MAAG Company
The MAAG Group comprises successful and renowned companies, each with their own impressive history. Automatik Plastics Machinery, Ettlinger Kunststoffmaschinen, Maag Pump Systems, Gala Industries, Reduction Engineering Scheer and Xantec Steuerungs- und EDV Technik are today the strong and innovative product brands of the MAAG Group.
The history of the MAAG Group thus begins in the late 19th century, with the establishment of Scheer as a metal foundry and machine factory in Stuttgart, Germany, in 1890. Maag Pump Systems was founded in 1913. Automatik Plastics Machinery was founded in 1947. Gala Industries was founded in 1959, and Ettlinger Kunststoffmaschinen in 1983. The youngest member of MAAG Group – Xantec Steuerungs- und EDV-Technik was founded in 1994. Over the decades, they have all grown into experts in the various fields of polymer production and processing.
All the members of the MAAG Group contribute their supreme expertise and years of experience in developing and manufacturing superb machines, plants, systems, and software – and will continue doing so in the future. The bundling of core competencies, industry best practices, the attentive maintenance of existing business relationships and creation of new ones, all provide the foundations for maximum customer satisfaction throughout the Group.
High-Capacity Model
MAAG/Gala is the market leader for high capacity dryers. Large resin producers have the need for high capacity, continuous operation pellet dryers. By utilizing patented processes and innovative equipment designs, MAAG/Gala is capable to manufacture centrifugal pellet dryers with outputs up to 150 metric tons per hour (330,000 lbs/hr). Design innovations such as segmented rotor designs, wedge wire rotor screens, leak proof bearing seals in combination with high quality steel options assure our customers highest reliability. All MAAG/Gala pellet dryers are supplied with door timed interlocks and local power disconnect for operator safety.
Heavy duty construction
Designed for high capacity, continuous use
Designed for long-term production
Door safety interlocks
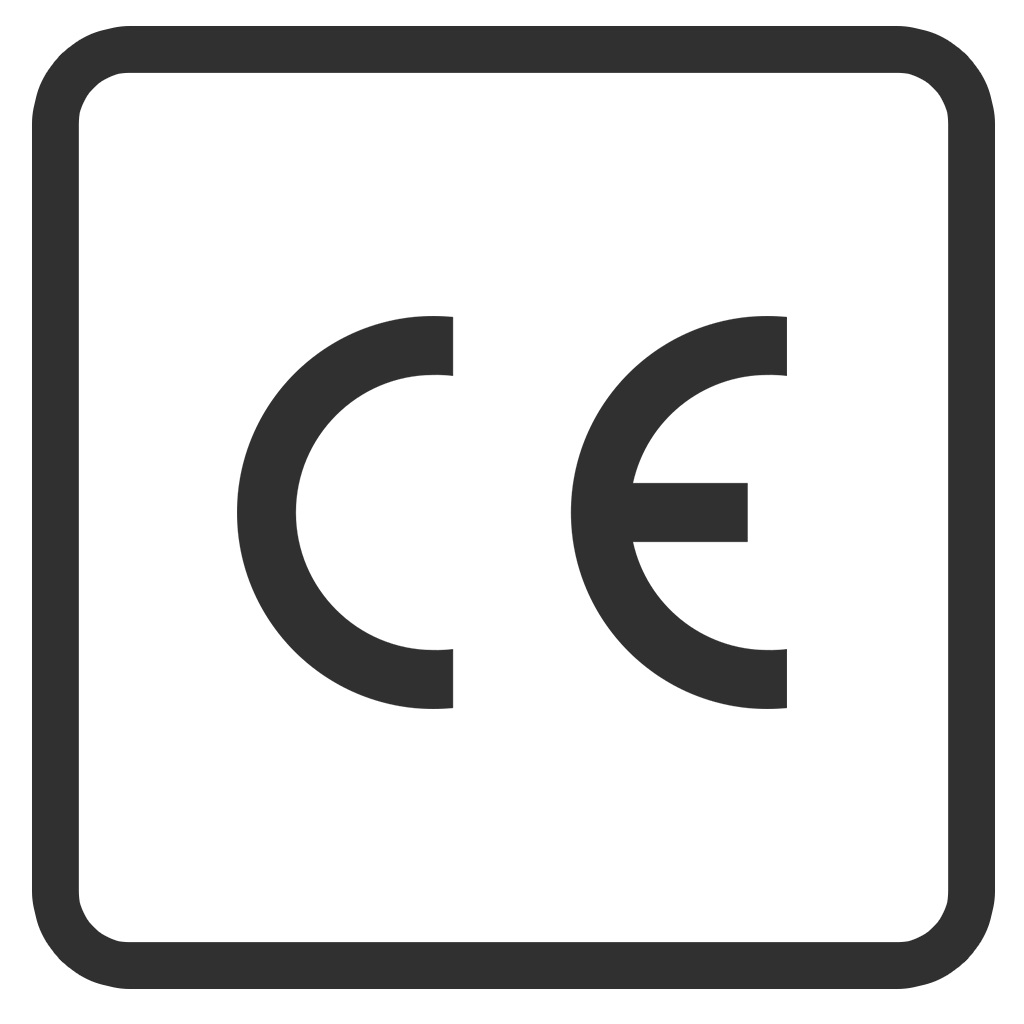
CENTRO centrifugal dryer
Energy-efficient drying with minimal required space
The CENTRO series of dryers is suitable for use with both underwater pelletizing and underwater strand pelletizing systems. Well thoughtout and highly accessible components, such as the core rotor device, serve to provide excellent operating characteristics and efficient servicing.
Excellent pellet quality
Compact design
Pneumatic interlock
Integrated pre-dewatering
Easy exchange
Special design
Adjustable rotor speed
Self-cleaning system
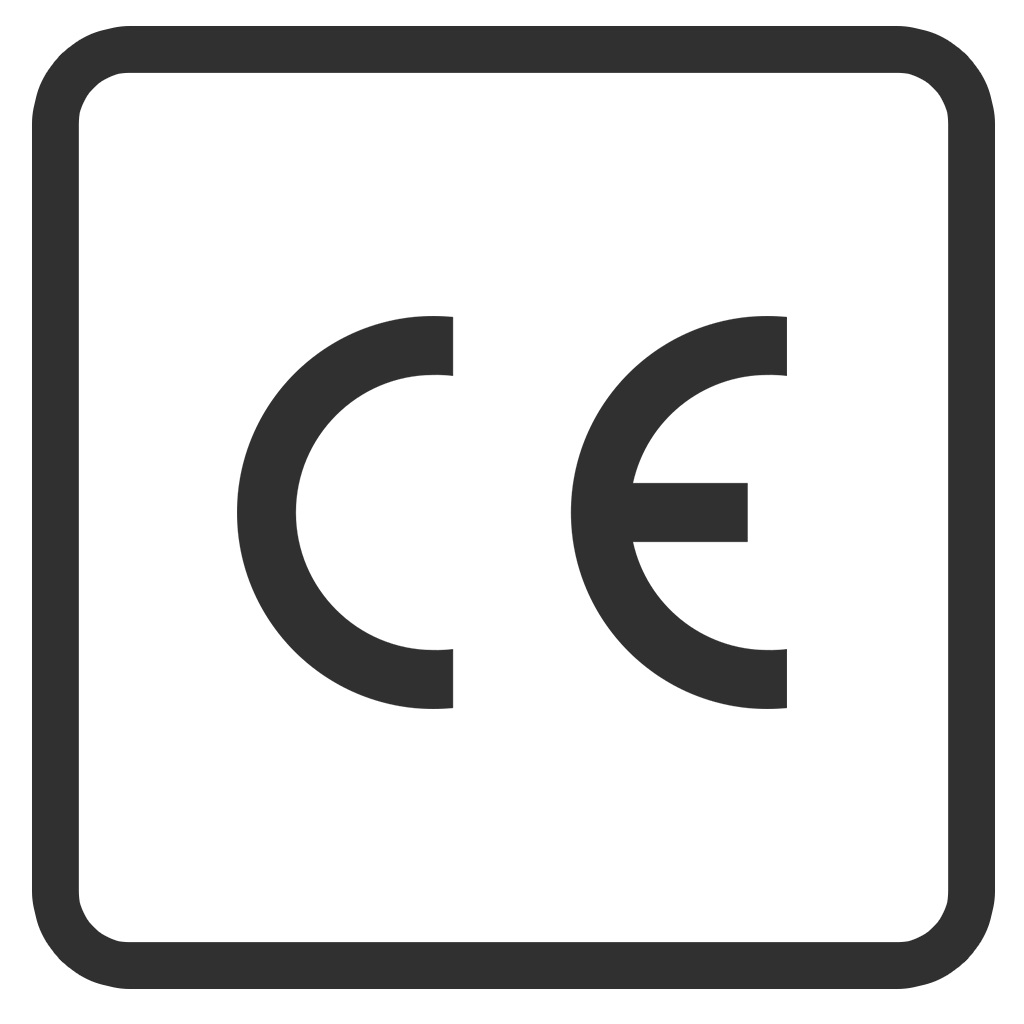
Model SC - Self-Cleaning
Self-Cleaning
The Gala Self-Cleaning Pellet Dryer is designed to achieve a high degree of self-cleaning which will reduce the otherwise common downtimes to a minimum. In most cases, this centrifugal pellet dryer does not need to be cleaned and nor opened to prepare the system for a color change.
Easy to clean
Low noise
Isolated housing
Safety interlock timed by the door
Output up to 2,500 kg / h
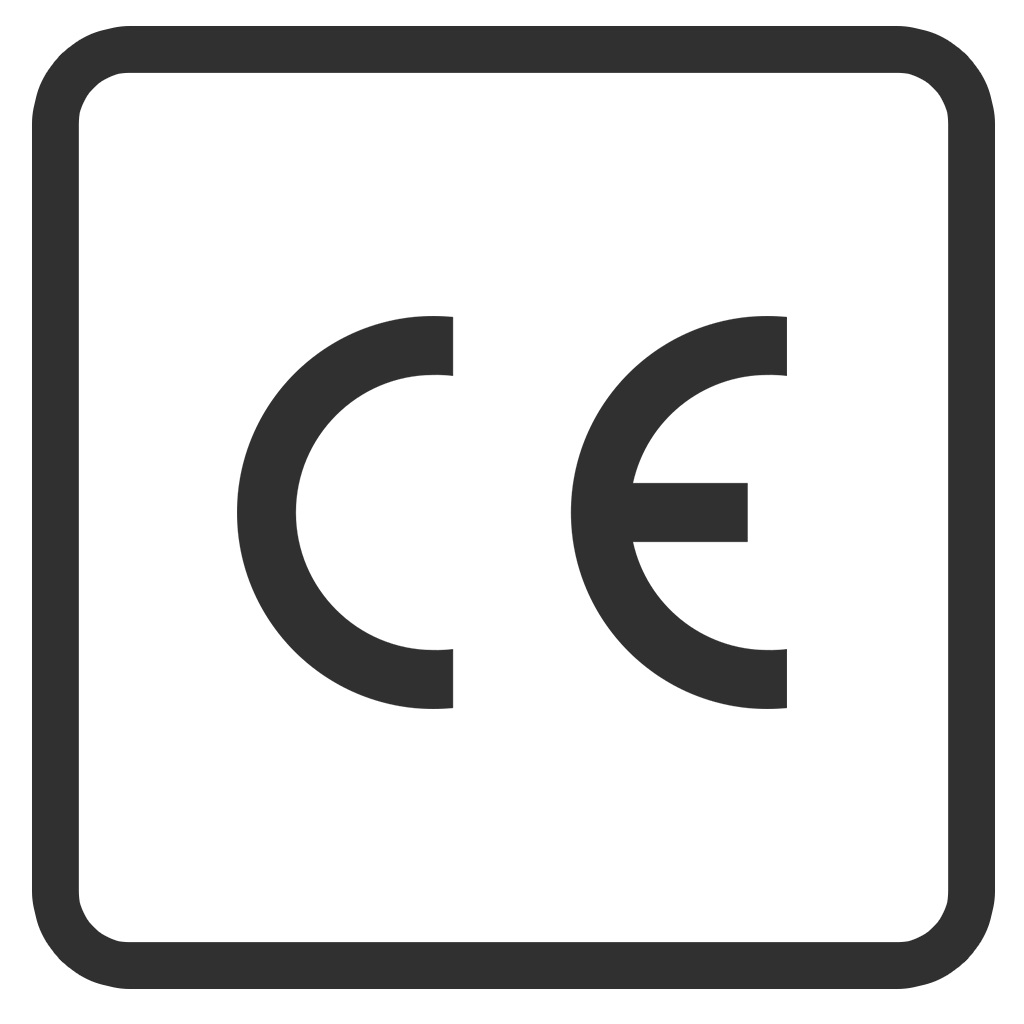
EA - Easy Acces
All members of the EASY ACCESS centrifugal pellet dryer series from Gala offer wide doors which permit easy, convenient and safe access for internal cleaning and maintenance. All Gala pellet dryers are supplied with door timed interlocks and local power disconnect for operator safety in polymer manufacturing.
Easy to clean
Low maintenance
Large, wide door
Safety interlock timed by the door
Output from 1,000 kg / h to 85,000 kg / h
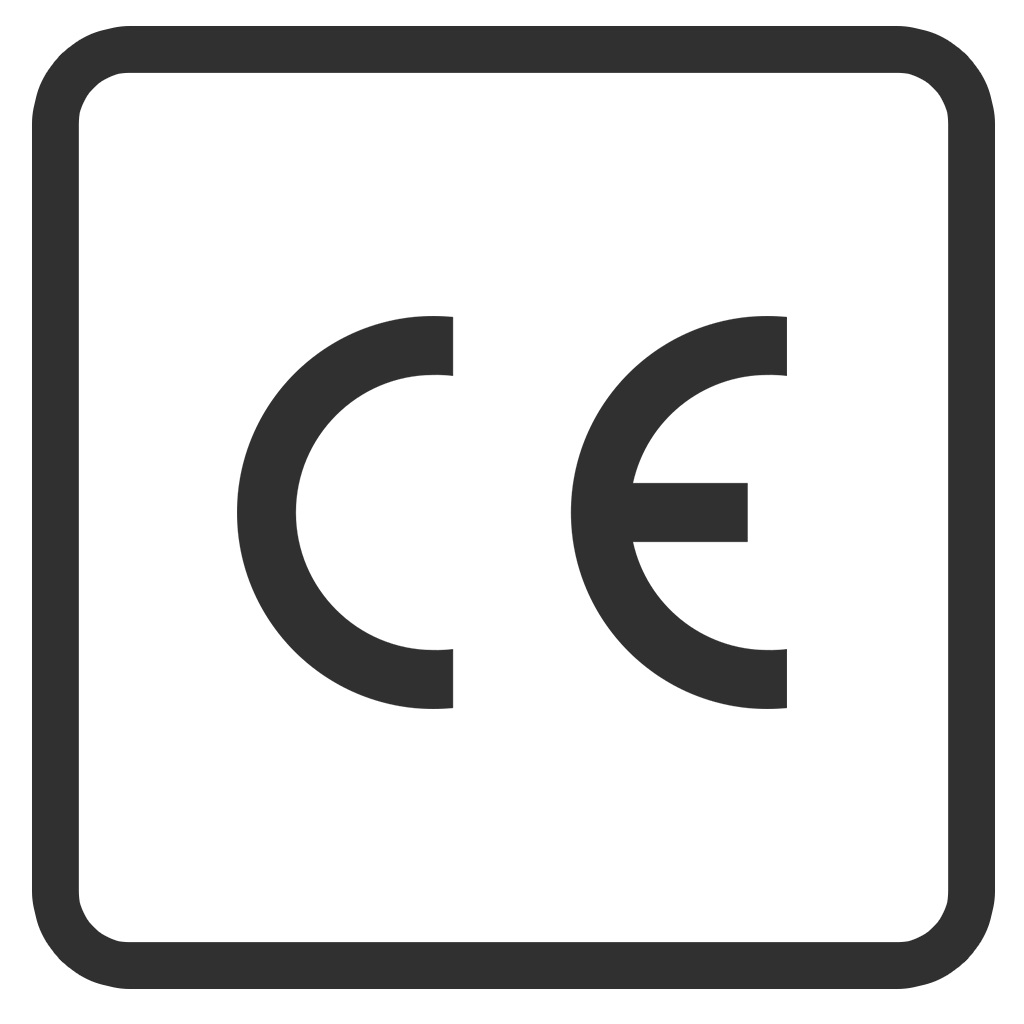
COLORex Color Mixer
Ambient pulverizer and color pulverizer – COLORex Color Mixer
The COLORex Color Mixer is used to mix product in-line with a ambient pulverizer and color pulverizer to eliminate the cleaning time of a central mixer. It can also be used off-line with a loader system and multiple feeders. The mixer
COLORex Color Mixer is portable, easily moved to alternate locations
On Demand Color (portable, versatile)
Eliminates Batch Mixing
Changeover time decreased (i.e. from black to yellow in under 1 hour)
No confined space permits needed
Color straight from the pulverizer or a weigh station
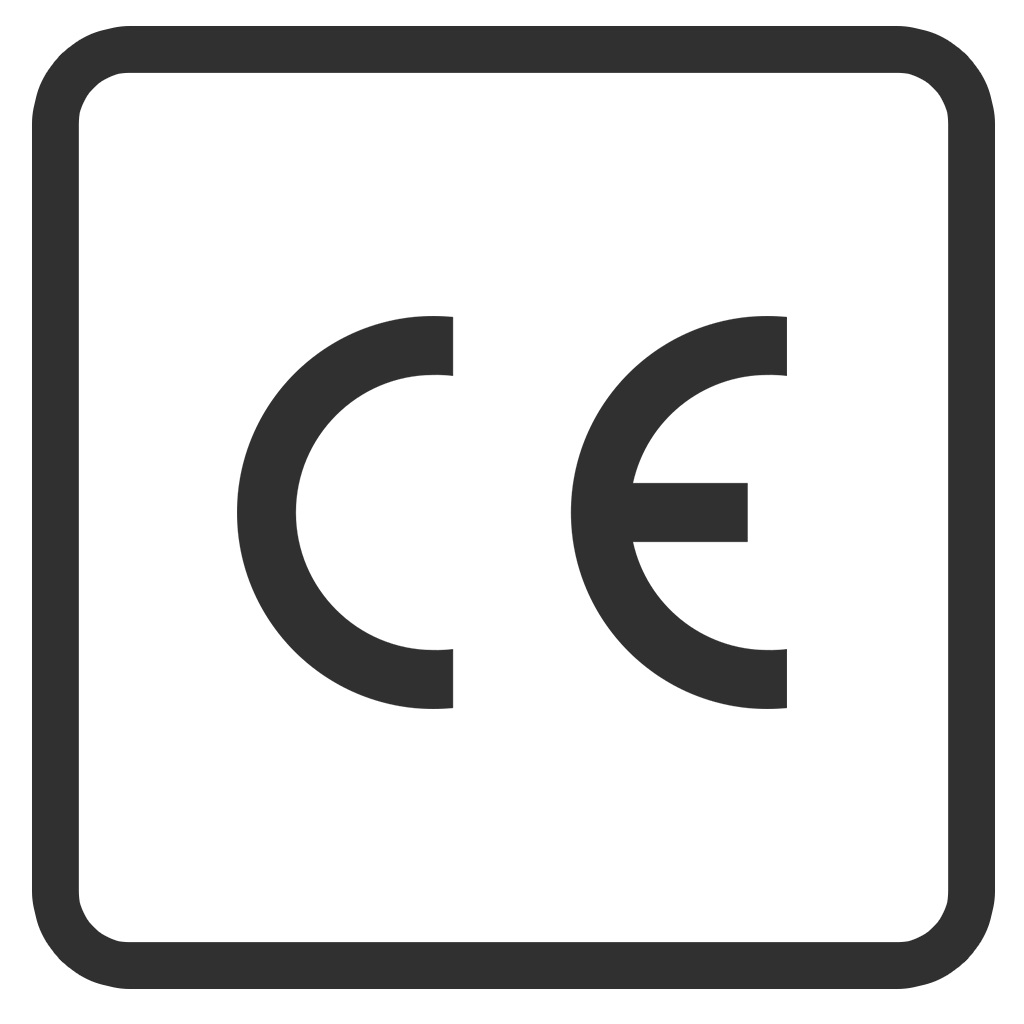
Disposable Disc Technology
Disc mill perfomance with reduced operation costs for pulverizer disc technology
Our technically sophisticated systems of disc mills use liquid nitrogen to cool down a feed material prior to and/or during milling to either help prevent its melting or decomposition, or achieve embrittlement in the pulverizer discs. Because each product is unique, throughput rates will vary.
Lower cost of operation
Light weight for easy handling
Reduced shipping cost
Increased airflow for better cooling
Retrofit kits for existing RE pulverizers
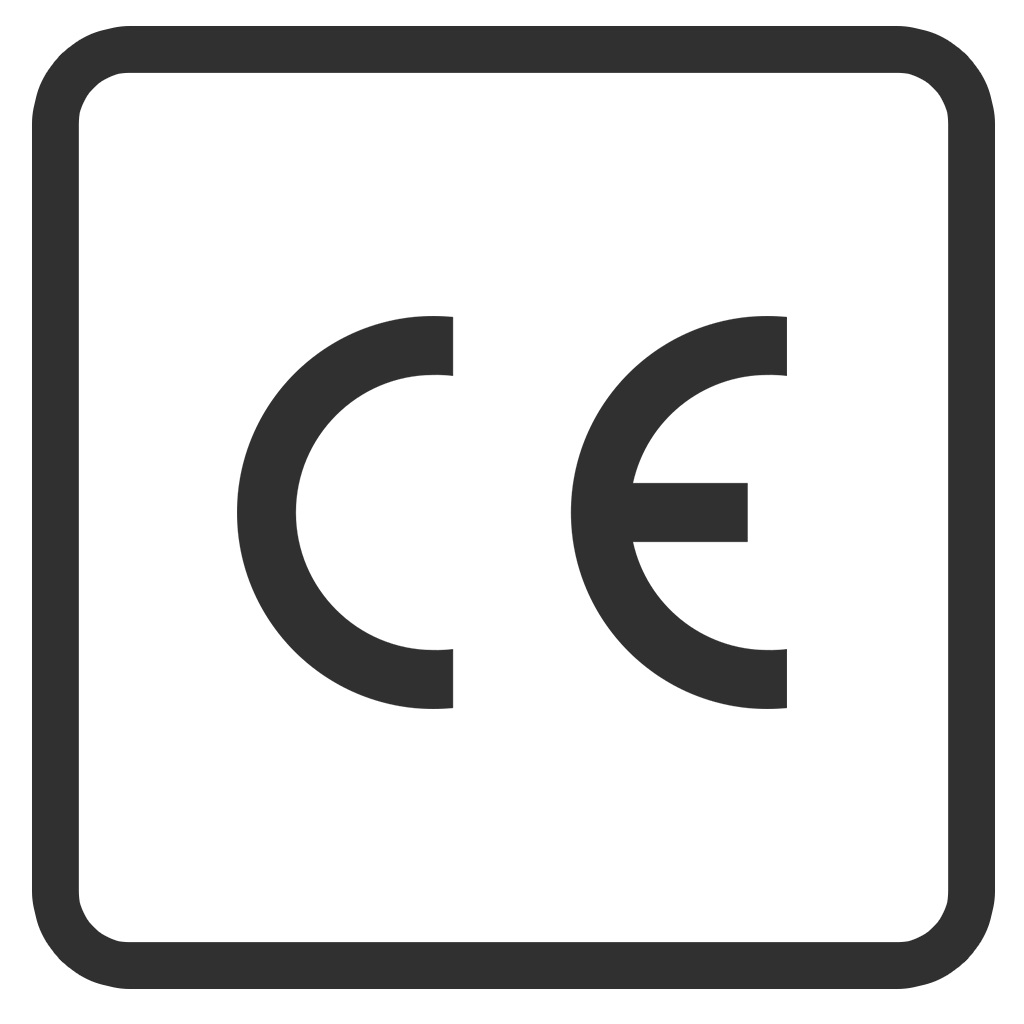
Pulverizing System 85XLP
The plastic cryogenic pulverizer with the ideal solution for in-house production
The Reduction Engineering pulverizer 85XLP, with its compact design, is the perfect fit for the medium throughput range or the ideal solution for in-house production. This unit of the cryogenic plastic pulverizer, with its integrated PLC controls, assures fully automatic production at a high level with very little operating effort. As with all Reduction Engineering pulverizers, this air-cooled pulverizer incorporates our state-of-the-art technology that facilitates quick clean-downs and change-over times.
Energy efficient
Shim-less gapping of discs
Small footprint
Remote access to machine interface
Best control of particle size distribution
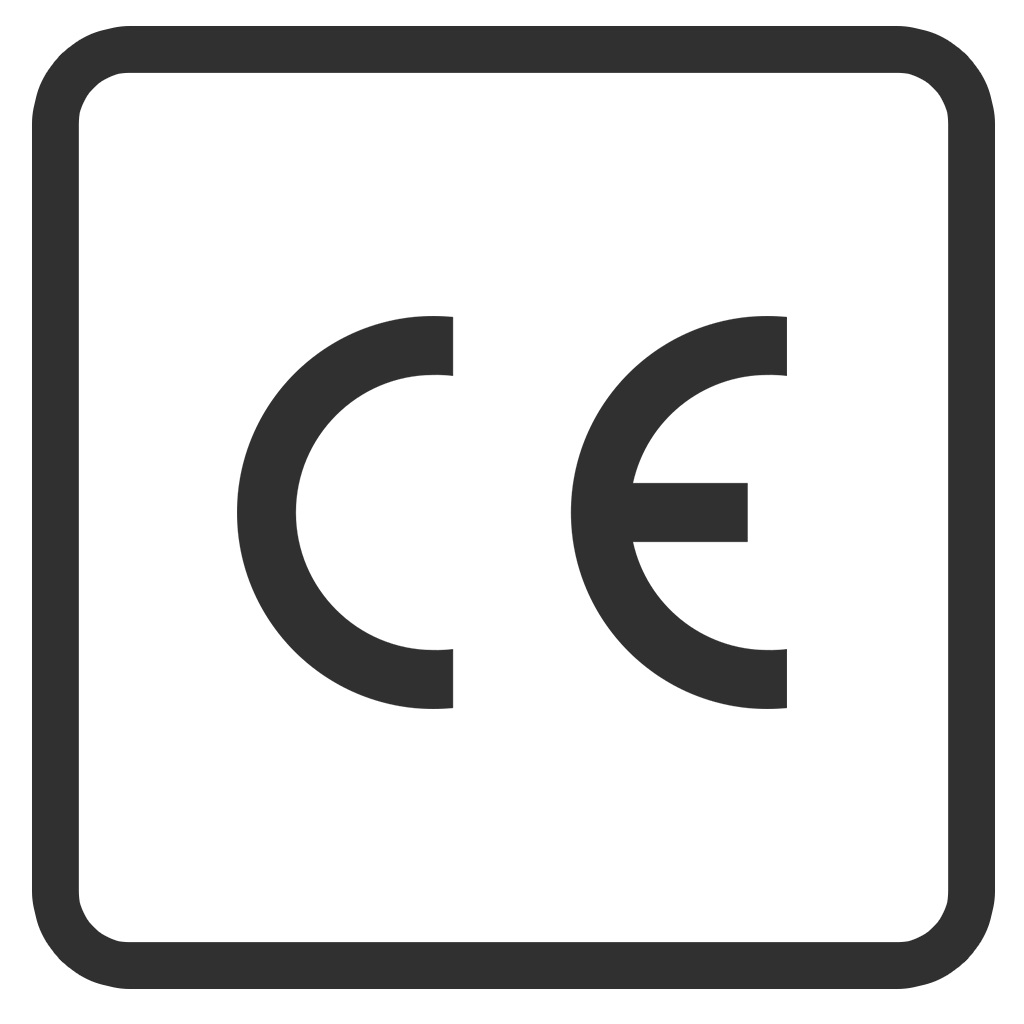
Lab Pulverizer REX tech
The plastic cryogenic pulverizer is manufactured for cryogenic operation
The REX tech, our lab scale pulverizer, makes sampling and trials for R&D fast and simple. Depending on the selected equipment, the REX tech can be cooled with ambient air or nitrogen. This versatile cryogenic plastic pulverizer can service a wide variety of applications in which top-quality sample powders are required. Almost anything can be trialed on this unit – engineered resins, rubber, adhesives, pharmaceuticals, and food grades on the lab pulverizer.
Elimination of outside services for trials
Less waste for in house testing
Ambient & Cryogenic ready
Versatile hopper design for inlet/outlet
Small footprint, equipped with casters for easy portability
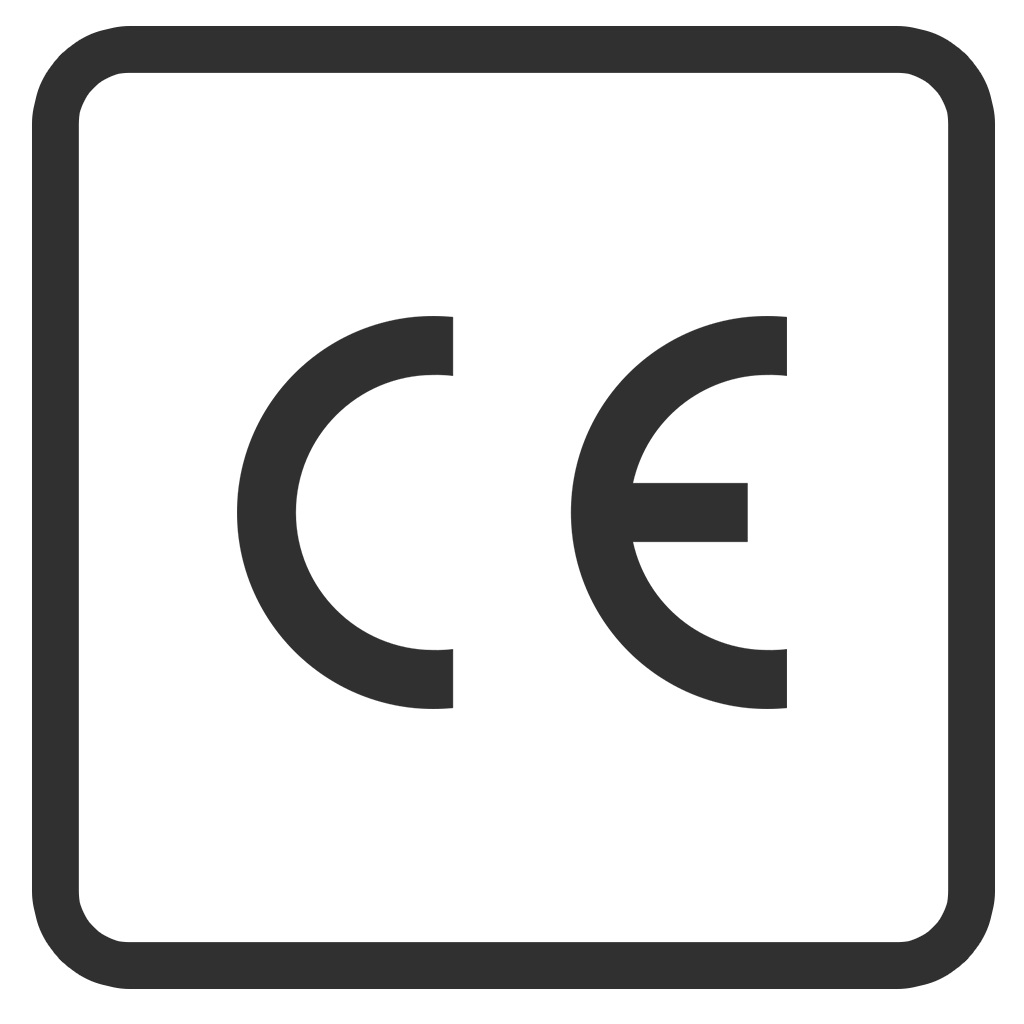
BATCH SAMPLER
Compact, fully automatic pellet sampling unit
Whether raw material or end product, modern industry often produces large quantities of bulk material. Regular analyses are required to ensure that pellets meet your quality standards. The BATCH SAMPLER is a compact, fully automatic system taking pellet samples by means of a suction lance at the end of the classifier.
Minimal maintenance
Flexible positioning
Automatic sampling 2 to 5 kg
Integrated gravimetric control
Integration into existing process management
Compactly built and flexible positioning, IP 55 protection
Plug and Play
One button control
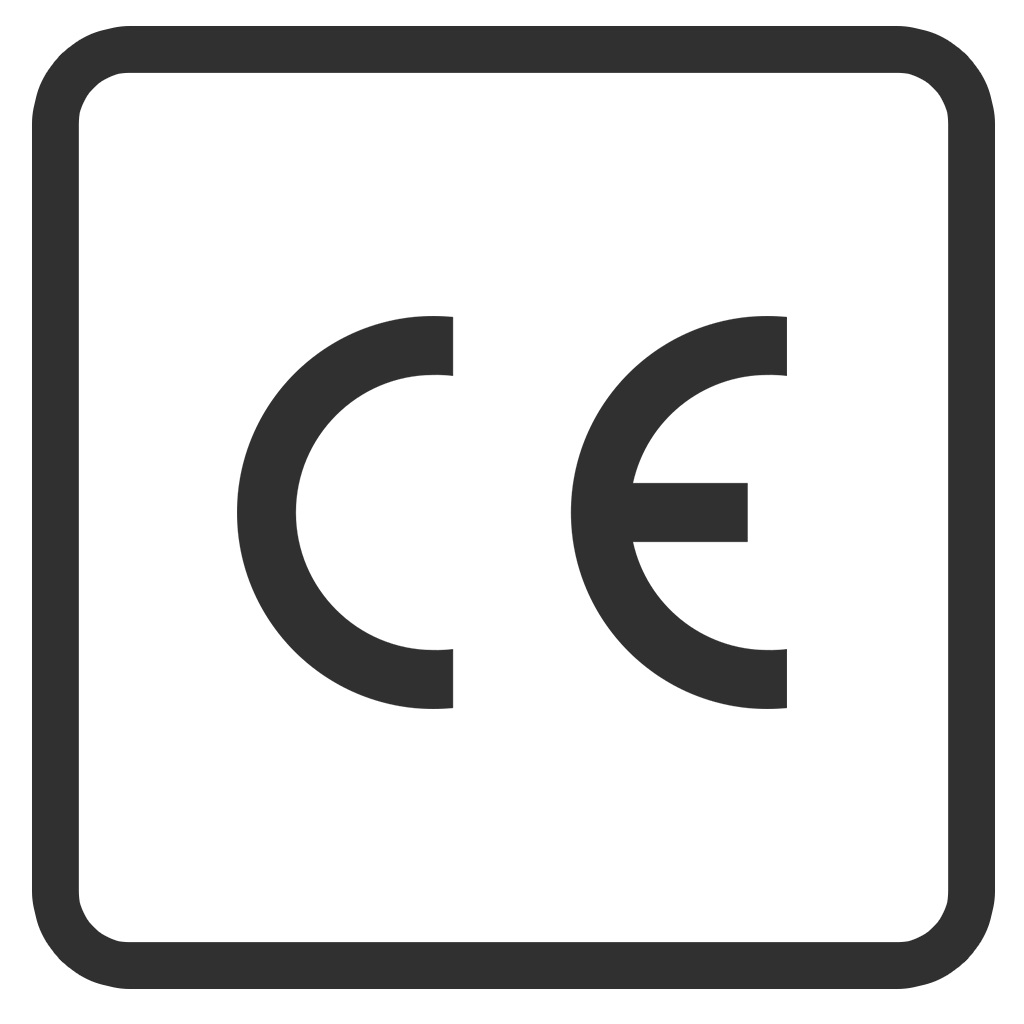
AUTO PELLET SAMPLER
Innovative pellet sampling unit for laboratory applications
The AUTO PELLET SAMPLER is designed for the lab or any other designated place where pellet samples from the production are needed. The fully automatic sampling system transports a container specially developed to collect pellets from the classifying sieve to the measuring device – overcoming several floors or distances of up to 300 m is no obstacle.
Compact design and flexible placement
Easy to use and automatic cleaning
Low maintenance
Automatic sample of up to 2 kg of pellets from several production lines
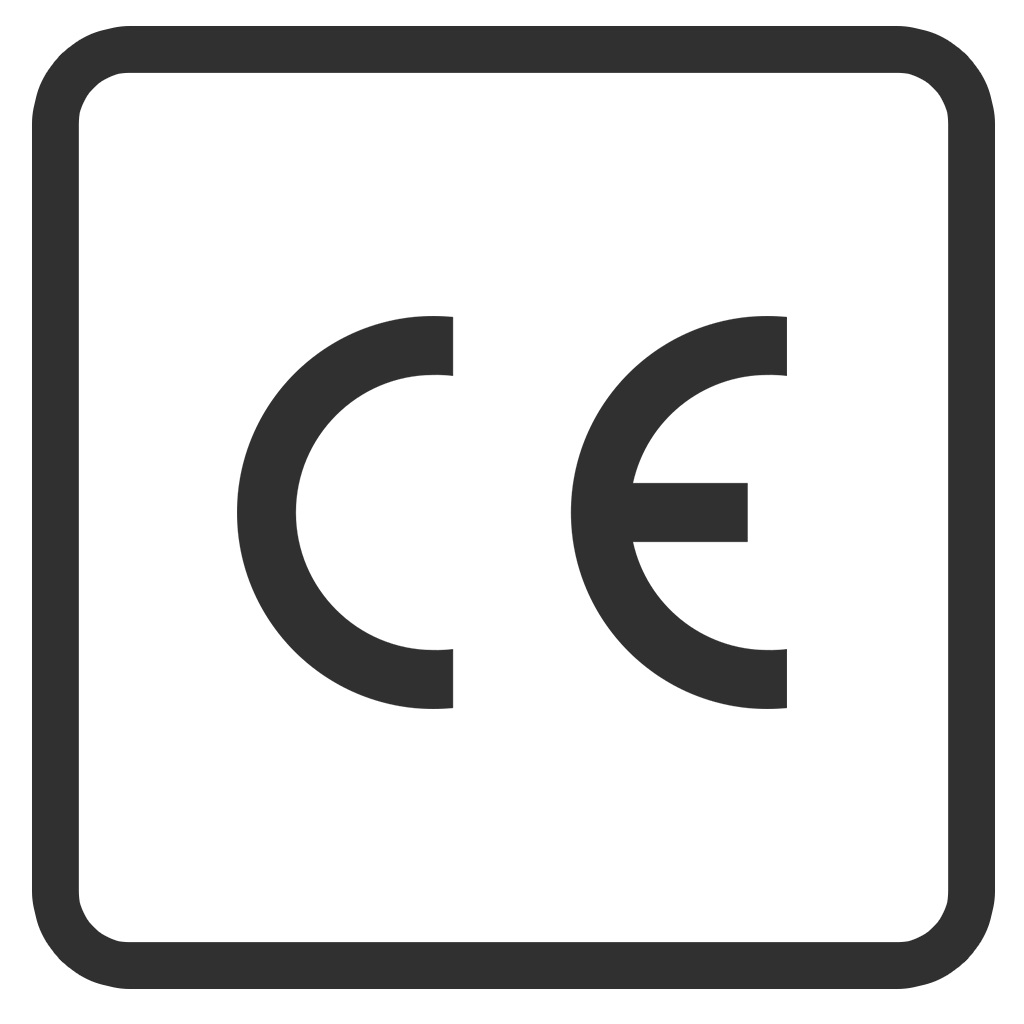
COLOR CONTROL
Efficient process control and color measurement on the pellets
The COLOR CONTROL system was developed for online color measurement directly on the pellet and is one of the most modern online color measuring systems in the world.
Fast measurement: <2 minutes
Contactless measurement
Only 35 ml of measuring material
Bad ones are filtered out
Fast color correction
The extruder does not have to be stopped
Car quality monitoring
Mixing quality control
Automatic control
Inspection tool
Dosing unit control
Increases production capacity
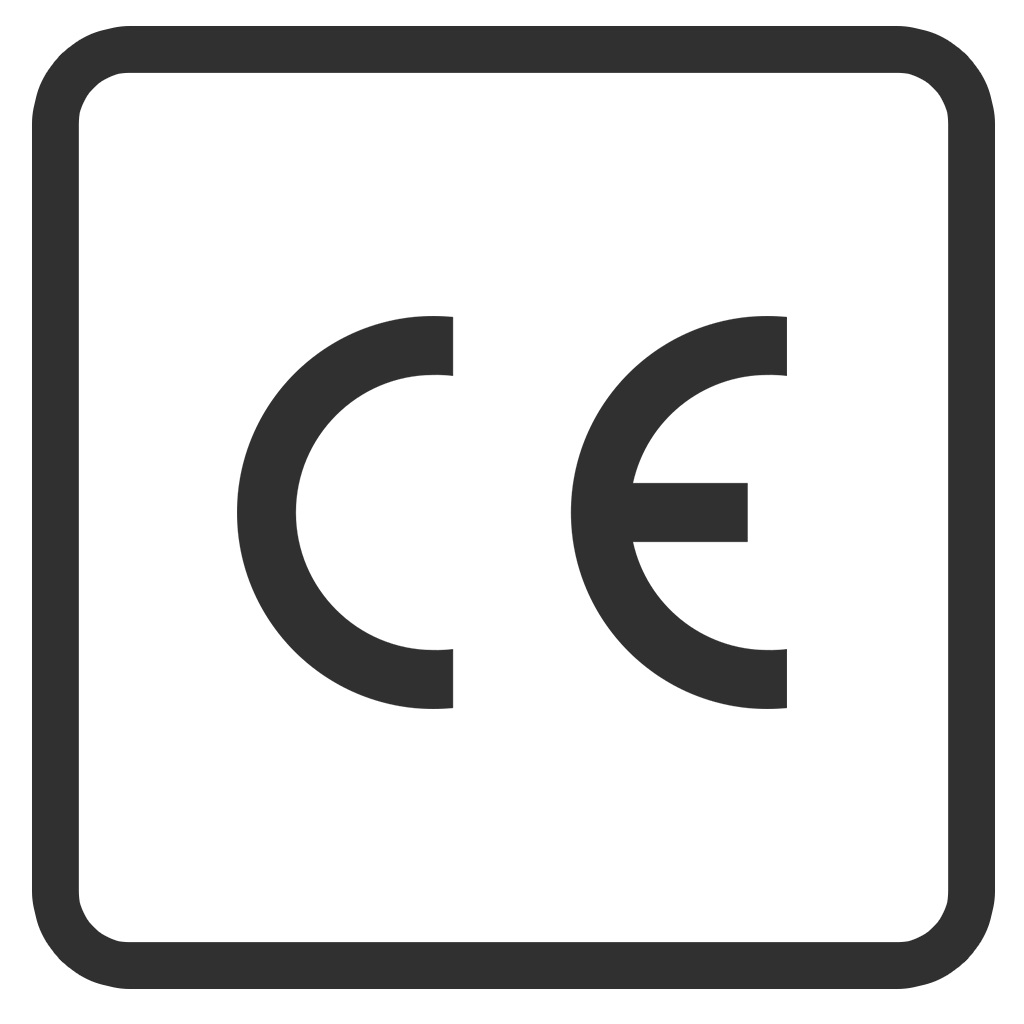
COLOR DOSING
Precise and quick dosing through optimal dosing precision and flexible and automatic process control
Precise dosing is a prerequisite for high-quality products. Complex color recipes in particular require trouble-free solutions during the dosing process. Optimum dosing precision and flexible and automated process control are decisive criteria – requirements that our dosing system meets. The system can be expanded modularly, and thus grows with the needs of plant operators.
Highly accurate measurement
Accurate reproducibility
Dosage of up to six ingredients
Dye change within 60 s
Robust and easy to clean
Easy retrofitting
Process automation
Integration into COLOR CONTROL
Guarantees higher quality
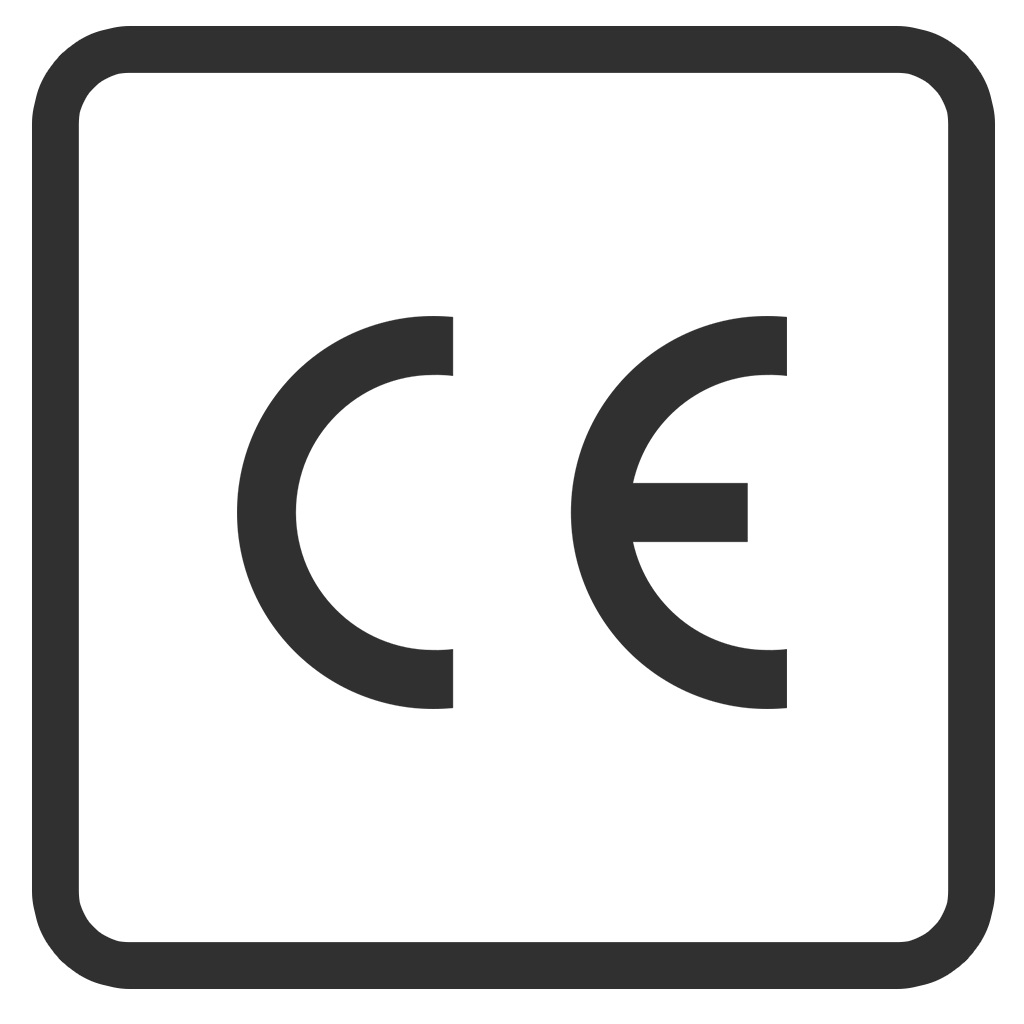