MAAG Company
The MAAG Group comprises successful and renowned companies, each with their own impressive history. Automatik Plastics Machinery, Ettlinger Kunststoffmaschinen, Maag Pump Systems, Gala Industries, Reduction Engineering Scheer and Xantec Steuerungs- und EDV Technik are today the strong and innovative product brands of the MAAG Group.
The history of the MAAG Group thus begins in the late 19th century, with the establishment of Scheer as a metal foundry and machine factory in Stuttgart, Germany, in 1890. Maag Pump Systems was founded in 1913. Automatik Plastics Machinery was founded in 1947. Gala Industries was founded in 1959, and Ettlinger Kunststoffmaschinen in 1983. The youngest member of MAAG Group – Xantec Steuerungs- und EDV-Technik was founded in 1994. Over the decades, they have all grown into experts in the various fields of polymer production and processing.
All the members of the MAAG Group contribute their supreme expertise and years of experience in developing and manufacturing superb machines, plants, systems, and software – and will continue doing so in the future. The bundling of core competencies, industry best practices, the attentive maintenance of existing business relationships and creation of new ones, all provide the foundations for maximum customer satisfaction throughout the Group.
High performance Melt Filters – The ECO Series
The continuous melt filters in the ERF series are suitable for materials with up to 16% by weight contamination and are guaranteed to remain in use for long periods without changing the filter. Our ERF melt filters are capable of processing a wide range of polymers (e.g. LDPE, LLDPE, HDPE, PP, PS, ABS, PC / ABS, TPE, TPU, POM). All solid or elastomer foreign particles such as paper,wood, aluminum, copper, rubber, silicone, or high-melting polymer composites are efficiently removed.
The classic application for ERF melt filters is repelletizing lines, but they are also successfully employed for sheet and profile extrusion. ERF melt filters can in principle be used in any extrusion line – either single or twin-screw and irrespective of the type of pelletizing system or other downstream unit. Three different sizes enable throughputs from 150 to 10,000 kg/h depending on the application.
Suitable for Compounding, Recycling, Extrusion
Fully automatic, continuous operation
Up to 18% contaminants removed
Extremely low melt losses
More reliable processing due to constant pressure at the filter outlet
No need to replace the screen for several weeks, or possibly months, depending on the material and the application
Completely closed system with no entrapped air
Short contaminant residence times in the filter
Very simple replacement of the scraper from outside using a hydraulic cylinder
Elastomers (rubber, silicone) are efficiently filtered and discharged before they have a chance to be forced through the filter screen
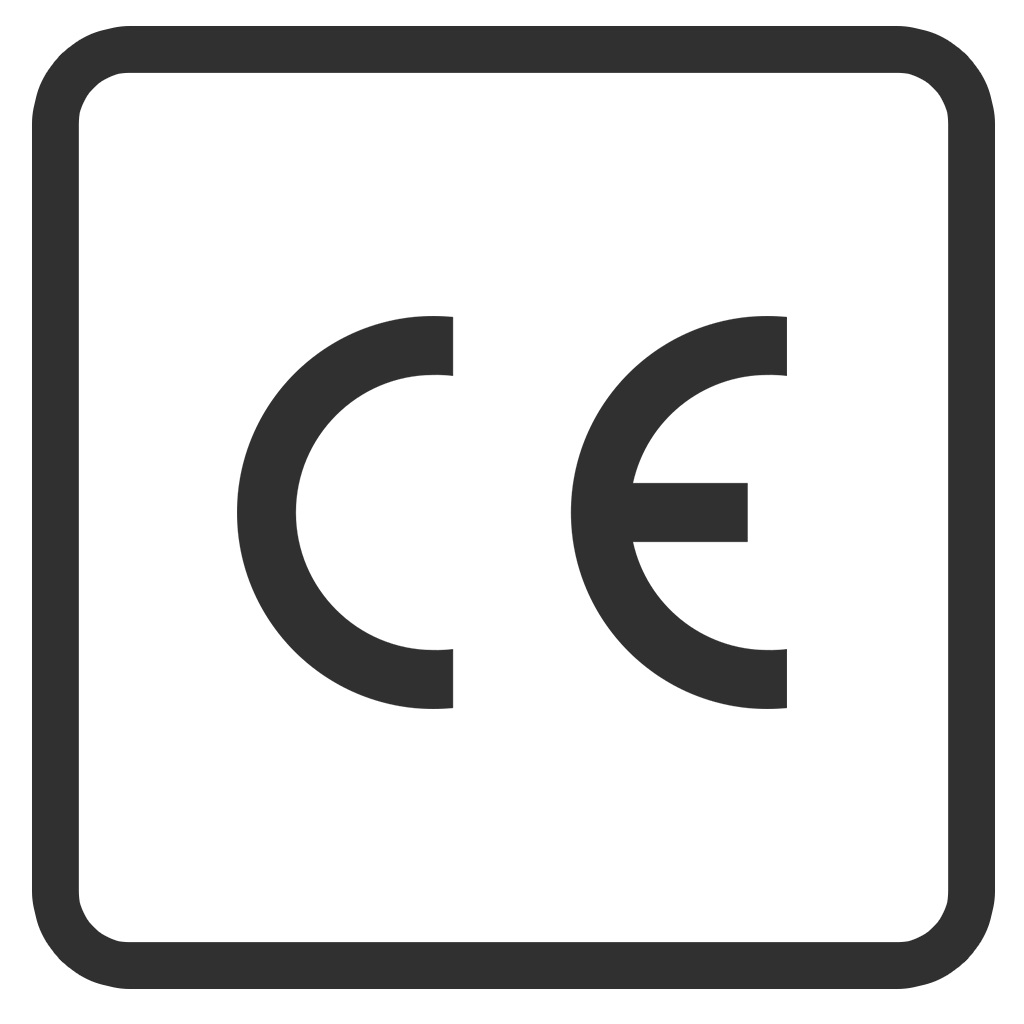
High performance Melt Filters - The ERF Series
The continuous melt filters in the ERF series are suitable for materials with up to 16% by weight contamination and are guaranteed to remain in use for long periods without changing the filter. Our ERF melt filters are capable of processing a wide range of polymers (e.g. LDPE, LLDPE, HDPE, PP, PS, ABS, PC / ABS, TPE, TPU, POM). All solid or elastomer foreign particles such as paper,wood, aluminum, copper, rubber, silicone, or high-melting polymer composites are efficiently removed.
The classic application for ERF melt filters is repelletizing lines, but they are also successfully employed for sheet and profile extrusion. ERF melt filters can in principle be used in any extrusion line – either single or twin-screw and irrespective of the type of pelletizing system or other downstream unit. Three different sizes enable throughputs from 150 to 10,000 kg/h depending on the application.
Suitable for Compounding, Recycling, Extrusion
Fully automatic, continuous operation
Up to 18% contaminants removed
Extremely low melt losses
More reliable processing due to constant pressure at the filter outlet
No need to replace the screen for several weeks, or possibly months, depending on the material and the application
Completely closed system with no entrapped air
Short contaminant residence times in the filter
Very simple replacement of the scraper from outside using a hydraulic cylinder
Elastomers (rubber, silicone) are efficiently filtered and discharged before they have a chance to be forced through the filter screen
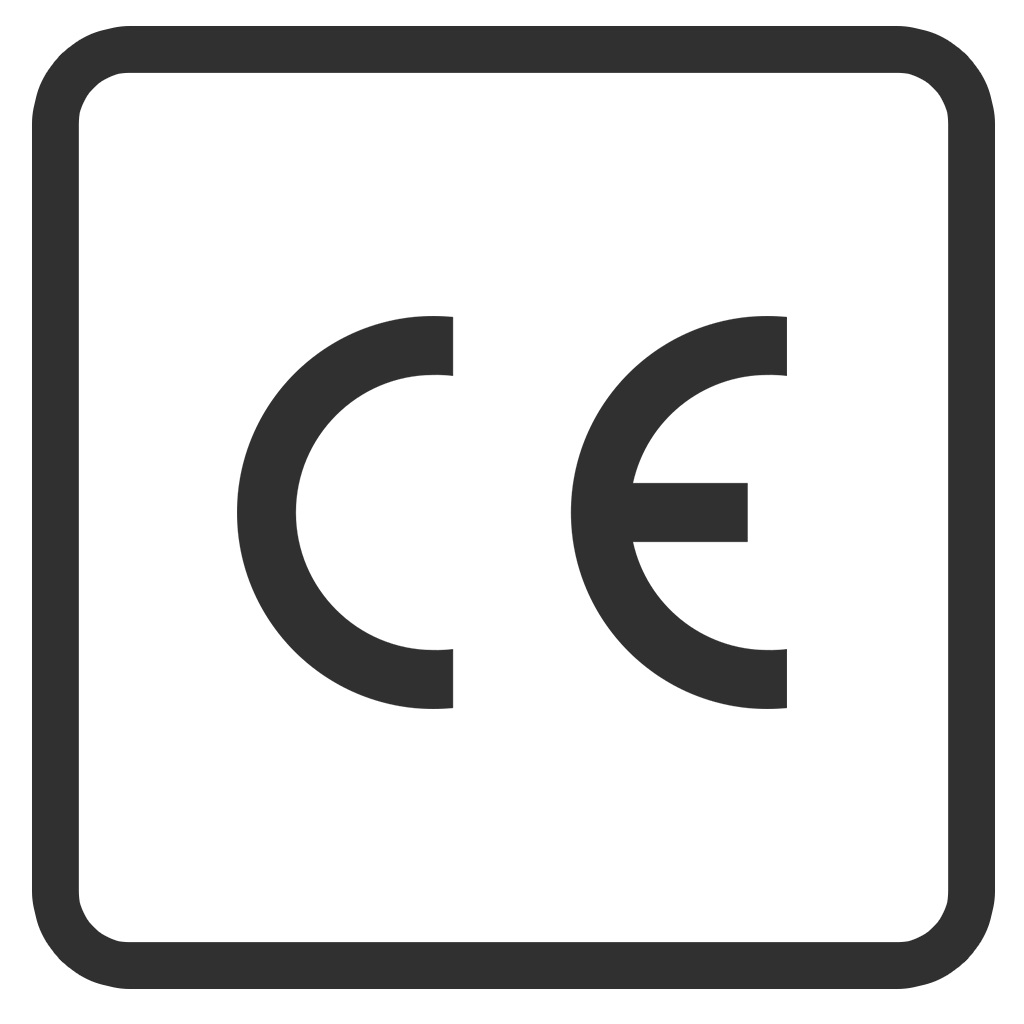
CSC/BF-4F
Automtic self cleaning screen changer for polymer extrusion industry and filtration systems
MAAG backflush automatic self cleaning screen changers are based on the proven double-piston design which operates without any mechanical seals. The screen changers are equipped with four screen cavities. This design is used mainly in recycling applications for filtration systems.
Multiple screen usage
Simple operation and uncomplicated control
High operational reliaility
Short material residence time
Leak-free mode of operation
Low pressure consumption
Flow channel geometry without any dead spots
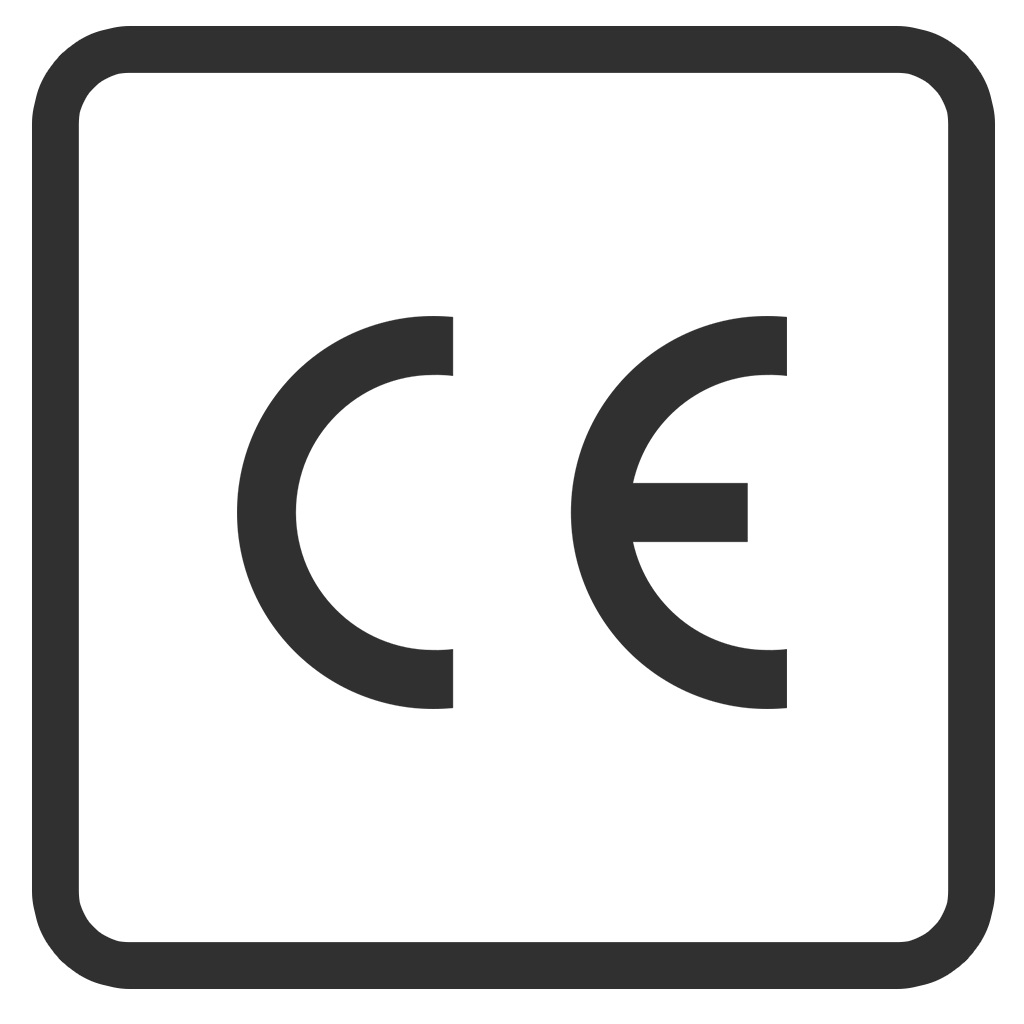
CSC-R - Screen changer with curved filter screens
MAAG’s CSC-R large scale screen changer with curved screens is designed for the use of one-way filter screens which do not require cleaning after the simple and safe screen change. The screen bearing pistons belong to MAAG’s modular filter system and its patented design use 75% of the piston surface as active filtration area. Also this filter execution can be installed for vertical or horizontal melt flow directly at the reactor discharge melt pump or pelletizer booster melt pump to avoid additional piping for reduction of melt residence time.
Suitable for Resin & Virgin Polymer Production
Up to 4x more filter area than circular screen cavities
Higher throughput
Multiplied screen life time
Smaller hydraulic unit
Lower melt pressure
Higher filtration fineness
Reduced flux rate kg/h/cm2
Ultra-compact design
Less heating capacity
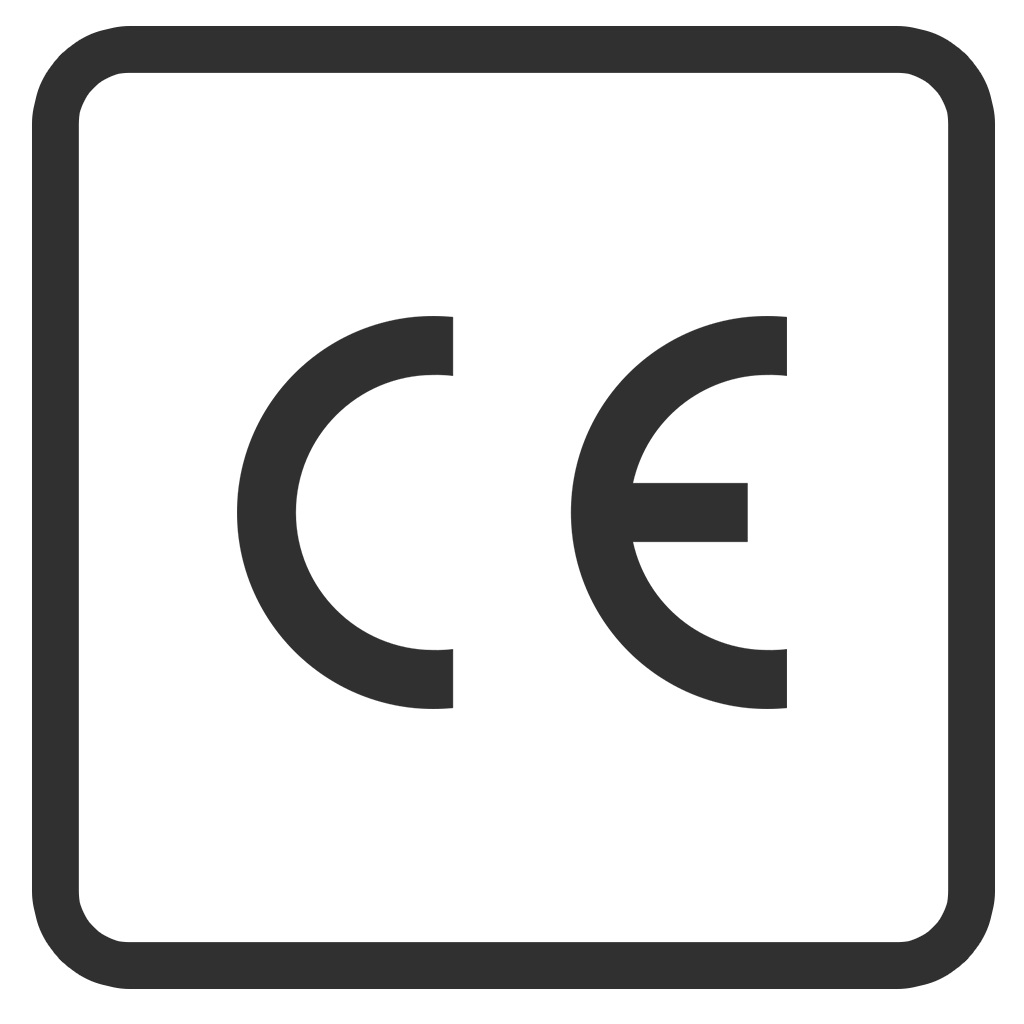
CSC-C - Polymer filtration for polymer production, polymer processing and extrusion
MAAG’s CSC-C large scale screen changer with candle filter elements is the right choice if short melt residence time, small footprint and a simplified candle change are required. Depending on the polymer type, melt viscosity, reactor throughput, and filter fineness, the screen changer size and number of pistons are customized to the application. The patented design allows the use of pleated micronex® candle filter elements with fiber metal felt (FMF) media, or cylindrical Multinex candles filter elements with interchangeable filter sleeves.
Suitable for Resin & Virgin Polymer Production
Filter elements
Vertical / horizontal installation
2/4 pistons
Patented design
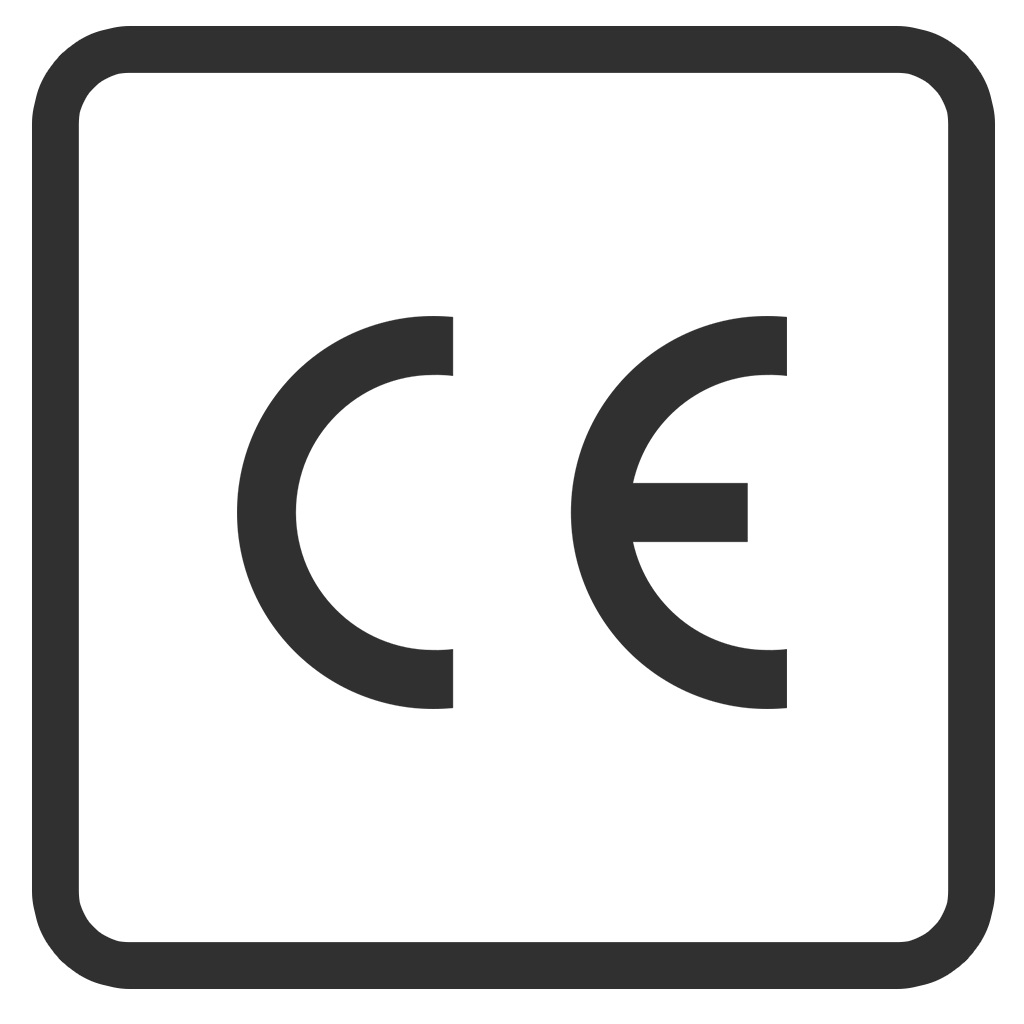
Simplex - Discountinuous large area polymer filtration applications for industry and extrusion
MAAG-designed simplex polymer filter systems can be provided with either fixed or removable vessels. A compact preheat station with spare vessel is also available for locating near the polymer processing line for quick changeout. They are custom designed to minimize initial pressure drop and maximize polymer filter element life. Our proprietary sizing program, based on more than 20 years of experience in the field of polymer production and extrusion, incorporates your operating data to size each system for maximum performance and optimized flow while maintaining compact dimensions.
Suitable for Resin & Virgin Polymer Production, Extrusion
Lower cost
Easier operation
Less space requirements
Minimized pressure drop
Horizontal or vertical design
No diverter valves
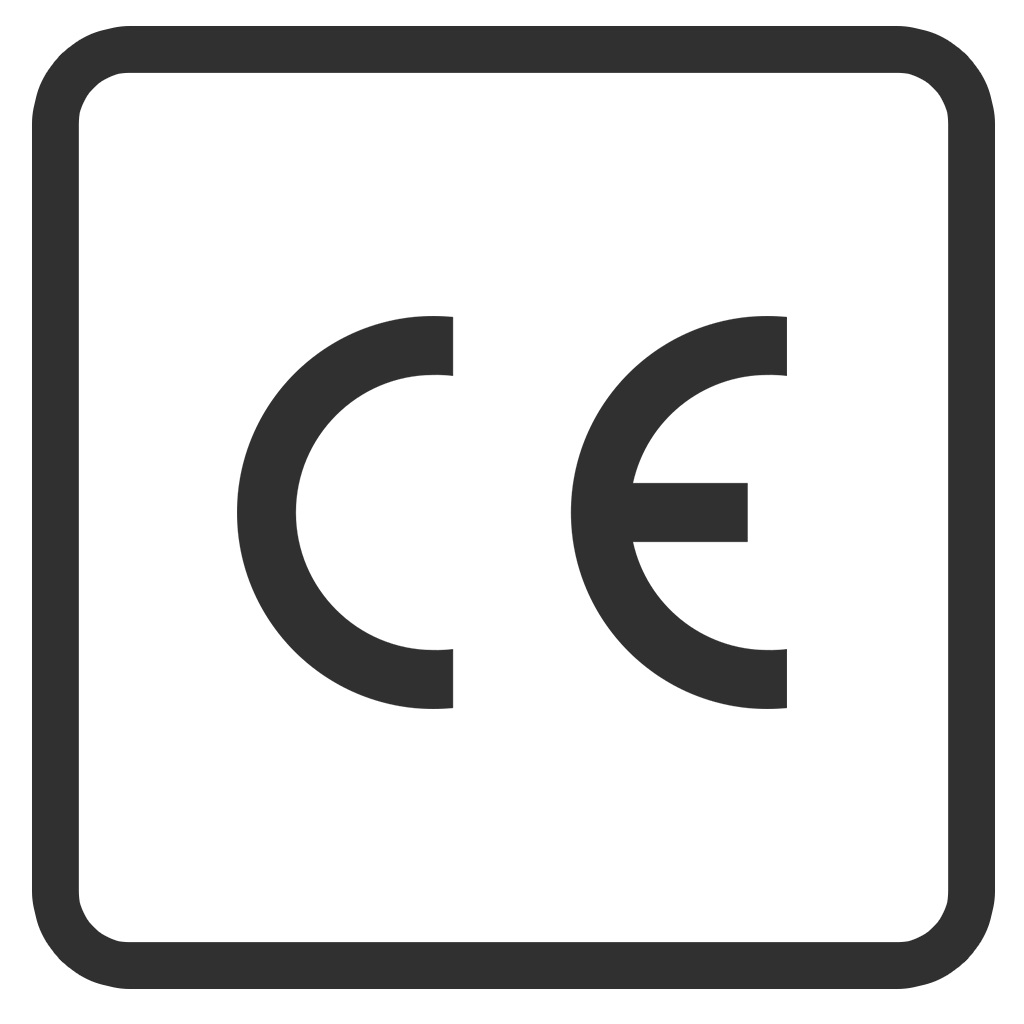
multinex
Polymer filter candles and application for masterbatch and polymer filtration
MAAG multinex polymer filter candles are tailor-made for use in continuously operating dual bolt screen changers of the MAAG CSC-P/C series for polymer filtration.Compared to typical polymer application round screen plates, they increase the active screening area up to 60
Optimized for high viscosities
Reusable candle bodies
Economic perforated sleeve exchange
Screen mesh or metal fiber fleeze
Filter fineness 0.5-500 micron
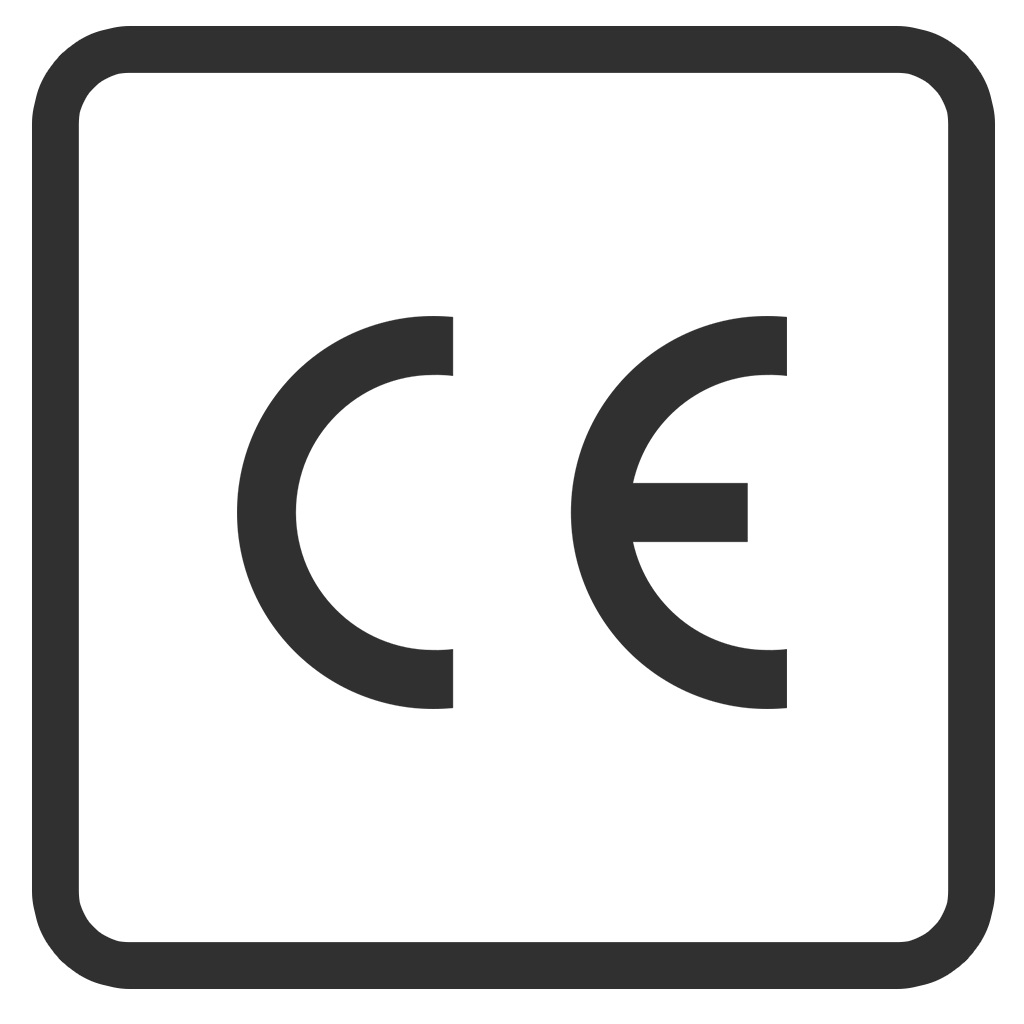
micronex
Polymer application and polymer filtration with filter elements for large areas
MAAG offers high-quality polymer filter elements designed for long term use and multiple cleanings. MAAG can provide standard design polymer application or build to your requirements regarding:
Filter elements designed for individual processes
Optimized polymer flow
Maximized filter area
Lowest possible pressure loss
Designed to retain hard and deformable particles
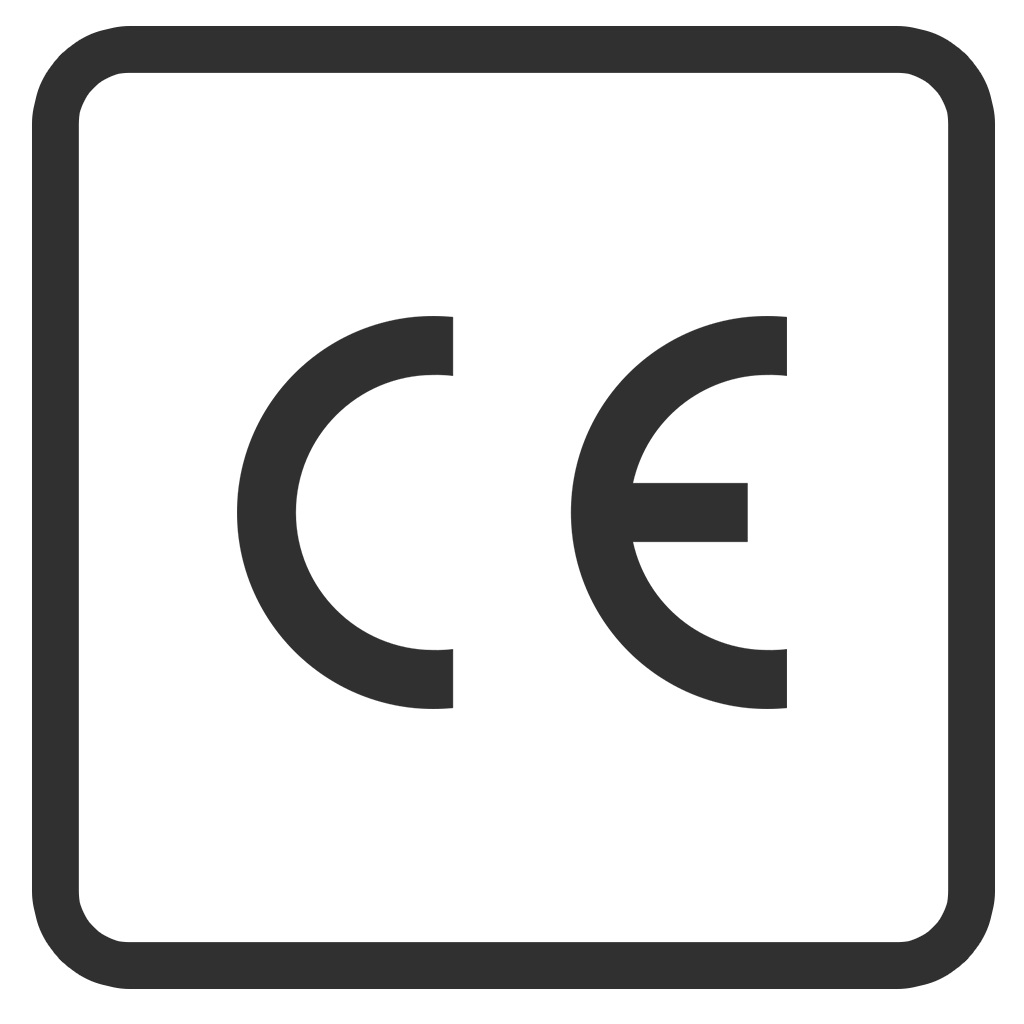
DFS - Continuous large area polymer filtration systems
MAAG’s new generation Duplex Filter System (DFS). The new DFS incorporates a new patented solid body DIVEXpro switch over valve. The vent and drain valves are also newly designed and integrated into the body of the DIVEXpro. Combined with MAAG’s established MICRONEX® filter candles the new generation filter system can meet the harsh demands of polymer filtration. For chemical recycling applications with low viscosity and high contamination levels the new generation DFS-BF is capable of performing an automated backflush cleaning of the filter candles during operation.
Suitable for Resin & Virgin Polymer Production
Reliable sealing
Improved venting
Better draining
Simplified vessel changeout
Improved accessibility
Safer operation
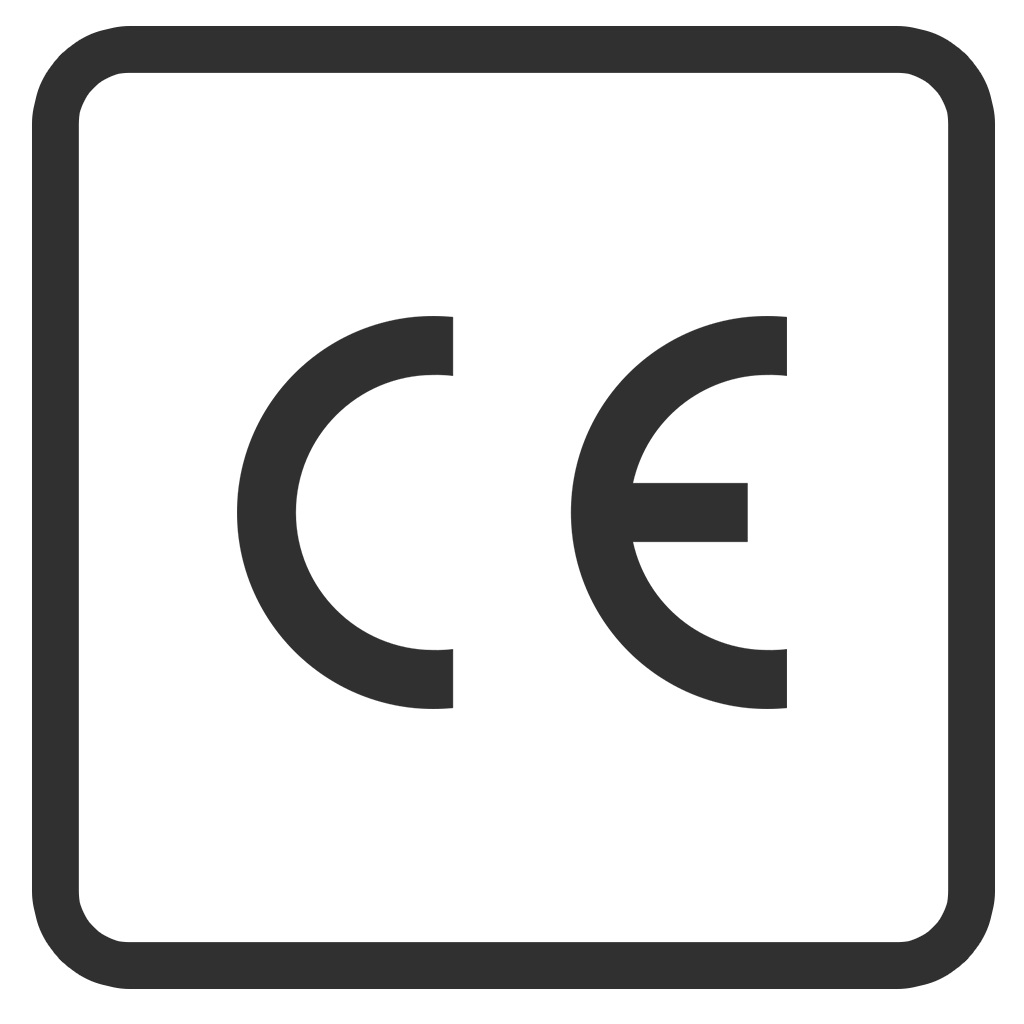
CSC - Continuous screen changers and double pistion screenchangers for filtration systems
Continuous CSC screen changers from MAAG with their robust and leak-free operation meet highest quality standards with respect to melt filtration. Due to their constantly improved functionality continuous screen changers from MAAG increase product quality significantly. CSC screen changers are based on the proven double-piston design that operates without any additional seals. Their sturdy construction available in all sizes and designs guarantees a reliable and leak-free filtration of polymer melt for many years.
Suitable for¨Rotomolding, Hot Melt Adhesives, Resin & Virgin Polymer Production, Masterbatch, Compounding, Recycling, ExtrusionSimple operation and uncomplicated screen changing
High operational reliability
Short material residence time
Leak-free mode of operation
Low pressure consumption
Flow channel geometry without any dead spots
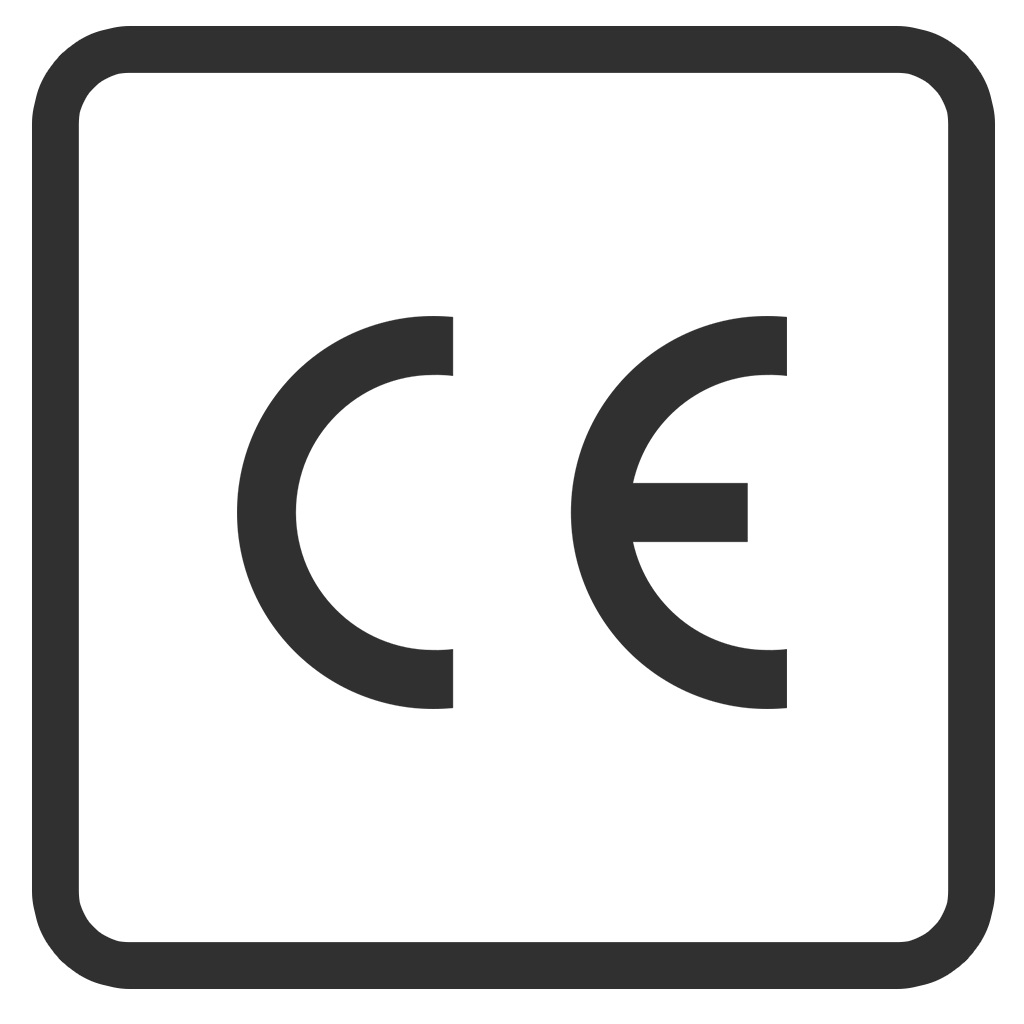
FSC-OEM
Optimized flat screen changer for processing of plastics
The flow optimized new version of MAAG´s FSC hydraulic and manual screen changers assist operators of plastic extrusion lines in achieving a reduced equipment footprint, reduced residence time and improved residence time distribution.
Reduction of pressure loss
Optimized flow
Increased production speed
Energy efficiency
Elimination of pressure fluctuations
Reduction of material consumption
Easy maintenance
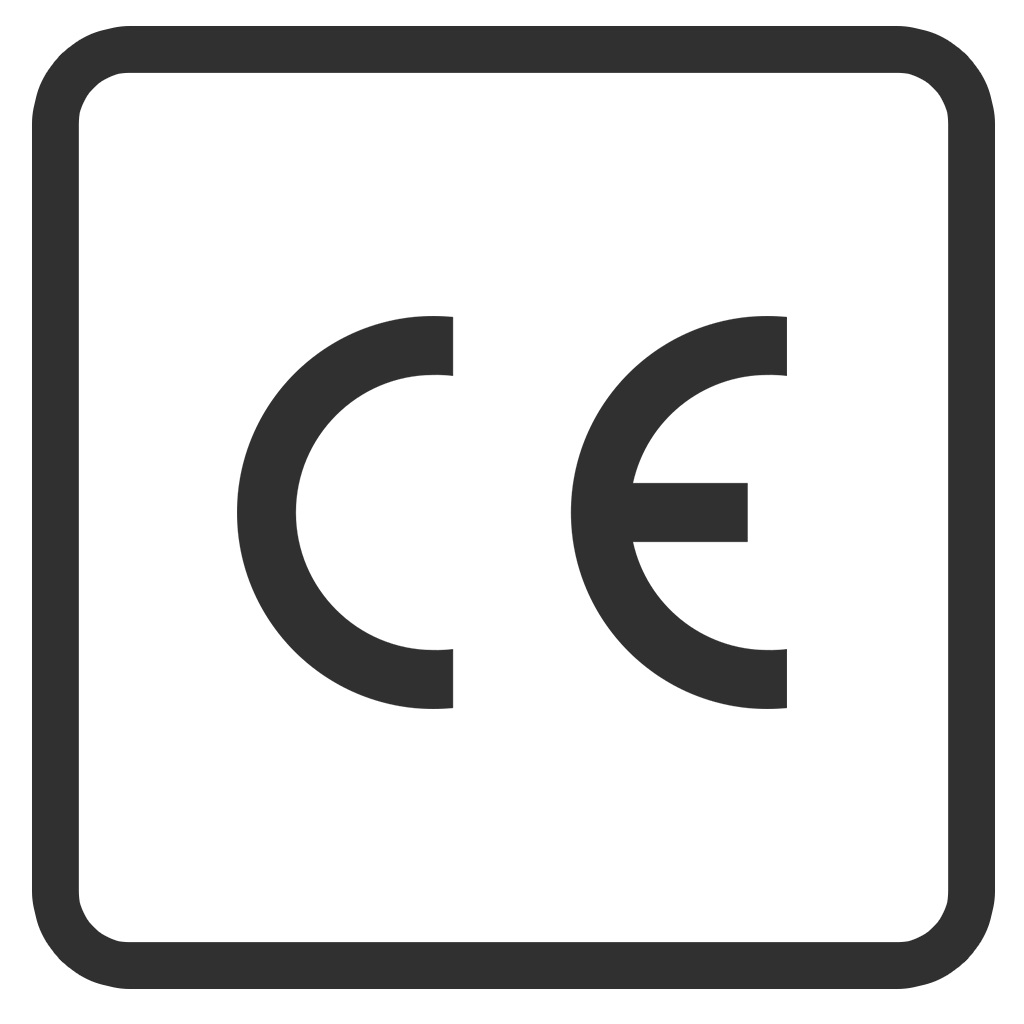
HSC - Manual screen changer and plate screen changer for filtration solutions and extrusion processes
Manual screen changers from Maag have been the first choice of cost-effective filtration systems in extrusion lines for many years. Starting at size 45, the manual screen changers optionally come with transmission gearing. Here, the breaker plate is equipped with patented gearing and a pinion which allows an effortless screen change even in restricted space conditions or high sealing pressures. The manual screen changer guarantees the protection of gear pumps and fine extrusion die gaps from damage and dirt accumulation.
Suitable for Recycling, Extrusion
Simple operation with quick screen change
High operational reliability
Short material residence time
Leak-free mode of operation
Low pressure consumption
Flow channel geometry without any dead spots
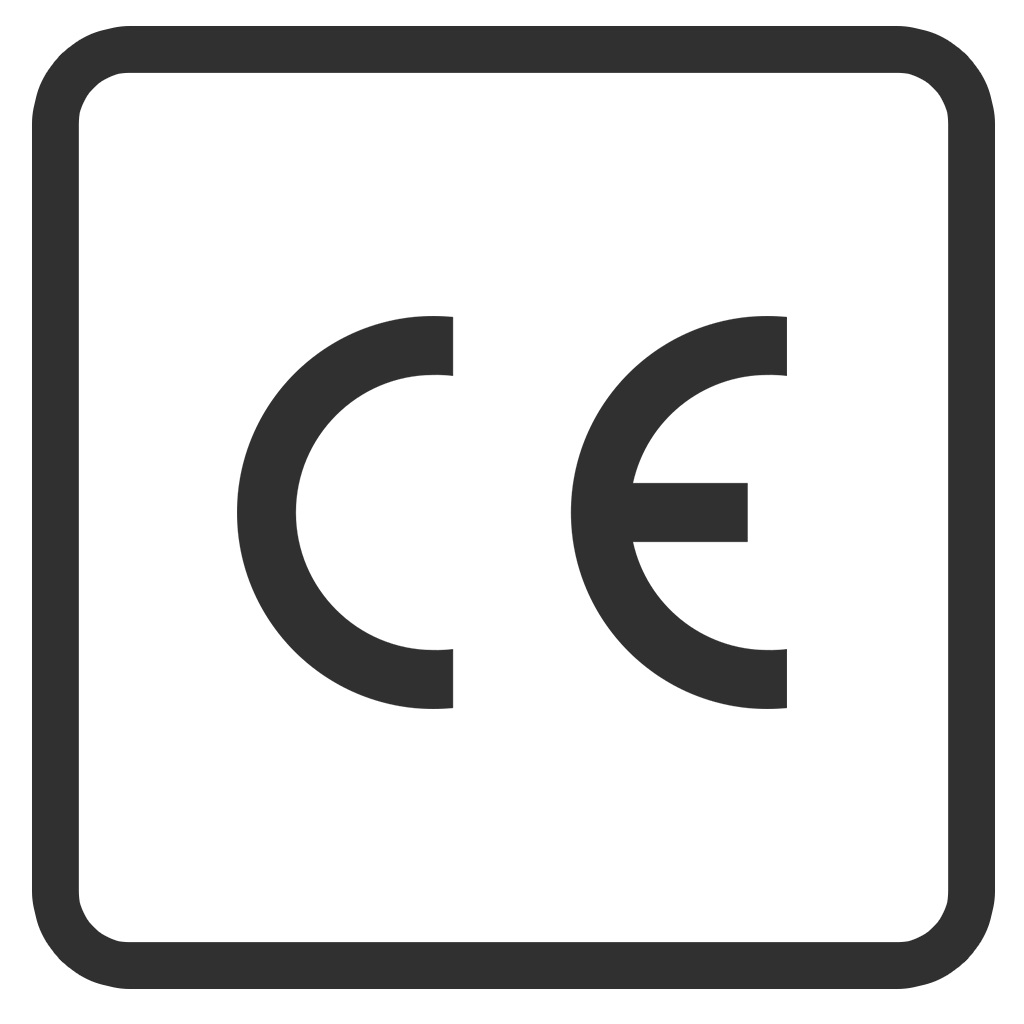