MAAG Company
The MAAG Group comprises successful and renowned companies, each with their own impressive history. Automatik Plastics Machinery, Ettlinger Kunststoffmaschinen, Maag Pump Systems, Gala Industries, Reduction Engineering Scheer and Xantec Steuerungs- und EDV Technik are today the strong and innovative product brands of the MAAG Group.
The history of the MAAG Group thus begins in the late 19th century, with the establishment of Scheer as a metal foundry and machine factory in Stuttgart, Germany, in 1890. Maag Pump Systems was founded in 1913. Automatik Plastics Machinery was founded in 1947. Gala Industries was founded in 1959, and Ettlinger Kunststoffmaschinen in 1983. The youngest member of MAAG Group – Xantec Steuerungs- und EDV-Technik was founded in 1994. Over the decades, they have all grown into experts in the various fields of polymer production and processing.
All the members of the MAAG Group contribute their supreme expertise and years of experience in developing and manufacturing superb machines, plants, systems, and software – and will continue doing so in the future. The bundling of core competencies, industry best practices, the attentive maintenance of existing business relationships and creation of new ones, all provide the foundations for maximum customer satisfaction throughout the Group.
Wet Cut “WS” Series
Waterslide pelletizing system and wet cut strand pelletizing system
The “WS” Series Wet Cut Waterslide pelletizing system and Wet Cut Strand pelletizing system enables you to run a wide variety of materials with little or no operator assistance. Strand conditioning water is used to improve pellet quality by reducing fines.
Custom Built
Superior Service
In-house Engineering Support
Increased Production
Less Floor Space Required
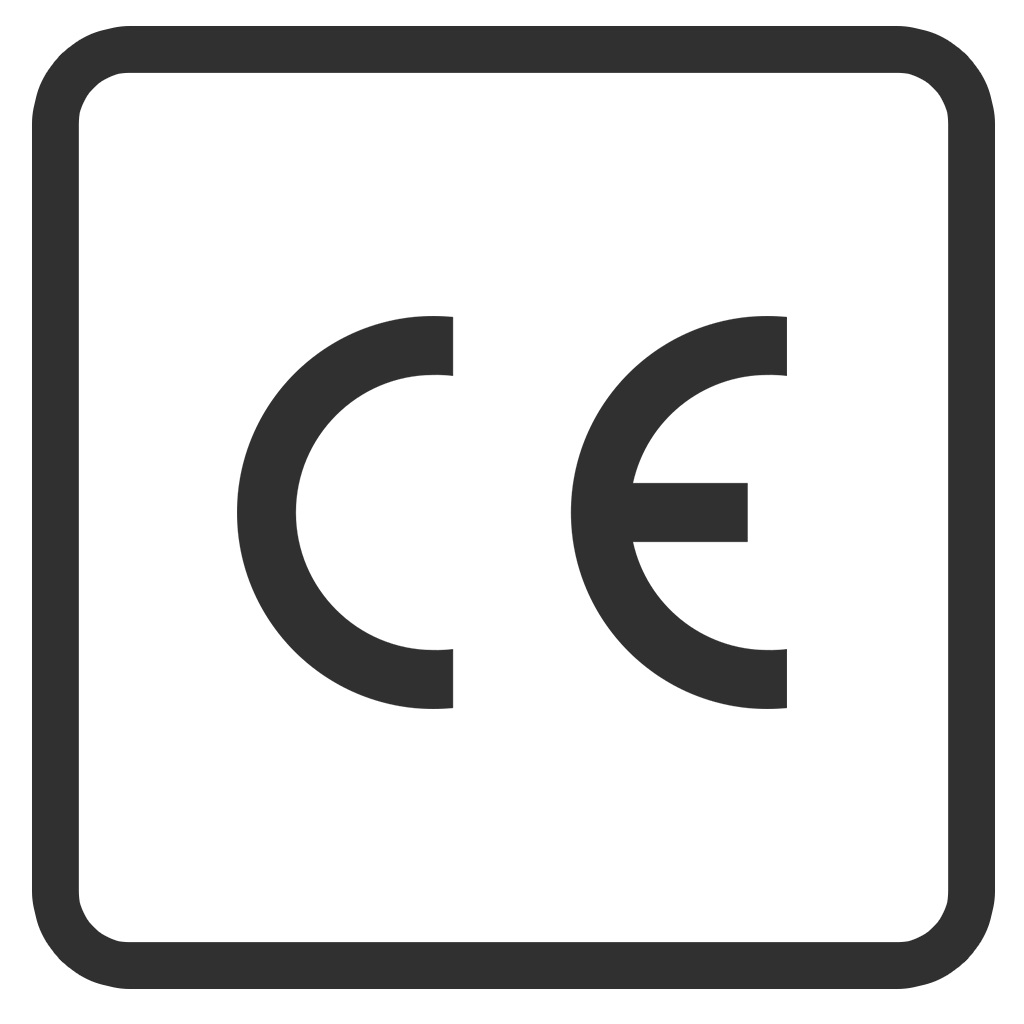
M-USG
Underwater pelletizing system for spring pelletizers - M-USG
The M-USG underwater pelletization system has been producing virgin polymers worldwide for decades. The extremely flexible system guarantees a high level of system availability, especially during continuous operation, and meets the highest quality requirements for cylindrical pellets.
Excellent, consistent quality pellets
Outputs up to 20,000 kg / h
Quick-change cutting head
High level of automation
Easy availability
Extremely durable cutting tools
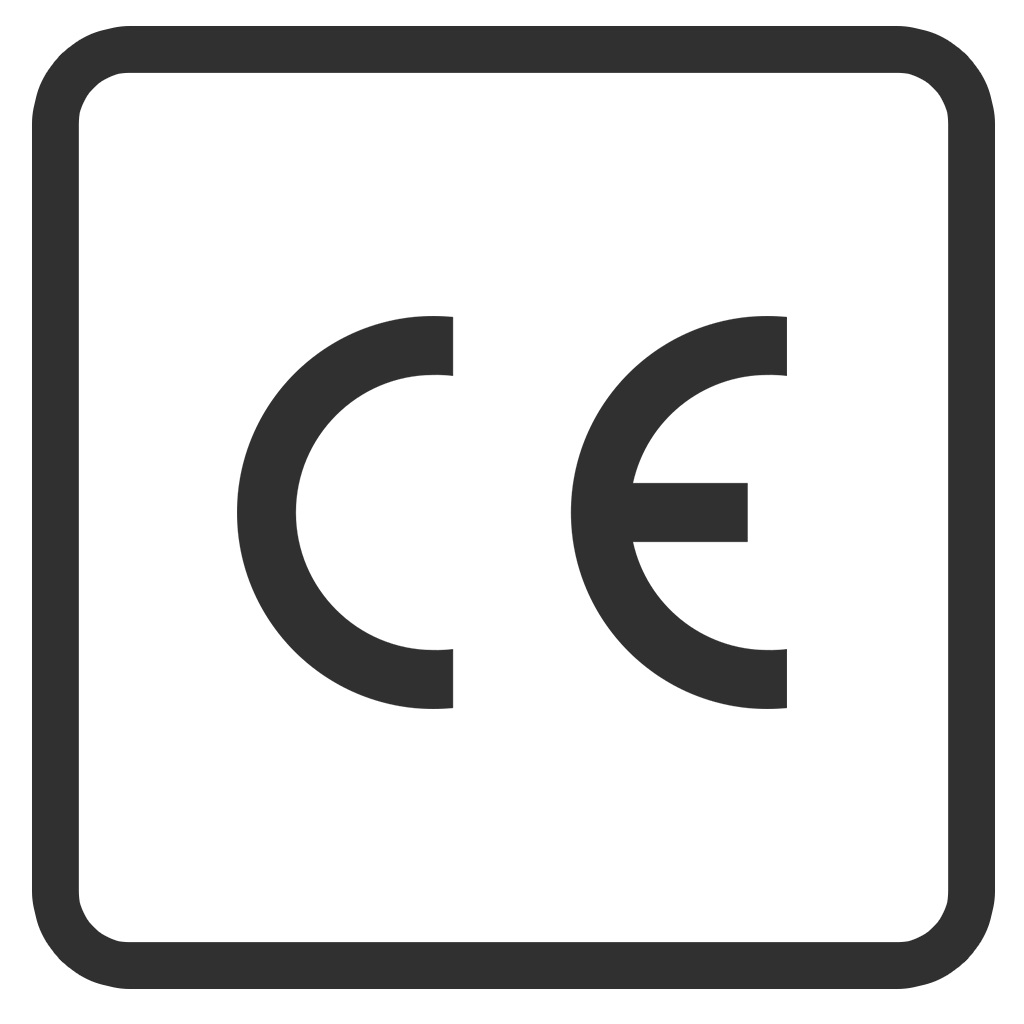
S3000 Pultrusion Series
Strand pelletizing and dry cut pelletizing for extrusion technology - S3000 Pultrusion Series
New extrusion technology of strand pelletizing and dry cut pelletizing is helping compounders of long fiber reinforced materials reach faster line speeds. Reduction Engineering Scheer was asked to specifically design a plastic pelletizer for better strand control and improve the pellets’ shape and cut quality. Traditionally, pultrusion pelletizers were fed strands by a belt puller only. The S3000 Series has been fitted with a front end feedroll mechanism. Coupled with the puller, the feedrolls ensure the strand control necessary for pellet accuracy and quality.
Unique Rotor Design for Maximum throughputs
Wide Feed Entrance
Insulated sound hood optional
Stainless Steel contact areas
Tool-less entry
Air Actuated Upper Feedroll
Dual drive optional
Designed per customer application
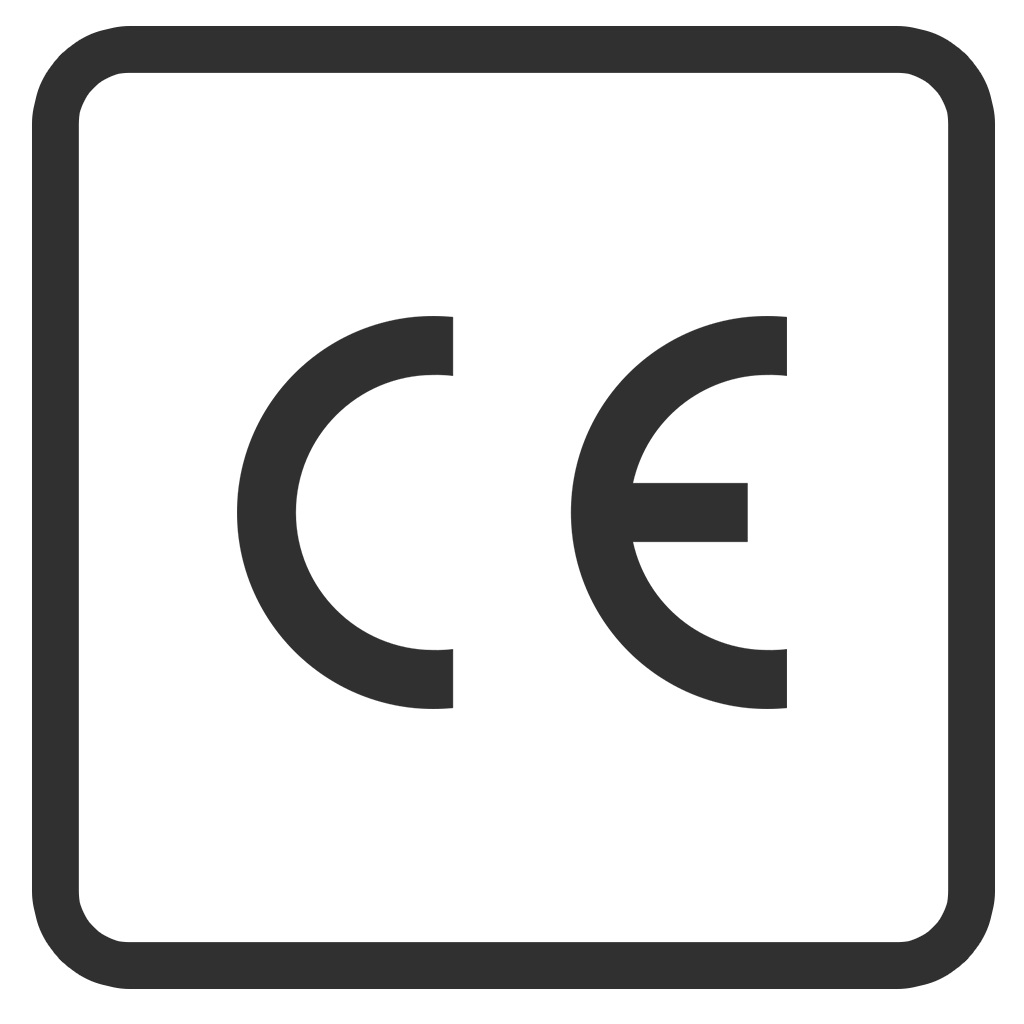
M-ASG for pultruded LFT pellets
Strand pelletizing and dry cut pelletizing processing - M-ASG for pultruded LFT pellets
The proven WSG dry-cut pelletizing and strand pelletizing systems with M-ASG pelletizers produce the highest quality of cylindrical pellets particularly suitable for further processing.
Compact solution
Robust design
Feed roller with its own motor
Changes in the length and weight of pellets
Long life
Wear resistance
Easy access for cleaning
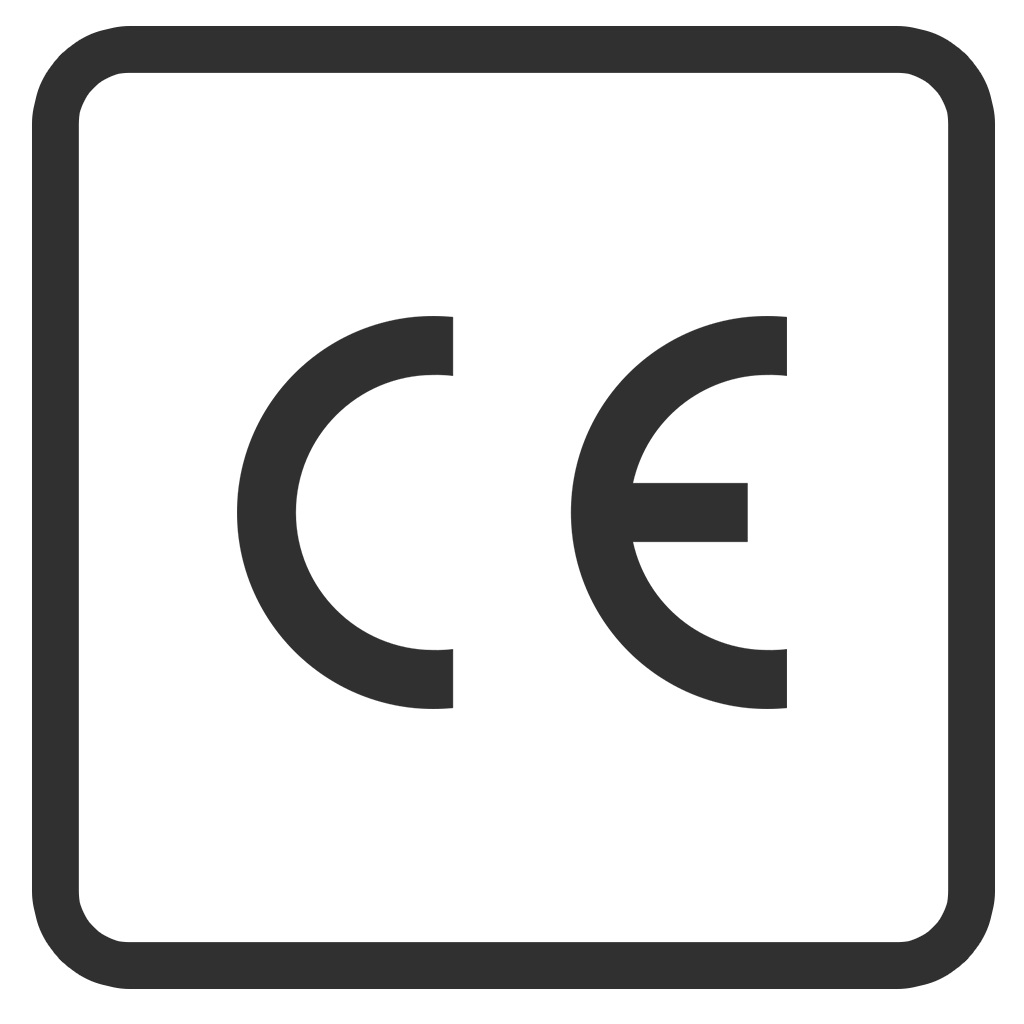
Pelletizing Systems for Glass Fiber Compounds
In the past, glass fiber compounds were usually produced by strand pelletizing. Recently, however, there has been a clear trend toward underwater pelleting. Wear resistance and optimized machine concepts have shown that high throughput rates and low wear costs are possible for glass fiber compounds from underwater pelletizing systems.
Glass Fiber Compounds
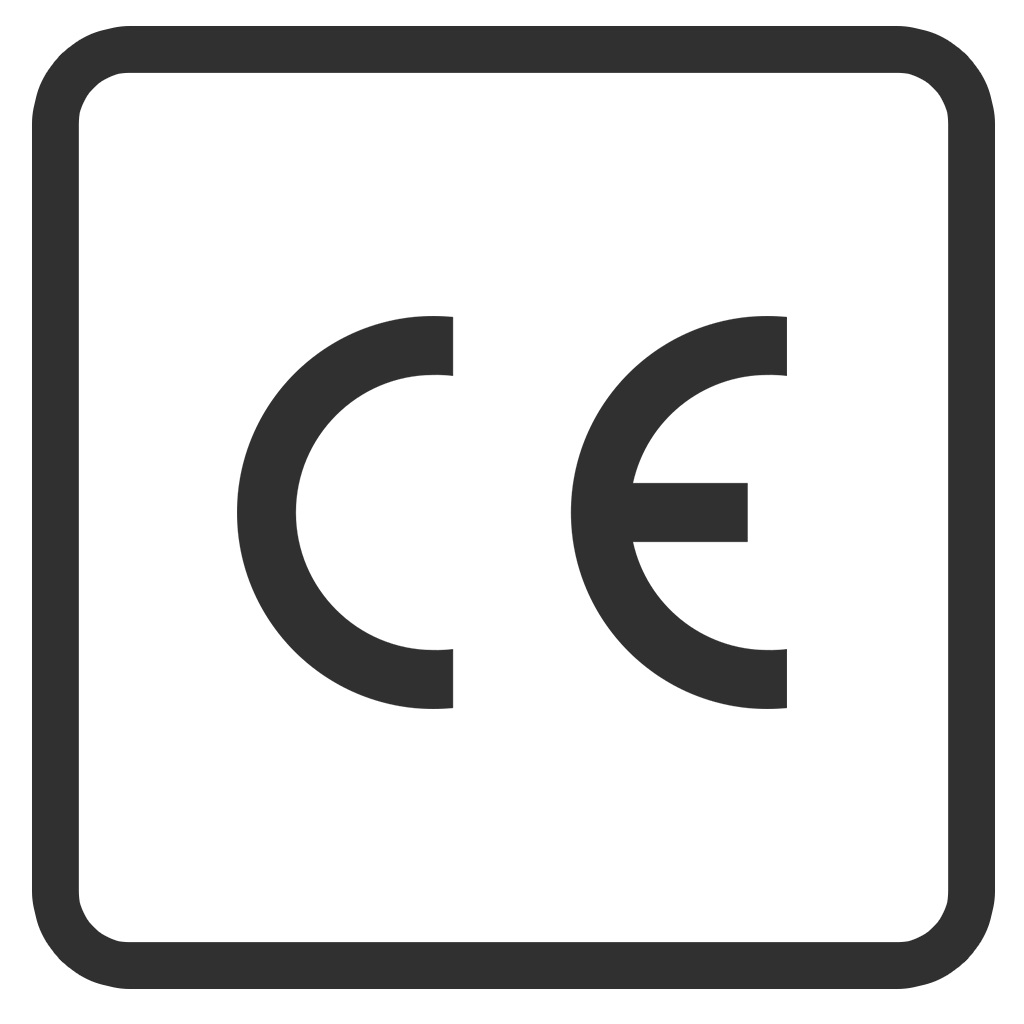
LWCP
Low Waste Continuous Production
The LWCP System concept was designed to allow the user to operate the production waste recycling machine on a continuous basis and to increase output without interruptions from a defined minimum throughput up to the maximum line throughput.
Lower costs for start-ups
Less material waste
Lower operating costs
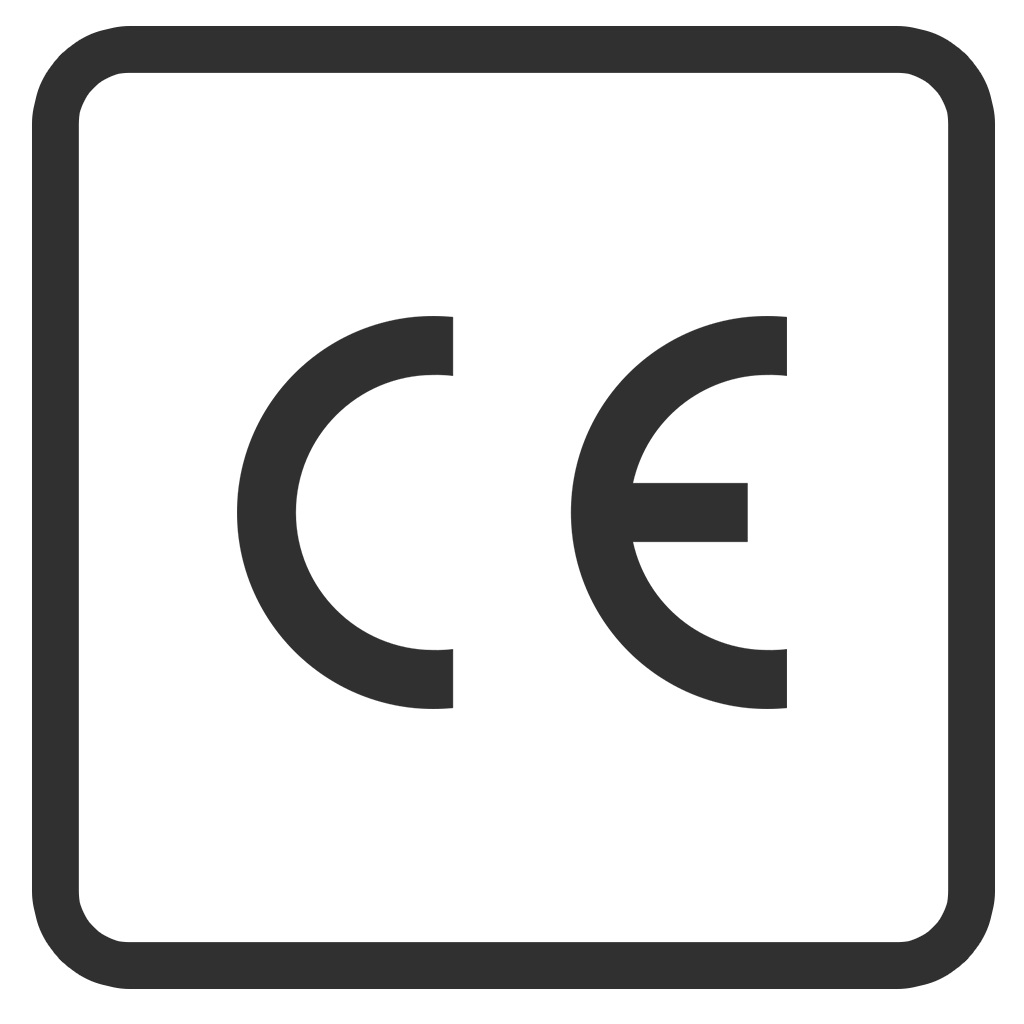
CLS Compact Lab System
Pellet Rates up to 500 kg/h
Gala’s COMPACT LAB SYSTEM, a underwater pelletizing system is used downstream of an extruder or gear pump for polymer production. Used in laboratory settings and by compounders when underwater pelletizing processes and drying samples of polyethylene, polypropylene, polystyrene, ABS, flexible PVC and other polymers.
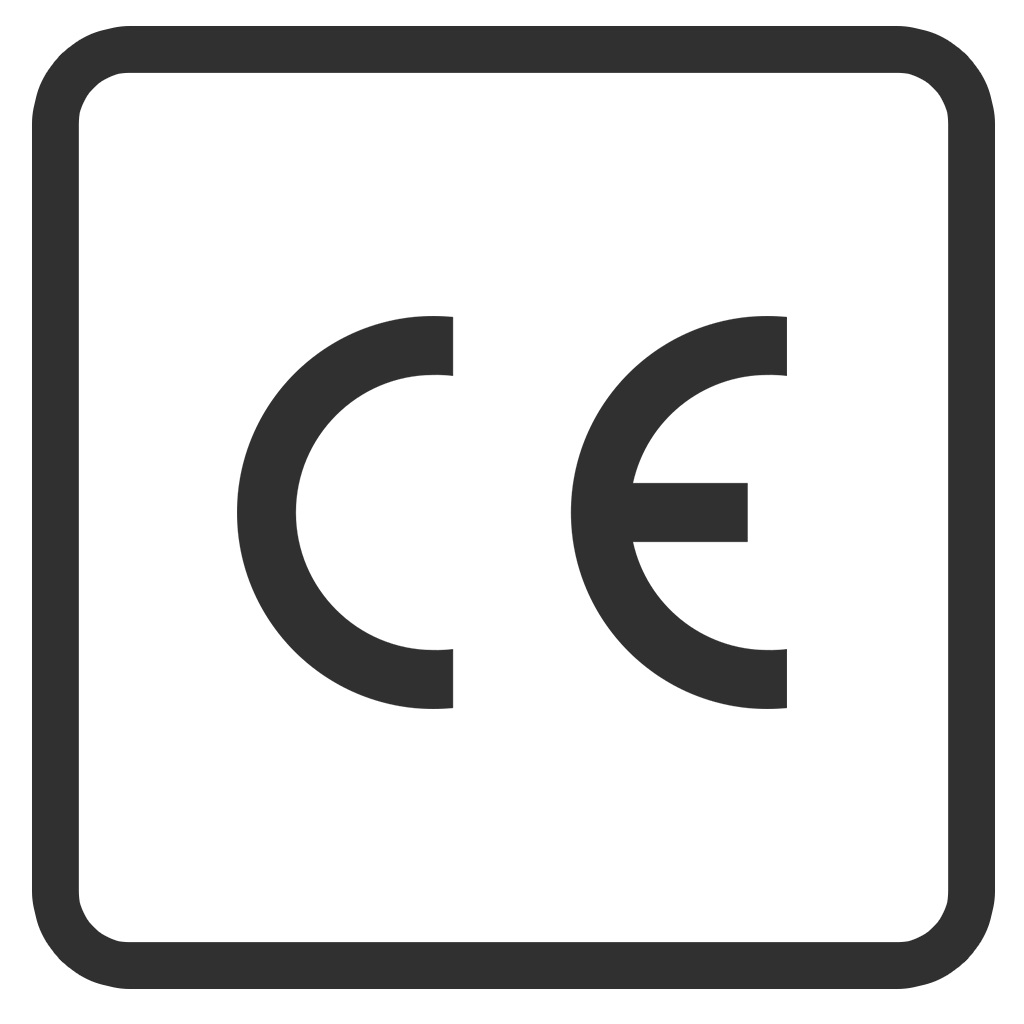
Flexline
The objective of the Flexline System for underwater pelletizing processes: The Flexline machine concept for underwater pellitizing systems is a logical extension of Gala technology. The machine concept permits complex product changes within a matter of minutes to minimize unproductive time for polymer and compound manufacturers.
Quick start
Minimal need for work
Flexibility in processing a wider range of recipes
Wear-resistant tools
Minimizes quality variations
Material savings
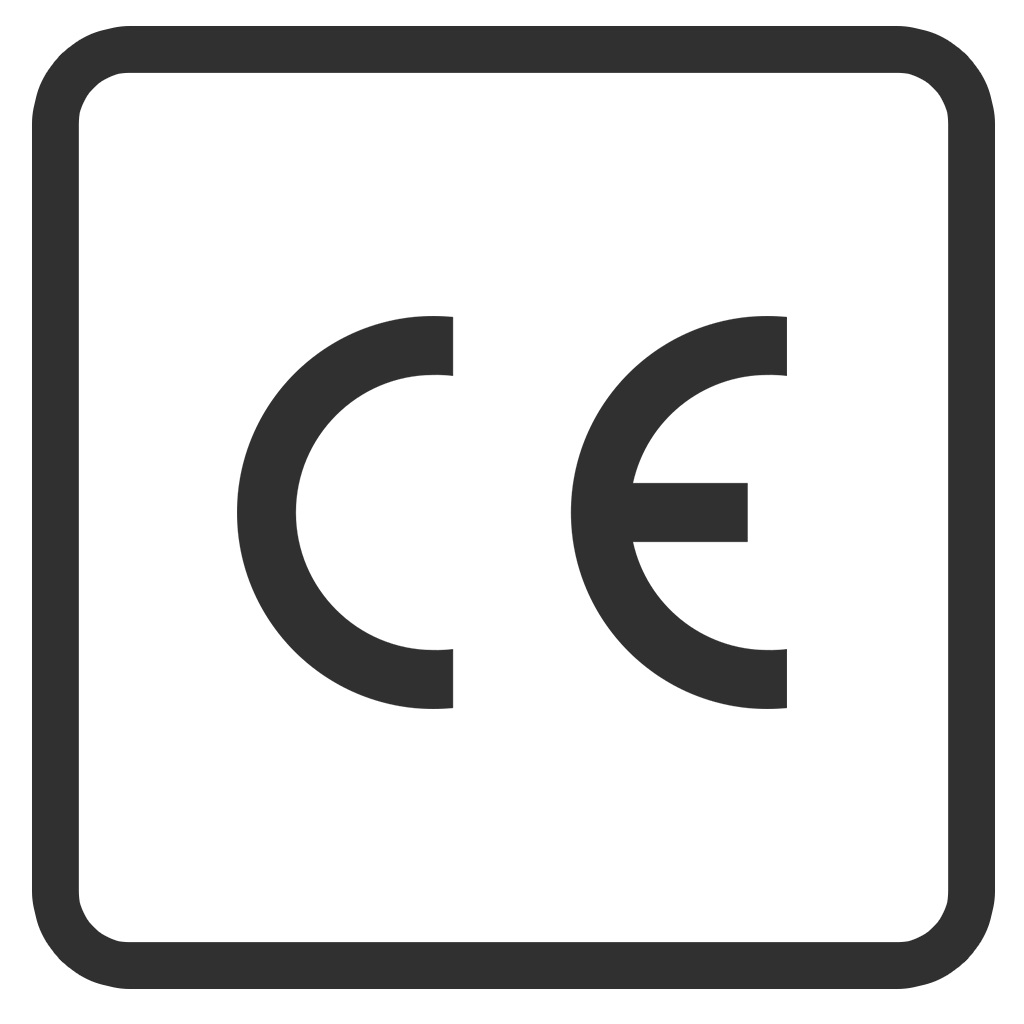
E-Series®
For pellet rates up to 1.500 kg/h, (depending on equipment configuration and polymers)
A value engineered underwater pelletizing system and underwater pelletizing process designed to economically pelletize and dry thermoplastics—polyethylene, polypropylene, polystyrene, rigid PVC, flexible PVC, and more—for polymer production at throughput rates of up to 1,500 kg/h (3307 lbs/hr.)
Simple and compact
Includes a fully functional control system
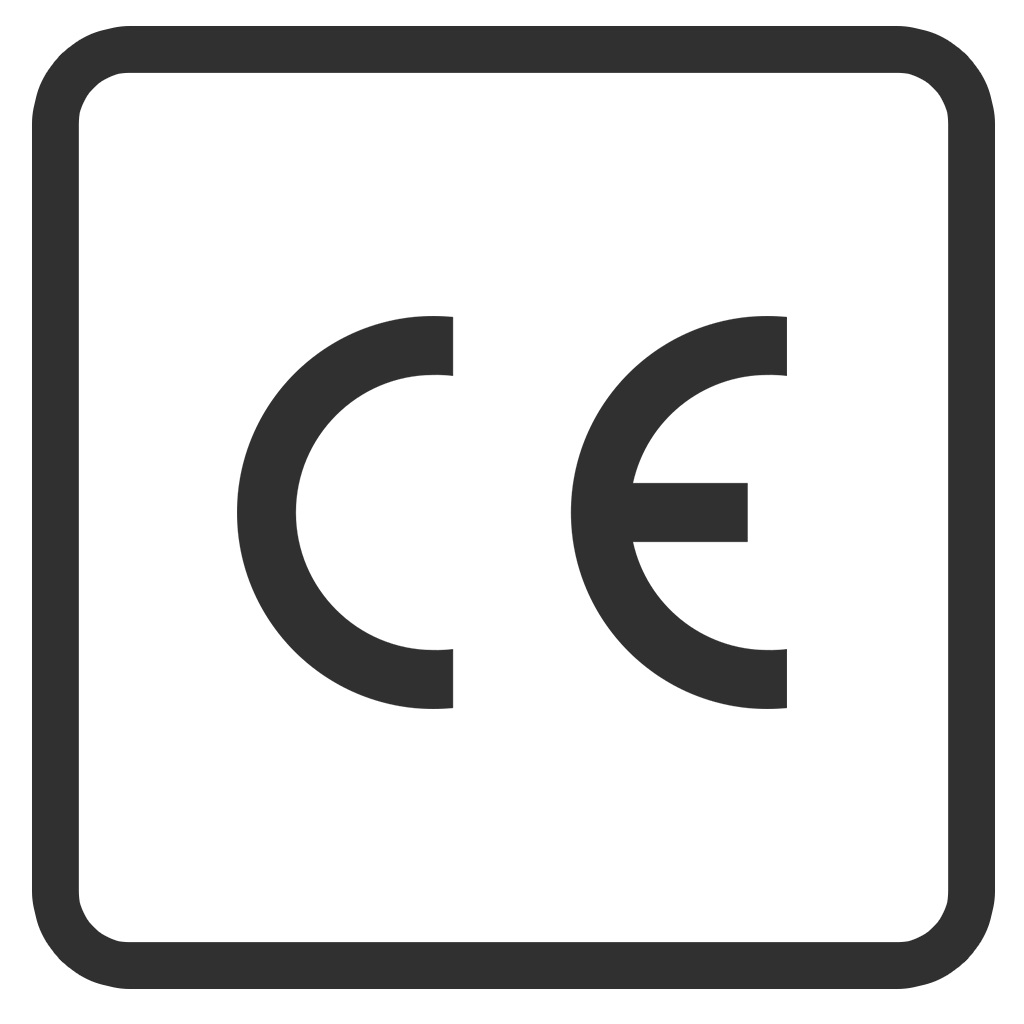
SPHERO®
Underwater pelletizing systems for highly profitable throughput rates of up to 36,000 kg per hour
The SPHERO® underwater pelletizing system has been particularly designed to process thermoplastics and produces spherical pellets. This most flexible system for underwater cutting is applied in the production of raw materials, compounds, masterbatches, engineering plastics, recyclate, organic and wood polymer composites, thermoplastics elastomers, microgranulate, hot-melt adhesives, and more.
It has reached the quality of a pellet
Convenient and safe service
Increased production performance
Fast product change
Optional approach
Increased process independence
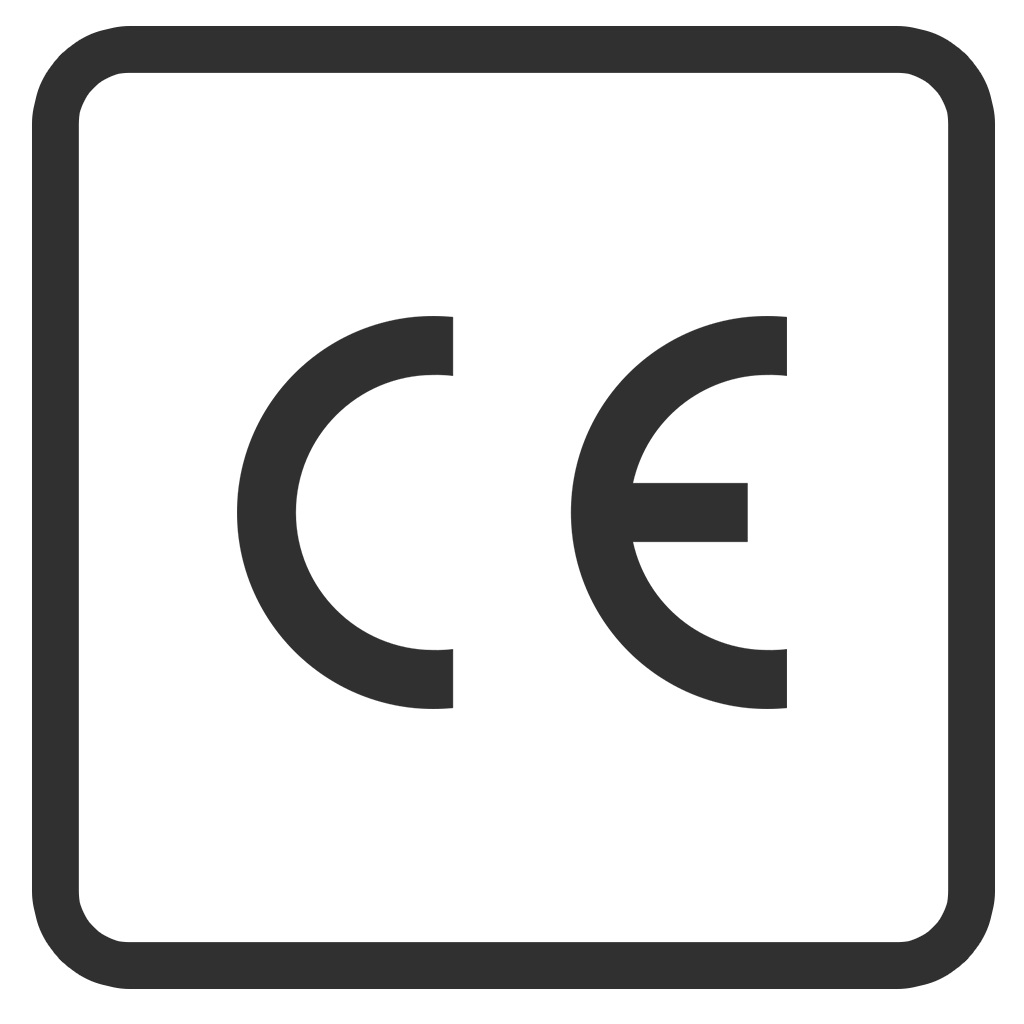
SLC
Spring-Loaded Pelletizer
The Spring Loaded Cutter (SLC) is a cost efficient solution for underwater pelletizing basic polymers at lower rates. The SLC pelletizer uses constant spring pressure to adjust the cutter blades to the die plate, reducing the need for operator attention and underwater cutting. The cutter hub is connected to the motor shaft through a telescoping spring sleeve, and the blades are automatically positioned against the die plate using spring force. The blade force can be adjusted per application or product by simply changing springs.
Cost effective solution
Simple control
Low maintenance
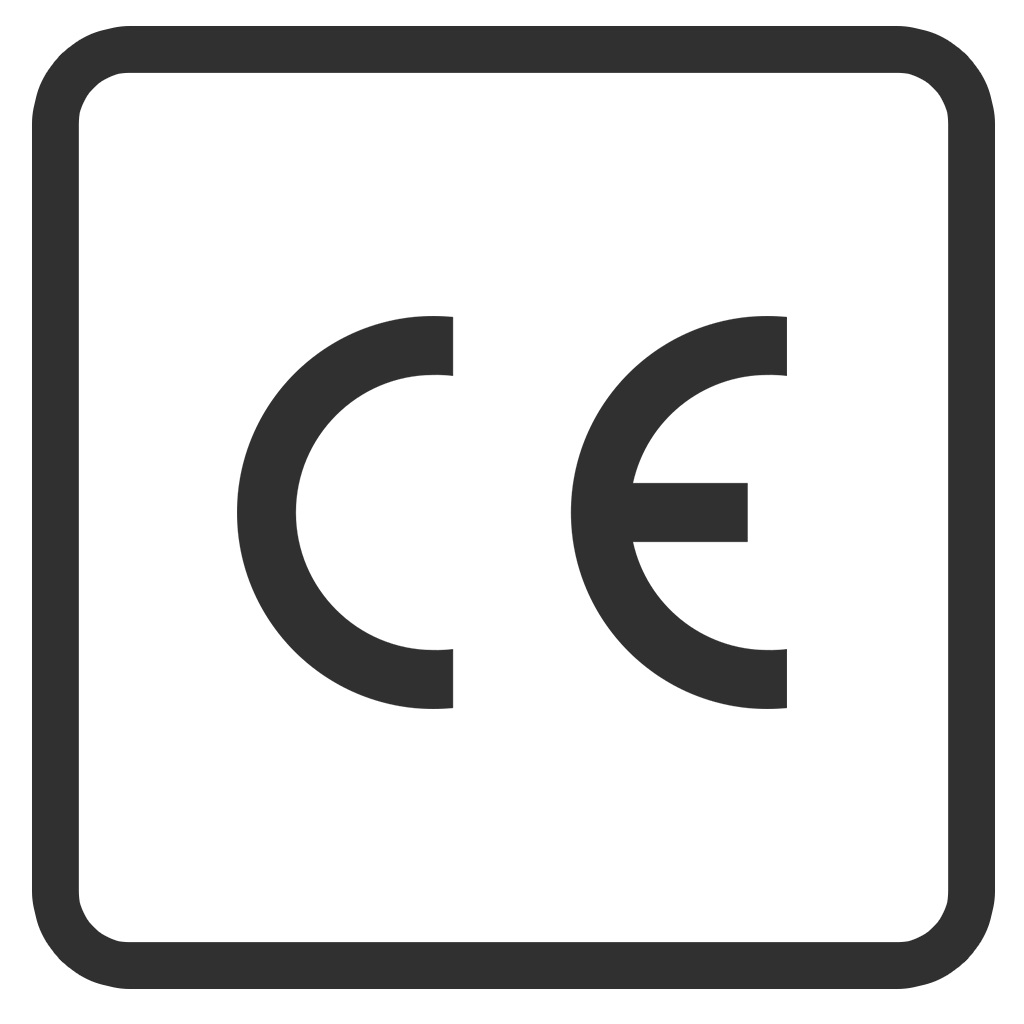
ZHULI®
Advanced, cost-effective underwater pelletizing technology
ZHULI® is an underwater pelletizing system with integrated pellet dryer and process water handling, designed to process a wide range of polymers and thermoplastics. The efficient system is characterized by high flexibility and small footprint. ZHULI® is manufactured locally with key components made in Germany. With an installed base of more than 9,000 underwater pelletizing systems, we help our customers to achieve the maximum level of profitability.
Ideal for all thermoplastics
Outputs up to 1,800 kg / h
Fully enclosed system
Small size and user friendly
Quick product exchange
Pellets of excellent quality
Long life
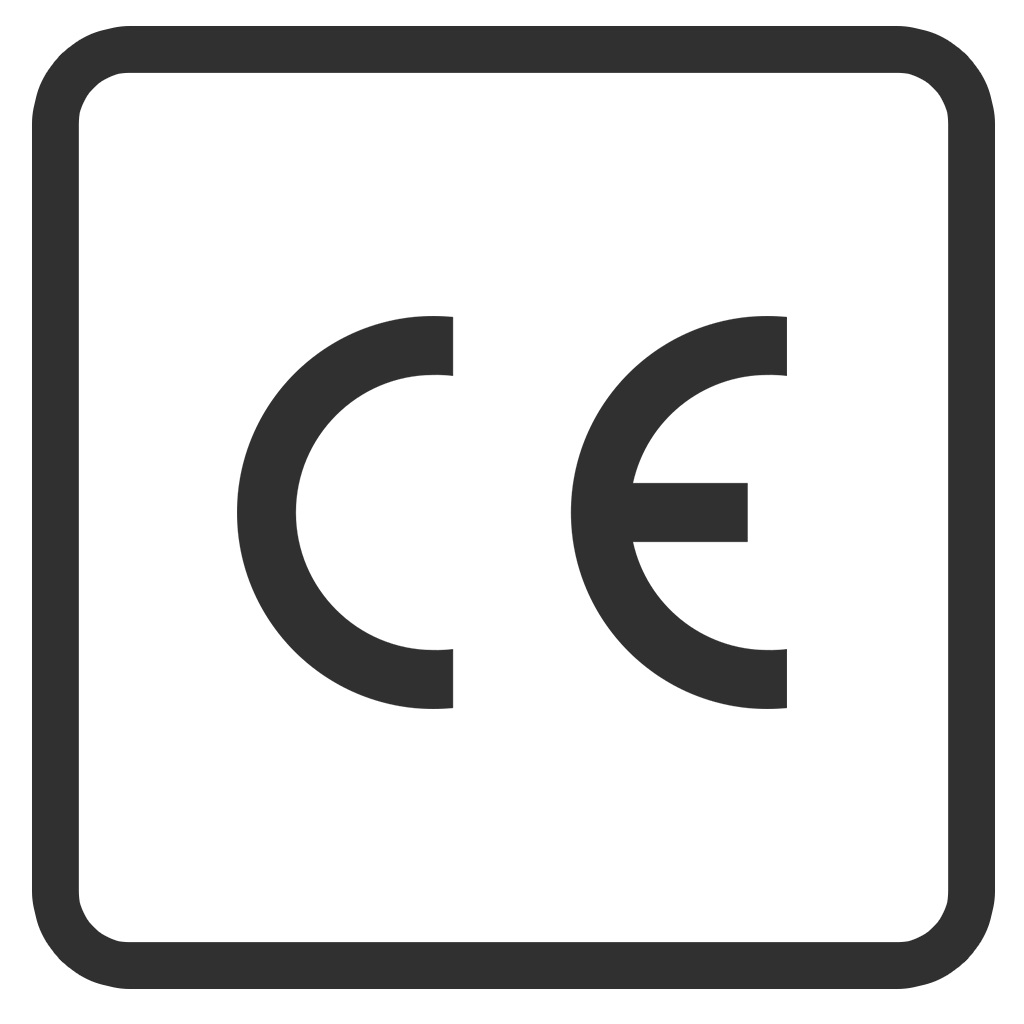