CSC-R - Screen changer with curved filter screens
MAAG’s CSC-R large scale screen changer with curved screens is designed for the use of one-way filter screens which do not require cleaning after the simple and safe screen change. The screen bearing pistons belong to MAAG’s modular filter system and its patented design use 75% of the piston surface as active filtration area. Also this filter execution can be installed for vertical or horizontal melt flow directly at the reactor discharge melt pump or pelletizer booster melt pump to avoid additional piping for reduction of melt residence time.
Suitable for Resin & Virgin Polymer Production
Up to 4x more filter area than circular screen cavities
Higher throughput
Multiplied screen life time
Smaller hydraulic unit
Lower melt pressure
Higher filtration fineness
Reduced flux rate kg/h/cm2
Ultra-compact design
Less heating capacity
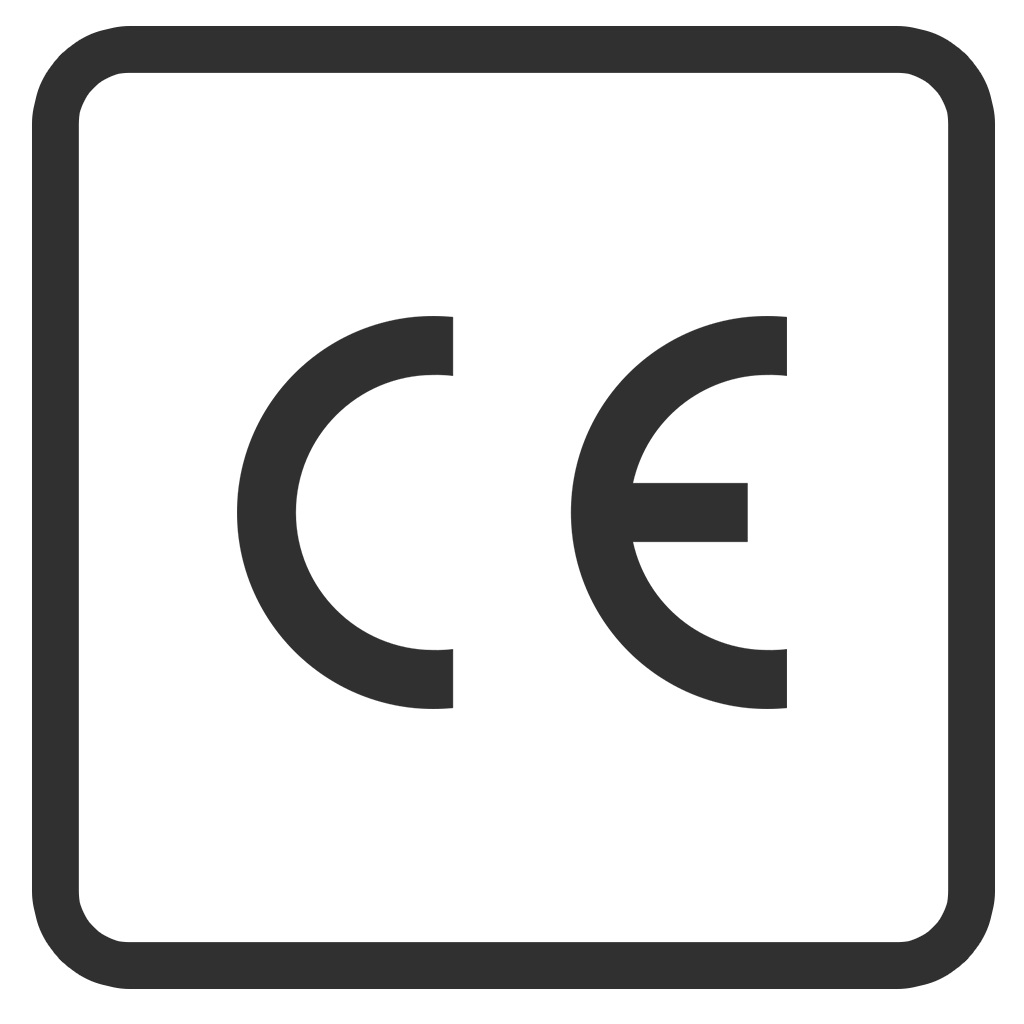
CSC-C - Polymer filtration for polymer production, polymer processing and extrusion
MAAG’s CSC-C large scale screen changer with candle filter elements is the right choice if short melt residence time, small footprint and a simplified candle change are required. Depending on the polymer type, melt viscosity, reactor throughput, and filter fineness, the screen changer size and number of pistons are customized to the application. The patented design allows the use of pleated micronex® candle filter elements with fiber metal felt (FMF) media, or cylindrical Multinex candles filter elements with interchangeable filter sleeves.
Suitable for Resin & Virgin Polymer Production
Filter elements
Vertical / horizontal installation
2/4 pistons
Patented design
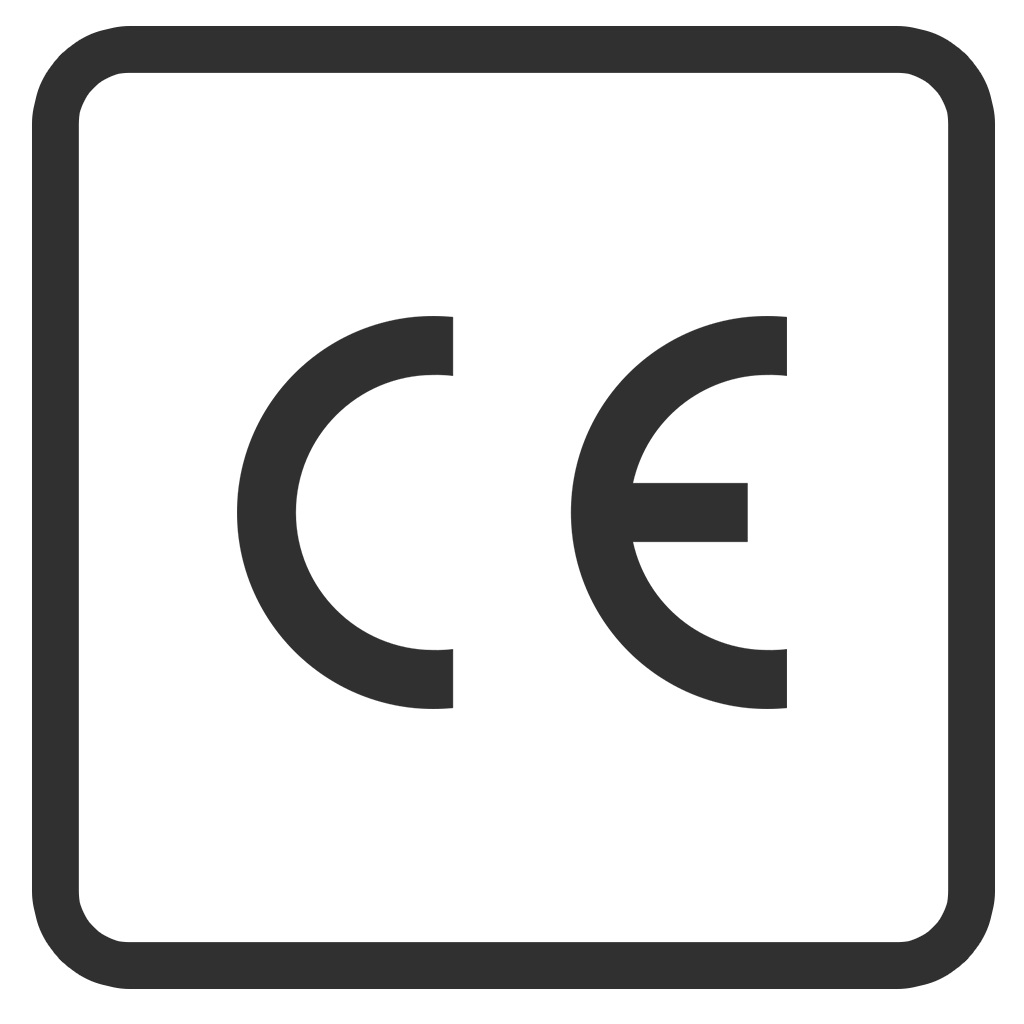
CSC - Continuous screen changers and double pistion screenchangers for filtration systems
Continuous CSC screen changers from MAAG with their robust and leak-free operation meet highest quality standards with respect to melt filtration. Due to their constantly improved functionality continuous screen changers from MAAG increase product quality significantly. CSC screen changers are based on the proven double-piston design that operates without any additional seals. Their sturdy construction available in all sizes and designs guarantees a reliable and leak-free filtration of polymer melt for many years.
Suitable for¨Rotomolding, Hot Melt Adhesives, Resin & Virgin Polymer Production, Masterbatch, Compounding, Recycling, ExtrusionSimple operation and uncomplicated screen changing
High operational reliability
Short material residence time
Leak-free mode of operation
Low pressure consumption
Flow channel geometry without any dead spots
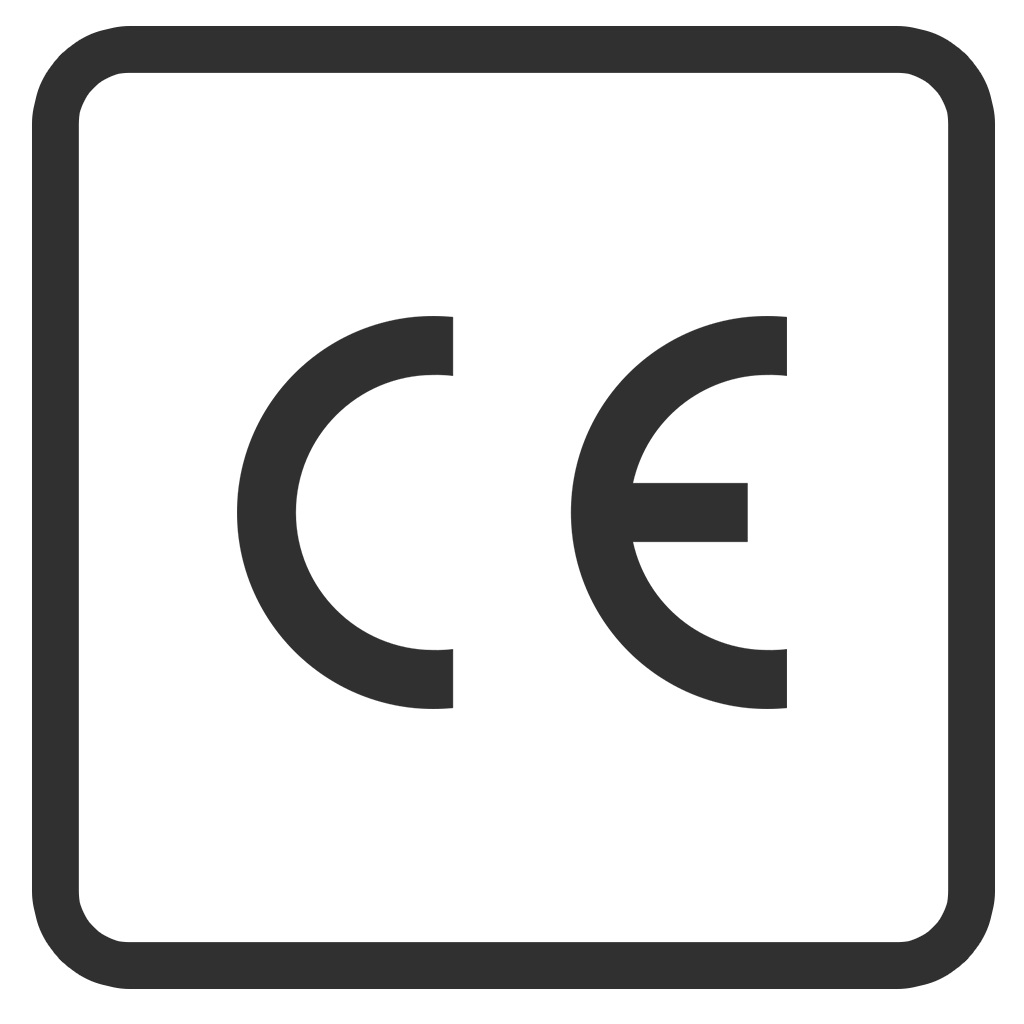
DSC - Single piston screen changer for extrusion and compounding applications
Discontinuous DSC screen changers from MAAG with their robust and leak-free operation meet highest quality standards with respect to melt filtration. Due to their constantly improved functionality continuous screen changers from Maag increase product quality significantly. DSC screen changers are based on the proven single-piston design that operates without any additional seals. Their sturdy construction available in all sizes and designs guarantees a reliable and leak-free filtration of polymer melts for many years.
Suitable for Masterbatch, Compounding, Recycling, Extrusion, Hot Melt Adhesives
Simple operation and uncomplicated screen changing
High operational reliability
Short material residence time
Leak-free mode of operation
Low pressure consumption
Flow channel geometry without any dead spots
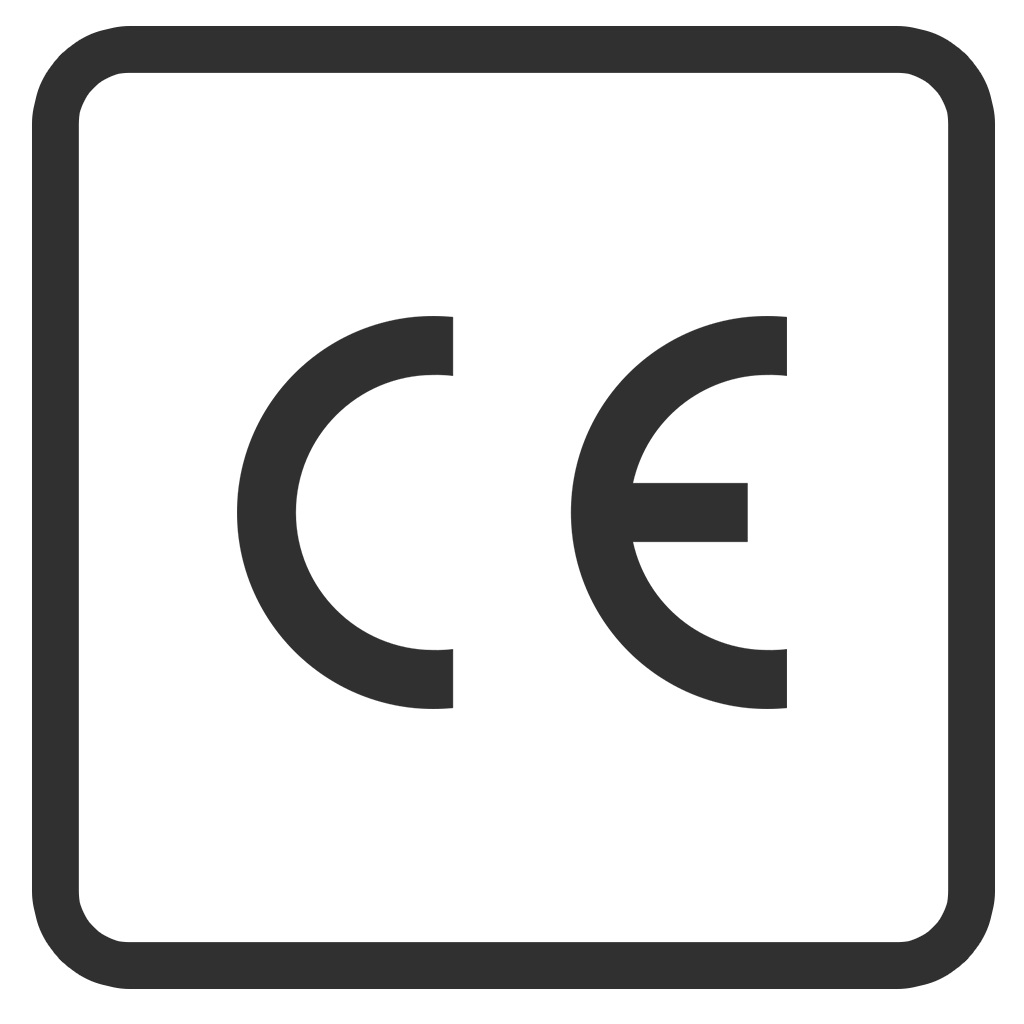
DFS - Continuous large area polymer filtration systems
MAAG’s new generation Duplex Filter System (DFS). The new DFS incorporates a new patented solid body DIVEXpro switch over valve. The vent and drain valves are also newly designed and integrated into the body of the DIVEXpro. Combined with MAAG’s established MICRONEX® filter candles the new generation filter system can meet the harsh demands of polymer filtration. For chemical recycling applications with low viscosity and high contamination levels the new generation DFS-BF is capable of performing an automated backflush cleaning of the filter candles during operation.
Suitable for Resin & Virgin Polymer Production
Reliable sealing
Improved venting
Better draining
Simplified vessel changeout
Improved accessibility
Safer operation
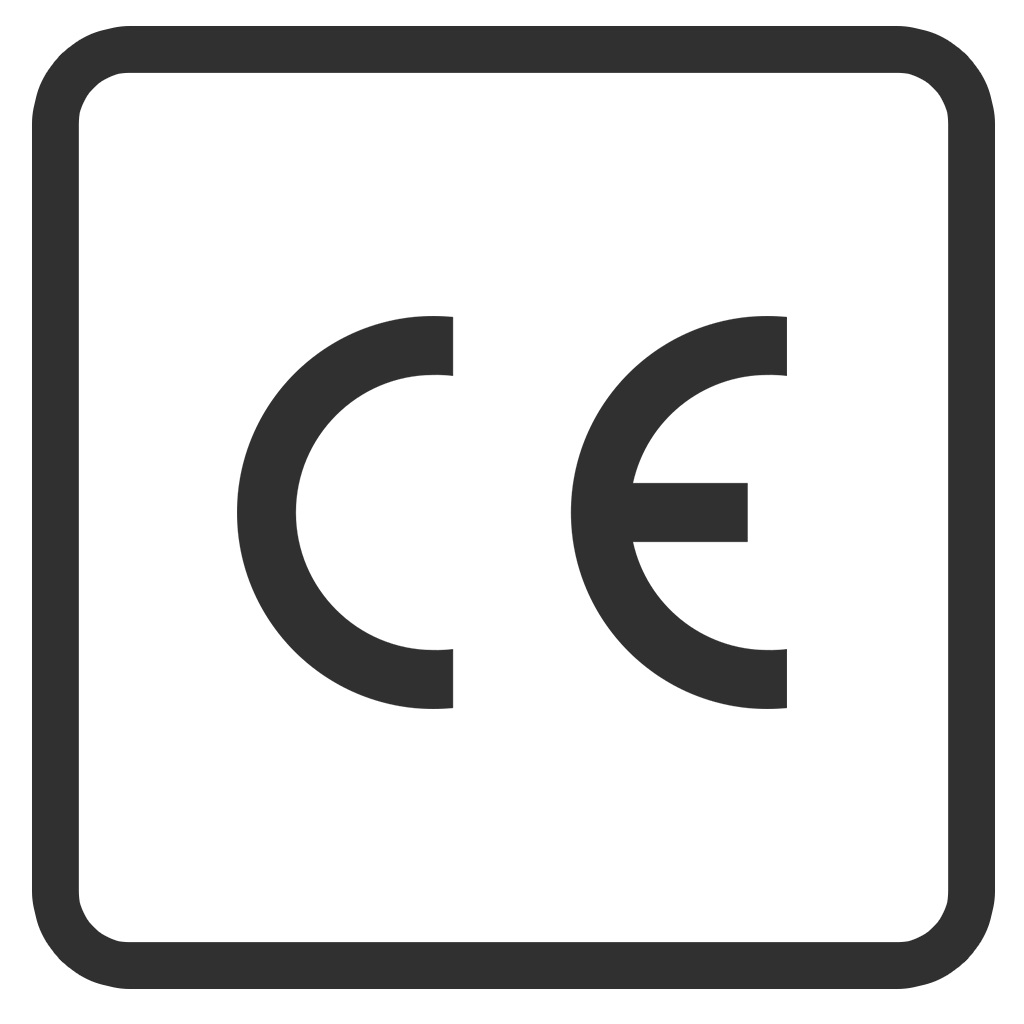
Simplex - Discountinuous large area polymer filtration applications for industry and extrusion
MAAG-designed simplex polymer filter systems can be provided with either fixed or removable vessels. A compact preheat station with spare vessel is also available for locating near the polymer processing line for quick changeout. They are custom designed to minimize initial pressure drop and maximize polymer filter element life. Our proprietary sizing program, based on more than 20 years of experience in the field of polymer production and extrusion, incorporates your operating data to size each system for maximum performance and optimized flow while maintaining compact dimensions.
Suitable for Resin & Virgin Polymer Production, Extrusion
Lower cost
Easier operation
Less space requirements
Minimized pressure drop
Horizontal or vertical design
No diverter valves
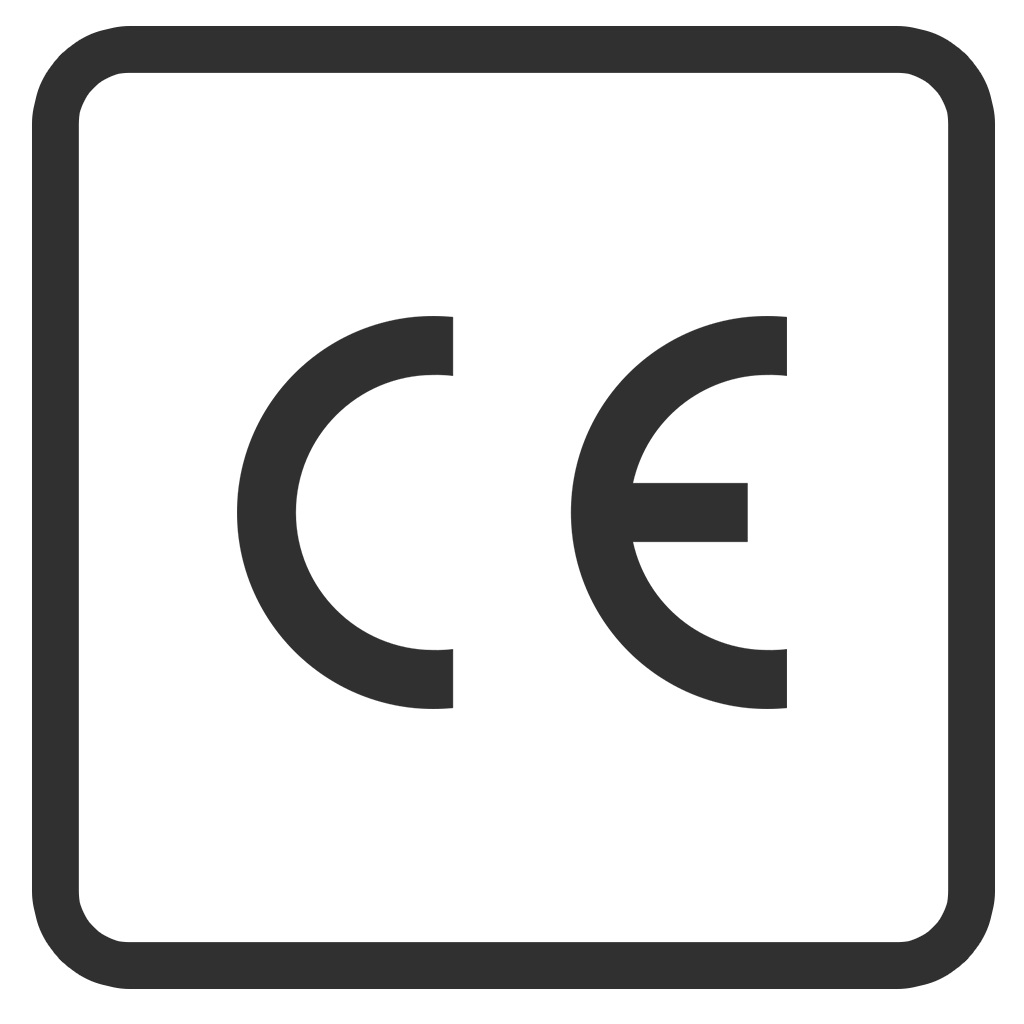
HSC - Manual screen changer and plate screen changer for filtration solutions and extrusion processes
Manual screen changers from Maag have been the first choice of cost-effective filtration systems in extrusion lines for many years. Starting at size 45, the manual screen changers optionally come with transmission gearing. Here, the breaker plate is equipped with patented gearing and a pinion which allows an effortless screen change even in restricted space conditions or high sealing pressures. The manual screen changer guarantees the protection of gear pumps and fine extrusion die gaps from damage and dirt accumulation.
Suitable for Recycling, Extrusion
Simple operation with quick screen change
High operational reliability
Short material residence time
Leak-free mode of operation
Low pressure consumption
Flow channel geometry without any dead spots
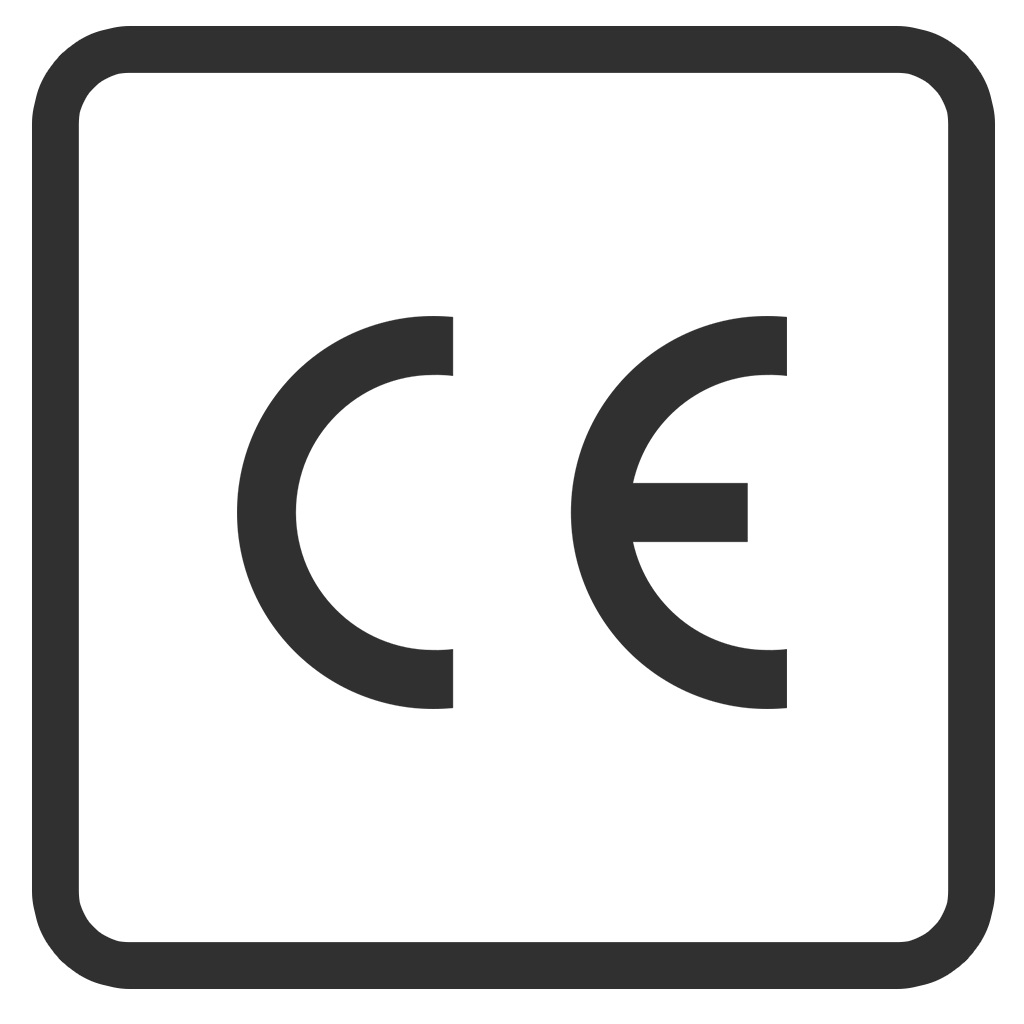
FSC - Hydraulic plate screen changer for filtration systems and polymer production
FSC screen changers from Maag are equipped with a pressure-adaptive sealing system as a standard. Thanks to this sealing system, the required sealing forces are adjusted to the actual melt pressure automatically. The narrow design is especially suited for being used in applications with thermally sensitive materials. Their solid and robust construction, available in all sizes and designs, ensures a reliable and leakfree filtration of molten polymers for many years. The hydraulically operated screen changer reliably guarantees the protection of melt pumps and mold gaps from damage and dirt.
Suitable for Compounding, Recycling, Extrusion, Masterbatch
Simple operation and uncomplicated screen changing
High operational reliability
Short material residence time
Leak-free mode of operation
Low pressure consumption
Flow channel geometry without any dead spots
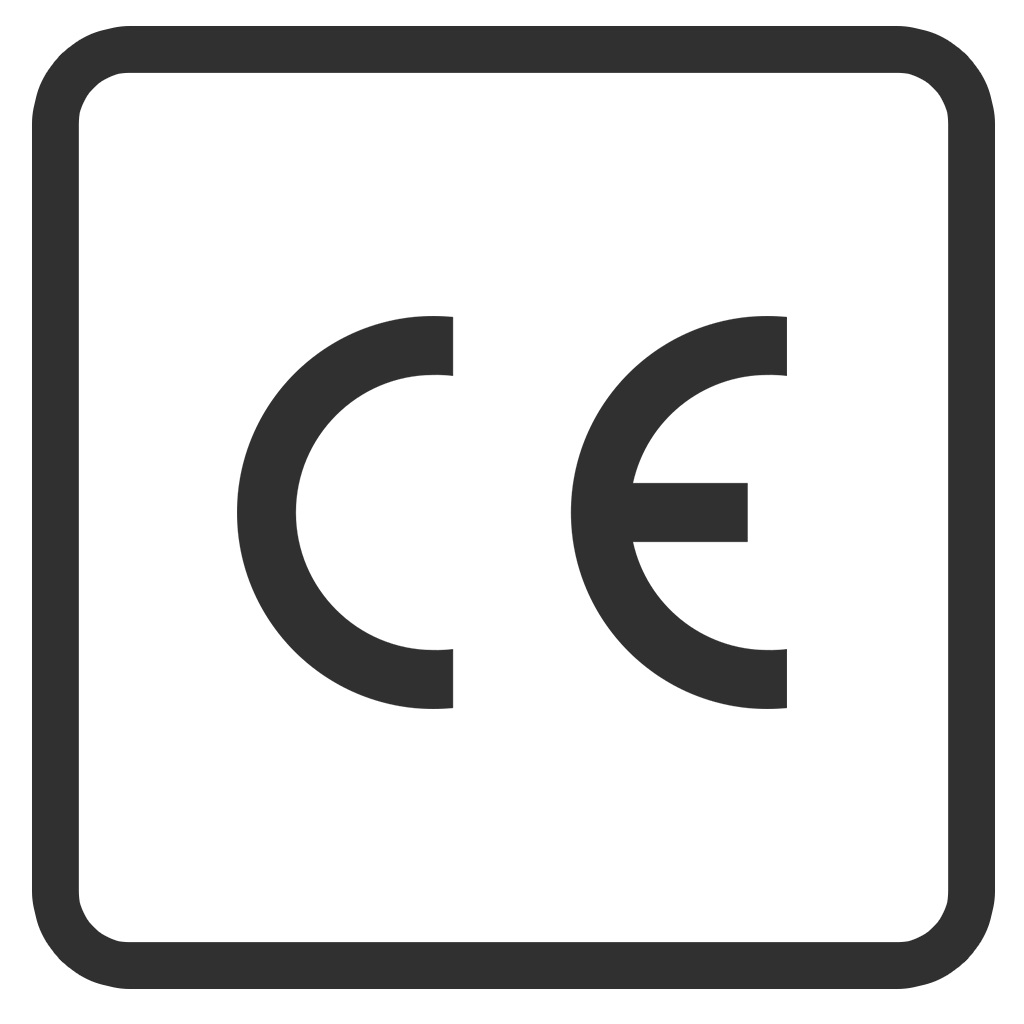
SSC
Effective single piston screen changer for reliable melt cost effective filtration solution
The compact single-piston screen changers SSC from MAAG provide a cost-effective filtration alternative for extrusion applications which allow for interruptions in the melt stream during screen changeovers. SSC operate without any additional seal.
Simple operation and uncomplicated screen changing
High operational reliability
Short material residence time
Leak-free mode of operation
Low pressure consumption
Flow channel geometry without any dead spots
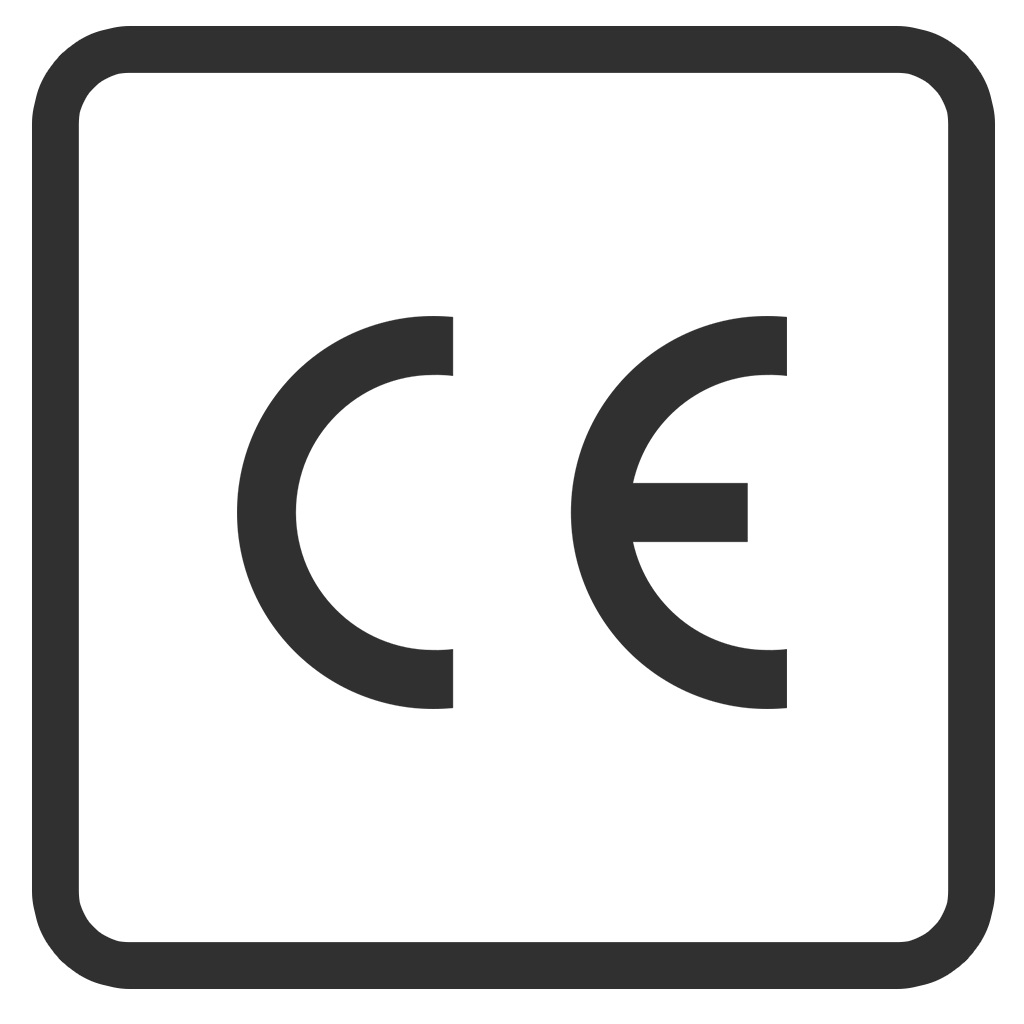